شبیه سازی اکستروژن لوله فولاد زنگ نزن آستنیتی AISI304-فروش استنلس استیل 304
شبیه سازی اکستروژن لوله فولاد زنگ نزن آستنیتی AISI 304 و مقایسه نتایج با روابط کران بالا
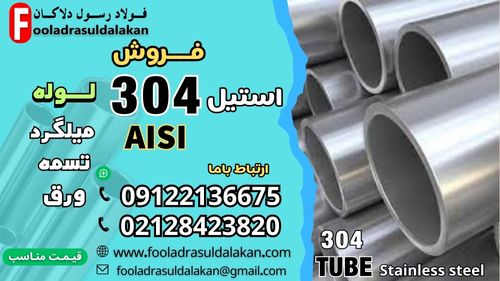
شبیه سازی اکستروژن
چکیده
هدف پژوهش، بررسی اثر دمای اولیه شمش، سرعت اکستروژن. نسبت اکستروژن و زاویه قالب روی فرایند اکستروژن لوله فولاد زنگ نزن 304. به ویژه نیروی اکستروژن و نیل به پارامترهای بهینه برای انجام فرایند بود. برای شبیه سازی نرم افزار آباکوس استفاده شد. دوازده نمونه با شرایط اولیه مختلف بررسی شد. با توجه به تقارن محوری فرایند، برای شبیه سازی مدل متقارن محوری دو بعدی استفاده شد. همچنین برای حل فرایند، حل جفت شده مکانیکی-حرارتی استفاده شد. برای نیل به درجه های آزادی مورد نیاز، از المان CAX4RT استفاده شد. دمای اولیه شدیدترین اثر را روی نیروی اکستروژن دارد. نتایج شبیه سازی با نتایج تحلیل ریاضی انطباق خوبی را نشان داد.
واژه های کلیدی: اکستروژن لوله، فولاد زنگ نزن AISI 304، شبیه سازی، روش تحلیلی حد بالایی
Numerical Simulation of Tube Exrusion process of AISI304 and Comparing with Upper Bound Solutions
M.R. Bahmani K.Farmanesh G.Borhani
Abstract
The study purpose was to evaluate the effect of initial billet temperature, extrusion speed, extrusion ratio and angle on the tube extrusion process of AISI304. particularly the extrusion force, and achieve optimal parameters. Abaqus software was used for the simulation purpose. 12 samples were evaluated with different initial conditions. Two – dimensional axisymmetric model was used to simulate the process, due to the axial symmetry of the process. Mechanical – thermal coupled solution was used fo process solution. Also, CAX4RT elements were used fo achieving all the degress of freedom. The initial temperature was found to have the strongest effect on the force.
key words Tube Extrusion; AISI 304 Stainless steel; Simulation; Upper Bound Method.
مقدمه
اکستروژن یکی از فرایندهای معمول شکل دهی حجیم برای تغییر شکل مواد به محصولات نیمه تمام است [1]. یکی از محصولاتی که با این روش تلوید می شود، لوله های بدون درز است. لوله بدون درز فولاد زنگ نزن AISI 304، قطعه مهمی است. که در صنعت نفت، صنعت حمل و نقل و صنایع دفاع کاربرد وسیعی دارد. که به طور عمده به علت مقاومت به خوردگی، و اکسید شدن عالی آن و کارایی خوب آن تحت دماهای بالا و پایین است [2].
لوله های بدون درز فولاد زنگ نزن، می تواند توسط روش اکستروژن با استفاده از شیشه به عنوان روانکار، تولید شود. فرایند در دمای بالا انجام می شود و با تغییر شکل های بزرگ و نرخ کرنش های بالا مرتبط است.
بطور معمول، تحلیل فرایند شکل دهی فلزات، با استفاده از شیوه های تحلیلی، عددی، یا فیزیکی انجام می شود [3]. به علت پیچیدگی رابطه های درگیر در شیوه تحلیلی، چنین روش هایی تنها برای حالت هندسی و شرایط مرزی ساده کاربرد دارد [3]. طراحی، کنترل و بهینه سازی فرایند شکل دهی، به دانش تحلیلی در زمینه سیلان فلز، تنش ها و انتقال حرارت و همچنین اطلاعات فنی مربوط به روانکاری، تکنیک های گرم کردن و سرد کردن، جابجایی مواد، طراحی قالب و تولید و تجهیزات شکل دهی نیاز دارد [4].
هدف اصلی استفاده از تحلیل در شکل دهی فلزات، تحقیق در مورد مکانیک فرایندهای تغییر شکل پلاستیک با اهداف عمده ززیر می باشد.
. تعیین روابط حرکتی (شکل، سرعت ها، نرخ کرنش و کرنش). بیش شمش خام یا قطعه نیمه تمام و محصول نهایی، برای مثال پیش بینی سیلان فلز در حین عملیات شکل دهی می باشد.
. تعیین حدود شکل پذیری یا قابلیت تولید.
. پیش بینی تنش ها، نیروها، و انرژی لازم برای انجام عملیات شکل دهی [4].
بهینه سازی فرایند اکستروژن صنعتی اغلب روی روش تجربی استوار می باشد. که نتیجه آن محدودیت در بهره وری می باشد. از طرفی با توجه به اینکه پیش بینی های سریع توسط شبیه سازی های کامپیوتری انجام می شود. که در بهبود قابلیت رفتار یکپارچه بار اعمالی و تجهیزات داخلی فرایند مؤثر است [5]. می توان با شبیه سازی فرایند اکستروژن به شرایط بهینه ای برای انجام عملی این فرایند رسید.
شبیه سازی اجزای محدود ابزاری مهم در طراحی و توسعه اکستروژن و فرایندهای دیگر تولیدی می باشد. بیشترین کارهای شبیه سازی در مورد اکستروژن آلومینیم است. ولی کارهایی نیز در زمینه اکستروژن فولاد و تیتانیم انجام شده [6] است. که از آن جمله می توان به کارهای دامو داران و شیوپوری [7]، لی و همکاران [8] روی تیتانیم و کارهای هانسون [11]، جانسون و هانسون [6]، سزار کوفسکی و همکاران [12] و هانسون و دامکین [13] روی فولاد اشاره کرد.
شبیه سازی اکستروژن با استفاده از روش اجزای محدود، در طول دهه گذشته عادی تر می باشد. معمول ترین روش در این نوع شبیه سازی، استفاده از دمای شمش یکنواخت به عنوان شرایط اولیه در مدل اکستروژن است. حالت اولیه گرم کردن و حمل و نقل، اغلب نادیده گرفته می شود [14]. هرچند روش اجزای محدود می تواند مبنای درستی برای مطالعه و بهینه کردن تغییر شکل اتفاق افتاده در فرایند اکستروژن پیچیده فراهم کند، نمی تواند ابزار را طراحی کند [15].
اهمیت مدل سازی و شبیه سازی در صنعت شکل دهی فلزات به سختی در طول دهه های گذشته افزایش یافته است [16]. استفاده از روش المان محدود برای شبیه ساززی فرایندهای شکل دهی فلزات در اواخر دهه 1960 آغاز شد. از جمله اولین کسانی که برای حل مسأله خود از این روش استفاده کردند. باید به مارشال و کینگ در سال 1967 و لی کوبایاشی در سال 1970 اشاره کرد که با مسائل الاستیک-پلاستیک سروکار داشتند [17].
شبیه سازی فرایند با استفاده از روش المان محدود در حال حاضر به عنوان یک ابزار مهم برای توسعه محصول و فرایند قابل پذیرش است. با این حال، معرفی شبیه سازی کامپیوتری در تکنولوژی اکستروژن به سرعت دیگر بخش های صنعت تولید نبوده است. این موضوع در اصل به دلیل تغییر شکل های بسیار بزرگی است. که این شبیه سای را از لحاظ فنی به چالش کشیده و کامپیوتر طلب کرده است. شبیه سازی فرایندهای اکستروژن گرم به وضوح یکی از مشکل ترین مسائل در مدل سازی فرایند است [16].
با این حال، پتانسیل استفاده از روش های عددی برای تجزیه و تحلیل اکستروژن بالا می باشد. اهمیت فرایند کلی، از جمله حالت ناپایدار اولیه اکستروژن، می تواند تجزیه و تحلیل شود [18]. برای مثال تکامل تنش، نرخ کرنش و دما در مواد در طول فرایند را می توان در جزئیات مورد مطالعه قرار داد. چون ظرفیت سخت افزاری و نرم افزاری رایانه در حال افزایش است. بدون شک روش اجزای محدود یک ابزار پرکاربرد برای توسعه و بهینه سازی اکستروژن است.
در این کار براساس مطالعاتی که روی کارهای قبلی انجام گرفت. سعی بر این است که شرایط بهینه ای از فرایند اکستروژن برای تولید لوله های فولاد زنگ نزن بدست آید. این شرایط شامل دمای اولیه شمش، نسبت اکستروژن، سرعت اکستروژن و زاویه قالب برای به حداقل رسانی نیروی مورد نیاز برای فرایند می باشد.
از دیگر اهداف این تحقیق بدست آوری منحنی های تنش – کرنش و نرخ کرنش در منطقه تغییر شکل. و در شرایط اولیه مختلف، و مقایسه آن با نتایج حاصل از روابط تحلیلی. و همچنین نیل به شرایط و پارامترهای بهینه برای دست یابی به کمترین نیروی اکستروژن در انجام فرایند می باشد. افزایش دمای سطح خروجی نیز در حین فرایند مورد بررسی قرار می گیرد و با نتایج حاصل از روابط تحلیلی مقایسه می شود.
شرح فرایند اجزای محدود
هندسه مدل و شرایط اولیه آن. با توجه به هندسه متقارن محوری فرایند اکستروژن، مدل اجزای محدود دو بعدی متقارن محوری استفاده شد. شکل (1) مدل اولیه را پس از چیدمان اجزا در کنار هم نشان می دهد. همانطور که در شکل (1) نمایان و مشخص است، سنبه متحرک و متصل به فک مدل گردید. ابعاد مدل اولیه برای اکستروژن لوله فولاد زنگ نزن 304 AISI در جدول (1) معلوم و مشخص است. سایر پارامترهای اولیه مدل اکستروژن در جدول (2) نمایان و مشخص است.
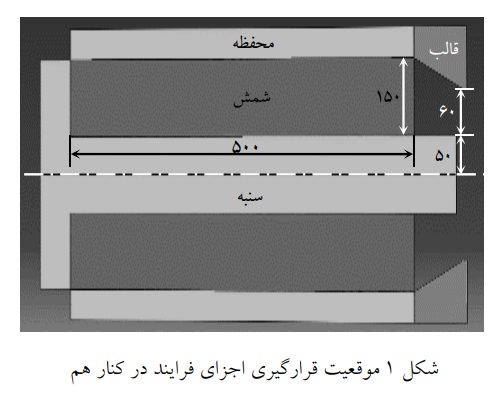
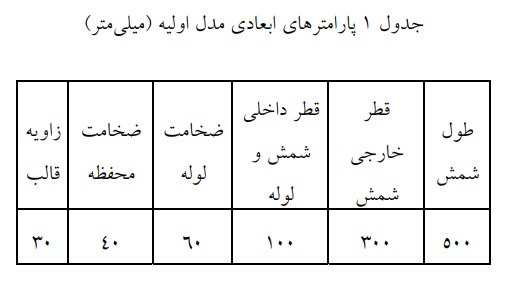
شمش اولیه در مدل سازی به صورت پیش سوراخی در نظر گیری شد. همچنین از خواص فولاد زنگ نزن 304 AISI مورد بکارگیری برای شمش اولیه و خواص فولاد مقاوم به حرارت AISI H13. برای مدل سازی تجهیزات فرایند استفاده شد.
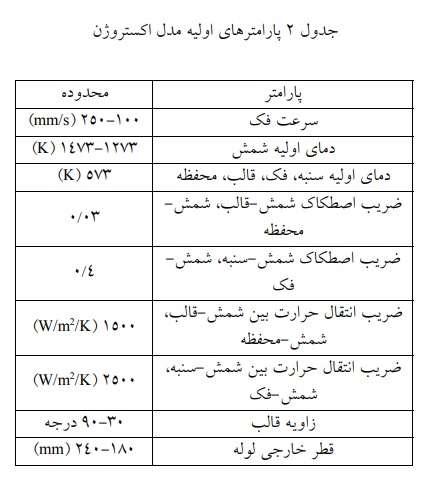
گام تحلیل و طراحی مش. با توجه به شرایط تعیینی تحقیق و شرایط فرایند که در آن. تحلیل تنش در طول فرایند وابستگی به توزیع دما و همچنین توزیع دما دارای وابستگی به حل تنش بود. در این تحقیق از تحلیل جابجایی حرارتی کاملاً جفت شده ( Dynamic, Temp-disp,Explicit) استفاده شد. که در آن حل های مکانیکی و حرارتی به صورت همزمان استخراج می شود.
برای مش بندی نمونه، پس از بررسی المان های گوناگون با درجات آزادی مختلف. و با توجه به شرایط مدل که یک مدل دوبعدی متقارن بکارگیری شد. و نوع تحلیل که از تحلیل جابجیایی- حرارتی کاملاً جفتی بکارگیری شد. برای دستیابی به درجات آزادی مورد نیاز تحلیل، از المان CAX4RT روی نمونه استفاده شد. این المان یک المان چهارگوش متقارن محوری جفتی حرارتی-مکانیکی با چهار گره می باشد که همزمان به جابجایی و دما وابستگی دارد. مش بندی مدل با این المان و با استفاده از روش مش بندی لاگرانژی-اویلری اختیاری انجام شد. شکل (2) مدل مش بندی شده را نشان می دهد.
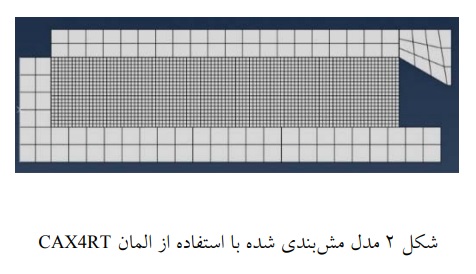
شرایط مدل. در این تحقیق اثر پارامترهای اولیه روی فرایند با تغییر آنها مورد بررسی قرار گرفت. جدول (3) مدل های مورد بررسی و شرایط آنها را نشان می دهد. همچنین مدل های ایجادی در نرم افزار آباکوس 6 و با استفاده از روش حل صریح، حل شد.
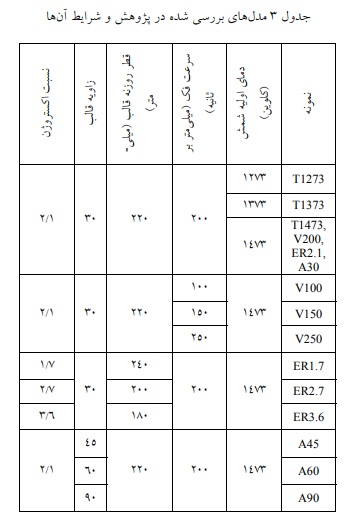
شرح حل تحلیلی
برای حل تحلیلی فرایند از روش تحلیل کران بالایی استفاده شد. در این، حل ها با کمینه ساختن توان کل فرمول سازی شده، پیدا می شوند که این کار با انتخاب میدان سرعت جنبشی قابل قبول انجام می شود [19]. منطقه تغییر شکل با سطح یک قالب، سطح یک سنبه استوانه ای و دو سطح عمودی در ورودی قالب (یا شروع منطقه مرده). و خروجی قالب محدود شده است. این منطقه در شکل (3) نمایان و مشخص است. در این منطقه میدان سرعت در سیستم مختصات استوانه ای به صورت زیر می باشد [20].
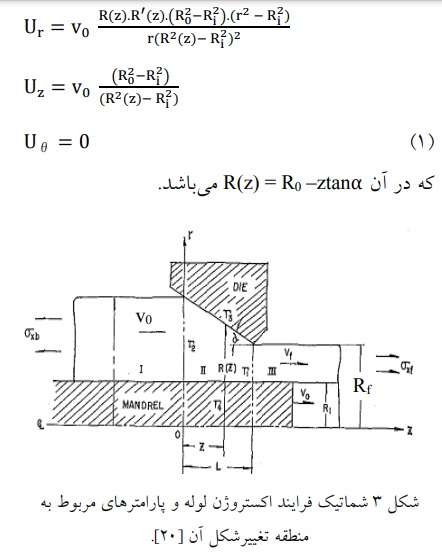
تغییر شکل تنها در این منطقه اتفاق می افتد. در سیستم مختصات استوانه ای، نرخ کرنش با مشتق گیری از میدان های سرعت، از رابطه های زیر بدست می آید [20].
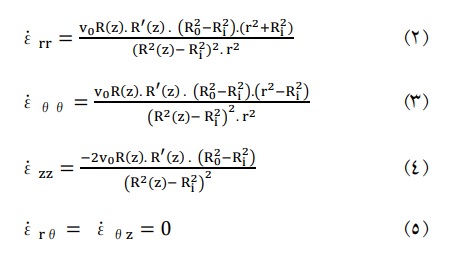

همچنین نرخ کرنش متوسط در طول فرایند اکستروژن از رابطه پیشنهادی فلثام محاسبه می شود [21].

اما برای محاسبه نیروی اکستروژن باید توان تغییر شکل ماده در فرایند اکستروزن را محاسبه کرد. توان بیرونی برای تغییر شکل ماده در فرایند اکستروژن لوله توسط رابطه زیر محاسبه می شود [22].

با بدست آوردن توان هر یک از سطوح در منطقه تغییر شکل و محاسبه توان کل، توان کل محاسبه شده را با رابطه (8) معادل سازی کرده که نتیجه آن بدست آوردن فشار اکستروژن از رابطه زیر می باشد [22].
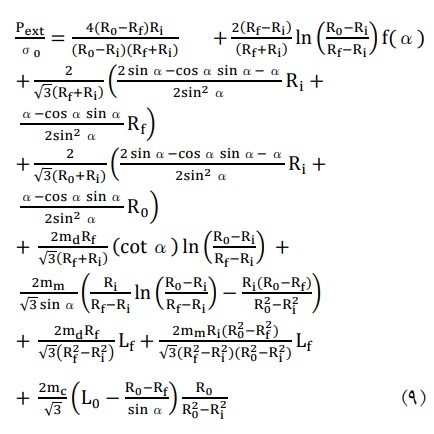
در این رابطه تابع f(a) با استفاده از رابطه زیر محاسبه می شود [22].
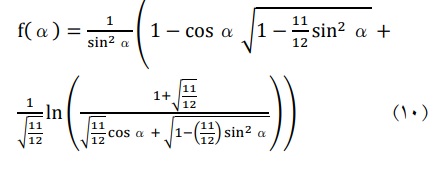
همچنین σ0 که برابر با تنش میانگین است. از رابطه زیر بدست می آید [23].

در فرایند اکستروژن داغ با توجه به بالا بودن دما، تنش سیلان به تغییرات دما وابسته بوده. و همچنین نرخ کرنش نیز در مقدار آن مؤثر است. جانسون و کوک رابطه ای را برای تنش سیلان ارائه دادند. که وابستگی آن به کرنش، نرخ کرنش و دما را در نظر گرفتند. این رابطه به صورت زیر می باشد [24].
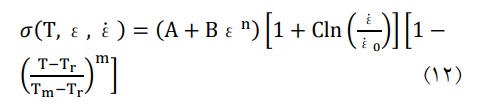
پارامترهای این رابطه برای فولاد زنگ نزن 304 در جدول (4) نمایان و مشخص است.
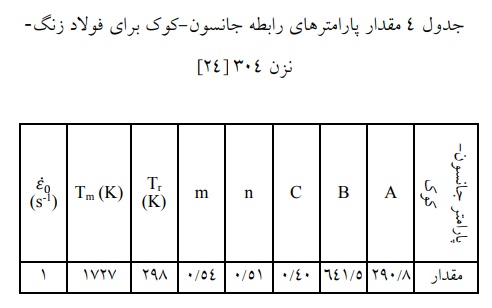
برای اینکه بتوان از رابطه استفاده کرد. نیاز به محاسبه نرخ کرنش فرایند است. نرخ کرنش متوسط در طول اکستروژن با استفاده از رابطه (7) محاسبه می شود.
اما در شکل دهی حرارتی، دمای قطعه به دلیل تغییر شکل حرارتی افزایش می یابد که این افزایش دما با استفاده از رابطه زیر محاسبه می شود [25].

همچنین در اثر اصطکاک بین شمش و قالب، مقداری حرارت تولید می شود که از آن در محاسبات صرفنظر شد.
نتایج بحث
اثر پارامترهای اولیه روی نیروی اکستروژن. شکل (4) منحنی نیروی اکستروژن برحسب مسافت فک را در دمای اولیه شمش مختلف نشان می دهد. همانطور که مشاهده می شود. در ابتدای فرایند، نیروی اکستروژن به سرعت افزایش یافت تا به مقدار بیشینه خود برسد. پس از نیل نیروی اکستروژن به مقدار بیشینه مورد نیاز فرایند، روند کاهشی آن شکل می گیرد. در واقع در ابتدا به دلیل وجود اصطکاک در فصل مشترک شمش و تجهیزات، نیروی اکستروژن به مقدار بیشینه خود می رسد. و سپس به حالت پایدار می رسد [25]. این روند در کارهای [26,12,11] نیز مشاهده شده است.
طبق آنچه قبلاً گفته شد، با افزایش دمای اولیه شمش، نیروی اکستروژن کاهش می یابد [27] که شکل 5 این کاهش را به وضوح نشان می دهد. این در حالی است با افزایش 200 درجه ای دما از 1273 کلوین به 1473 کلوین. نیروی اکستروژن از حدود 20 مگانیوتن به 10 مگانیوتن کاهش پیدا کرده است. که نشان دهنده کاهش شدید در نیروی اکستروژن می باشد. در واقع با افزایش 200 درجه ای دمای اولیه شمش، نیروی اکستروژن به نصف می رسد. علت این موضوع به اثر دما روی تنش سیلان مربوط می باشد. در واقع با افزایش دمای شمش، تنش سیلان ماده کاهش می یابد و لذا مقاومت ماده در برابر تغییر شکل کاهش می یابد. که این امر باعث کاهش نیروی اکستروژن می شود.
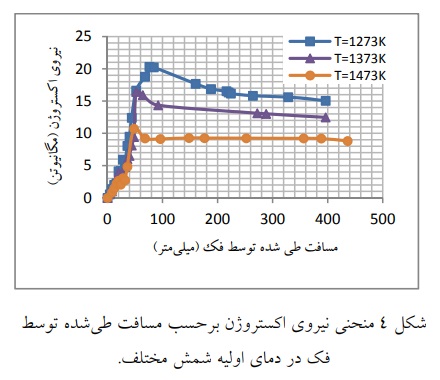
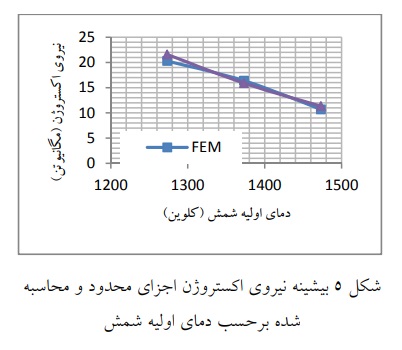
برای بررسی صحت نتایج، نیروی اکستروژن با استفاده از رابطه (9) محاسبه شد. و با نتایج حاصل از مدل قیاس گردید. که حاصل این قیاس در شکل (5) وجود دارد. این شکل بیشینه نیروی اکستروژن حاصل از مدل و مورد محاسبه را بر حسب دمای اولیه شمش نشان می دهد.
مقایسه نتایج نشان می دهد تطابق نتایج حاصل از مدل و محاسبه گردید. به گونه ای که حداکثر اختلاف بین نتایج 5% است. که این میزان خطا در نتایج مدل قابل قبول است.
شکل (6) منحنی نیروی اکستروژن بر حسب مسافتی که طی می شود توسط فک را در سرعت اکستروژن های مختلف نشان می دهد. در این شکل نیز مشابه شکل (4)، نیروی اکستروژن در ابتدای فرایند با افزایش سریع، به مقدار بیشینه خود می رسد. و پس از آن روند کاهشی آن شکل می گیرد.
منحنی های شکل (6) به طور واضح اثر ناچیز سرعت اکستروژن را روی نیروی اکستروژن نمایش می دهند. در واقع طبق آنچه در این شکل مشخص است. با افزایش سرعت اکستروژن از 100 به 250 میلی متر بر ثانیه، تنها یک مگانیوتن به نیروی اکستروژن افزون گردید.
در شکل (7) بیشینه نیروی اکستروژن حاصل از شبیه سازی و روابط تحلیلی در سرعت های مختلف نمایان و مشخص است. طبق این شکل با افزایش سرعت اکستروژن، نیروی اکستروژن افزایش می یابد. که این افزایش ناچیز است و قابل صرف نظر است. لذا می توان گفت افزایش سرعت اکستروژن اثر چندانی روی نیروی اکستروژن ندارد. که این موضوع در کار یانگ و همکاران [26] نیز مشاهده شد. هر چند در این کار مشخص شد که کاهش بیش از حد سرعت اکستروژن باعث کاهش دمای شمش در حین فرایند. و لذا باعث افزایش نیروی اکستروژن می شود.
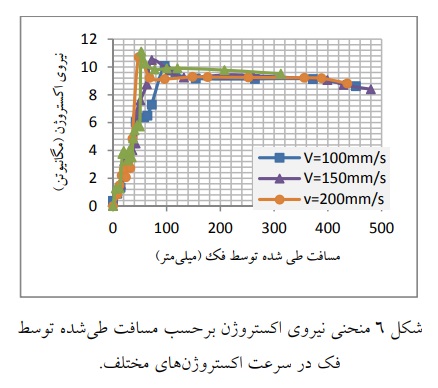
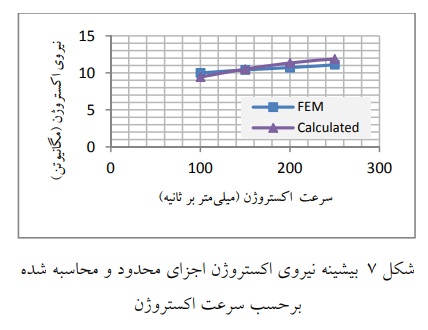
با مقایسه نتایج حاصل از مدل و نتایج محاسبه شده، حداکثر اختلاف بین نتایج حدود 6% است. که این میزان خطا در نتایج مدل قابل قبول است. و لذا می توان صحت نتایج حاصل از مدل را تأیید کرد.
شکل (8) منحنی نیروی اکستروژن بر حسب مسافت فک را در نسبت اکستروژن های مختلف نشان می دهد. در این شکل نیز روند منحنی نیرو مشابه شکل های (4 و 6) است.
همانطور که در منحنی های شکل (8) مشخص است. نسبت اکستروژن روی نیروی اکستروژن اثر قابل قبولی دارد. در واقع طبق آنچه در این شکل مشخص است. با افزایش نسبت اکستروژن از 2/1 به 3/6، نیروی اکستروژن از حدود 11 مگانیوتن به حدود 19 مگانیوتن می رسد. علت این افزایش را می توان در نحوه جریان یافتن ماده در نسبت اکستروژن های مختلف جست و جو کرد.
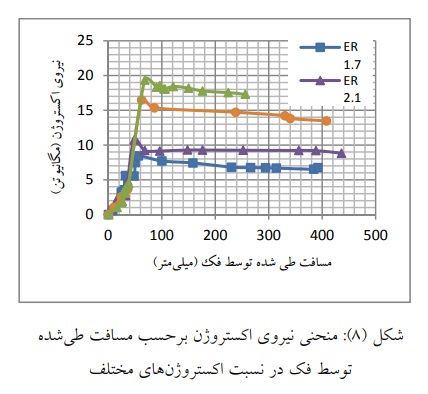
با افزایش نسبت اکستروژن، جریان ماده در کناره ها، که در تماس با سطح قالب و سنبه است. کند شده و در مرکز آن جریان ماده تندتر خواهد بود. این حالت جریان باعث آشفتگی حرکت ماده در خروج از قالب شد و مانع از نیل شمش به حالت پایدار می رسد. لذا برای گذر از این حالت و نیل به حالت پایدار (ناحیه 2 در منحنی نیروی اکستروژن)، نیروی بیشتری به شمش وارد می شود. شکل (9) جریان ماده را در زمان 0/4 ثانیه برای نسبت اکستروژن های مختلف نشان می دهد.
همانطور که در شکل (9) مشاهده می شود. با افزایش نسبت اکستروژن، تلاطم در جریان ماده بیشتر شده و ماده به صورتی خارج می شود. که مرکز آن زودتر از کناره ها از قالب خارج می شود. در [23] نیز به این موضوع اشاره شده است.
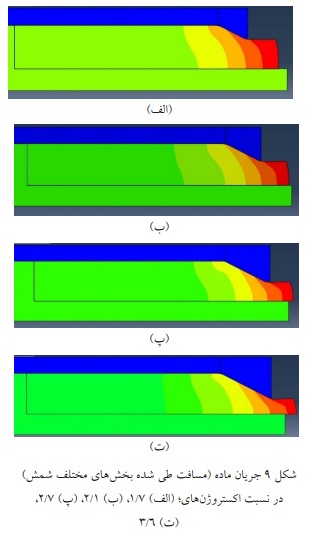
در شکل (10) بیشینه نیروی اکستروژن حاصل از شبیه سازی و روابط تحلیلی در نسبت های اکستروژن مختلف نشان دهی شد. طبق این شکل با افزایش نسبت اکستروژن، نیروی اکستروژن با افزایش قابل توجهی روبرو گردید. با توجه به شکل، می توان گفت با دو برابر شدگی نسبت اکستروژن، نیروی اکستروژن نیز تقریباً به دو برابر مقدار خود می رسد. با این حال، نسبت اکستروژن بعد از دمای اولیه شمش، بیشترین اثر را روی نیروی اکستروژن دارد و طبق آنچه در کار هانسون و جانسون [12] نیز مشاهده شد. دمای اولیه شمش شدیدترین اثر را روی نیروی اکستروژن دارد.
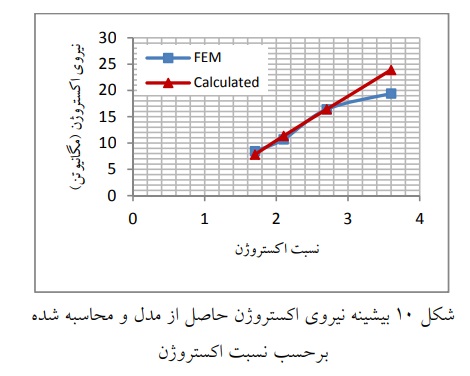
با مقایسه نتایج حاصل از مدل و نتایج مورد محاسبه ، حداکثر اختلاف بین نتایج حدود 18% است. که این میزان خطا را می توان ناشی از تولید حرارت در اثر اصطکاک قالب و شمش دانست که در محاسبات در نظر قرار نگرفت. شکل (11) منحنی نیروی اکستروژن بر حسب مسافت فک را در زاویه قالب های مختلف نشان می دهد. در این شکل نیز تغییرات نیروی اکستروژن مشابه شکل های (8,6,4) میباشد.
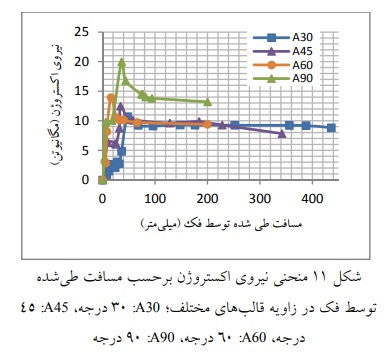
همانطور که در منحنی های شکل (11) مشخص است. زاویه قالب روی نیروی اکستروژن اثرگذار هست. طبق آنچه در شکل مشخص است. افزایش زاویه قالب، باعث افزایش نیروی اکستروژن می شود. و تغییر زاویه قالب از 30 درجه به 60 درجه موجب افزایش نیروی اکستروژن از حدود 10 مگانیوتن به حدود 14 مگانیوتن می شود. همچنین با تغییر زاویه قالب به 90 درجه و در واقع استفاده از قالب مسطح، نیروی اکستروژن به حدود 20 مگانیوتن خواهد رسید. علت این افزایش را علاوه بر آنچه قبلاً در مورد جریان ماده بیان شد. می توان به شکل گیری منطقه مرده در پشت قالب، با افزایش زاویه آن، مرتبط دانست.
با افزایش زاویه قالب، به علت کاهش سیلان ماده، جریان ماده در کناره ها، که در تماس با سطح قالب و سنبه است. کند می شود و در مرکز آن جریان ماده تندتر خواهد بود. این کندی جریان در کناره ها باعث می شود. که برای عبور از قالب، به نیروی بیشتری نیاز شود. که نیروی اضافی صرف عبور ماده از پشت قالب می شود. شکل (12) جریان ماده را در زمان 0/4 ثانیه برای زاویه قالب های مختلف نشان می دهد.
همان طور که در شکل مشاهده می شود. با افزایش زاویه قالب، تلاطم در جریان ماده بیشتر می شود و ماده به – صورتی خارج می شود. که مرکز آن زودتر از کناره ها از قالب خارج می شود. در [23] و همچنین در کار سفوقلو و گدیکلی [3] نیز به این موضوع اشاره شده است. این تلاطم در جریان ماده به گونه ای است که با افزایش زاویه مشخصی، بین لایه های ماده در پشت قالب، برش ایجاد می شود. و ماده در پشت قالب، جریان می یابد. که این جریان ماده در شکل های (12-پ و 12-ت) مشخص است.
شکل (13) بیشینه نیروی اکستروژن حاصل از شبیه سازی و روابط تحلیلی را در زاویه قالب های مختلف نشان می دهد. با توجه به شکل و نتایج حاصل از مدل، می توان گفت با تغییر زاویه قالب از 30 درجه به 90 درجه. (تغییر نوع قالب از قالب مخروطی به قالب مسطح)، نیروی اکستروژن تقریباً دو برابر می شود. در واقع می توان گفت افزایش زاویه قالب و تغییر نوع قالب از مخروطی به مسطح باعث افزایش نیروی اکستروژن می شود.

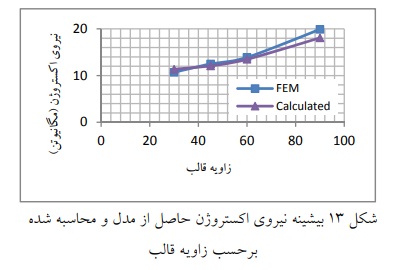
با مقایسه نتایج حاصل از مدل و نتایج مورد محاسبه، حداکثر اختلاف بین نتایج حدود 9% است. که علت این میزان خطا را نیز مشابه آنچه قبلاً بیان شد، می توان ناشی از تولید حرارت در اثر اصطکاک قالب. و شمش دانست که در محاسبات مدنظر قرار نگرفت.
اثر پارامترهای اولیه روی نرخ کرنش و اجزای آن. از آنجایی که در شبیه سازی فرایند از مدل متقارن محوری دوبعدی استفاده شد. لذا نتایج مورد حاصل نیز در مختصات استوانه ای می باشد. شکل (14) مؤلفه های نرخ کرنش حاصل از اجزای محدود و روابط محاسباتی (رابطه (2). تا رابطه (6)) را در منطقه تغییر شکل (دهانه ورودی قالب تا دهانه خروجی قالب) در دماهای اولیه شمش مختلف نشان می دهد. به جز نرخ کرنش در جهت اکستروژن، جهت سایر اجزای نرخ کرنش در خلاف جهت خود و به سمت خروج قالب می باشد.
منحنی های موجود در شکل نشان می دهد که دمای اولیه شمش، نرخ کرنش را تحت تأثیر قرار نمی دهد. هرچند اختلاف ناچیزی بین منحنی نرخ کرنش در دماهای مختلف وجود دارد. که قابل چشم پوشی است. همچنین بین نتایج حاصل از مدل و روابط برای نرخ کرنش جزئی، انطباق مشهود است. همچنین شکل (14) نشان می دهد که با نزدیک شدن به خروجی قالب، نرخ کرنش های جزئی افزایش می یابد. وجود نرخ کرنش در جهت θ (شکل 14-ج) بیانگر آن است. که در حین تغییر شکل شمش و خروج آن از قالب، شمش دچار پیچش نیز می شود.
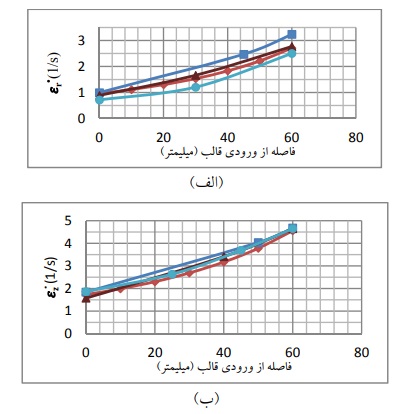
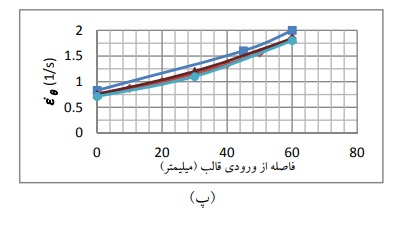
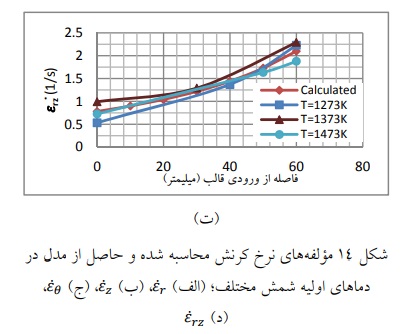
از آنجایی که بیشترین سرعت حرکت ماده در لحظه خروج از قالب است. اجزای نرخ کرنش نیز در خروجی قالب به مقدار بیشینه خود می رسند که این موضوع در شکل (14) به وضوح مشخص است.
در شکل (15) نرخ کرنش متوسط حاصل از مدل و محاسبه شده با استفاده از رابطه (7). در منطقه تغییر شکل، بر حسب دمای اولیه شمش نمایان و مشخص است. نتایج نشان می دهد. که با افزایش دما تغییر چندانی در نرخ کرنش متوسط در منطقه تغییر شکل ایجاد نمی شود.
با این وجود، با توجه به روابط مربوط به مؤلفه های نرخ کرنش (رابطه (2) تا رابطه (6)). و همچنین رابطه (7) که مربوط به نرخ کرنش متوسط است، مشاهده می شود. که نرخ کرنش یک پارامتر هندسی بوده و مستقل از دما می باشد. لذا این افزایش ناچیز در اثر تغییر دما نبوده و به همراه اختلاف بین نتایج محاسبه شده. و نتایج حاصل از مدل، می تواند به شرایط محاسباتی مدل برگردد.
شکل (17) نرخ کرنش در جهت اکستروژن را برای نتایج حاصل از مدل اجزای محدود و نتایج مورد حاصل از رابطه (4) نشان می دهد. با افزایش زاویه قالب، نرخ کرنش افزایش یافته است. این افزایش را می توان با مقایسه مقدار نرخ کرنش در خروجی قالب مشاهده کرد. به طوری که در زاویه قالب 30 درجه، نرخ کرنش در خروجی قالب. حدود 4.5 برثانیه و در زاویه قالب 45 درجه، نرخ کرنش در خروجی قالب، حدود 10 برثاینه می باشد.
برای بیان بهتر و مشاهده واضح تر هندسی بودن نرخ کرنش. نتایج مربوط به نرخ کرنش متوسط که مدل اجزای محدود و روابط تحلیلی مورد حاصل است. در شکل (16) برای تغییر سرعت اکستروژن، نسبت به اکستروژن و زاویه قالب، نمایان و مشخص است.
همانطور که در شکل (16) مشاهده می شود. سرعت اکستروژن و نسبت اکستروژن روی نرخ کرنش متوسط اثر مستقیم دارد. ولی نرخ کرنش متوسط مستقل از زاویه قالب است که این موضوع در رابطه (7) نیز به وضوح مشخص است. با این حال، با توجه به شکل (17) و روابط (2) تا (6)، زاویه قالب روی مؤلفه های نرخ کرنش مؤثر است.
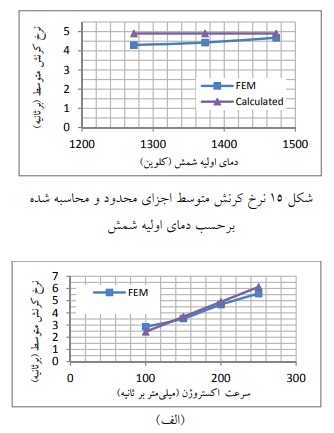
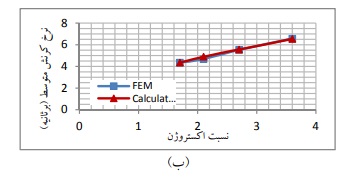
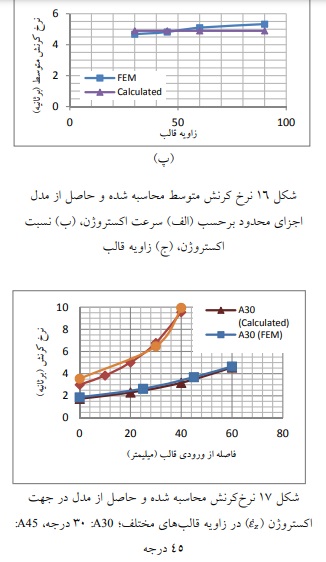
طبق آنچه در شکل های (16 و 17) مشاهده می شود. نتایج حاصل از مدل اجزای محدود و نتایج حاصل از روابط تحلیلی، انطباق خوبی را نشان می دهد. و حداکثر اختلاف بین نتایج حدود 8% بوده که قابل قبول می باشد.
اثر پارامترهای اولیه روی تنش سیلان. شکل (18) منحنی های تنش سیلان بر حسب کرنش پلاستیک حاصل از مدل اجزای محدود. و رابطه (12) را در دماهای اولیه شمش مختلف، سرعت اکستروژن های مختلف. نسبت اکستروژن های مختلف و زاویه قالب های مختلف نشان می دهد. همانطور که در منحنی های مربوط به مدل اجزای محدود مشاهده می شود. تنش سیلان ابتدا افزایش یافته و سپس به حالت تقریباً ثابتی می رسد. همچنین مقدار تنش سیلان با افزایش دما، کاهش می یابد. و با افزایش سرعت اکستروژن و نسبت اکستروژن، افزایش یافت. با این حال منحنی های مربوط به رابطه (12) سیر صعودی را در تنش سیلان نشان می دهد.
روند صعودی موجود در منحنی های مربوط به رابطه (12) به این علت است. که در محاسبات انجام شده، افزایش دما در حین فرایند، در رابطه در نظر گرفته نشد. در واقع با ثابت فرض کردن دما در محاسبات، با افزایش کرنش، تنش سیلان ماده نیز افزایش می یابد.
این در حالی است که در شرایط واقعی، کار مکانیکی باعث افزایش دما می شود. و در اکستروژن نیز با توجه به اینکه تغییر شکل شدید انجام می شود. حرارت تولید می شود. به گونه ای که این تولید حرارت که حدود 98% کار انجامی را شامل می شود. علاوه بر اینکه با افت دما در قطعه به علت انتقال حرارت بین شمش و تجهیزات فرایند مقابله می کند. باعث افزایش دما قطعه نیز می شود. این افزایش دما باعث کاهش مقاومت ماده در برابر تغییر شکل و در پی آن کاهش تنش سیلان ماده می شود.
شکل (19) بیشینه افزایش دما را در دو حالت نتایج حاصل از مدل اجزای محدود و نتایج حاصل از محاسبه رابطه (13). در دماهای اولیه مختلف، سرعت اکستروژن های مختلف و نسبت اکستروژن های مختلف نشان می دهد.
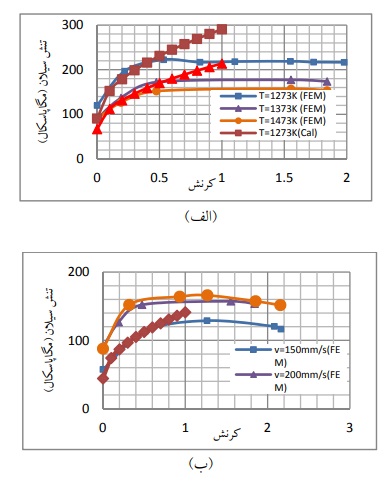
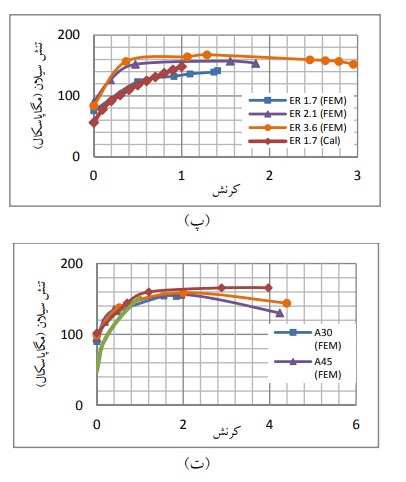
شکل 18 منحنی های تنش سیلان-کرنش پلاستیک حاصل از مدل اجزای محدود و رابطه تحلیلی در (الف). دماهای اولیه شمش مختلف، (ب) سرعت اکستروژن های مختلف، (ج) نسبت اکستروژن های مختلف، (د) زاویه قالب های مختلف
همانطور که در شکل (19 الف و ب) مشاهده می شود. با کاهش دمای اولیه شمش، یا افزایش سرعت اکستروژن و یا افزایش نسبت اکستروژن. میزان افزایش در دمای شمش در حین عملیات اکستروژن بیشتر می شود. روند تغییرات دما وابسته به دمای اولیه شمش و سرعت اکستروژن، در کار یانگ و همکارانش [26] که روی آلیاژ مقاوم به خوردگی 825 آلیاژی انجام شده نیز مشابه آن چیزی است که از این کار بدست آمده است.
روند مورد بحث، در دو حالت مورد محاسبه و نتایج حاصل از مدل اجزای محدود به وضوح مشخص است. علت این موضوع به رابطه تنش سیلان ماده با دما و رابطه دما با کار تغییر شکل بر می گردد. در واقع با کاهش دمای اولیه شمش، تنش سیلان ماده افزایش می یابد و با افزایش تنش سیلان ماده. مقاومت آن در برابر کار تغییر شکل بیشتر می شود. و لذا میزان کار انجامی برای انجام تغییر شکل مورد نظر بیشتر می شود. همچنین افزایش سرعت فرایند باعث افزایش کار مورد نیاز برای تغییر شکل میشود. لذا از آنجایی که کاهش دمای اولیه و افزایش سرعت اکستروژن، باعث افزایش کار مورد نیاز تغییر شکل می شود. با توجه به تبدیل 98% کار تغییر شکل به حرارت، افزایش دمای بیشتری اتفاق می افتد.
همانطور که در شکل (19) مشاهده می شود. حداکثر اختلاف بین نتایج حاصل از مدل اجزای محدود و نتایج حاصل از رابطه (13) حدود 15% است. که از دلایل آن می توان به صرف نظر کردن از محاسبه حرارت تولیدی در اثر اصطکاک بین قالب و شمش. به علت کم بودن مقدار آن دانست.
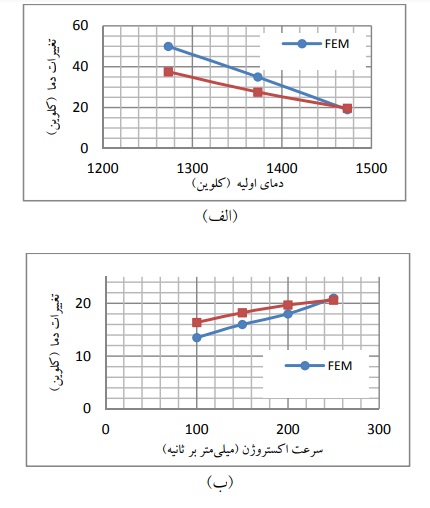
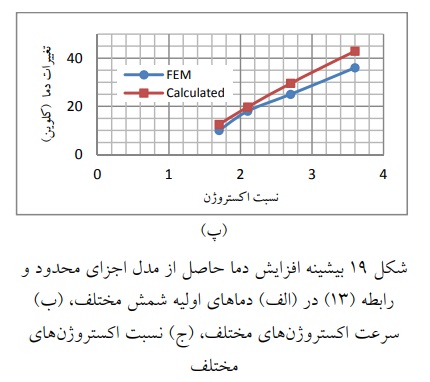
شبیه سازی اکستروژن
نتیجه گیری
-دمای اولیه شمشال بیشترین اثر را در روی نیروی اکستروژن داد. به طوری که با افزایش دمای اولیه از 1273 به 1473 کلوین، نیروی اکستروژن نصف می شود. و از حدود 20 مگانیوتن به حدود 10 مگانیوتن رسید. به عبارتی دیگر با افزایش 17% دمای اولیه، نیرو حدود 50% کاهش یافت.
-سرعت اکستروژن، اثر ناچیزی روی نیروی اکستروژن دارد. به طوری که با افزایش سرعت اکستروژن از 100 به 200 میلی متر برثانیه، حدود یک مگانیوتن به نیروی اکستروژن اضافه می شود. به عبارتی دیگر با دو برابر شدن سرعت اکستروژن، حدود 8% افزایش در نیروی اکستروژن ایجاد شد.
-نسبت اکستروژن نیز مانند دمای اولیه شمش، اثر قابل توجهی روی نیروی اکستروژن دارد. که بیشترین علت آن تغییر سیلان ماده با تغییر نسبت اکستروژن و در واقع با افزایش نسبت اکستروژن، جریان دچار آشفتگی بیشتر می شود. که موجب افزایش نیروی مورد نیاز برای جریان یافتگی ماده از دهانه قالب می شود.
شبیه سازی اکستروژن
-زاویه قالب تأثیر چندانی روی نیروی اکستروژن ندارد. و به بیانی دیگر نسبت به سایر متغیرها تأثیر آن ناچیز است. به طوری که با افزایش زاویه قالب از 30 درجه به 60 درجه حدود سه مگانیوتن به نیروی اکستروژن افزوده می شود. با این حال نوع قالب اثر قابل قبولی روی نیروی اکستروژن دارد. به طوری که انجام فرایند با قالب مخروطی زاویه 30 درجه، حدود نیمی از نیروی مورد نیاز فرایند با قالب مسطح را نیاز دارد.
-پارامترهای بهینه مورد حاصل برای انجام فرایند اکستروژن لوله فولاد زنگ نزن 304. استفاده از دما اولیه شمشال حدود 1473 کلوین، سرعت اکستروژن بین 150 تا 250 میلی متر بر ثانیه. نسبت اکستروژن کمتر از 2/7 و ترجیحاً 2/1 و کمتر از آن. و زاویه قالب کمتر از 45 درجه و ترجیحاً 30 درجه و پایین تر. برای عدم شکل گیری منطقه مرده و یا کاهش محدوده این منطقه، می باشد. که شرایط انجام فرایند با کمترین نیروی اکستروژن را فراهم می کند.
محمد رضا بهمنی – خسرو فرمنش-غلامحسین برهانی
فولاد رسول دلاکان
با سالها تجربۀ ارزشمند و گرانبها در عرصه تأمین و توزیع انواع ورق آلیاژی و انواع فولاد آلیاژی. و با گواهینامه ها و آنالیزهای معتبری که ضمیمه محصولاتش به مشتریان خویش میها می کند. توانسته رضایتمندی مشتریان خویش را همواره فراهم آورد.
صنعتگر شریف و گرامی از اینکه ما را جهت خرید کالا (فولاد آلیاژی) مورد نیاز خویش. انتخاب می نمایید از شما سپاسگزاریم.
ارتباط با ما
02128423820 – 09122136675
واتس آپ: 09122136675 – فکس: 02128423820
اینستاگرام: fooladdalakan
ایمیل : fooladrasuldalakan@gmail.com