تأثیر نورد سرد و آنیل بر ریزساختار و خواص مکانیکی فولاد مارجینگ نیکل-کروم-منگنز دار نانو
بررسی تأثیر نورد سرد و آنیل بر ریزساختار و خواص مکانیکی فولاد مارجینگ نیکل-کروم-منگنز دار نانو ساختار شده
تأثیر نورد سرد
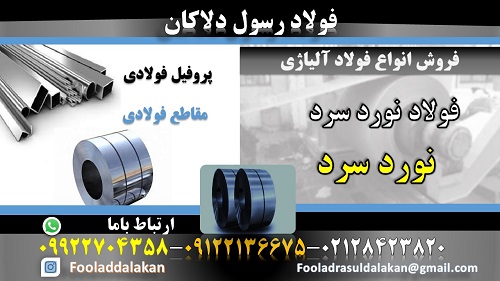
نورد اصطلاحی است که شامل مجموعه ای از کارها و عملیات بر روی فولاد و فلز می باشد . این عملیات و فرآیند شامل چرخاندن، سمباده کاری، پولیش کاری و غیره می شود. تمامی این مراحل تحمیل شده و اصلاح شده نورم گرم می باشد.
نورد سرد چیست؟
فولاد نورد سرد همان فولاد نورد گرمی می باشد که پردازش و کار بیشتری روی آن انجام شده است. برای دستیابی به فولاد نورد سرد فولادهای نورد گرم را در دمای اتاق نورد می کنند. تا فولاد نورد سرد شود. اگر بخواهیم به طور فنی و دقیق تر تعریفی از نورد سرد داشته باشیم. اصطلاح نورد مختص به ورقه هایی که بین غلتک های فشرده می شود. تا به ورقه های نورد سرد تبدیل شوند گفته می شود. بنابراین میله ها و لوله نورد گرم، پس از سرد شدن با فرآیندی به نام کشش سرد به میله و لوله سردکار تبدیل می شوند.
از ویژگی های فولاد در هوای سرد می توان به افزایش خواص مکانیکی. و بهبود سطح کیفی استحکام کششی و بهبود عملکرد فولاد اشاره کرد. این در حالی است که فولاد در هوای سرد شکل پذیری و اندازه گیری درصد کشش کاهش می یابد.
تعدادی از فولادها که میزان کربن آنها کم بوده و یا میزان نیتروژنشان در ترکیب فولاد کم است. به راحتی کار سرد انجام می دهند. اضافه کردن نیتروژن به عمد می تواند بخشی از ترک خوردگی را در هنگام کار سرد جبران کند.
اگر برخشی از فولاد نیاز به خراش، تعویض، انباشته شدن و یا در غیر این صورت سرد شدن پس از ماشین کاری دارد، باید اطمینان حاصل کرد که این فولاد دوباره با نیتروژن آغشته نمی شود علت این کار هم این است که نیتروژن در فرآیند ذوب فلز به فولاد اضافه می شود و نباید این کار را تکرار کرد. از نکات دیگری که باید در عملیات سرد کردن مطمئن شد این است. که نورد سرد در طراحی سرد به جای عملیات سنگین، عملیات استاندارد است. حواله سنگین، شکل پذیری باقی مانده در نوار را کاهش می دهد. اما جدا سازی تراشه ها از فولاد را آسان تر می کند.
مزایای نورد سرد در فولادها
از مزایای نورد سرد در فولادها میتوان به موارد زیر اشاره کرد:
- افزایش قدرت
- سطح بهبود یافته
- تحمل و کنترل غلظت بعدی
- صافی بهبود یافته
- ماشین کاری بهبود یافته
- افزایش قدرت
بطور گسترده ای شناخته شده است که فشار کار سرد باعث تغییر در خواص بیشتر فلزات می شود. هنگامی که میله های فولادی نورد با استفاده از سرد شدن از طریق قالب خنک می شوند. افزایش قابل توجهی در عملکرد و استحکام کششی حاصل می شود. در عین حال، از کاهش سطح و درصد درازمدت کاسته می شود.
ویژگی های فرآیند نورد سرد
از ویژگی های ممتار و برجسته فرآیند نورد سرد می توان به افزایش سختی ماده مورد نظر. و افزایش نابجایی در ساختار کریستالی ماده اشاره کرد. همچنین تنش تسلیم ماده در نورد سرد افزایش می یابد. در عملیات نورد سرد روغن کاری راحت تر انجام می شود. و با نبود سرما و اکسید شدن سطح بهتر می شود. و تلورانس ماده کمتر می شود.
از محصولات ایجاد شده در فرآیند نورد سرد اکثراً در خودروسازی، تجهیزات خانگی مانند یخچال. اجاق گاز، ماشین های ظرف شویی و لباسشویی، دستگاه های الکتریکی مخازن، تجهیزات ساختمانی و غیره استفاده می شود.
اثر طراحی سرد بر خصوصیت کششی میله فولادی
در صورت افزایش خصوصیات مقاومتی و کششی میله فولادی انعطاف پذیری آن کاهش می یابد. در صورت کاهش سرما تا حدود استحکام عملکردی میله ها با سرعت بیشتری از مقاومت کششی افزایش می یابد. که این کار باعث افزایش قدرت نیز می شود.
میله های فولادی نورد گرم در دماهای بالا ساخته می شوند. بنابراین سطح دارای مقیاس ساینده سختی است که از اکسیدهای مختلف آهن تشکیل شده است. به منظور سرد شدن میله ها. پره های سرمایی عملیات جداسازی را با انفجار شلیک یا ترشی اسیدی انجام می دهند. با کشش میله ها سطح نیز بهبود می یابد. این در حالی است که میله های Cold Drawn معمولاً دارای 50 دستگاه میکروچینک و حداکثر تجهیزات مدرن هستند. که معمولاً 25-30 اینچ کار می کنند.
دسته بندی ورق سرد
ورقه های نورد سرد بسته به نوع آلیاژ به کار رفته در آن ها. به سه دسته تقسیم بندی می گردند که عبارتند از :
- معمولی St12
- نیمه کشش St13
- نیمه کشش St14
بخش های اصلی و مهم نورد عبارت اند از:
- ریخته گری
- کوره پیش گرم
- نورد گرم
- اسید شویی
- نورد سرد
- آنلینگ
- تمپر میل
اولین بخش نورد لوله ریخته گری است. که در این مرحله شمش های فولادی با اندازه و سایزهای مشخص تولید می شوند. سپس در قسمت کوره های پیش گرم این شمش های ساخته شده. آرام آرام گرم می شوند تا به دمای یکنواختی برسند. این یکنواختی باعث کاهش شدید نیرو و گشتاور لازم برای نورد می شود.
سپس مرحله نورد گرم شروع میشود. در این قسمت از نورد گرم به وسیله نورد گرم سنگین و به کمک کاهش های بزرگ در سطح مقطع.شمش را به تختال تبدیل می کننند. سپس تختال ایجاد شده در قسمت قبلی به ورق هایی با ضخامت حداکثر 6 میلی متر تبدیل میشود.
در این مرحله اگر ورقه ها نیاز به نورد سرد و افزایش کیفیت سطح نداشته باشند. بعد از این مرحله قیچی زنی می شوند. در غیر این صورت به شکل کلاف پیچ در آمده و وارد خط نورد سرد می شوند. ورق به دست آمده از نورد گرم به جهت افزایش کیفیت سطح و آماده شدن جهت انجام فرآیند نورد سرد. و پوسته زدایی برای کاهش سایش غلتک ها وارد مرحله اسید شویی می شود.
بعد از مرحله اسید شویی، فولاد مورد نظر که با کویل شناخته می شود. به جهت افزایش کیفیت سطح، کاهش ضخامت و دستیابی به خواص مکانیکی مورد نظر وارد خط نورد سرد می شود. که حاصل آن کویل هایی با ضخامت کمتر و دقت و کیفیت بالاتر. به صورت کلاف یا ورق گالوانیزه و روغنی است. علت نامگذاری نورد سرد این است که تغییر شکل در دمای زیر دمای تبلور مجدد صورت می گیرد.
برای افزایش خواص مکانیکی فلز و رسیدن به محصولی یکنواخت تر پس از نورد سرد. به دلیل اینکه عملیات های مختلفی روی ورق گالوانیزه و روغنی انجام شده است. روی کلاف عملیات حرارتی انجام می شود. سپس برای حذف تغییر شکل های ناخواسته و تولید ورقی صاف ورق ها. با ضخامت بیش از 5% میلی متر وارد تمپر مبل می شود.
تأثیر نورد سرد
بررسی تأثیر نورد سرد و آنیل بر ریزساختار و خواص مکانیکی فولاد مارجینگ نیکل-کروم-منگنز دار نانو ساختار شده
نورد سرد و آنیل ساختارهایی با درصد بالای مارتنزیت، زیر مجموعه جدیدی از فرآیندهای ترمومکانیکی پیشرفته می باشد. که تحت عنوان فرآیند مارتنزیت شناخته شده است. در این تحقیق یک فولاد آلیاژی با ترکیب اسمی Fe-5Ni-10Cr-8Mn (درصد وزنی) در کوره خلاء ریخته گری شد. و پس از همگن سازی تحت دو مرحله نورد سرد به میزان 50%. و دو مرحله آنیل پس از نورد در دماهای مختلف قرار گرفت. آزمایش های XRD، سختی سنجی، آزمایش کشش و EBSD بر روی نمونه ها انجام شد.
نتایج نشان داد که نورد در دو مرحله و دمای آنیل 600 درجه سانتی گراد با زمان یک ساعت. بهینه ترین حالت برای رسیدن به یک ساختار فوق ریزدانه/نانوساختار است. همچنین آستنیت باقیمانده حاصل از آنیل دوفازی در این آلیاژ از نظر مکانیکی ناپایدار بوده و حین بارگذاری کششی به مارتنزیت استحاله یافت و خاصیت TRIP از خود نشان داد. استحکام کششی این فولاد در شرایط بهینه 1050Mpa و درصد ازدیاد طول نسبی آن 28 درصد بدست آمد. که به صورت تغییر شکل یکنواخت قبل از گلویی می باشد.
تأثیر نورد سرد

تولید فولادهای فوق ریزدانه از طریق روش های تغییر شکل پلاستیک شدید (SPD). و فرآیند ترمومکانیکی پیشرفته (TMCP) امکان پذیر است (Song & Poing,2006). روش های تغییر شکل پلاستیک شدید بسیاری در تولید انواع فلزات فوق ریز دانه/نانوساختار ابداع شده اند. اما فقط تعداد محدودی از این روش ها در مقالات گزارش شده اند. که در زمینه تولید فولادهای فوق ریزدانه/نانوساختار مفید بوده اند.
که شامل فشار تحت کانال زاویه ای با مقطع یکسان (Segal,1981&Reznikov)(ECAP). فرآیند اتصال نورد تجمعی (Saito,1999&Utsunomiya)(ARAB). پیچش تحت فشار بالا (Ivanisenko,2003&Lojkowski)(HPT). و اکستروژن برشی ساده (Pardis,2009&Ebrahimi)(SSE). با اعمال کرنش پلاستیک شدید بر روی فلز، منجر به کاهش شدید اندازه دانه می شوند. فرآیندهای ترمومکانیکی سابقه طولانی برای کاهش اندازه دانه در فولادها دارند که کاربرد صنعتی گسترده ای نیز پیدا کرده اند. این فرآیندها با اعمال کرنش کمتر و پیوستگی فرآیند و کنترل رژیم حرارتی. روش مناسبی برای کاهش اندازه دانه به شمار می آیند (Maki,2009&Tsuji).
تأثیر نورد سرد
یکی از فرآیندهای ترمومکانیکی که امروزه برای تولید فولادهای زنگ نزن آستنیتی فوق ریزدانه. توجه زیادی را به خود جلب کرده، فرآیند مارتنزیت است. نورد سرد و آنیل فولاد مارتنزیتی روشی است. که به وسیله تیسوجی و همکارانش در سال 2001 برای تولید فولادهای فوق ریزدانه استفاده کردند (Tsuji,Ueji,2002).
این فرآیند شامل نورد سرد سنگین برای تبدیل آستنیت(γ) نیمه پایدار به مارتنزیت (َα). در حین کرنش و در ادامه بازگشت مارتنزیت به آستنیت. در طی آنیل در زمان ها و دماهای نسبتاً پایین می باشد.
این روش به دلیل سهولت در تولید قطعات بزرگ نظیر ورق از اهمیت ویژه ای برخوردار است. در این روش آستنیت در اثر تغییر شکل سرد به مارتنزیت تبدیل می شود. و در در ادامه فرآیند تغییر شکل. مارتنزیت موجود در ریزساختار خرد شده و مکان های مناسب جوانه زنی. را برای بازگشت مارتنزیت به آستنیت در حین عملیات آنیل بعدی فرآهم می کند. و منجر به ریزدانگی فولاد و بهبود خواص مکانیکی آن می گردد. در این فرآیند انتخاب صحیح پارامترهای مؤثر بر آنیل بازگشت. جهت حصول ساختاری با اندازه دانه های نانو و زیرمیکرون از اهمیت ویژه ای برخوردار است.
مواد و روش تحقیق
در این تحقیق به منظور تهیه یک فولاد آلیاژی با ترکیب اسمی Fe-5Ni-10Cr-8Mn (درصد وزنی) از مواد اولیه با خلوص بالا استفاده شد. عملیات ذوب و آلیاژ سازی در کوره ذوب قوسی تحت خلاء (VAR) انجام شد. پس از عملیات آلیاژسازی و ریخته گری. شمش تحت عملیات همگن کردن به منظور از بین بردن جدایش های ریخته گری. به مدت 40 ساعت تحت دمای 1070 سانتی گراد قرار گرفت. ترکیب شیمیایی بدست آمده از تست کوانتومتری در جدول 1 نشان داده شده است.
تأثیر نورد سرد
در مرحله اول نمونه تحت عملیات نورد به میزان 5%. و آنیل در دمای 600 درجه سانتی گراد به مدت یک ساعت قرار گرفت. و در مرحله دوم نورد به میزان 50% و آنیل در دمای 600 درجه سانتی گراد مجدداً انجام شد. سرد کردن نمونه پس از همگن سازی در داخل آب و پس از هر مرحله آنیل. در داخل نیتروژن مایع انجام گرفت. در شکل 1 نحوه ی انجام عملیات ترمومکانیکی بکار رفته در این تحقیق نشان داده شده است.
بررسی های متالوگرافی، پراش اشعه ایکس و سختی سنجی ویکرز. با بار 100kg بعد از هر مرحله بر روی نمونه انجام شد. و در انتها آزمون کشش مطابق استاندارد JIS Z 2210 شماره 7 بر روی نمونه ها. در دمای محیط و تحت سرعت فک 1mm/min انجام گرفت. و آزمایش پراس الکترون برگشتی (EBSD) در راستای عمود بر نورد در مساحتی در حدود 25×50 میکرومتر تصویربرداری شد.
نتایج و بحث
شکل 2 تصویر میکروسکوپ نوردی ریزساختار قبل و بعد از همگن سازی را نشان می دهد. همانطور که در شکل 2-الف دیده می شود. نمونه ریختگی قبل از همگن سازی جدایش های دندریتی را نشان می دهد. در این تصویر مناطق تیره رنگ، مارتنزیت های تشکیل شده. و مناطق سفید رنگ آستنیت های باقی مانده. در مناطق غنی از عناصر آلیاژی در بین بازوهای دندریتی را نشان می دهد.
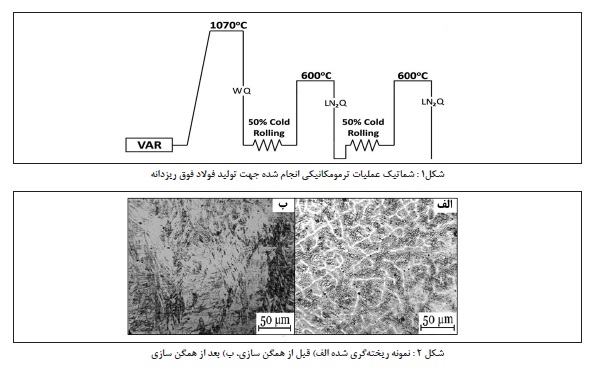
پدیده های مزبور ناشی از سرد شدن غیرتعادلی در ضمن انجماد و عدم نفوذ کامل عناصر آلیاژی می باشد. این موضوع موجب افت خواص مکانیکی فولاد از جمله قابلیت کارگرم و کارسرد می شود. (اصول کاربرد عملیات حرارتی فولادها، 1378).از این رو، ساختار ریختگی فولاد باید به کمک عملیات همگن سازی مناسب یکنواخت شود. در تصویر 2-ب ریزساختار نمونه همگن سازی شده در دمای 1070 درجه سانتی گراد. و زمان 40 ساعت و سرد شده در آب نشان داده شده است. شکل 2-ب نشان می دهد که در اثر همگن سازی طولانی ساختار دندریتی از بین رفته. و شبکه پیوسته فاز آستنیت بین دندریتی حذف شده و ساختار یکنواخت مارتنزیتی بدست آمده است.
تأثیر نورد سرد
الگوی پراش اشعه ایکس نمونه همگن شده در شکل 3-الف نشان داده شده است. که خطوط پراش مربوط به آهن bcc را نشان می دهد که با ساختار مارتنزیتی ` α مطابقت دارد. در کنار این خطوط بازتاب های ضعیف مربوط به آهن (γ) fcc و آهن bcc (ε) نیز مشاهده می شود که وجود آستنیت باقیمانده به مقدار جزئی در ساختار را نشان می دهد. دلیل پایداری آستنیت در نمونه همگن شده، وجود عناصر آلیاژی نیکل و منگنز در بین بازوهای دندریتی می باشد. که غلظت بالای آنها می تواند سبب کاهش دمای تشکیل مارتنزیت و در نتیجه پایداری شیمیایی گردد. شکل 3-ب الگوی پراش اشعه ایکس ساختار نورد شده را نشان می دهد. همانطور که ملاحظه می شود، در حالت همگن پیک های آستنیت بصورت جزئی نمایان است.
در حالی که پس از نورد سرد، این پیک ها جای خود را به پیک های مارتنزیت می دهند. مارتنزیت در این فولادها به دلیل کربن کم، دارای ساختار انعطاف پذیر می باشد. در اثر 50 درصد نورد سرد اول تمام فاز آستنیت به مارتنزیت تبدیل شده است. و سختی نمونه به مقدار 373 ویکرز افزایش یافت. در ادامه نمونه تحت دمای 600 درجه سانتی گراد آنیل مرحله اول به مدت یک ساعت قرار گرفت.
تأثیر نورد سرد
شکل 4-الف الگوی پراش اشعه ایکس از نمونه را نشان می دهد. خرد شدن دانه های مارتنزیت و کوچک شدن آنها سبب پایدار شدن فاز آستنیت شده است. همچنین در این فولادها نیکل و منگنز با تشکیل رسوب NiMn بر روی پایداری آستنیت تأثیر می گذارد. و سبب تسریع در تشکیل آستنیت برگشتی می شود. سختی در این مرحله به میزان 367 ویکرز بدست آمد. که با توجه به اینکه در این فولادها کربن بسیار کمی وجود دارد. میزان سختی فازهای آستنیت و مارتنزیت تفاوت چندانی با هم ندارند. تشکیل رسوبات آلیاژی بسیار ریز و با چگالی بالا در فاز مارتنزیت دلیل افزایش سختی در دماهای پایین می باشد. (حسین نژاد & نیلی احمد آبادی، 1381). نمونه ها پس از آنیل مرحله اول تحت 50 درصد نورد مرحله دوم. و آنیل در دمای 600 درجه سانتی گراد در مدت زمان یک ساعت قرار گرفت.
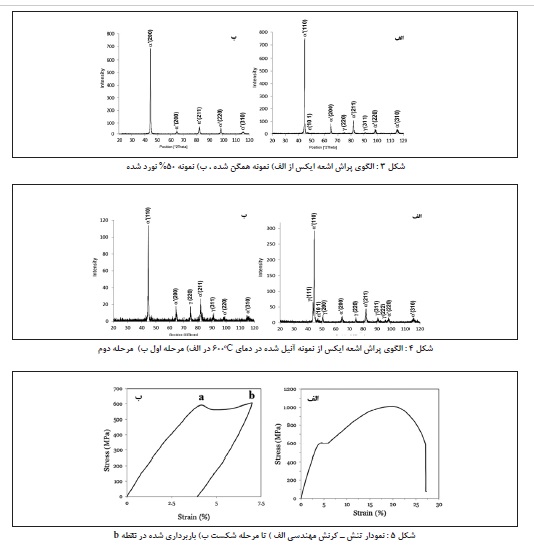
میزان آستنیت و مارتنزیت به کمک الگوی پراش اشعه ایکس در شکل 4-ب نشان داده شده است. ریز شدن اندازه دانه در اثر نورد سرد مرحله دوم و کاهش دمای Ms سبب شده. تا در فرآیند آنیل مرحله دوم در دمای 600 درجه سانتی گراد. ساختار دو فازی آستنیت و مارتنزیت در نمونه تشکیل شود. این فرآیند سبب شد تا ساختار ریزدانه تر شده و سختی افزایش یابد و به میزان 290 ویکرز بدست آید.
تأثیر نورد سرد
برای آزمون کشش مطابق استاندارد توضیح داده شده نمونه تهیه شد و سپس تحت آزمایش کشش قرار گرفت. نتایج این آزمایش به صورت منحنی تنش-کرنش مهندسی در شکل 5-الف نشان داده شده است. در نمونه بعد از تسلیم، وجود یک پلاتو شبیه پدیده نقطه تسلیم را نشان می دهد. این موضوع مورد توجه بیشتر قرار گرفت.
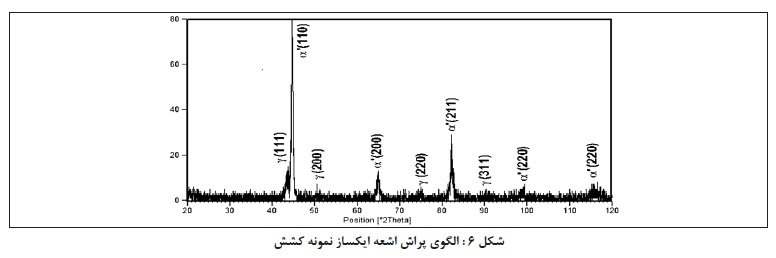
در شکل 5- ب تغییرات تنش پس از باربرداری از انتهای ناحیه پلاتو نشان داده شده است. که عدم برگشت پذیری کامل کرنش را نشان می دهد.
الگوی پراش اشعه ایکس نمونه برداری شده در قسمت وسط نمونه تست کشش در شکل 6 نشان داده شده است. که مقادیر کمتر آستنیت را نشان می دهد. و بنابراین می توان گفت که پلاتو ناشی از استحاله دینامیک آستنیت باقیمانده. به مارتنزیت در حین آزمایش کشش بوده است. با توجه به میزان آستنیت و مارتنزیت قبل و بعد از انجام آزمایش به این نتیجه می توان رسید. که در حین انجام آزمایش کشش، فاز نرم آستنیت ابتدا تغییر شکل یافته. و پس از کرنش دچار ناپایداری مکانیکی میگردد. به عبارت دیگر ابتدا آستنیت، تغییر شکل یافته و بدنبال آن به مارتنزیت تبدیل می گردد.
تبدیل فوق سبب افزایش حجم و کارسختی موضعی شده و از ناپایداری کششی جلوگیری می کند. توان و نرخ کارسختی بالا در این نمونه ناشی از تغییر شکل و کارسخت شدن فاز آستنیت است. و تبدیل آستنیت کار سخت شده به مارتنزیت از گلویی شدن موضعی. در نقطه a تا b در شکل 5-ب جلوگیری نموده. و سبب شد توان کار سختی یا میزان تغییر شکل یکنواخت در این نمونه افزایش یابد. تبدیل آستنیت به مارتنزیت در حین کار مکانیکی سبب افزایش انعطاف پذیری می شود و به TRIP معروف است. فولادهایی که تغییر شکل پلاستیک، تحریک کننده دگرگونی در آنهاست. و از آن تغییر حالت به منظور بهبود و انعطاف پذیری کمک می گیرند. به فولادهای TRIP معروف هستند.
در این فولادها در اثر کرنش یا همان تغییر شکل پلاستیک، آستنیت به مارتنزیت تبدیل می شود. از طرف دیگر مارتنزیت ایجاد شده در اثر کرنش به علت وجود چگالی بالایی از نابجایی ها. در ساختار در برابر گلویی شدن مقاومت کرده. و در نتیجه ترکیب خوبی از استحکام بالا و انعطاف پذیری خوب را موجب می شود .(De Cooman,2004). تحلیل داده های حاصل از الگوی پراش اشعه ایکس در نقطه b نیز نشان می دهد. که در این فولاد در حین انجام آزمایش کشش، آستنیت به مارتنزیت تبدیل می شود.
در مقایسه نتایج با کار لی و همکاران (Ma,Jin,2005,&Lee) پیش بینی شد. که نمونه به ساختار فوق ریزدانه/نانو ساختار رسیده باشد. که برای اثبات این موضوع آزمون پراش الکترون برگشتی (EBSD) از نمونه گرفته شد. آزمایش EBSD از نمونه در راستای عمود بر نورد (ND) انجام گرفت. و مساحتی در حدود 25× 50 میکرومتر و تصویربرداری شد. فاصله روبش بین نقاط به میزان 300 نانومتر انتخاب گردید. برای داشتن یک الگوی EBSD با کیفیت خوب نیاز به آماده سازی مناسب نمونه است.
در این پژوهش برای آماده سازی نمونه بعد از مراحل سنباده زنی و انجام پولیش مکانیکی. از پولیش الکتروشیمیایی برای آماده سازی نهایی بر روی سطح انجام شد. و تصاویری از اندازه دان، جهات کریستالی، تصاویر فازی و داده های خام از نوع مرزدانه ها بدست آمد. شکل 7 تصویر بدست آمده از EBSD نشان دهنده جهات کریستالی در نمونه می باشد. که در راستای عمود بر نورد بدست آمد. با در نظر گرفتن خط مقیاس و تفاوت در رنگ دانه ها، میانگین اندازه دانه ها زیر یک میکرومتر و در محدوده فوق ریزدانه/نانو ساختار بدست آمد. رنگ قالب در هر جهت نشان دهنده بیشترین دسته صفحات کریستالی در آن جهت می باشد. در مقایسه صفحات کریستالی 1 0 1 در راستای Y، و صفحات کریستالی 1 1 1 در راستای X. نسبت به دیگر صفحات از دانسیته بیشتری برخوردار است (پایان نامه کارشناسی ارشد، 1392).
تصویر بدست آمده از EBSD نشان دهنده جهات کریستالی در نمونه می باشد. که در راستای عمود بر نورد بدست آمد. با در نظر گرفتن خط مقیاس و تفاوت در رنگ دانه هاف میانگین اندازه دانه ها زیر یک میکرومتر و در محدوده فوق ریزدانه/نانو ساختار بدست آمد (پایان نامه کارشناسی ارشد, 1392).
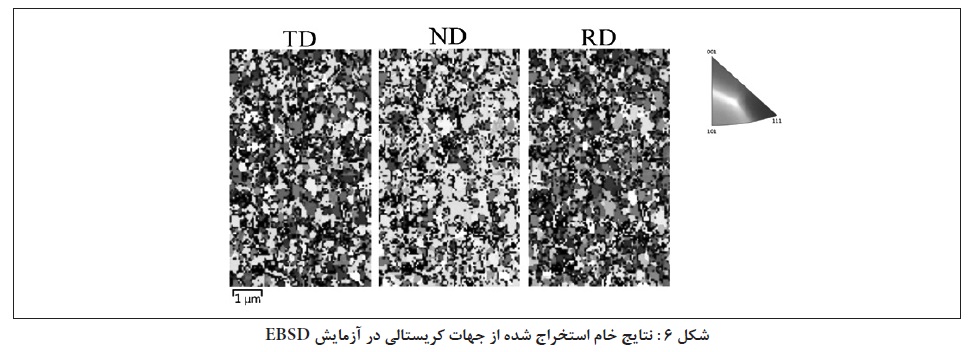
نتیجه گیری
1)عملیات مارتنزیتی دو مرحله در دمای 600 درجه سانتی گراد. به مدت یک ساعت و نورد 50 درصد در هر مرحله در این فولاد. سبب بدست آمدن ساختار زیر یک میکرون و در محدوده فوق ریزدانه/نانو ساختار می شود.
2) فولاد نانو ساختار تولید شده دارای استحکام تسلیم 1050Mpa به همراه ازدیاد طول 28% می باشد.
3) ریزدانه کردن در این آلیاژ سبب پایداری فاز آستنیت می شود.
4) حداکثر تافنس و انعطاف پذیری در این آلیاژ ناشی از وقوع پدیده TRIP و ریزدانه شدن است.
دانشکده مهندسی مواد دانشگاه صنعتی سهند
فولاد رسول دلاکان
با سالها تجربۀ ارزشمند و گرانبها در عرصه تأمین و توزیع انواع ورق آلیاژی و انواع فولاد آلیاژی. با گواهینامه ها و آنالیزهای معتبری که ضمیمه محصولاتش به مشتریان خویش ارائه داده است. توانسته رضایتمندی مشتریان خویش را همواره فراهم آورد.
صنعتگر شریف و گرامی از اینکه ما را جهت خرید کالا (فولاد آلیاژی) مورد نیاز خویش. انتخاب می نمایید از شما سپاسگزاریم.
ارتباط با ما
02128423820 – 09122136675– 09922704358
واتس آپ: 09122136675
اینستاگرام: fooladdalakan
ایمیل : fooladrasuldalakan@gmail.com