بسته بندی-قوطی فلزی-انواع قوطی فلزی-جایگاه صنعت بسته بندی در ایران و جهان-عدل بندی
بسته بندی پلی است بین تولید کننده و مصرف کننده
بسته بندی
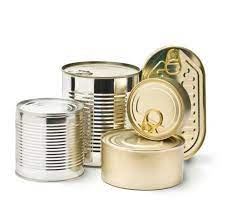
نوع بشر از بدو آفرینش، آنگاه که موفق به ساخت ادوات و تجهیزات جهت بهبود وضعیت زندگی خود شد. جهت نقل مکان آنها نیازمند بَسته بندی گردید.
بَسته بندی به لحاظ دارا بودن ویژگی های خاص در زمینه های مختلف و فراهم نمودن امکان ذخیره سازی فرآورده های گوناگون. از جمله مواد غذایی بخصوص پس از دسترسی به فنون پاستوریزاسیون از اهمیت ویژه ای برخوردار شد.
صنعت بَسته بندی بعنوان یکی از مهمترین و تعیین کننده ترین عوامل مؤثر عرضه کالا. و موفقیت در کسب بازار، هم اکنون تمامی فعالیت های تولیدی و بازرگانی را در جهان متوجه خود کرده. به نحوی که اگرچه مقوله جدیدی در صنعت و اقتصاد نیست. ولی با تحولاتی که یافت توجه بسیاری را به خود جلب نمود. و به عاملی تعیین کننده در موفقیت عرضه کالا و خدمات مبدل گردید.
متأسفانه با تمام اهمیت آن هنوز در ایران توجهی اساسی به آن نشده. و می توان گفت صنعت قوطی سازی که شاید. یکی از مهمترین شاخه های صنعت بسته بندی است. آنچنان که باید مورد توجه قرار نگرفته. گرچه در سالهای اخیر اقداماتی در جهت نوسازی آن بعمل آمد. ولی هنوز راهی دراز در پیش است.
جایگاه صنعت بسته بندی در ایران و جهان
اهمیت صنایع بَسته بندی در دنیای امروز و نقش تعیین کننده آن در حفظ و نگهداری. شکیل شدن کالا، سهولت حمل و نقل، طول عمر، استحکام، قیمت اتمامی، و… در حدی است که گاهاً اهمیت آن در جلب مشتری بیش از کیفیت محتوی است. بدین جهت به آن بها دادند و در نتیجه به پیشرفت های بسیار نائل گردیده. به نحوی که سیستم بَسته بندی در حال حاضر، حتی با ده سال گذشته نیز قابل مقایسه نیست.
اما متأسفانه در کشور ما این گروه علاوه بر مشکلات عام صنعت. همانند عدم ثبات و قانون مندی اقتصادی، تأثیرپذیری از نرخ ارز، مدیرت ناکارآمد، کمبود نیروی متخصص، افزایش بی رویه دستمزدها. قانون کار، تورم، نیروی کار غیر متخصص، کثرت عوارض، مالیات ها و… در سالهای اول انقلاب یعنی در دوران ارزهای ارزان با نامهربانی مسئولین وقت روبرو بوده. بطوری که ارز تخصیصی به آن اساساً صرف ورود مواد اولیه و قطعات یدکی گردید. و سهم چندانی جهت بازسازی، نوسازی و جایگزینی ماشین آلات اختصاص نیافت. و در نتیجه از کاروان پیشرفت تکنولوژی بسیار عقب ماند. البته باید اذعان داشت.
که صنعت بَسته بندی نیز همانند سایر گروه های صنعت. در دوران سازندگی به پیشرفت هائی نائل آمد. از جمله استفاده از ماشین آلات مدرن ولی متأسفانه دارای حلقه های مفقوده ایست. که باعث ناکارا شدن آن گردیده که مهمترین آن شاید عدم توجه لازم به آموزش، تحقیقات و نوآوری باشد.
به هرحال به منظور بررسی این صنعت بعلت گستردگی دامنه و تنوع مواد اولیه مصرفی. و به تبع آن تفاوت تکنولوژی، می بایست ابتدا آن را به گروه هائی تقسیم نمود.
1-بندی با فلز
2-با چوب، کاغذ یا مقوا
3- با مواد شیمیایی همچون نایلون، پلاستیک و …
4- با شیشه و سرامیک
5- با الیاف و پارچه
نظر به اینکه مطلب مورد بحث این پروژه فقط بخشی از صنعت عدل بندی فلزیست. لذا از ورود به بحث سایر گروه ها خودداری می گردد.
معرفی بسته بندی فلزی
این نوع از صنعت به عنوان یکی از مهمترین و تعیین کننده ترین عوامل مؤثر در بازارهای جهانی. و به لحاظ دارا بودن ویژگی های خاص در زمینه گوناگون و فراهم نمودن امکان ذخیره سازی فرآورده های کشاورزی. و غذایی در مقطع زمانی خاص و در مواقع بحرانی همواره انگیزۀ لازم جهت صرف وقت و هزینه های بالا را دارد.
از آنجا که بَسته بندی تکنولوژی لازم برای حفظ و نگهداری سلامت کالا در مقابل خطرات گوناگون، مهمتر از همه فساد، را دارا می باشد. لذا با توجه به اصول علمی و با در نظر گیری ویژگی های کلای مورد عدل بندی، باید صنعتی به کارگیری شود. که محصول مورد عدل بندی پس از طی مراحل مختلف حرارتی. نگهداری و حمل و نقل، کاملاً سالم و با حفظ ارزشهای غذایی خود به دست مصرف کننده برسد. که در هر مورد باید بَسته بندی خصوصیات خاص خود را داشته باشد. که در این مسیر نیاز به بَسته بندی های مقاوم و بهتر منجر به پیدایش و توسعه ظروف فلزی گردید.
در تقسیم بندی، عدل بندی به گواهی آمارهای موجود، بَسته بندی فلزی را می توان. یکی از مهمترین شاخه های این گروه از صنعت تلقی نمود.
در بخشی از گزارشی که توسط انستیتو تولیدکنندگان قوطی (CMI) با بررسی نظرات 1000 آمریکایی انجام گرفت. 88% مردم آمریکا اذعان نموده اند که عدل بندی سنتی مورد علاقه آنها شامل به ترتیب بَسته بندی فلزی، شیشه ای و پلاستیک است. و 60% قوطی های فلزی را بر عدل بندی های جدید امروزی ترجیج دادند. از آنجا که قوطی فلزی نسبت به سایر انواع عدل بندی امکان حفظ مواد غذایی در طول مدت، بدون کمک نگهدارنده ها را دارد. لذا قوطی فلزی با 68% محبوبیت به عنوان شایع ترین نوع بَسته بندی معروف شدند.
بَسته بندی فلزی خوراکی ها
تعریف بسته بندی فلزی:
منظور از عدل بندی فلزی است که ماده اولیه اصلی مصرفی برای عدل بندی کالای فلزی می باشد. بدیهی است سایر مواد بعنوان مواد کمکی و جنبی در این گروه استفاده می شود.
امروزه ظروف فلزی به عنوان بخشی از عدل بندی مواد خوراکی در اشکال مختلف با زندگی روزمره مردم عجین است. و تمام افراد جامعه در اکثر مصارف روزانه خود با یک یا چند شکل مختلف آن روبرو می باشند.
به طور کلی و اصطلاحاً بَسته بندی فلزی اشکال مختلف دارد. مانند قوطی کنسرو. قوطی نوشابه، قوطی آئروسل، تیوپ آلومینیومی، اسپری ها، قوطی های رنگ، محصولات پزشکی، بَسته بندی مواد شیمیایی. قوطی های روغن های غذایی و صنعتی، بشکه ها، گالن هاو… ورق های فولادی و ورق های آلومینیومی عمده ترین مواد اولیه این صنعت می باشد.
ورق های فولادی مصرفی در صنعت عدل بندی مواد غذایی پوششی از جنس قلع با ضخامتی در هر دو طرف ورق را دارند. و در سایر موارد ورق های آلومینیومی و فولادی هر دو منظور محافظت دیواره ظرف فلزی. و محتوی آن پوششی پلیمری به نام لاک در سطح داخلی دارند. که نوع لاک مربط به نوع محتوی ظرف عدل بندی متفاوت است.
گزارش Landell Mills اعلام می کند. 61% قوطی های فولادی و 6% قوطی های آلومینیومی به منظور عدل بندی مواد غذایی به کارگیری می شوند. و بررسی دقیق آماری نشان می دهد. که سبزیجات 30%، غذای حیوانات 23%، غذاهای آماده 13% و ماهی 11% سهم بسته بندی فلزی را به خود اختصاص داده اند.
زیرگروه های بَسته بندی فلزی:
این گروه را می توان به زیر گروه های ذیل تقسیم نمود.
الف: جعبه ، صندوق، کانتینر
ب: سیلندر، منبع و مخزن
پ: چلیک و بشکه
ت: قوطی و حلب
خصوصیات قوطی فلزی
قوطی فلزی اگرچه رایج ترین وسیله عرضه بسیاری از محصولات بخصوص مواد کشاورزی و دامی است. ولی بعلت گرانی قیمت مواد اولیه و حساسیت تولید نیازمند به استفاده از روش های مدرن. و تولید انبوه جهت استفاده از صرفه جویهای حاصله برای کاهش قیمت نهایی محصول و در عین حال حفظ کیفیت لازم می باشد. و همین امر باعث لزوم انجام سرمایه گذاری های ثابت سنگین و بکارگیری ماشین آلات بسیار مدرن و پیشرفته گردیده است. در نتیجه منابع تأمین ماشین آلات و مواد اولیه مرغوب محدود و برای بسیاری از کشورهای جهان، صنعتی وابسته محسوب می گردد.
میزان وابستگی این صنعت در ایران بخصوص در زمینه قوطی های غذائی از نظر ماشین آلات 100%. و از نظر مواد اولیه حدود 95% می باشد. (فقط تینر، مرکب، مایع لاستیک، سیم مسی که کلاً مواد جانبی هستند از منابع داخل قابل تأمین است).
مزایا و معایت بسته بندی فلزی
مزایا
1- بسته بندی فلزی محیطی غیر قابل نفوذ و محافظ عالی از خواص مواد غذایی. (حفظ بو، طعم، رنگ و ارزش غذایی مواد برای مدت طولانی، ایجاد می کند.
2-قابلیت نگهداری کامل مواد در حالت های جامد، مایع و گازها
3- مقاومت و استحکام بالا در برابر حرارت
4- دوام و استحکام مکانیکی خوب در حمل و نقل و انبار کردن
5- قابلیت تهیه با سایز و فرم های دلخواه و متنوع
6- ایجاد تسهیلات خاص نظیر جابه جایی در خط تولید به وسیله خاصیت مغناطیسی
7- قابلیت بازیافت و عدم آلودگی محیط زیست را دارد.
معایب
1- حمل و نقل و انبارداری قوطی های خالی حجم زیادی اشغال می کند
2- انبار قوطی ها بایستی عاری از بخار و رطوبت باشد
3- ساخت قوطی فلزی نیاز به تکنولوژی ویژه و دانش فنی بالا دارد
بازرسی ظاهری و چگونگی نگهداری
1- زنگ زدگی: در سطوح داخلی و خارجی قوطی باعث سوراخ شدن قوطی می شود. و موجبات فساد محتوی آن را فراهم می کند. که به علت نگهداری طولانی مدت در مناطق مرطوب، سرد کردن بیش از حد قوطی ها و تعریق آنها و… می باشد.
2- تورم قوطی: گاهی منجر به انفجار قوطی می شود. و در بعضی موارد باعث نشتی درزهای قوطی می شود. که علت های متفاوتی دارد. اما خطرناکترین آنها فساد میکروبی آن می باشد. یخ زدگی محتوی آن، تغییرات جوی در محل تولید و مصرف، واکنش های شیمیایی بین جدار قوطی و اسیدهای آلی موجود در غذا و … از دیگر دلایل آن می باشند.
3-bucking: شکل طبیعی قوطی به صورتی کج از بین می رود و امکان ایجاد نشتی در درزهای بدنه، سر و کف قوطی افزایش می یابد.
4- چین خوردگی: معمولاً در سر یا کف و در انتهای دو طرف دیواره ایجاد می شود. که اندازه گیری آن بصری بوده و وسیله دقیقی به منظور اندازه گیری آن وجود ندارد. اما چین خوردگی نباید در حدی باشد که نشتی ایجاد کند.
5- Lip,Vee,Deep: که به شکل انحنای عمیق، به شکل V و یا لب در محل اتصال سر یا کف به قوطی. و در اثر نقص ماشین درب بندی ایجاد می شود که باعث نشتی می شود.
6- تورفتگی بدنه: اگر شیبی در درز بدنه حاصل شود. موجب باز شدن درز و نفوذ عوامل فساد به داخل قوطی می گردد. که با پارگی در ناحیه برچسب یا Leible نمایان می شود.
7- دوایر متحدالمرکز: که در سر و کف قوطی و گاهاً در دیواره ها که حالت ارتجاعی به قوطی می دهد. و باعث افزایش استحکام قوطی می شود.
8- نشانه گذاری کف قوطی: توسط سازنده قوطی انجام می شود. و در آن نوع لاک توسط سازنده قوطی مشخص می شود و باید هماهنگ با غذای محتوی آن باشد.
نوع لاک A: مقاوم در برابر محیط های اسیدی (مرکبات گوجه فرنگی آلو قرمز توت فرنگی و …)
نوع لاک B: مقاوم در محیط های غیر اسیدی و غیر خورنده (پنیر و…)
لاک C: مقاوم در محیط های گوگردی مانند (گوشت، ماهی، لوبیا، نخود سبز و…)
تاریخچه قوطی سازی در ایران
اولین سازنده قوطی در ایران (در بخش خصوصی) شخصی است. ارمنی به نام آقای توتونف که از روسیه به ایران آمد. و با وسائل بسیار ساده و پرسهای دستی. و با استفاده از ورقهایی که از حلب های خالی نفت و بنزین بدست آورد(در آن موقع در ایران ورق حلب نبود). اقدام به تولید قوطی نمود.
البته شرکت نفت جهت تأمین حلب و بشکه مورد نیازش سالها قبل کارخانه ای در آبادان احداث نموده بود. که تولیداتش منحصراً در اختیار خود شرکت بوده و به بازار عرضه نمی گردید.
پش از مرگ توتونف در جاده چالوس تعدادی از شاگردانش همچون آقایان خامنه ای، اویسی، آرام و … اقدام به ایجاد واحدهای قوطی سازی با ماشین آلات قدیمی مورد خریداری از شرکت نفت آبادان و نیز تجهیزات ساده دیگر نمودند. ضمناً اولین واحد چاپ روی ورق توسط آقای حمیدی و شرکا (شرکت فر) در سال 1334 دایر گردید.
بنابراین اولین سازندگان قوطی در ایران بعد از توتونف رامی بایست آقایان خامنه ای، اویسی ، آرام محمدی (قوطی سازی ایران) دانست.
اولین کارخانه قوطی سازی به مفهوم امروز در شرکت روغن نباتی قو. جهت ساخت قوطی روغن نباتی و اولین خطوط تولید قوطی کمپوت و کنسرو در شرکن صنایع بسته بندی ایران. تابع به گروه صنعتی بهشهر که در سال 1342 توسط آقای لاجوردی تأسیس شد نصب گردید.
روند رشد قوطی سازی در ایران
در سالهای قبل از انقلاب بدلیل پائین بودن جمعیت و تمرکز آنها در روستاها (بیش از 70%) نیاز کشور به قوطی محدود بوود. لذا این کالا اساساً توسط مصرف کنندگان آن یعنی تولید کنندگان مواد غذائی و مواد شیمیائی، بعنوان تولید جنبی تولید می شد. که مازاد بر نیاز آنها به بازار عرضه می گردید. و واحدهائی که تولید آنها فقط قوطی یا حلب باشد بسیار محدود و انگشت شمار بود.
در سالهای پس از انقالب بدلایل مختلف از جمله افزایش جمعیت، تمرکز جمعیت در شهرها، جنگ تحمیلی، تغییر الگوی مصرف و… تقاضا برای قوطی افزایش یافت. لذا ضمن توسعه و تکمیل واحدهای گذشته تعداد زیادی واحدهای جدید ایجاد شده اند. که مهمترین آنها عبارتند از شرکت های صنایع بسته بندی تبریز، زاگرس، مهرآذر، تولید و گسترش کیافرین و بقیه، واحدهای کوچک محسوب می گردند. که اکثراً سازنده قوطی های کششی جهت مواد غذائی و یا قوطی های چند تکه مواد شیمیائی با ماشین آلات داخلی. و یا دست دوم و فرسوده بوده که طبق ضوابط مربوطه جهت آنها کارت شناسائی یا گواهی فعالیت صنعتی صادر شده. و از نظر تعداد مجموعاً بیش از 150 واحد می باشد.
بروز جنگ و شروع محدودیت های ارزی. باعث عدم توجه کافی به این گروه و قرار گیری آن در گروه سوم اولویت های بخش فلزی در سالهای گذشته. و تخصیص ناکافی ارز به این گروه گردید. ضمن اینکه سهمیه مورد تخصیص اساساً صرف خرید مواد اولیه و قطعات یدکی شد. و مسئله جایگزینی ماشین آلات و خرید اطلاعات فنی جدید نیز تقریباً به فراموشی سپرده شد. که حاصل آن عقب افتادگی از دانش روز و کاهش شدید کیفیت قوطی و تشکیل کمیته فنی ارتقاء کیفیت قوطی بود.
لازم به ذکر است که در سال 1371 با حمایت بی دریغ اداره کل صنایع فلزی. جهت ورود چند خط مدرن برای ساخت قوطی غذائی و لاک و چاپ بعنوان جایگزینی تخصیص ارز شد. که خود نقش اساسی در بهبود کیفیت داشته است. ضمن اینکه در سالهای اخیر بخش خصوصی نسبت به ورود ماشین آلات مدرن قوطی سازی و لاک و چاپ اقدام نمود. که تعدادی نصب و راه اندازی شد و تعدادی در حال نصب می باشد. در نتیجه مشکل کمی قوطی کاملاً حل شد. و امروزه توان تولید قوطی غذائی در کشور بیش از نیاز می باشد.
و از نظر کیفی هم واحدهای بزرگ سازنده قوطی غذائی موفق به کسب مهر استاندارد گردیده اند. یعنی حداقل از کیفیت قابل قبول برخوردارند ولی هنوز مشکلات و حلقه های مفقوده ای وجود دارد. که اساسی ترین آنها عدم وجود یا محدودیت امکانات تحقیق. آزمایشگاه های مجهز، کتب و منابع علمی به زبان فارسی، کلاس های آموزشی، نیروی انسانی ماهر و… و همچنین گرانی هزینه برای دسترسی به منابع علمی خارجی و دانش و تکنولوژی می باشد.
وضعیت تولید قوطی فلزی کشور
با توجه به پیشرفت تکنولوژی و دستیابی به دانش فنی که باعث تولید انبوه گردیده است. در حال حاضر قوطی فلزی می تواند بعنوان یکی از اقتصادی ترین ظروف بسته بندی در کشور مورد استفاده قرار گیرد. قوطی فلزی بعنوان یکی از مطمئن ترین ظروفی که قابلیت بالایی در حفاظت و ماندگاری مظروف خود را دارد، مورد استفاده قرار می گیرد.
تولید قوطی فلزی بعنوان یکی از ظروری ترین ابزار مورد استفاده در صنایع غذایی تبدیلی، طی 20 سال گذشته رشد چشمگیری دارد. ضمن اینکه این نوع ظرف جهت بسته بندی سایر تولیدات صنعتی عمدتاً مایع مانند روغن موتور، رنگ مواد شیمیایی و… نیز مورد استفاده قرار میگیرد. یکی از عمده مشکلات این صنعت وابستگی شدید آن به واردات مواد اولیه یعنی ورق حلب (تین پلیت) می باشد. که در حال حاضر بصورت کامل از خارج وارد می شود. که طبیعتاً با توجه به منابع محدود خارجی قیمت آن متأثر از وضعیت جهانی این کالا بوده. و لذا قیمت قوطی فلزی نیز در داخل کشور می تواند بسیار متغیر باشد.
البته لازم به توضیح است که با توجه به اینکه قوطی های فلزی توسط واحدهای تولید کننده قوطی تولید می گردند. ولی از این قوطی ها در صنایع مختلفی که دارای ماشین آلات پر کن مخصوص تولیدات خود می باشند مورد استفاده قرار می گیرند. که با توجه به اینکه این ماشین آلات عمدتاً ماشین آلات با ارزشی هستند. که واحدهای مذکور به راحتی قادر به تغییر خطوط بسته بندی خود نمی باشند. لذا عمدتاً تغییرات قیمت قوطی به واحدهای مصرف کننده تحمیل می گردد. و واحدهای تولید کننده قوطی فلزی از این بابت از حاشیه امنتیت برخوردارند.
ظروف بسته بندی فلزی به دو شاخه اصلی حلب و قوطی تقسیم می گردد. حلب عبارت است از ظرفی چهار گوش تولیدی از ورق حلب با ظرفیت 5 الی 17 کیلوگرم. و قوطی عبارت است از ظرفی چهار گوش یا گرد تولیدی از ورق حلب یا آلومینیوم با ظرفیت عدل بندی حداکثر 5 کیلو گرم.
قوطی فلزی نیز از نظر مواد اولیه مورد مصرف به دو نوع… حلبی و آلومینیومی تقسیم می گردد. که اکثریت احدهای تولید کننده داخلی از نوع قطی حلبی می باشند. و این قوطی نیز در تقسیم بندی های ریزتر به قوطی های حلبی معمولی. تحت فشار، درز دار (چند تکه) و بدون درز (کششی) تقسیم می گردند.
مواد اولیه مورد مصرف در قوطی فلزی حلبی که عمده واحدهای تولیدی در این زمینه فعالیت می نمایند. عبارت است از: ورق حلب با روکش قلع (که به تین پلیت موسوم است). و ورق حلب فاقد قلع (که به تین فری استیل موسوم است). به ضخات 0.15 میلیمتر الی 0.6 میلیمتر، سیم مسی، لحیم، مایع لاستیکی، لاک خارجی (جهت حفاظت قوطی در مقابل زنگ زدگی). لاک داخلی (به منظور جلوگیری از بروز واکنش شیمیایی بین محتوی ظرف و فلز). پودر درز جوش، تینر و مرکب، همانطور که قبلاً نیز بیان شد. مواد اولیه اصلی این صنعت یعنی حلب، وارداتی است. و فقط تینر، مرکب، مایع لاستیک، سیم مسی که مواد جنبی هستند از منابع داخلی قابل تأمین است.
ظرفیت تولید قوطی مورد مصرف در صنایع غذایی در سال 1380 معادل 85000 تن بود. که در سال 1385 این ظرفیت تا 120000 تن معادل 1/4 میلیارد عدد قوطی افزایش یافت. ضمن اینکه خطوط تولیدی جدید الاحداث بر اساس نیازهای روز احداث گردیده اند. که قابلیت تولید قوطی های کوچک حتی تا ظرفیت 70 گرم را داشته. ضمن اینکه نوع قوطی فلزی با دربهای آسان باز شو (Open Easy) نیز در برنامه تولید واحدهای جدید الأحداث قرار دارد.
در خصوص سایر واحدهای تولید ظروف فلزی لازم بذکر است. که در زمینه تولید قوطی فلزی مورد مصرف صنایع شیمیایی (غیر غذایی) تعداد 120 واحد تولیدی با ظرفیت سالیانه حدود 100 هزار تن. و در زمینه حلب بهداشتی تعداد 10 واحد تولیدی با ظرفیت تولید سالیانه حدود 18 هزار تن. و بشکه قیر و روغن صنعتی تعداد 64 واحد صنعتی با ظرفیت تولید سالیانه حدود 370 هزار تن در کشور فعال می باشند.
در زمینه تولید قوطی اسپری تولیدی با حلب تعداد 3 واحد تولیدی با ظرفیت سالیانه حدود 10 هزارتن. و قوطی اسپری آلومینیوم 1 واحد با ظرفیت تولید سالیانه 1200 تن. و تیوپ آلومینیوم تعداد 10 واحد تولیدی با ظرفیت تولید سالیانه 500 میلیون عدد فعال می باشند.
در مورد واردات و صادرات قوطی های فلزی لازم به توضیح است. که با توجه به حجیم بودن ظروف مذکور که عملاً کرایه حمل آن نسبت به ارزش کالا از حد متعارف بیشتر می گردد. این ظروف واردات و صادرات قابل ذکری نداشته است. ولی بدلیل گرانی تکنولوژی تولید قوطی های آلومینیومی که در داخل کشور تولید می گردد. و همچنین قوطی های خاص و گران قیمت مقدار کمی از اینگونه قوطی ها وارد می گردند. که با توجه به اینکه تعرفه این قوطی ها با تعرفه چیلک، بشکه و سایر ظروف فلزی مشترک می باشد. آمار واردات مندرج در کتاب واردات گمرک قابل تفکیک و استناد نمی باشد.
شرکت صنایع بسته بندی ایران
شرکت صنایع بسته بندی ایران بعنوان بزرگترین کارخانه تولید قوطی است. که از نظر خط تولید، میزان ورق مصرفی و تولید قوطی بالاترین سهم را در کشور دارد.
مصرف ورق این کارخانه – به جز ورقی مصرفی در روغن نباتیها-سالانه حدود 12000 تن است. که بیشتر برای قوطی های 200 گرمی، 500 گرمی (دو نوع) و یک کیلویی مصرف می شود. این شرکت حلب های برای احجام 900 گرمی، 1700 گرمی و 2700 گرمی نیز تولید می کند.
صنایع قوطی تبریز
به گفته مهدی اکرامی خط دوم چاپ و خط سوم لاک زنی شرکت صنایع قوطی تبریز راه اندازی گردید. و در آینده ای نزدیک با راه اندازی خطوط تولید درب های ایزی اپن (Easy Open) و پیل آف (Peel off). و تولید قوطی های 3 و 5 کیلویی این شرکت قادر خواهد بود. بخش بزرگی از نیازهای تولیدکنندگان داخلی را به قوطی های فلزی تأمین نمایند.
اکرامی می افزاید: صنایع قوطی تبریز در سال 1375 تأسیس شد. و حالا یکی از بزرگترین تولیدکنندگان قوطی های فلزی مواد غذایی، نوشابه، اسپری و درب قوطی در ایران به شمار می رود.
مدیر این واحد می گوید که توانستند اعتماد شرکت های معتبر تولیدی داخلی و خارجی را به دست آورند. وی می افزاید: تمام مراحل لیتوگرافی، لاک زنی، چاپ، تولید قوطی، درب، کنترل کیفیت و بسته بندی با ماشین آلات پیشرفته. و تحت کنترل دقیق سیستم های مکانیزه کامپیوتری انجام می شود. و در سایه این تلاش ها علاوه بر اخذ گواهی استاندارد ملی و ایزو 2000-1-900. این واحد تولیدی موفق به دریافت پروانه تأیید صلاحیت آزمایشگاه آکرودیته (EN 17025) نیز گردید.
اکرامی در مورد دیگر طرح های این واحد می گوید: در حال بررسی امکان تولید و کاربرد قوطی های تزیینی برای بسته بندی محصولات خشک. از قبیل چای، بیسکویت، شکلات، پسته و غیره هستیم تا به این وسیله استقبال بازار جهانی از محصولات داخلی افزایش یابد. این شرکت به گسترش فرهنگ بسته بندی در کشور و رواج استفاده از قوطی های فلزی علاقه مند بوده. و هر پیشنهادی را برای تولید قوطی های اختصاصی با علاقه مندی مورد بررسی قرار می دهد.
ساخت قوطی
مواد لازم جهت ساخت قوطی
1- ورق حلب: ورق بسیار نازک آهنی است که چنانچه با قلع روکش گردد. Tin Plate و اگر فاقد قلع باشد TFS ( Tin free steel) نام می گیرد. سه نوع فولاد بدون قلع مورد استفاده قرار می گیرد که عبارتند از:
الف- فولادی که روئین گردد بصورت شیمیائی (Chemically passivated steel) که روی سطح خود یک لایه فسفات – کرومات دارد.
ب- فولاد مورد پوشش با کروم یا یک لایه اکسید کروم
پ- فولاد مورد پوشش با آلومینیوم که دارای بعضی مشکلات در کشش، جوشکاری و اتصالات می باشد.
باید توجه داشت که ورق تین پلیت علاوه بر ایجاد یک پوشش محافظتی در روی فولاد. نقشی کاتدی داشته و امکان اکسیداسیون نقاط پوشش نشده یا مکانهایی که بصورت سوزنی فاقد پوشش می باشند را به حداقل می رساند. این پوشش قلعی از حل شدن آهن در برخی نوشیدنی ها که قادرند طعم نامطلوب آهن را به خود بگیرند جلوگیری می کند. ورق بدون قلع (TFS) این مزیت را نداشته و برای محافظت از سطح فولاد نیازمند پوشش کامل است. ولی در عوض چسبندگی لعاب ها و لاک ها به آن بهتر از ورق تین پلیت می باشد.
در ایران مصرف این ورق محدود و آن هم برای ساخت در و کف قوطی استفاده می شود. ولی طبق آزمایشات انجامی در مؤسسه استاندارد استفاده از آن با پوشش لاک مناسب برای تولید قوطی کششی مناسب تر است.
نظر به اینکه کیفیت ورق مصرفی در قوطی غذائی بسیار مهم است. می بایست در انتخاب آن دقت شود که مهمترین شاخصه های آن عبارتند از:
ورق فولادی از نظر آلیاژی تقسیمات متنوعی دارد و مهمترین انواع ورق فولادی مصرفی در صنعت قوطی سازی و ظروف فلزی عبارتند از:
1- نوع MR: این نوع فولاد دارای مقاومت خوبی در برابر خوردگی (Corrosion) دارد و ناخالصی در آن به حداقلی است. برای مصارف عمومی از این ورق استفاده می شود.
2- نوع L: برای بسته بندی محصولات غذایی خورنده بکار می رود. در این نوع فولاد سایر عناصر نظیر فسفر، سیلیکون، نیکل، کروم و مس به حداقل مقدار محدود می باشد.
3-فولاد MC: در این نوعن فولاد مقادیر بیشتری از فسفر نسبت به فولاد نوع L وجود دارد.
4- نوع D: این نوع که در اثر گذشت زمان نیز خصوصیات خود را حفظ می کند (Non aging) توسط آلومینیوم آرام می شود. (Aluminium Killd) و به منظور بهبود خصوصیات کشش پذیری پروسس می شود.
ضمناً باید توجه داشت که ورق های نوع SR (Single reduced) دارای سختی کمتر. و مقاومت بیشتر و ورق های نوع DR (Double reduced) دارای سختی بیشتر و ضخامت کمتر می باشند.
ب- ضخامت (Tickness)
در ساخت قوطی و حلب فلزی معمولاً از ورق های حلب به ضخامت 0.18 تا 0.32 میلیمتر استفاده میشود. البته در خطوط مدرن مجهز به بیدر (خط انداز) از ورق های نازکتر به ضخامت 0.16 میلیمتر استفاده می شود.
پ- یکنواختی (Monotony)
ورق حلب می بایست کلیه سطوح آن کاملاً یکناخت باشد
ت- پوشش قطع (Tin coating)
سطح ورق می بایست با روش های بسیار دقیق قلع اندود گردد. پوشش قلع بسته به مورد مصرف ورق متفاوت است. حداقل استاندارد اندود قلع در هر روی ورق برای تولید قوطی در سیستم متریک 2.8gr/m2 و حداکثر 11.2gr/m2. و در سیستم اینچی حداقل 0.25LBS و حداکثر 1LBS است.
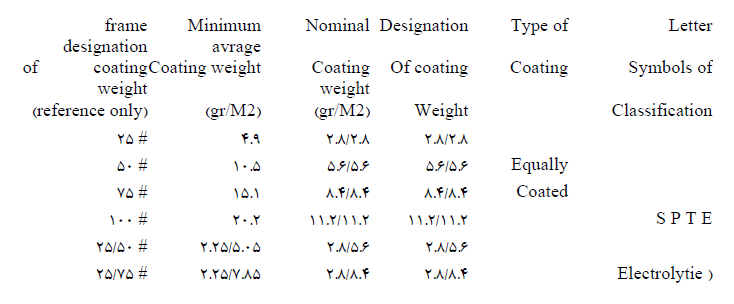
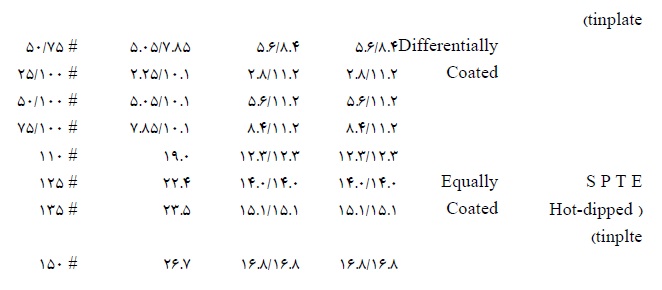
مناسب ترین و اقتصادی ترین پوشش قلع جهت ورق حلب برای ساختن قوطی کمپوت. و کنسرو 5.6/2.8gr/m2 و یا معادل آن در سیستم اینچی می باشد.
ت-سختی (Temper)
میزان سختی مورد نیاز ورق بر حسب سیستم تولید قوطی متفاوت است. مثلاً در خطوط قوطی سازی یا سیستم اروپائی از ورق T3 و با سیستم آمریکائی از ورق T5 استفاده می شود. ضمناً ماشین آلات قوطی سازی در ایران کلاً سیستم اروپائی است. لذا به ایران ورق حلب با سختی 3 (T3) وارد می شود.
جدول سختی ورق تین پلیت
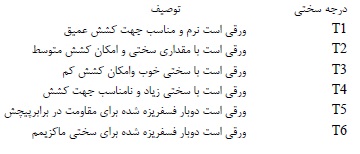
2- سیم مسی
مفتولی است مسی با خلوص بالا به قطر 1.38 یا 1.5 میلیمتر که در سیستم درز جوش مورد استفاده قرار می گیرد.
3- لحیم
آلیاژی است از سرب و روی که جهت دوخت بدنه قوطی مورد استفاده قرار می گیرد.
4- مایع لاستیک
به منظور جلوگیری از نشت محتوی از درون قوطی از موادی موسوم به مایع لاستیک استفاده می شود. جنس مایع لاستیک با توجه به نوع محتوی قوطی تعییم می گردد. متداولی که بدین منظور استفاده می شوند. شامل لاتکس، لاستیک مصنوعی و پلاستیک های نرم می باشد. این پوشش معمولاً دور کف و یا در قوطی قرار می گیرد.
مواد لازم جهت پوشش قوطی
در صورت لزوم جهت پوشش داخل و یا خارج قوطی (بر حسب مورد) از مواد ذیل استفاده می شود.
الف- لاک (Laquer)
نظریه اینکه بسیاری از موادی که در بسته های فلزی بسته بندی می شوند. بسیار فعال هست و در مدت زمان کوتاهی با عدل ها واکنش نشان می دهند. و سبب خوردگی می گردند، لذا با قرار گیری یک لایه نازک بین عدل و محصول مانع این کار می شوند. بدیهی است این لایه برای محصولات مختلف متفاوت است تا از ترکیب احتمالی محصول با لایه محافظ، جلوگیری گردد.
لاک مصرفی جهت قوطی های مواد غذائی عبارت است از محلول رزین یا ترکیبی از رزین و روغن هایی که خشک می شوند. در حلال های فرار شیمیایی که پس از پختن به صورت لایه ای سخت بر روی ورق باقی می ماند.
لاک از نظر کاربرد به دو گروه تقسیم می گردد.
1- لاک خارجی : جهت حفاظت قوطی از زنگ زدگی در مناطق مرطوب و یا برای تزئین بکار می رود.
2- لاک داخلی: این نوع لاک به منظور جلوگیری از بروز واکنش شیمیائی بین محتوی و فلز می باشد. که بر حسب نوع محتوی دارائی ویژگی های مختلفی است. متداولترین لاک های مصرفی در ایران عبارتند از:
الف- لاک سفید (White laqure) این لاک با پایه های مختلف شیمیائی تولید می گردد. و دارای مقاومت زیاد در مقابل مواد با خوردندگی بالا مانند رب گوجه فرنگی می باشد.
ب- لاک آلومینیوم پیگمنت (Aluminium pigment laquer). بطور کلی برای پوشش سطح داخلی قوطی مواد گوشتی و تن ماهی (مواد پروتئینی). از این نوع لاک که به رنگ خاکستری است استفاده می شود.
پ- لاک بژ (Beig laquer) این لاک دارای مقاومت خوب در مقابل مواد با خورندگی بالاست. که در بخش های بعدی در مورد لاک توضیحات بیشتری خواهد آمد.
ب- پودر درز جوش:
در اثر جوشکاری درز قوطی در سیستم (Seam welding) روکش قلع روی ورق از بین می رود و فلز در موضع مذکور ضعیف می شود. این محل با پودری که پس از پخت بصورت نواری روی آنرا می پوشاند پوشش دهی می شود. پودر انتخابی می بایستی با لاک نشانده شده روی ورق هم خانواده باشد تا کشش مولکولی مناسبی فراهم گردد.
پ- تینر (Tiner):
از آن به عنوان یک حلال استفاده می شود و فرمول آن می بایست با لاک مربوطه هماهنگی داشته باشد.
ت- مرکب (Ink):
از آن جهت چاپ روی قوطی استفاده می شود
روش های تولید:
همچنانکه قبلاً بیان شد از نظر تکنولوژی ساخت، قوطی غذائی به دو گروه قوطی های کششی و درز دار تقسیم می گردند.
الف- قوطی کششی:
این نوع قوطی شامل دو قسمت است بدنه و در، نحوه تولید بدین قرار است.
1- بدنه: ابتدا ورق لاک می خورد و در صورت لزوم چاپی با قیچی های گیوتینی به ابعاد مورد نظر برش می خورد. و سپس قطعات حاصله (بلانک ها) در دستگاه تغذیه پرس (فیدر) قرار می گیرد. به توسط فیدر ورق به داخل قالب ارسال می گردد. و عمل ساخت بدنه و فلنج لبه بالائی با هم انجام می گردد. بدنه تولیدی در کارتن قرار می گیرد و به انبار منتقل می شود.
2- در: ابتدا ورق لاک می خورد با قیچی گیوتینی به ابعاد مورد نظر برش می خورد. (در واحدهای بزرگ جهت صرفه جوئی در مصرف ورق حلب عمل برش با قیچی زیگزاک انجام می شود). بلانکهای حاصله در دستگاه تغذیه (فیدر) قرار می گیرد و توسط آن به داخل قالب هدایت می شود. پس از انجام پرس، در تولیدی ه به داخل دستگاهی به نام کرلر هدایت می شود. و سپس توسط کارگر به فیدر دستگاه زننده مایع لاستیک منتقل می شود. توسط این دستگاه مایع لاستیک به داخل شیار دور در می چسبد. و بر حسب آنکه مایع لاستیک هوا خشک باشد و یا نیازمند به کوره به روش مناسب این مایع خشک میشود. و سپس در قوطی، در کارتن قرار می گیرد و به انبار ارسال می شود.
ب- قوطی درز دار:
این نوع قوطی شامل سه قسمت است بدنه، در و کف.
1- بدنه: ابتدا ورق لاک می خورد و احتمالاً چاپی توسط قیچی های رول بر به ابعاد مورد نظر برش می خورد. بلانکهای حاصله در قسمت فیدر ماشین بدنه ساز قرار می گیرد. و به توسط آن بطور خودکار به داخل ماشین ارسال می گردد. بلانک ابتدا لول می شود. و سپس به یکی از روش های عبور از وان لحیم و یا درز جوش با سیم مسی، درز آن دوخت می شود.
سپس به وسیله ماشین پودر پاش پودر درز جوش روی محل جوش می شود و پاشش می شود. و با عبور از کوره این پودر پخت می شود و بصورت نواری روی محل جوش را کاملاً می پوشاند. پس از آن لبه های بالا و پائین بدنه توسط ماشین فلنجر، فلنج می شود. و سپس کف قوطی توسط ماشین سیمر به بدنه قوطی وصل می شود. بدنه آماده شده در کارتن گذاشته شده و به انبار منتقل می گردد. کلیه این مراحل بصورت اتوماتیک و پیوسته انجام می شود.
2- در و کف: در و کف قوطی کاملاً مشابه یکدیگر و سیستم تولید همان است که در مورد در قوطی کششی توضیح داده شده. لازم به توضیح است امروزه جهت کاهش تمام شده قوطی در کارخانجات مدرن. معمولاً جهت تولید در و پا کف از قالب دوبل استفاده می شود. و در زمینه ساخت بدنه نیز از ماشین های پارتینگ و بیدینگ استفاده میشود. بدین مفهوم که بلانک ها به طور دو برابر بریده می شوند. لذا پس از جوش و پودر درز جوش بدنه توسط ماشین پارتینگ بریده و تبدیل به دو عدد می گردد. ضمن آنکه ماشین بیدینگ روی بدنه خط می اندازد و بدین ترتیب هم سرعت ماشین افزایش می یابد. و هم از ورق نازکتر جهت ساخت بدنه استفاده می شود. و استحکام لازم توسط خطوط ایجاد شده روی بدنه تأمین می گردد.
در مورد قوطی نوشابه دو سر بدنه ابتدا توسط ماشین نکر قدری جمع می گردد. (محل قرار گرفتن نکر قبل از بیدر است) و پس از آنکه کف پا در قوطی بسته شد. مجدداً داخل قوطی لاک زده می شود. که این لاک با عبور قوطی از کوره مربوطه خشک میشود و بعد از آن بدنه قوطی کارتن می شود و به انبار منتقل می گردد.
روش های دوخت بدنه:
برای دوخت بدنه قوطی های درز دار از روش های مختلفی برحسب مورد مصرف قوطی استفاده می شود که عبارتند از:
الف- سیستم درز کوب (Side seamer)
در این روش دو لبه ورق بدنه به هم قلاب شده و سپس کوبیده می گردد. این روش ابتدائی بوده و برای قوطی های غیر غذائی که محتوی آن مایع غلیظ (مثل رنگ) و یا جامد باشد استفاده می گردد.
ب- سیستم لحیم (Soldering)
در این سیستم لحیم به روش های مختلف دستی (با هویه). نیمه خودکار (روش چند شاخه) و خودکار (وان لحیم) جهت دوخت درز بدنه قوطی مورد استفاده قرار می گیرد.
پ- سیستم چسب (Cementing)
درز بدنه با چسب مخصوص به یکدیگر متصل می گردد. این روش فقط در موارد خاص استفاده می شود.
ث- سیستم درز جوش (Seam welding)
در این روش مفتول مسی با روش جوش با مقاومت الکتریکی (Electrical Resistance Welding) ERW باعث جوش درز قوطی می گردد. در این روش سیم مسی، مصرف نشده و فقط تغییر فرم می دهد.
وضعیت استاندارد:
قوطی غذائی در کشور مشمول استاندارد اجباری است و استانداردهای مربوطه به شرح ذیل می باشد:
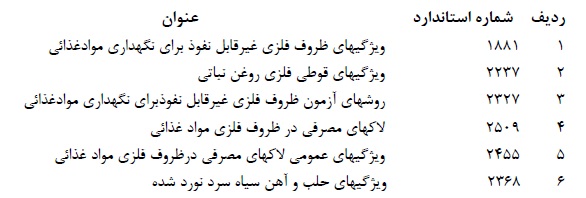
اضافه می شود چون سالها از زمان تدوین استاندارد قوطی می گذرد. اخیراً اقداماتی در جهت بازنگری و تجدید نظر در آن بعمل آمد. از جمله، چندین جلسه با حضور متخصصین مربوطه در مؤسسه استاندارد تشکیل شد.
انواع ورق های تولید قوطی:
بطورکلی در صنعت قوطی سازی چندین نوع ورق از جمله ورق قلع اندود، ورق بدون قلع و ورق آلومینیوم مورد استفاده قرار می گیرد. با توجه به اینکه مصرف سالیانه ورق قلع اندود و بدون قلع در کشورمان بیش از 250000 تن در سال است. و تولید شرکت فولاد مبارکه (تنها تولید کننده این نوع ورق) کمتر از 100000 تن در سال می باشد. سالیانه بیش از 150000 تن از این ورق در ضخامت های مختلف وارد کشورمان می شود.
بخشی از ورق های وارداتی از کشورهای اروپایی و ژاپن و بخش دیگری نیز از کشورهای روسیه و آسیای میانه وارد کشورمان می شود. که متأسفانه کیفیت ورق قلع اندود وارداتی از کشورهای روسیه و آسیای میانه بسیار پایین است. و مصرف آن ضایعات زیادی به بار می آورد. تولید ورق قلع اندود در شرکت فولاد مبارکه چندی است که به صورت انبوه تولید می شود. که کیفیت آن نسبت به انواع ورق های قلع اندود وارداتی از کشورهای روسیه و آسیای میانه بهتر است.
از آنجایی که شرکت فولاد مبارکه که این نوع ورق را فقط در یک و یا دو گرید تولید می کند. بنابراین مصرف آنها در خطوط تولید پیشرفته قوطی سازی امکان پذیر نیست. سایر مواد اولیه مصرفی از جمله لاک های غذائی و غیر غذایی برای تولید قوطی های سه تکه مناسبند. ولی برای بعضی از محصولات (از جمله انواع درب ایزی اپن، انواع درب پیل اف. درب شیشه، قوطی های کششی و یا قوطی های تخصصی) قابل مصرف نیستند. انواع مرکب چاپ نیز در داخل کشور تولید می شوند. ولی برای مصارف قوطی سازی هنوز بصورت یقین قابل مصرف نیستند. و باید در این زمینه تحقیقات بیشتری انجام شود. سایر مواد اولیه مصرفی بخشی مانند (سیم مسی، مایع لاستیک، انواع تینر و غیره) در کشور تولید می شوند.
و قسمتی نیز وارداتی هستند. مانند پودر درز جوش، انواع مرکب چاپ، انواع مواد کمکی چاب و غیره. بطور کلی می تواون گفت که صنایع تولید کننده مواد اولیه، لوازم و تجهیزات قوطی سازی پیشرفت های خوبی داشته اند. ولی با توجه به تحولات تکنولوژیک در سطح بین المللی در کوتاه مدت، نیاز است. که سرعت بسته بندی فلزی و چاپ روی فلز به پای این صنایع پیشرفت کند. در غیر اینصورت تأمین کلیه مواد و لوازم مصرفی فقط با واردات امکان پذیر خواهد بود.
همچنین با توجه به تنوع تولید محصولات از جمله قوطی فلزی، درب ایزی اپن، درب شیشه و غیره. که میبایست مواد اولیه متفاوتی جهت تولید آنها به کارگیری می شد. تهیه و خرید این نوع مواد بسیار دشوار خواهد بود. چرا که قسمتی از آنها-که شامل حقوقق و عوارض گمرکی ورودی بسیار بالا هستند. وارداتی و جزو کالاهای تخصصی محسوب می شوند.
اغلب مواد مذکور دارای عمر مصرف کوتاه بوده و غیر قابل نگهداری به صورت طولانی بصورت طولانی مدت هستند. بدیهی است که بیش از 70% مواد اولیه مصرفی صنعت بسته بندی فلزی (قوطی سازی) وارداتی است. بنابراین حجم عظیمی از نقدینگی جهت تولید مستمر و ارایه محصولات با کیفیت ممتاز مورد نیاز خواهد بود. در این میان کمک مالی بانک ها بسیار ضروری به نظر می رسد.
فرآیند تولید قوطی فلزی با استفاده از ورق قلع اندود
تولید قوطی کنسرو از ورق قلع اندود در ایران برای نخستین بار در سال 1309 شمسی توسط شخصی به نام درخشان صورت گرفت. او که از مهاجران ساکن شوروی بود پس از انقلاب اکتبر به ایران بازگشت و چون تحصیل کرده مدرسه آشپزی مسکو بود. با استفاده از تجارب خود، اولین کارگاه ابتدایی قوطی سازی در ایران را راه انداخت.
بسته بندی
او با استفاد از پیت های خالی بنزین شرکت نفت و مسطح کردن آن ها با دست. ورق تولیدی را از داخل قلع مذاب عبور داد و از آن ها قوطی می ساخت. در سال 1336 شمسی ورق لاک اندود و قوطی آتولیدی از خارج وارد ایران شد. و در سال 1344 لاکزنی اتوماتیک امروزی در ایران برای نخستین بار نصب و مورد بهره برداری قرار گرفت. اگرچه در مجموع عمر قوطی سازی در ایران از 75 سال تجاوز نمی کند. در مقایسه با عمر این صنعت در جهان (حدود 180 سال) قابل تأمل است.
با روش های نخستین، یک کارگر خوب و ماهر، چهار قوطی در هر روز تولید می کرد. این در حالی است که امروزه سرعت تولید خطوط قوطی سازی پیشرفته حتی به بیش از هزار قوطی در دقیقه می رسد. در طول سالهای پس از پیدایش صنعت قوطی سازی تغییرات بسیاری در ماشین آلات و دانش این فن آوری ایجاد گردید. و همواره شاهد پیشرفت و صمع اخبار جدید در این زمینه هستیم.
افزایش سرعت تولید به بیش از یک هزار قوطی در دقیقه. افزایش استحکام قوطی ها به وجود آمدن اشکال و اندازه های متنوع. استفاده از تزئینات چاپی بر روی قوطی و ابداع درهای متنوع موسوم به راحت باز شو (Easy Open) در آنها. در کنار کاهش وزن قوطی شاخص های اصلی روند پیشرفت قوطی سازی به شمار می آیند.
روش های تولید قوطی فلزی از جنس ورق قلع اندود:
تولید قوطی کنسرو از جنس ورق قلع اندود، بر خلاف تصور عموم که آن را آسان می دانند. مستلزم دانستن بسیاری از مهارت های نوین و فن آوری های روز است.
دقت و ابعاد قطعات در تجهیزات و ماشین آلات تولیدی تابع تولرانس هایی در حد چند میکرون است. که این صنعت را در گروه صنایع دقیق جای می دهد. مهمترین انواع قوطی، قوطی فلزی غذایی یا غیر غذائی به صورت دو تکه یا سه تکه هستند.
الف- قوطی سه تکه (Piece can-3)
1- قوطی با بدنه درز جوش: بدنه قوطی بعد از رول شدن. با روش جوشکاری الکتریکی مقاومتی Electrical Resistance Welding (ERW) به صورت سیلندر در می آید.
2- قوطی با بدنه درز جوش لیزری
3- قوطی با بدنه درز لحیمی (این روش بعلت آلودگی ناشی از آلیاژ لحیم کاری دیگر استفاده نمی شود)
4- روش های دیگری نیز برای دوخت درز بدنه قوطی وجود دارد که در کشور ما متداول نیست.
ب- قوطی دو تکه (2-Piece can)
1- قوطی دو تکه (Drawn & Wall Ironed can) DI قوطی های دو تکه بلند. که در اثر عملیات و اتو شدن ورق در قالب کشش شکل می گیرد و کف و بدنه آنها از یک جنس است.
2- قوطی دو تکه کششی، قطی های دو تکه با عملیات کشش با نسبت کشش کم تر. و جریان مواد به داخل قالب تولید می شود. و بدنه و کف قوطی از یک جنس هستند.
مراحل تولید قوطی سه تکه
1-لاک اندود کردن ورق قلع اندود در خط لاک زنی
2- برش قطعات بدنه قوطی (Body Blank) در دستگاه قیچی دوبل (Dublex Slitter)
بسته بندی
3- تولید سیلندر بدنه قوطی در دستگاه بدنه ساز
4- شکل گیری پوشش درزجوش بدنه از داخل توسط پودر یا لاک به روش الکترواستاتیک جهت حفاظت این قسمت از خوردگی
5- پخته شدن و چسبیدن پودر (یا لاک بیرون درز) به سیلندر بدنه در کوره مخصوص (Seam Coating Curing Oven)
6- انجام عملیات: تقسیم بدنه (Parting)، کنگره ای کردن (Beading). تغییر شکل سطح مقطع قوطی، برگشت لبه بدنه (Flanging)، دوخت کف به بدنه (Seaming). که یک یا چند مرحله و در یک یا چند ماشین با توجه به نیاز و نوع تجهیزات به کار گیری شد. در پایان عملیات تولید صورت می پذیرد.
مرحله تولید قوطی دو تکه
1- لاک اندود کردن ورق قلع اندود در خط لاک زنی
2-برش ورق های بدنه به شکل زیگزاگ یا ساده و یا بدون برش در روش تغذیه ورق (Sheet Feading)
3- تغذیه ورق قلع اندود به داخل پرس و تولید قوطی دو تکه کششی با لبه برگشتی در پرس مخصوص. که عملیات کشش و باز کشش (Draw & Redraw)، برش زواید (Trimming). و برگشت لبه ها در آن یکجا انجام می شود.
اغلب خطوط قوطی سازی در ایران در طول دهه اخیر با انواع ماشین آلات جدید و مدرن تجهیز شدند. گرایش به استفاده از ورق های قلع اندود نازک تر جهت صرفه جویی در مصرف مواد اولیه. از مشخصه های اصلی این خطوط محسوب می شود. کاهش ضخامت ورق ها در کنار افزایش سرعت تولید، مستلزم رعایت هر چه بیشتر محدوده های کیفی مختلف مورد نیاز. در تولید مواد اولیه، مخصوصاً ورق های قطع اندود است.
گفتنی است که طرح چاپی روی قوطی های دو تکه کششی با نرم افزار مخصوص طراحی می شود. در این نوع قوطی ها طرح چاپی روی ورق پس از کشش شکل اصلی خود را پیدا می کند. شرکت اسپانیایی لاجی تک از جمله مراکزی است که این سرویس را انجام می دهد. و بسیاری از شرکت های ایرانی طرح خود را به آنجا سفارش می دهند.
نکات مورد توجه و مشکلات و محدودیت های مربوط به ورق قلع اندود در صنعت قوطی سازی به طور مختصر به صورت زیر است:
1- مشخصات ورق مصرفی پیشنهادی از سوی سازنده ماشین در دستگاه های بدنه ساز قوطی. مخصوصاً دستگاه های با سرعت بالا لازم است به دقت رعایت شود.
2- رعایت جهت نورد (Rolling Direction) در خطوط تولید بدنه قوطی با روش جوشکاری مقاومتی الزامی است.
3- عدم رعایت تولرانس های ابعادی در یک باندل ورق، عملیات لاک زنی و ایجاد نوار دقیق بدون لاک (Margin). و برش قیچی بدنه را دچار اشکال سازد.
4- عملیات برگشت لبه ها برای ورق های با سختی بیشتر از حد معین با روش چرخشی (Spin Flanging) انجام می شود. در حالی که این عملیات برای روق های با تمپر و سختی کم با روش حدیده ای (Die Flanging) صورت می پذیرد. هزینه قطعات و تجهیزات روش چرخشی به مراتب بیشتر از روش دوم است.
بسته بندی
رفتار برگشت فنری ورق (Spring Back) در شرایط یکسان از نظر قطعات و ماشین آلات تولید. با تغییر در سختی ورق تغییر نموده و فاکتورهای دوخت قوطی به عنوان اساسی ترین عامل کیفی محصول تغییرات آشکار می نماید.
پروفیل قطعات مورد استفاده جهت ایجاد کنگره (Bead) در بدنه قوطی ثابت است. و تغییرات سختی ورق، در میزان عمق این کنگره ها و در نتیجه ممان اینرسی حاصله. و مقاومت در برابر فشارهای داخلی قوطی که پر است، تأثیر چشمگیر دارد.
5- اغلب ماشین آلات صنعت قوطی سازی در ایران با ورق (Sheet) قلع اندود تغذیه می شود. و به علت فقدان امکانات لاک و چاپ کلاف (رول) در کشور این نوع محصول مورد مصرف مستقیم قرار نمی گیرد.
6-قلع: تحقیقات نشان می دهد افزایش قلع مستلزم افزایش جریان جوشکاری است. تغییرات خارج از حدود استاندارد، از کیفیت جوش درز بدنه و مقاومت آن در برابر فشارهای مختلف ناشی از فرآیند مواد غذایی کاست.
آگرچه پوشش قلع در اصل جهت افزایش مقاومت ورق در برابر خوردگی. قابلیت جوشکاری و لحیم کاری و لاک کاری و ایجاد ظاهری خوشایند، بر ورق پایه به کار می رود. تجارب حاصله نشان می دهد. که وجود قلع همچنین سایش قطعات تولید را کاهش و شکل پذیری ورق را افزایش می دهند و بهبود می بخشد. افزایش قلع اگرچه عامل اصی افزایش قیمت نهایی ورق محسوب می شود. و با جریان جوش رابطه معکوس دارد. ولی در قوطی های کششی و فرآیند اتوکاری نقش مفید و مستقیم دارد.
بسته بندی
از پدیده هایی که در مورد قلع ورق ها قابل ذکر است اتصال ذرات قلع به صورت جوش سرد به قطعات تولیدی است. این ذرات در طول زمان به قطعاتی که وظیفه شکل دهی ورق را به عهده دارند. متصل می شوند که لازم است زدوده شوند. قطعاتی مانند طبق های دوخت (Seaming Chuck)، قرقره های دوخت (Seaming Rollers) و رولرهای بدنه ساز در معرض این مشکل واقع می شوند.
7- غیرفعال کردن (Passivation): این کار جهت افزایش مقاومت سطح ورق در برابر اکسیداسیون و ارتقای کیفیت لاک کاری و چاپ صورت می گیرد. دور روش برای غیرفعال نمودن متداول می باشد. در روش 311 محلول دی کرومات سدیم به صورت کاتدیک بر روی ورق نشانده می شود. عمده سازندگان از این روش بهره می گیرند. روش 300 که با قرار گیری ورق در محلول کرومات سدیم به آسانی انجام می شود. بعلت آلودگی محیط زیست، در کشورهایی که آلودگی محیط زندگی و آب و خاک از اهمیت بالایی برخوردار است، دیگر مورد توجه نمی باشد.
8- روغن کاری (Oiling): با مراجعه به دستورالعمل های بهداشتی صنایعی که با ورق قلع اندود سروکار دارند. تنفس و تماس مستمر با ذرات و گازهای ناشی از فرایندهای مختلف تولید و شکل دهی این گونه ورق ها با عملیات جوشکاری. گداختن، برش، سنگ کاری و ماشین کاری، به خاطر وجودو ذرات کربن، کروم، آهن، منگنز، نیکل. سیلیکون و قلع مستلزم رعایت نکات ایمنی و تمهیداتی است تا عوارض کم تری به بار آورند. از جمله مواردی که در کاهش ذرات گرد و غبار ناشی از عملیات بر روی ورق های قلع اندود مؤثرند. استفاده از روغن های مجاز و مناسب برای صنایع غذایی است که در این مرحله به کار می رود. این روش از جذب رطوبت محیط نیز جلوگیری می کند.
مقادیر روغن و توزیع یکنواختی و عمر آن اهمیت به سزایی در کیفیت لاک کاری و عملیات پوشش دهی ورق دارد. بهتر است این روغن با روش های متعارف قبل از ورود به مراحل پشش دهی، کنترل و تحت بررسی قرار گیرد. بعضی از این روشها بدین ترتیب است:
الف- تست شکست آب (Water-Break test): آسان ترین روش برای اطمینان از وجود روغن بر روی ورق محسوب می شود.
ب- تست به روش الیپسومتر (Ellipsometer): معمول ترین روش برای تعیین ضخامت روغن می باشد. که به کمک دستگاهی به همین نام بر مبنای اصول اپتیکی انجام می گیرد.
ج- تست به روش سکسله (Soxhlet Method): در گذشته روش اصلی تعیین صخامت روغن. بر روی ورق قلع اندود به حساب می آمد. و در حال حاضر با روش های آسان تر و سریع تر جایگزین گردید. این روش در استاندارد ASTM 623 تشریح گردید. و اساس آن بر پایه برداشتن روغن از سطح معینی از ورق به کمک یک حلال جوشان. مانند کلروفورم و اندازه گیری روغن به جای مانده پس از تبخیر این حلال است.
9- بسته بندی ورق قلع اندود:.عدل بندی نامناسب و قابلیت نفوذ رطوبت محیط تا زمان مصرف به همراه نفوذ پذیری شدید. ناشی از خاصیت کششی سطحی موجود بین ورق ها، خسارت جبران ناپذیری به این تولید صنعتی وارد می سازد.
روشهای جدید در صنعت قوطی سازی
با توجه به اینکه قوطی فلزی غذایی از نظر حفظ کیفیت محتوای خود از جمله ویتامین ها. پروتئین ها و سایر مواد جزو بهترین نوع بسته بندی به شمار می آید. و امکان نگهداری محصول با بیش از دو سال تاریخ مصرف وجود دارد.
و قابل بازیافت به صورت مستقیم و غیر مستقیم می باشد. بنابراین تا کنون هیچ نوع بسته بندی دیگری نتوانسته است. جایگزین قوطی فلزی شود. به همین علت تحولات در این نوع صنعت از جمله قوطی سازی روند صعود دارد. و از نظر تکنولوژیک پیشرفت های قابل ملاحظه ای را تجربه کرده است.
در کشورمان نیز همین روند از بدو ایجاد تولید انواع قوطی های فلزی مشاهده گردید. به نحوی که در گذشته از قوطی های فلزی با حجم بیشترو با سیستم درز لحیمی استفاده می شد. ولی از چندین سال قبل تاکنون از قوطی های فلزی با حجم کمتر و یا سیستم درز جوش استفاده می شود. علت تغییر درز لحیمی به درز جوش، تغییر تکنولوژی تولید در 25 سال اخیر بودهو علت کاهش حجم قوطی ها. کاهش توان خرید مصرف کننده نهایی و همچنین روند صنعتی شدن جامعه است.
صنعت قوطی سازی در ایران از زبان یکی از فعالان صنعتی در این زمینه
صنعت قوطی سازی از نظر تنوع تولید و چاپ، طی یک دهه اخیر پیشرفت محسوسی داشته است. علاوه بر دستاوردهای تکنولوژیک ارتقای سلیقه عمومی در جامعه و آگاهی نسبت به انواع بسته بندی ها نیز. رقابتی آن در بازار از جمله عوامل پیشرفت بسته بندی های فلزی بوده است.
(برای مثال قوطی های روغن خوراگی که چند سال پیش به صورت چاپ تک رنگ یا دو رنگ و بدون ورنی به بازار می رفت. حالا با چاپ چهار رنگ و حساسیت از نظر رنگ و طراحی و کیفیت چاپ تولید می شوند).
صنعت قوطی سازی در حال نوسازی است. با توجه به رشد قابل توجه عدل بندی مقوایی و کارتن، انتظار می رود. که بسته بندی های فلزی نیز پا به پای آنها رشد کنند. اما در این صنعت، به خاطر سنگینی حجم سرمایه گذاری، حرکت قدری کندتر است. و البته کاستی های صنعت قوطی سازی تنها به مشکل سرمایه گذاری محدود نمی شود.
بسته بندی –مشکلات تولید و چاپ قوطی
بر اساس تجربه چند ساله و ارتباط نزدیک با مسائل اجرایی تولید قوطی. می توانم جمع بندی زیرا را از مسایل و مشکلات این صنعت ارایه دهم.
1- فقدان نیروی ماهر و متخصصانی که ضمن تجربه حرفه ای، فرصت حضور در دوره های آموزشی و کسب دانش فنی را دارا باشند.
2- نداشتن ارتباط با دنیای قوطی سازی و منزوی ماندن صنایع ما در عرصه جهانی. به طوری که انتقال دانش فنی و تجربه و نیز تأمین لوازم و تجهیزات و مواد مصرفی مطلوب را با دشواری مواجه می سازد.
3- پایین بودن قیمت قوطی سازی و چاپ فلز: در حالی که سلیقه مشتریان ارتقاء یافت. و کیفیت قوطی را از نظر شکل، لاک و چاپ آن، در حد بالایی انتظار دارند، آمادگی لازم برای پرداخت هزینه های آن را ندارند.
4- فقدان مؤسسات پژوهشی و اطلاع رسانی مستقل و کارآمد نیز به نوبه خود کاستی هایی را در صنعت موجب می شود.
متأسفانه مراکز و سازمان های انگشت شماری که کم و بیش با این صنعت ارتباط دارند. فاقد ظرفیت ها و کارآیای لازم هستند.
5- برنامه ریزی واوحدهای قوطی سازی به طور معمول تابع میزان تولید و نوع محصولات کارخانجات مواد غذایی است. تحولات اقتصادی و افت و خیزهای تولید در این محصولات، موجب اخلال در برنامه ریزی می شود.
6- عدم تطابق تولید ورق داخلی با نیازهای کارخانه های قوطی سازی. ورق تولیدی توسط فولاد مبارکه به خاطر بعضی طرح ها و خطوط که در سطح آن است. و چرب بودن آن از طرفی و نیز درجه سختی نامناسب برای قطوی سازی اتوماتیک، پاسخگوی نیاز ما نیست.
حتی در صورت بهبود کیفیت محصول و رشد به سطح تولید اسمی، باز هم تولید فولاد مبارکه کفایت مصرف ورق را نمی کند. و واردات آن، ضروری است.
7- دشواری بیش از پیش در بازار جهانی برای تأمین ورق طی دو، سه سال اخیر از طرفی قیمت جهانی ورق افزایش یافت. و از طرف دیگر به دلیل خریدهای عمده چین، بازار وضعیت خاصی پیدا کرده است. چین به خاطر مصرف چشمگیر ورق های فلزی و تین پلیت، تولید یکی، دو سال آینده. چند کارخانه را پیش خرید کرده و اکنون تأمین ورق کار آسانی نیست.
در حالی که برای یک کارخانه قوطی سازی بسیار اهمیت دارد. که بداند چه مقدار ورق را در چه ابعاد. و با چه مشخصاتی و در چه زمانی تهیه کند، ما در واقع حق انتخاب چندانی در این زمینه نداریم.
تغییر ذائقه مصرف کنندگان
بازار مصرف بسته بندی های فلزی از چند جهت دستخوش تغییر بوده است.
بسته بندی های بزرگی برای مواد غذایی، جای خود را به قوطی های کوچک تر می دهد. برای مثال در سال های گذشته، خانواده ها روغن را در قوطی های 17 کیلویی می خریدند. ولی امروزه اغللب بسته بندی های یک کیلویی را ترجیج می دهند. هرچند که قوطی های بزرگ تر همچنان مورد نیاز هستند.
بخاطر زندگی مدرن و اشتغال اعضای خانواده، مصرف غذای نیم پخت بیشتر گردید. که به نوبه خود به افزایش بسته بندی های از جمله انواع قوطی و کنسرو می انجامد. برای مثال چند سال پیش ما فکر نمی کردیم. مایه ماکارونی را آماده در یک طرف از فروشگاه بخریم. ولی به مرور زمان این گونه محصولات در کشور ما زیاد می شوند.
قوطی های فانتزی کاربرد بیشتری می یابند (مثل جامدادی و …) که به خاطر تیراژ کم، به طور معمول در کارگاه های کوچک تولید می شوند. البته نوعی از قوطی ها هم برای گز و کالاهای مشابه مصرف می شوند. که به خاطر حساسیت در نوع جعبه و برجسته سازی سطح آنف در ایران تولید نمی شوند. (برای مثال قوطی گز سکه در ترکیه تولید می شود).
امکانات قوطی سازی های ما برای تولید جعبه های لوکس، محدود است. در صورت وجود تقاضا، صاحبان این صنعت نیز انگیزه سرمایه گذاری پیدا میکنند. اما به هر حال قوطی های لوکس، بازار محدودی دارند. شاید برای محصولی مثل گز استفاده از چنین بسته هایی مناسب باشد. ولی برای محصولی مانند رب گوجه فرنگی که بهای محتوی آن 50 تومان است، استفاده از یک قوطی 150 تومان توجیه پذیر نیست.
موارد بالا در مورد بازار جهانی و ایران تقریباً به یکسان صادق بود. تنها مورد اختلاف در مورد استفاده از قوطی های فلزی برای نوشابه است که در ایران تولید نمی شود. و تنها تعداد محدودی توسط برخی نوشابه سازها استفاده می شود که آن هم وارداتی است. یعنی قوطی های خالی به صورت چاپی وارد می شوند و فقط در اینجا پر می شوند. بنابراین هزینه آنها بالا است و در مقایسه با نوشابه های مورد ارائه در ظرف های پت، گران تر تمام می شوند.
مصرف کنندگان اروپایی به تدریج با احساس مسؤولیت نسبی بر حفظ محیط زیست، استفاده از تین پلیت. و قوطی های فلزی را به ظرف های پلاستیکی ترجیج می دهند. و حتی حاضرند بهای آن را بپردازند. اما در ایران به خاطر قدرت خرید پایین، نوشابه قوطی مورد استقبال قرار نمی گیرد. و البته محیط زیست به طور دایم با بطری های پلاستیکی مملو می شود.
مشکل دیگر در این ارتباط با سرمایه گذاری هنگفتی است که خط تولید قوطی نوشابه لازم دارد. بدیهی است که برخی کارخانه های قوطی سازی مطالعاتی در زمینه ایجاد خط تولید قوطی نوشابه انجام دادند. اما ضعف قدرت سرمایه گذاری و شرایط بازار مصرف تا کنون اجازه تحقق چنین پروژه ای را نداده است.
کیفیت چاپ قوطی
تنوع قوطی ها بدون پیشرفت در چاپ، نمی توانست موفقیتی در بازار کسب کند. امروز چاپ قوطی ها در مقایسه با پنج، شش سال گذشته بهبود چشمگیری پیدا کردند.
تا هفت سال پیش حداکثر 20 درصد قوطی ها چاپ می شد. آن هم اغلب یک رنگ و دو رنگ و بدون لاک – در حالی که الان حدود 80 درصد قوطی ها چاپ می شود. آنهم چهار رنگ و با ورنی.
هم به دلیل رقابت و هم سلیقه عمومی و هم وارد شدن در بازار صادراتی، حالا سفارش دهندگان قوطی. نسبت به چاپ دقت و کنترل بیشتری دارند.
سالهای پذشته وقتی طرحی برای چاپ به ما می دادند، انتظار داشتند چیزی شبیه به آن و یا نزدیک به آن چاپ کنیم. ولی حالا تأکید می کنند که دقیقاً هم رنگ را می خواهیم و مثلاً لوگو ما با رنگ معین خودش چاپ شود.
در مورد چاپ قوطی یکی از روغن ها، طراح و ناظر چاپ برای تصویر مرغ گریلی، بسیار حساسیت نشان می دهند. که دقیقاً حالت سرخشدگی آن پیدا باشد.
دست اندرکاران صنعت قوطی باید از این دقت ها و سخت گیری ها خوشحال باشند. زیرا همین گرایش باعث ارتقای کیفیت کار آنها می شود.
در پاسخ به این تقاضاهای مشتریان شرکت بسته بندی ایران با تقبل هزینه و صرف وقت بسیار. برای عضی از کارها قبل از چاپ به نمونه گیری و چاپ آزمایش اقدام می کنند. و پس از حصول نتیجه مطلوب و تأیید مشتری، چاپ را شروع می کنند.
به تازگی یکی از شرکت های قوطی سازی فعال در پیشرو در تبریز، دستگه نمونه گیری را نیز در مجموعه خود به کار می گیرند. که روشی مناسب برای نمونه گیری قبل از چاپ است.
با توجه به این که لاک زنی هم یکی از مراحل اساسی تولید قوطی است. ارتقای کیفیت لاک ها نیز اهمیت ویژه ای دارد. وضعیت لاک از نظر سازگاری با محتوای قوطی و قوام آن، از نظر واردات بهداشت و مؤسسه استاندارد نیز بسیار مهم قلمداد می شود.
علی رغم رشد کمی و کیفی لاک های ایراین، متأسفانه در مواردی، لاک های تولید داخل برای کار مناسب نیستند. در چنین مواردی ما ریسک نمی کنیم. و از لاک خارجی استفاده می کنیم. زیرا سرنوشت یک محصول در بازار به کیفیت لاک مربوط می شود.
طی چندین سال رویه شرکت های قوطی سازی، حمایت از سازندگان لاک های داخلی بوده است. اما تا کی می توان با کاستی ها مماشات کرد؟
وقت آن است که تولیدکنندگان لاک- که از بسیاری جهات کیفیت محصول خود را ارتقاء دادند. برای برطرف سازی پاره ای اشکالات محصول خود اقدام کنند.
صنعت چاپ روی فلز
اصولاً نوع و کیفیت بسته بندی هر کالا نشانگر هویت آن کالا می باشد. در این میان چاپ هر نوع بسته بندی اهمیت ویژه ای دارد. که چاپ انواع قوطی های فلزی غذایی و غیره هویت و ارزش کالا را به خریدار ارایه می دهد. چرا که خریدار هر کالا بیشتر تحت تأثیر کیفیت بسته بندی و چاپ آن قرار می گیرد. و بعد از حصول اطمینان از هویت کالا و درک ارزش آن، اقدام به خرید می کند.
با توجه به اینکه صنعت قوطی سازی جزو صنایع قدیمی کشورمان به شمار می رود. بیش از 70% ماشین آلات و تجهیزات کارخانجات قوطی سازی و چاپ مربوط به 25 الی 35 سال پیش می باشد. که در همین راستا واردات ماشین آلات مستعمل در سال های گذشته روند پیر بودن تجهیزات این صنعت را تشدید نموده است.
ولی با توجه به اینکه پتانسیل صنایع فرآوری محصولات کشاورزی و صنایع تبدیلی کشورمان بسیار نامحدود است. و اکثر محصولات غذایی کنسروی، آب میوه و نوشابه و غیره قابل صادرات به کشورها هستند. بنابراین ایجاد ظرفیت های جدید قوطی سازی و چاپ روی فلز امری ضروری است. که در این راستا چندین واحد قوطی سازی برای تهیه و خرید آخرین تکنولوژی موجود صنعت قوطی سازی. و چاپ روی فلز جهت نوسازی هر دو صنعت اقدام کرده اند. حجم این سرمایه گذاری ها قابل توجه بوده و نیاز به حمایت های دولتی و بانکی دارد. چرا که ریسک پذیری این نوع پروژه ها بیش از حد متعارف است.
با ایجاد ظرفیت های جدید در صنعت قوطی سازی، تولید و ارایه محصولات مذکور با کیفیت بهتر. ظرفیت بیشتر، قیمت کمتر و امکان رقابت در بازارهای بین المللی را امکان پذیر می سازد. همچنین با ایجاد ظرفیت های جدید در صنعت چاپ روی فلز به لحاظ پیچیدگی فرآیند تولید. استمرار کیفیت چاپ با استفاده از سیستم های پیشرفته نمونه گیری و کنترل کیفیت تحقق پیدا کرد. به همین علت نیز مصرف کنندگان انواع قوطی فلزی تمایل بیشتری نسبت به مصرف قوطی های چاپدار. به لحاظ کیفیت ممتاز آن و حفظ هویت کالا و عدم امکان تقلب در تولید محصول نشان می دهند.
ورق های مصرفی در قوطی سازی های ایران اغلب وارداتی هستند. در حالیکه لاک و مرکب مصرفی در این صنعت تا حد زیادی از داخل کشور تأمین می شود. شناخت مشخصات فنی این مواد مصرفی و رعایت استانداردها. و دستورالعمل های مربوطه در مرحله لاک زنی و چاپ و نیز پخت آن، می توان به تولید بهتر و ضایعات کمتر بینجامد.
پیش از چاپ
قوطی های تین پلیت یکی از انواع بسته بندی است که کاربردهای متنوعی دارد. درون قوطی ها به طور معمول آنرا با لاک پوشش می دهند. و بیرون آن با چاپ تزیین می شود. چاپ حلب (تین پلیت) به روش افست انجام می گیرد. یعنی زینک های آن در لیتوگرافی تهیه می شود. در گذشته از پلیت های مسی استفاده می شد. اما اکنون پلیت های آلومینیومی مصرف می شوند. ضخامت این پلیت ها 2 میلی متر است. برای چاپ کارهای پر تیراژ، پلیت ها را می سوزانند تا استقامت آنها بیشتر شود.
ماشین چاپ حلب نیز دارای ساختار همانند ماشین های افست چاپ ورقی است. با این تفاوت که حرکت ورق فلزی به صورت مستقیم است و سیلندرها روی آن می چرخند و مانندن کاغذ به دور سیلندر نمی چرخند.
تقاوت دیگر چاپ فلز با چاپ کاغذ و مقوا، حرارت دادن فلز ضمن عبور از کوره های مخصوص است. در اینجا نکات مفیدی درباره مراحل لاکزنی، چاپ و پخت ورق های تین پلیت ارایه می شود.
لاک زنی
لاک نیز از جمله مسایلی است که در چاپ فلز به عنوان یکی از مهمترین عامل مطرح است.
داخل قوطی که در تماس با محتوای آن قرار می گیرد. باید با لایه ای از لاک پوشیده شود. به طور استاندارد سطح فلز باید در یک نوبت لاک زنی شود. اما در بعضی مواقع مثل مشکلات ماشین لاک زنی و کیفیت ناکارآمد لاک، این عمل دوباره تکرار می شود. تا نتیجه مطلوب به دست آید به طور عمده در این شرایط لاک دوم برای پوشش کامل لاک اول استفاده میشود.
البته قابل ذکر است که به صورت معمول درون قوطی های مربوط به مواد غذایی. را دو بار و داخل قوطی های صنعتی یک بار لاک می زنند. به طور مثال می توان به لاک شماره 1287 که مخصوص مواد غذایی است، اشاره کرد.
پس از انجام مرحله لاک زنی، فلز باید در کوره قرار گیرد تا عملیات پخت به طور کامل انجام شود. اگر لاک کمتر از مقدار زمانی که در دستورالعملش قید شده داخل کوره بماند، خوب پخته نمی شود. و به احتمال زیاد از سطح فلز کنده می شود. اما اگر زمان مناسب برای پخت انتخاب شود، لاک بعد از خروج از کوره به هیچ وجه از فلز جدا نمی شود.
لاک ها به طور معمول سفید رنگ بوده و دارای تاریخ مصرف هستند. اگر در مرحله لاک زنی از لاک تاریخ مصرف گذشته استفاده شود قوطی پس از مدتی دچار زنگ زدگی می شود.
لاک و کوتینگ
لاک را درون قوطی و برای حفظ محصول داخل آن استفاده می کنند. البته نوعی لاک بیرونی هم هست که برای سرو ته قوطی مصرف می شود. به طور عمده به رنگ طلایی است. اما کوتینگ را روی سطح فلز (خارج قوطی) و برای بهتر انجام شدن عملیات چاپی می زنند. شایان ذکر است که در ایران لاک و کوتینگ مناسب تولید می شود.
چاپ
ورق های فلزی که عملیات چاپ روی آنها انجام می شود. از قبل باید چربی گیری و جرقه گیری بشوند. تا امکان چاپ روی آنها میسر شود. بعد از انجام عملیات چربی گیری، می توان با کنترل رطوبت هوا از اکسید شدن ورق ها جلوگیری کرد.
ویژگی مهمی که یک ورق استاندارد باید داشته باشد ضخامت یکسان آن در تمامی سطوح است.
پس از انجام مراحل مهیا سازی پلیت و ورق چاپی، ورق های فلزی با سیستم مک و باد. از روی سینی بلند میشود و به ماشین چاپ تغذیه می گردد.
ماشین های فعلی به طور عمده دو رنگ هستند. و اگر کاری چهار رنگ باشد. ابتدا دو رنگ اولیه چاپ میشود و قبل از چاپ دو رنگ بعدی ورق در کوره قرار می گیرد. تا خوب بپذرد و مرکب روی فلز ثابت شود.
ماشین های جدید دو رنگ، در هر ساعت شش هزار ورق را چاپ می کنند. در حالی که ماشین های قدیمی تنها توانایی چاپ 4 هزار ورق را در ساعت داشتند.
ماشین های چاپ فلز به صورت واحدی (Unit) و 3 سیلندری کار می کنند. بعد از چاپ هر رنگ ورق درون ماشین به صورت افقی حرکت کرده و به واحد چاپ بعدی منتقل می شود.
ترکیب رنگ یکی از اساسی ترین مساله است که مورد توجه چاپگران فلز می باشد. چرا که آنها در بسیاری از مواقع در تهیه رنگ دلخواه دچار مشکل می شوند.
بعضی از رنگ ها در کار چاپی نیازمند ترکیب چندین رنگ هستند. که با ترکیب چهار رنگ اصلی به سرعت می توان به رنگ مورد نظر رسید. مرکب سفید شکری، رنگ خیلی خوبی است که با اضافه مقداری از آن قادر خواهیم بود به خوبی رنگ را پرداخت و مهیا کنیم.
رنگ های چاپی پس از گذر از کوره اندکی تغییر پیدا می کنند. که در این موضوع مرکب های ایرانی رفتار خوبی از خود نشان داده و تغییر چندانی نمی کنند. مرکب خارجی نسبت به مرکب ایرانی گران تر است. ولی در بیشتر چاپخانه ها از مرکب ایرانی استفاده می شود که البته این مرکب جوابگوی نیاز موجود است.
بعد از چاپ آخرین رنگ روی کار ورنی قرار می گیرد. خط چاپ، ورنی و کوره ممکن است. به صورت متناوب و پشت سر هم قرار گیرند. (In line)، یا به طور مستقل باشند (off line)، که در این صورت سرعت خط تولید پایین می آید. عملیات ورنی زنی با همان سیلندری که مخصوص چاپ است. انجام می گیرد. به این شکل که همان اندازه ای که می خواهیم ورنی روی کار بخورد لاستیک مورد نظر بریده خواهد شد. در ضمن برای لاک زنی هر محصول باید یک سیلندر لاستیکی به ابعاد، اندازه ورق. لبه کار و مارجین مناسب و مطابق نقشه آن کار تهیه شود.
پس از چاپ
پس از پایان عملیات چاپ، ورق باید داخل کوره قرار گیرد. قبل از کار بایستی ورق ها کنترل شود تا در طی مسیر مشکلی پیش نیاید. طول کوره های معمولی حدود 26 الی 33 متر است. داخل کوره زنجیری نصب می شود. که ویکت ها روی آن نصب میشود، ورق ها را به صورت تک تک در طول آن به جریان درآورد. اگر ورق ها روی هم قرار گیرند. به دلیل خیس بودن، خراشیده شده و از بین می روند. حرکت ورق ها در کوره به صورت اتوماتیک انجام می شود. کارهای چاپی باید با همان سرعتی که چاپ میشوند. از کوره بگذرند و اگر سرعت کم باشد احتمال سوخت ورق وجود دارد.
درون کوره 2 تا 3 مشعل وجود دارد که اغلب به صورت گازی کار می کنند. شعله ها به طور مستقیم با یک دیگ ( مخزن بزرگ بسته) برخورد می کنند. در آن قسمت خازن هایی وجود دارد که به طور مستقیم گرما را بخش و به ورق می رساند. قابل ذکر است که شعله نباید به طور مستقیم با ورق در تماس باشد. و بایستی حرارت و دمای کوره در کل مسیر تونل یکسان باشد.
تا ورق را نسوزاند. علاوه بر آن این دما باید کنترل شود تا باعث تغییر رنگ در لاک و رنگ نشود. در انتهای کوره دو هواکش بزرگ وجود دارد. تا ورق ها را خنک کند. و به دمای اولین برگرداند. در غیر این صورت ورق ها به دلیل بیش از حد داغ بودن به هم می چسبند. پس از عبور ورق از کوره و شروع مراحل تکمیلی کار، ورق های چاپی، در قسمت قوطی سازی قیچی می شوند. و از روی خط تا، خم می شوند و شکل نهایی قوطی را به خود می گیرند.
در فرم دهی تنوع زیادی است. که متأسفانه این تنوع هنوز در بسته بندی کالاهای ایرانی جایگاهی ندارد. بازار مصرف ایران به نوعی است که وارد کردن تجهیزات مورد نیاز این کار مقرون به صرفه به نظر نمی رسد. اغلب تولید کنندگان به دنبال این هستند که بسته بندی تضمین شده در بازار استفاده کنند. بد نیست یادآوری شود که بین کشورهای خاورمیانه، ترکیه هم از نظر چاپ و هم از نظر تنوع شکل قوطی پیشرفت بیشتری داشته است.
فولاد رسول دلاکان
با سالها تجربۀ ارزشمند و گرانبها در عرصه تأمین و توزیع انواع ورق آلیاژی و انواع فولاد آلیاژی. و با گواهینامه ها و آنالیزهای معتبری که ضمیمه محصولاتش به مشتریان خویش میها می کند. توانسته رضایتمندی مشتریان خویش را همواره فراهم آورد.
صنعتگر شریف و گرامی از اینکه ما را جهت خرید کالا (فولاد آلیاژی) مورد نیاز خویش. انتخاب می نمایید از شما سپاسگزاریم.
ارتباط با ما
02128423820 – 09122136675– 09922704358
واتس آپ: 09122136675 – فکس: 02128423820
اینستاگرام: fooladdalakan
ایمیل : fooladrasuldalakan@gmail.com