بررسی اثر دما و غلظت الکترولیت در فرآیند الکتروپولیش بر مقاومت به خوردگی اینکونل
بررسی اثر دما و غلظت
بررسی اثر دما و غلظت الکترولیت در فرآیند الکتروپولیش بر مقاومت به خوردگی آلیاژ اینکونل 718
چکیده
بهبود مقاومت به خوردگی توسط فرآیند الکتروپولیش یکی از راههای مهم در فرآیند اصلاح سطح میباشد. در این تحقیق اثر دو متغیر غلظت اسید پرکلریک و دمای حمام بر فرآیند الکتروپولیش. و تأثیر آن بر مقاومت به خوردگی آلیاژ اینکونل 718 بررسی شد. جهت بررسی ریزساختار و کیفیت زبری سطح، قبل و بعد از الکتروپولیش به ترتیب از تصاویر میکروسکوپ الکترونی روبشی و آزمون زبرسنجی سطح استفاده شد.
بررسی اثر دما و غلظت
جهت تعیین محدوده ولتاژ و جریان الکتروپولیش منحنیهای I-V به کار گیری شد. نتایج نشان داد دستیابی به سطحی یکنواخت و عاری از حفرات تنها در شرایطی حاصل میشود. که ترکیب الکترولیت حاوی 20 درصد حجمی اسید پرکلریک و دمای حمام برابر 15 درجه سانتیگراد باشد. تحت شرایط مذکور سرعت الکتروپولیش در مرزدانهها و درون دانهها به یکدیگر نزدیک میشود و منجر به ایجاد سطحی صاف و یکنواخت میگردد.
حداقل زبری سطح بعد از الکتروپولیش در شرایط بهینه 0/026μm به دست آمد. نتایج حاصل از آزمون پلاریزاسیون تافل در محلول 0.5M H2SO4+0.01M KSCN نشان داد. الکتروپولیش موجب کاهش چگالی جریان خوردگی و نجیبتر شدگی پتانسیل خوردگی در آلیاژ گردید. نمونه الکتروپولیشی در شرایط بهینه بیشترین مقاومت به خوردگی را از خود نشان داد. دلیل افزایش مقاومت به خوردگی در اثر الکتروپولیش به تشکیل لایه اکسیدی یکنواخت و ریزساختار عاری از حفرات در سطح نسبت دهی شد.
1- مقدمه
قطعاتی که شکلهای هندسی پیجیده دارند، همواره با مشکل عدم یکنواختی سطح روبرو میباشند. پولیشکاری مکانیکی نه تنها به افزایش مقاومت به خوردگی آلیاژها کمکی نمیکند. بلکه با تجمع هوا، ناخالصی، مواد چرب و اسیدها در سطح ناهموار (از دید میکروسکوپی)، پوسیدگی آلیاژ را تسریع مینماید [1]. همچنین پولیشکاری مکانیکی منجر به ایجاد تنشهای باقیمانده در سطح فلزات میشود. که در کاهش عمر کاری آلیاژ مؤثر است [3,2]. الکتروپولیش راهی مناسب برای کاهش زبری سطح و درخشندگی، به دلیل یکنواختی سطح در اندازههای نانومتری برای شکلهای هندسی بغرنج و درهم میباشد [3].
فروش فولاد آلیاژی فولاد رسول دلاکان
فرآیند الکتروپولیش اولین بار توسط مدسن1 در سال 1925 انجام شد [4]. در آن سال هدف از الکتروپولیش، بالا بردن کیفیت سطح آبکاری شده بود. توسعه و تکامل فرآیند الکتروپولیش به طور گسترده توسط ژاکوت2 در سال 1935 روی آلیاژ مس و فلزات دیگر صورت گرفت [5]. هدف از آن تحقیق میزان جلای سطح مورد الکتروپولیش در غلظتهای مختلف الکترولیت بود. الکتروپولیش با ایجاد یک لایه اکسیدی غیر فعال در برابر خوردگی، از خوردگی حفرهای و شکست هیدروژنی قطعه جلوگیری میکند [7,6].
محلول متداول مورد استفاده برای الکتروپولیش بیشتر روی اسیدهایی مثل پرکلریک، سولفوریک، فسفریک و اسید استیک متمرکز میباشد [7,2]. جین و همکاران پژوهشی را روی الکتروپولیش نیوبیوم انجام دادند و اثر پارارمترهای مختلف الکتروپولیش را روی زبری سطح و سرعت الکتروپولیش بررسی کردند [8]. نتایج حاصل از آن پژوهش نشان داد، الکتروپولیش خواص سطحی بسیار مطلوبی در آلیاژ ایجاد کرده. و میتواند راه حل مناسبی برای رفع حفره و عیوب سطحی در ورق نیوبیوم باشد.
قیمت فولاد آلیاژی فولاد رسول دلاکان
در پژوهشهای انجامی در خصوص الکتروپولیش فلزات خالص و تکفاز بسیار زیاد است. ولی در کمتر پژوهشی به الکتروپولیش آلیاژها و ترکیبات چند فازی مورد بررسی قرار گرفت. یکی از مشکلاتی که در ارتباط با الکتروپولیش آلیاژها وجود دارد. سرعت جدایش مواد از سطح نمونه با توجه به چند فازی بودن آلیاژ میباشد. سیمکا و همکارانش [9] مقاومت به خوردگی آلیاژ NiTi را با استفاده از فرآیند الکتروپولیش ارتقا دادند. ایشان دلیل افزایش مقاومت به خوردگی را در نتیجه تشکیل یک لایه پیوسته TiO2 روی سطح آلیاژ NiTi بیان کردند.
هان و همکارانش [10] با استفاده از روش الکتروپولیش مقاومت به اکسیداسیون فولاد 316 را ارتقا دادند. نتایج تحقیق آنها نشان داد، یک لایه اکسیدی دولایه متشکل از اکسید آهن در لایه بیرونی. و اکسید کروم در لایه داخلی در اثر الکتروپولیش ایجاد میشود. که همین لایه اکسیدی منجر به افزایش مقاومت به اکسیداسیون فولاد میشود. در پژوهش دیگری هان و همکارانش [11] اثر الکتروپولیش را روی مقاومت به خوردگی آلیاژ پایه نیکل 600 بررسی کردند. و نشان دادند که مقاومت به خوردگی آلیاژ 600 در اثر تشکیل یک لایه Cr2O3. در سطح افزایش قابل توجهی مییابد.
روتی و همکاران [12] به بررسی کیفیت سطح الکتروپولیشی سه نوع متفاوت فولاد زنگ نزن 316L تهیه گردید. به روش ریختهگری شده؛ افزودنیهای تولید لایهای (ALM3). و پوششدهی پاشش حرارتی (TSC4) پرداختند. نتایج تحقیق ایشان نشان داد فرآیند ساخت تأثیر بسیار زیادی بر کیفیت سطح الکتروپولیشی فولاد زنگ نزن دارد. بطوریکه کمترین زبری سطح در نمونه ریختهگری شده مشاهده شد. هان و همکارانش [13] نشان دادند الکتروپولیش آلیاژ 182 منجر به کاهش خوردگی، افزایش مقاومت به SCC و خوردگی بین دانهای میشود.
دلیل این اتفاق به شکلگیری لایه اکسیدی محافظ از جنس اکسید کروم در سطح میباشد. بابیلاس و همکاران [14] در پژوهشی آلیاژ Ti-15Mo را به دو روش آندایزینگ و الکتروپولیش اصلاح سطح کردند. نتایج یافتههای ایشان نشان داد مقاومت به خوردگی آلیاژ در هر دو روش افزایش مییابد. ولی تنها در روش الکتروپولیش لایه اکسیدی به صورت یکنواخت تشکیل میشود. که جنس این لایه ترکیبی از دو اکسید TiO2 و MoO3 میباشد.
این محققین با اندازهگیری زاویه ترشوندگی، نشان دادند که در روش الکتروپولیش زاویه ترشوندگی افزایش بیشتری مییابد. لیو و همکارانش [15] نشان دادند الکتروپولیش پوشش نیکل مورد آبکاری روی فولاد Q235A منجر به افزایش مدول الاستیک و سختی پوشش میگردد.
بررسی اثر دما و غلظت
آلیاژ اینکونل 718 نیز یکی از سوپر آلیاژهای پایه نیکل است. که به طور گسترده در صنایع هوایی و هستهای استفاده میشود. خواص مکانیکی این آلیاژ فوقالعاده بوده و مقاومت خوبی در برابر خوردگی در دماهای بالا از خود نشان میدهد. خواص مکانیکی بالای این آلیاژ باعث میشود تا نیل به سطحی صاف و درخشنده با استفاده از روشهای مکانیکی کار دشواری باشد [16]. از آنجایی که در صنایع هوایی و هستهایی، سطح و ویژگیهای سطح جزء مهمترین عوامل تأثیرگذار برای کاربرد آلیاژ میباشد. لذا دستیابی به روش مطمئن و مقرون به صرفه برای افزایش کیفیت سطح بسیار حائز اهمیت است.
در روش الکتروپولیش در صورت استفاده از یک الکترولیت مناسب. ناهمواریهای سطح به بهترین شکل زدوده شده و نیکل موجود در ریزساختار به صورت رقابتی با کروم حل میشود. در نتیجه یک سطح کامل براق با کیفیت آینه باقی میماند که غنی از کروم بوده و در مقابل خوردگی به شدت مقاوم است. اساس این فرآیند بر این اصل استوار است که سرعت پرداخت در نقاطی که بالاترین نسبت سطح را دارند، بیشتر است [17]. الکتروپولیش آلیاژ اینکونل 718 در یک چگالی جریان مشخص اتفاق میافتد.
این چگالی جریان در یک محدوده خاصی از ولتاژ میباشد. که ولتاژ بیشتر باعث انحلال لایه پسیو و کمتر از این محدوده ولتاژ عدم پرداخت مناسب میگردد [17]. رابطه بین چگالی جریان و پتانسیل در فرآیند الکتروپولیش توسط منحنیهای I-V بیان میشود. در شکل (1) رفتار منحنی نشان داده شده را میتوان به چهار ناحیه طبقهبندی کرد. منطقه A-B؛ در این محدوده، جریان به صورت خطی با ولتاژ افزایش مییابد و عمل اچ بر روی سطح آلیاژ اتفاق میافتد. در این محدوده مرزدانهها و مناطق بین فازی خورده میشود.
رفتار جریان در این منطقه بیشتر به ماهیت الکترولیت بر میگردد [18]. منطقه B-C؛ این محدوده به منطقه ناپایدار جریان معروف است. بسته به ماهیت الکترولیت متفاوت میباشد. هرچه مقدار این ناحیه کمتر باشد یک ویژگی خوب برای الکترولیت محسوب میشود. [18]. منطقه C-D؛ محدوده الکتروپولیش میباشد. جریان در این محدوده ثابت است. منطقه D-E؛ جبابهای گاز اکسیژن به آرامی تشکیل میشود.
این حبابها باعث تخریب فیلم و ایجاد حفرات بر روی آن میشود. هرچه محدوده جریان پایدار بیشتر و مقدار جریان در این محدوده کمتر باشد شرایط الکترولیت برای انجام فرآیند الکتروپولیش بهتر میشود [19]. راحمان همکارانش [20] نشان دادند که الکتروپولیش در ناحیه C-D؛ نسبت به ناحیه D-E. منجر به ایجاد سطحی با زبری حداقل و کمترین انرژی آزاد سطح میشود.
در این تحقیق سعی شده، با مطالعه و بررسی رفتار آلیاژ اینکونل 718 در الکترولیتهای مختلف، شرایط بهینهای برای الکتروپولیش آلیاژ اینکونل 718 حاصل شود.
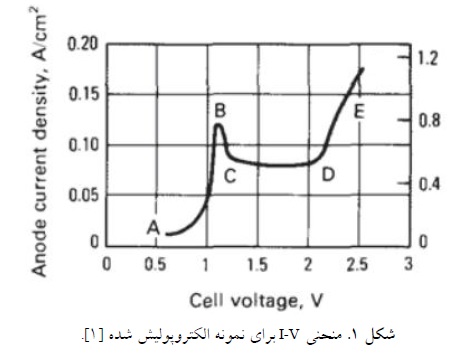
2- روش تحقیق
1-2- آمادهسازی نمونهها
برای الکتروپولیش آلیاژ اینکونل 718 نمونههایی از این آلیاژ در ابعاد 9×1/5 سانتیمتر و ضخامت در میلیمتر با استفاده از وایرکات برشی داده شد. نمونهها قبل از انجام فرآیند الکتروپولیش با سمباده به ترتیب 100 و 400 سمبادهزنی شدند. در انتها نمونهها با استون به منظور چربیزدایی شستشو و سپس خشک شدند.
2-2- الکتروپولیش نمونهها
جهت تهیه محلول الکتروپولیش از اسید پرکلریک (HCIO4). و اسید استیک (CH3COOH) با نسبتهای مختلف، به همراه 10 درصد حجمی آب دیونیزه استفاده شد. روش تهیه به اصورت میباشد که در بشری به حجم 400 میلیلیتر مقدار مشخصی اسید پرکلریک (از 10 تا 30 درصد حجمی) ریخته میشود. در ادامه اسید استیک به همراه آب دیونیزه به محلول اضافه میگردد. محلول بالا توسط یک همزن مغناطیسی با سرعت 500rpm به مدت ۱۲ ساعت همزده میشود. خلاصه شرایط مهیاسازی الکترولیتها در جدول ۱ نمایان و مشخص است. همچنین به منظور بررسی اثر دما، محلولهای S6,S5,S4 مطابق جدول (1) ایجاد و تولید شد.
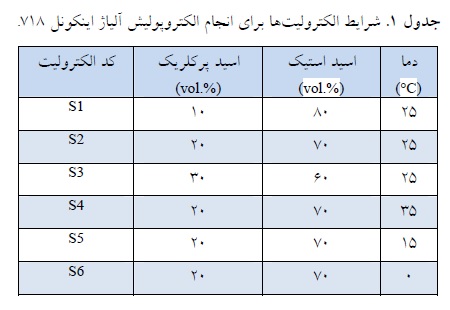
شکل (2) شماتیکی از تصویر سلول الکتروپولیش آلیاژ اینکونل 718 را نشان میدهد. کاتد از جنس فولاد زنگ نزن 316L میباشد [9]. جنس بدنه سلول از پیرکس و جنس درپوش پلیمری است. همچنین به منظور اعمال جریان و تنظیم ولتاژ از رکتیفایر مدل PSIP استفاده شد.
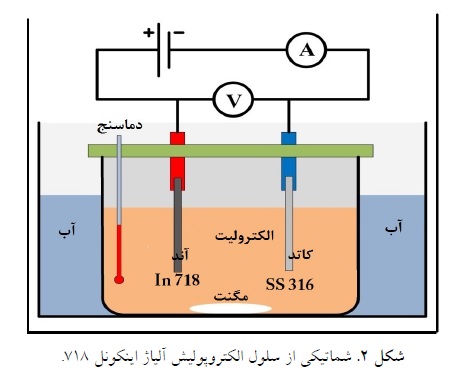
زمان الکتروپولیش برای تمامی نمونهها پنج دقیقه، سرعت چرخش الکترولیت در سلول برابر 150rpm. و فاصله بین آند و کاتد 15 سانتیگراد مد نظر قرار گرفت. مقدار جریان و پتانسیل اعمالی به سلول الکتروپولیش پس از استخراج دادهها از نمودار I-V مطابق جدول (2) اعمال شد. پس از فرآیند الکتروپولیش نمونهها با آب یونیزه شستشو و در دمای 10 درجه سانتیگراد خشک شدند.
3-2- مشخصهیابی
برای بررسی سطح نمونههای مورد الکتروپولیش از میکروسکوپ الکترونی روبشی مدل LEO-VP435 با ولتاژ KV 20 استفاده شد. به منظور اندازهگیری زبری سطح بعد از فرآیند الکتروپولیش از زبری سنج مدل الکومتر-7061 در دمای 25 درجه سانتیگراد استفاده شد.
جهت بررسی نمودار I-V و تأثیر فرآیند الکتروپولیش بر مقاومت به خوردگی آلیاژ از آزمون پلاریزاسیون تافل استفاده شد. آزمونهای الکتروشیمیایی براساس سیستم سه الکترودی صورت گرفت و اندازهگیری با دستگاه پتانسیواستات مدل Parstat 2273 انجام شد. الکترود مرجع از نوع کالومل اشباع (SCE)، کاتد از جنس پلاتین و الکترود کاری آلیاژ الکتروپولیشی. با سطح در معرض یک سانتیمتر مربع انتخاب شد.
محلول مورد استفاده برای انجام آزمون پلاریزاسیون تافل مطابق پژوهشهای گذشته. جهت بررسی خواص خوردگی آلیاژهای حاوی نیکل و کروم به صورت 0.5M, H2SO4+0.01M KSCN [2] انتخاب شد. محدوده پتانسیل انتخابی 250- تا 500 میلیولت نسبت به کالومل اشباع و نرخ روبش 1mV/s در دمای 25 درجه سانتیگراد مد نظر قرار گرفت. زمان غوطهوری نمونه برای نیل به حالت تعادل توسط آزمایش E vs T مشخص و برابر 30 دقیقه انتخاب شد. از نرم افزار corr view جهت استخراج پارامترهای الکتروشیمیایی استفاده شد.
بررسی اثر دما و غلظت
3- نتایج و بحث
1-3 اثر غلظت اسید پرکلریک و دما بر الکتروپولیش آلیاژ اینکونل 718
شکل (3) رفتار منحنی I-V برای نمونههای آلیاژ اینکونل 718 در الکترولیت اسید پر کلریک/اسید/آب در غلظتهای مختلف اسید پرکلریک (مطابق جدول1) نشان میدهد. الکترولیتهای S1 تا S3 به ترتیب حاوی 30,20,10 درصد حجمی از اسید پرکلریک میباشد.
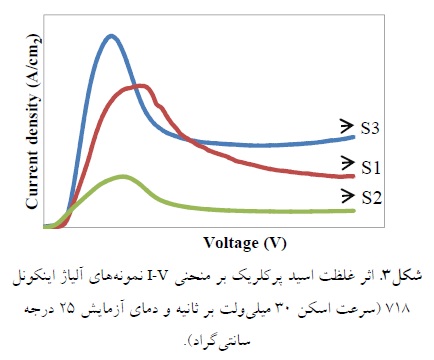
با توجه به شکل (3) در محلول حاوی 20 درصد حجمی اسید پرکلریک (محلول S2) منحنی I-V. رفتار بهینهتری برای الکتروپولیش آلیاژ اینکونل 718 از خود نشان میدهد. طول منطقه B-C (منطقه پایدار) در این الکترولیت کمتر و طول منطقه C-D (منطقه الکتروپولیش) بیشتر از دو الکترولیت دیگر میباشد. جدول (2) چگالی جریان و ولتاژ انتخابی در محدوده پایدار منحنی I-V برای هر الکترولیت، جهت الکتروپولیش آلیاژ اینکونل 718 را نشان میدهد.
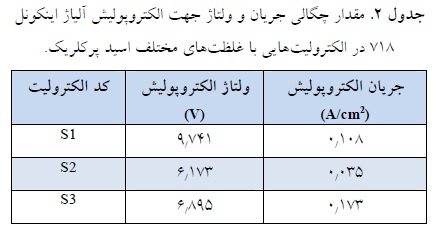
شکل (4) تصاویر ایجادی توسط SEM از سطح آلیاژ اینکونل 718 قبل و بعد از الکتروپولیش در الکترولیتهای S1 تا S3 را نشان میدهد. با توجه به شکل الکتروپولیش به میزان قابل توجهی باعث یکنواختی سطح آلیاژ اینکونل 718 گردید. شیارهای ناشی از مرحله مهیا سمبادهزنی به میزان قابل توجهی در نمونههای الکتروپولیش شده کاهش یافت. با دقت در تصاویر شکل (4-ب) و (4-د) مشخص میشود که انجام فرآیند الکتروپولیش. منجر به ایجاد حفرات در درون دانهها به خصوص نواحی نزدیک مرزدانهها گردید.
بررسی اثر دما و غلظت
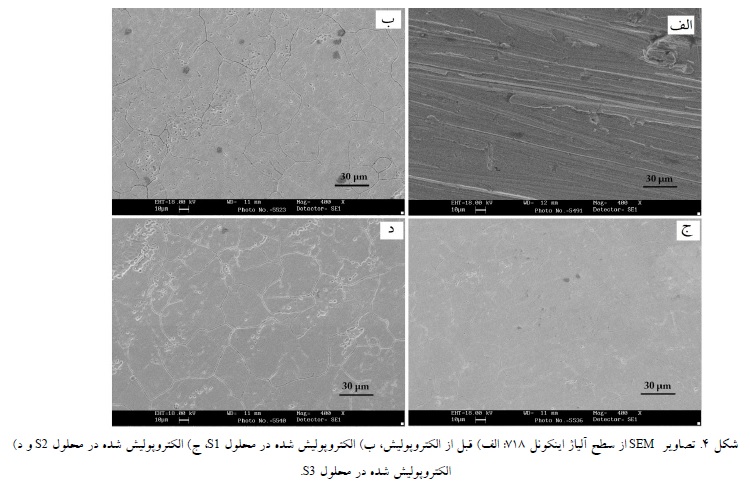

یکی از دلایل ایجاد این حفرات غلظت بالای عناصر آلیاژی در این نواحی میباشد [9]. مرزدانهها به دلیل سرعت خوردگی بیشتر نسبت به درون دانهها به طور مشخصی در تصاویر (ب) و (د) در شکل (4) مشخص میباشد. در خصوص تصویر (۴-ج) که مربوط به نمونه مورد الکتروپولیش در محلول S2 میباشد. شرایط به گونهای دیگر است. ضخامت مرزدانهها در این نمونه نسبت به دو نمونه دیگر از مقدار کمتری برخوردار است. که نشان دهنده نزدیک بودن سرعت الکتروپولیش در درون دانه و مرزدانه میباشد.
با توجه به منحنی I-V، کمترین میزان چگالی جریان در الکترولیت S2 مشاهده شد. جریان کمتر در محدوده پایدار منحنی I-V نشان دهنده سرعت یکنواخت فرآیند الکتروپولیش در مناطق مختلف ریزساختار میباشد [19,2]. همچنین میزان حفرات به وجود آمده در سطح نمونه الکتروپولیش شده در محلول S2 کمتر از سایر نمونهها میباشد. با توجه به بررسیهای انجامی مقدار بهینه اسید پرکلریک در الکترولیت. به جهت داشتن سرعت برابر الکتروپولیش در نقاط مختلف ریزساختار، برابر 20 درصد حجمی بهدست آمد.
شکل (5) تصویر SEM از آلیاژ اینکونل 718 بعد از الکتروپولیش در الکترولیت S2 در سه دمای 35,25,15,0 درجه سانتیگراد را نشان میدهد. با توجه به شکل با کاهش دما از ضخامت مرزدانهها کاسته شده. و در نمونه الکتروپولیشی در دمای صفر درجه سانتیگراد (شکل 5-د) مرزدانهها تا حدود زیادی ناپدید شدهاند. مورالی و همکارانش [19] نشان دادند با کاهش دمای الکتروپولیش طول منطقه پایدار (ناحیه C-D) در منحنی I-V افزایش مییابد. ولی این مقدار کاهش دما باید در حد بهینه مد نظر قرار میگیرد. کاهش شدید دما، منجر به افت جریان و پرداخت ضعیف فرآیند الکتروپولیش میشود.
با دقت در شکل 5 مشخص میشود که با کاهش دما از 35 به 15 درجه سانتیگراد میزان حفرات متشکل. در داخل دانهها کاهش مییابد. از طرفی با کاهش مجدد دمای الکتروپولیش از 15 به صفر درجه سانتیگراد تعداد حفرات افزایش یافت. به عبارت دیگر در دمای صفر درجه سانتیگراد سرعت فرآیند الکتروپولیش. در بعضی نواحی به صورت ترجیحی افزایش یافت و منجر به شکلگیری حفرات در سطح گردید. پژوهشهای گذشته در زمینه الکتروپولیش فلزات نشان میدهد که جنس لایه متشکل در سطح فلز، اکسیدی و هیدرواکسیدی میباشد [21,9,11].
این لایه در حین فرآیند الکتروپولیش شکل میگیرد و تمام سطح آلیاژ را میپوشاند. ضخامت لایه اکسیدی به قابلیت تشکیل اکسید، هیدرواکسید و همچنین به عدم انحلال در الکترولیت وابستگی دارد. [19] که تمامی این موارد وابسته به دمای فرآیند الکتروپولیش میباشد. لایه چسبناک باعث کنترل جریان و نقل و انتقال یونهای فلزی از نمونه در حین الکتروپولیش میشود. با کاهش ضخامت لایه اکسیدی جریان افزایش پیدا می٬کند و انتقال جرم سریعتر صورت میگیرد.
به عبارتی عامل کنترل کننده سرعت الکتروپولیش لایه چسبناک اکسیدی میباشد [22]. با توجه به بررسیهای انجام شده مقدار بهینه دمای حمام جهت دستیابی به ریزساختاری یکنواخت و عاری از حفرات 15 درجه سانتیگراد انتخاب شد.
شکل (6) نشان دهنده نتایج آزمون زبری سنجی سطح آلیاژ اینکونل 718 بعد از الکتروپولیش در شرایط مختلف میباشد. با توجه به شکل (6) در نمونه الکتروپولیش شده با الکترولیت با کد S5. حداقل زبری سطح و برابر 0/026 میکرومتر حاصل گردید. که امری دور از انتظار نیست. با توجه به تصاویر شکل (5)، ریزساختار عاری از حفرات با مرزدانههایی با ضخامت کم. تنها در نمونه الکتروپولیشی در الکترولیت با کد S5 نمایان و مشخص میباشد.
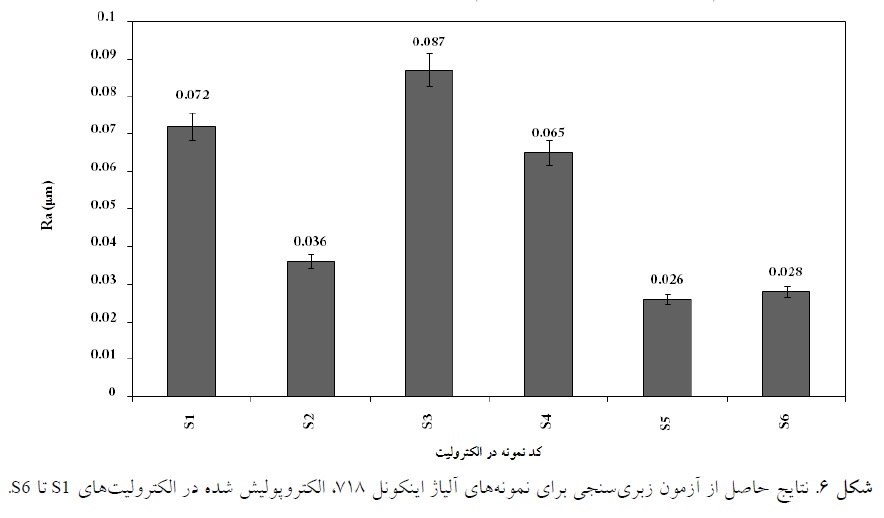
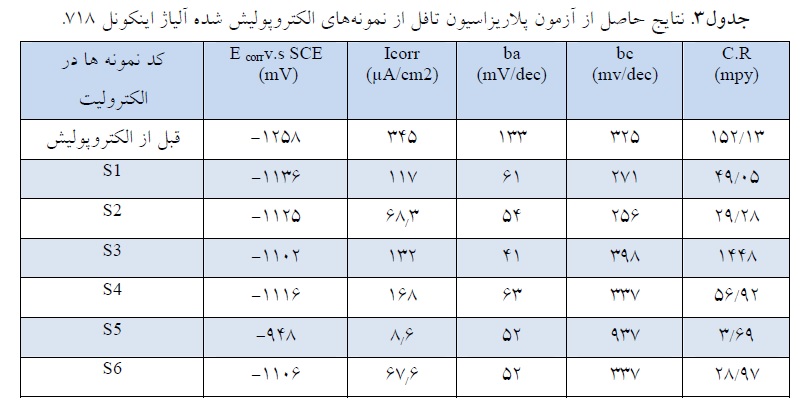
بررسی اثر دما و غلظت
2-3 اثر اکتروپولیش بر مقاومت به خوردگی
منحنی پلاریزاسیون تافل برای نمونههای الکتروپولیشی آلیاژ اینکونل 718 در شکل 7 و 8 نمایان و مشخص میباشد. با مقایسه نمودارهای پلاریزاسیون نمونهها، نمایان میشود که چگالی جریان خوردگی نمونههای الکتروپولیشی نسبت به قبل از الکتروپولیش کاهش مییابد. این مسأله نشان دهنده افزایش مقاومت به خوردگی نمونه بعد از الکتروپولیش نسبت به نمونه قبل از الکتروپولیش میباشد.
همچنین پتانسیل خوردگی نیز در این نمونهها بعد از الکتروپولیش به سمت مقادیر نجیبتر میل کرده است. با توجه به منحنیهای پلاریزاسیون در شکل 10، شدت جریان آندی در کلیه نمونهها. به طور تقریبی ثابت ولی شدت جریان کاتدی متفاوت میباشد.بنابراین کنترل کننده خوردگی نمونهها، واکنش کاتدی است.
جدول (3) نتایج حاصل از آزمون پلاریزاسیون تافل نمونهها را نشان میدهد. در خصوص نمونههای الکتروپولیشی، نجیبترین پتانسیل مربوط به نمونه مورد الکتروپولیش در الکترولیت با کد S5 و برابر 948- میلیولت میباشد.
با توجه به شکل (6) و جدول (3) با کاهش زبری سطح و کاهش حفرات در ریزساختار. و به طبع آن تشکیل لایه اکسیدی یکنواخت در ریزساختار آلیاژ. پتانسیل خوردگی به سمت مقادیر نجیب افزایش مییابد (اکسید کروم پایداری شیمیایی بالایی دارد). همچنین چگالی جریان خوردگی کاهش و به کمترین مقدار خود در نمونه مورد الکتروپولیش با الکترولیت با کد S5 و برابر 8/6 μA/cm2 میرسد. سرعت خوردگی در این نمونه عدد 3/69mpy محاسبه شد که نسبت به سایر نمونهها کمتر میباشد.
بررسی اثر دما و غلظت
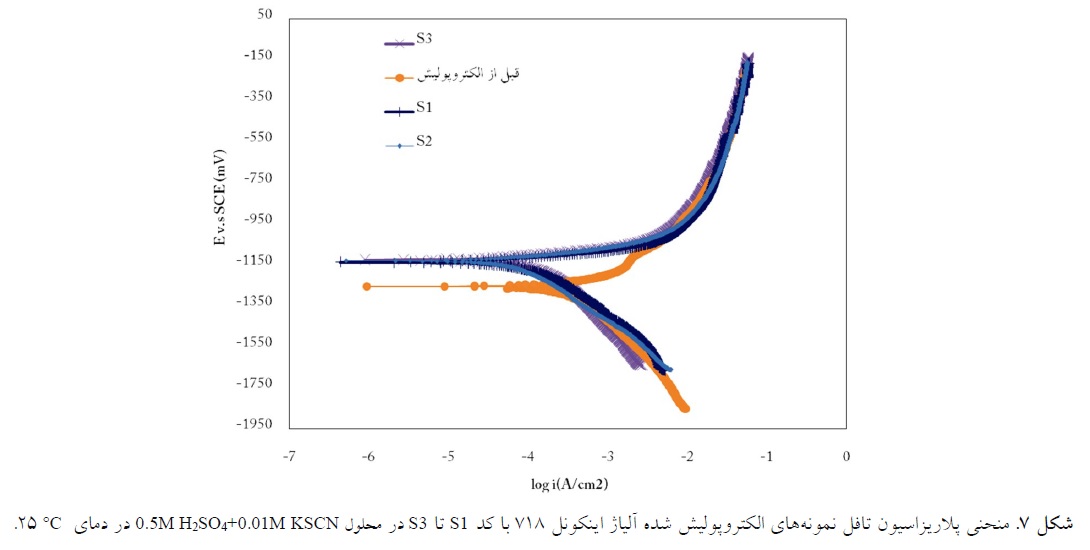
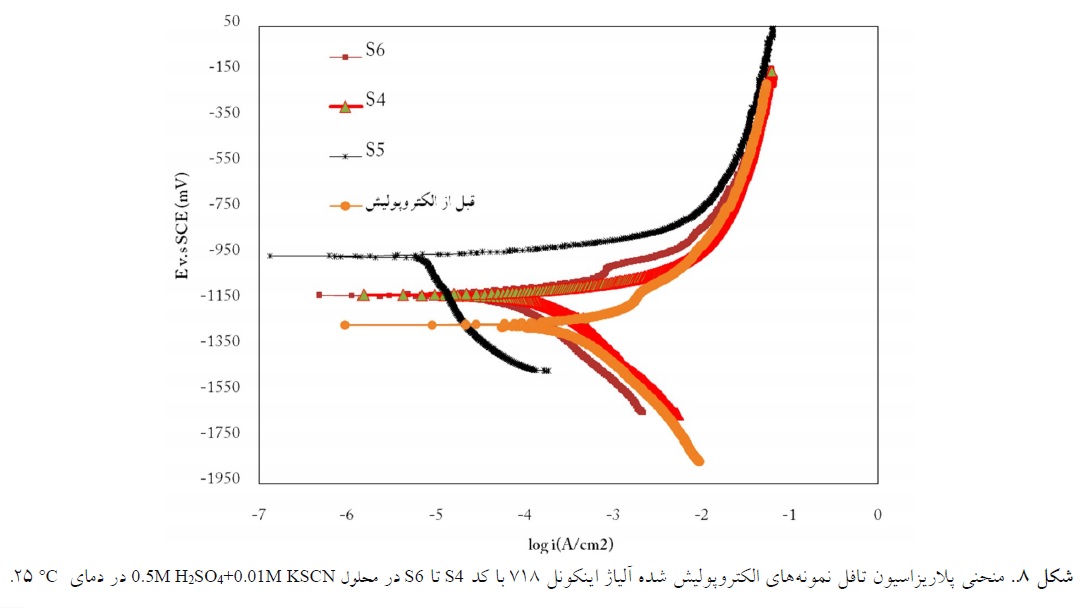
4-نتیجهگیری
در این تحقیق نمونههایی از آلیاژ اینکونل 718 در الکترولیت اسید پرکلریک/اسید استیک/آب در شرایط مختلف الکتروپولیش شد و نتایج زیر حاصل گردید:
1-از منحنی I-V بیشترین منطقه پایدار جریان جهت الکتروپولیش، در الکترولیت حاوی 20 درصد حجمی اسید پرکلریک حاصل گردید.
2-تصاویر حاصل از SEM نشان داد، فرآیند الکتروپولیش باعث بهبود کیفیت سطح و حذف آثار ناشی از عملیات سمبادهزنی گردید.
۳-با توجه به تصاویر SEM دمای بهینه حمام جهت الکتروپولیش آلیاژ اینکونل 718, 15 درجه سانتیگراد حاصل گردید.
4-کمترین مقدار زبری سطح بعد از الکتروپولیش عدد 0/026 میکرومتر حاصل شد که مربوط به نمونه الکتروپولیشی در شرایط بهینه غلظت و دما میباشد.
بررسی اثر دما و غلظت
5- منحنی پلاریزاسیون نمونهها در حالت قبل و بعد از الکتروپولیش نشان داد، مقاومت به خوردگی در اثر فرآیند الکتروپولیش افزایش قابل ملاحظهای مییابد.
حامد رحیمی،احسان صائب نوری
مرکز تحقیقات مواد پیشرفته، دانشکده مهندسی مواد، واحد نجف آباد، دانشگاه آزاد اسلامی، نجف آباد، ایران.
فولاد رسول دلاکان
با سالها تجربۀ ارزشمند و گرانبها در عرصه تأمین و توزیع انواع ورق آلیاژی و انواع فولاد آلیاژی. و با گواهینامه ها و آنالیزهای معتبری که ضمیمه محصولاتش به مشتریان خویش میها می کند. توانسته رضایتمندی مشتریان خویش را همواره فراهم آورد.
صنعتگر شریف و گرامی از اینکه ما را جهت خرید کالا (فولاد آلیاژی) مورد نیاز خویش. انتخاب می نمایید از شما سپاسگزاریم.
ارتباط با ما
02128423820 – 09122136675
واتس آپ: 09122136675 – فکس: 02128423820
اینستاگرام: fooladdalakan
ایمیل : fooladrasuldalakan@gmail.com