خوردگی و اهمیت آن-فولاد ضد خوردگی-فولاد ضدسایش-فولاد آلیاژی-ورق آلیاژی
خوردگی و اهمیت آن
خوردگی و اهمیت آن
1-تعریف خوردگی
خوردگی آسیب وارد شده به فلز در اثر واکنش با محیط است. هر فلزی تحت یک مکانیسم خاص خورده میشود. که تا حدی متفاوت از مواد دیگر است. خوردگی فرآیندی طبیعی برای فلزات است. که باعث واکنش آنها با محیط اطرافشان میشود تا ترکیبات پایدارتری تشکیل دهند [1]. نسبت به ویژگیهای محیط، فرآیند خوردگی به دو دستهی خوردگی شیمیایی و الکتروشیمیایی تقسیم میشود.
فرآیند خوردگی شیمیایی فرآیندی است که طی آن فلز با غیر الکترولیت (یک مایع یا گاز) واکنش میدهد. به عنوان مثال اکسیداسیون در هوا با دمای بالا. خوردگی اغلب فلزات در دمای اتاق و در محیطهای آبی صورت میگیرد. و ماهیت الکتروشیمیایی دارد. فرآیند خوردگی الکتروشیمیایی فرآیندی است که در آن فلز در الکترولیت اکسیدی و تشکیل کاتیونهای فلزی میدهد (معادله 1-1). این الکترونها توسط واکنش احیا مثل احیای آب یا اکسیژن مصرف میشوند (معادلات 1-2 و 1-3). هر دو واکنش الکتروشیمیایی اکسیداسیون و احیا برای رخ دهی خوردگی ضروری است [2].
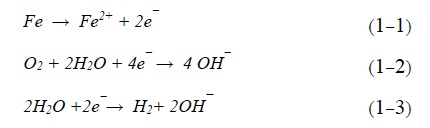
1-1-2-اهمیت مطالعه خوردگی و روشهای مقابله با آن
از آنجایی که فلزات مصرف وسیعی در جهان امروزی دارند. خوردگی تبدیل به پدیدهای شده که اطراف ما را احاطه کرده است. وسایل خانه، اتومبیل، تجهیزات صنعتی و لولههای نفت و گاز مورد حمله خوردگی قرار میگیرند. و این پدیده ضررهای مالی فراوانی را موجب میشود. امروزه خوردگی به عنوان رکن اساسی در کلیه زمینههای مهندسی درآمده است و روز به روز بر اهمیت آن افزوده میشود.
نتایع تعدادی از ارزیابیهای مورد انجام در کشورهای پیشرفته نمایان و مشخص است. که زیانهای مالی ناشی از پدیده خوردگی حدود 4-3 درصد تولید ناخالص ملی (GNP) را شامل میشود. البته با به کارگیری روشهای کنترل یا پیشگیری و بهرهگیری از تکنولوژیهای موجود، در حدود 20 درصد از این خسارات را میتوان کاهش داد. مهمترین و معمولترین روشهای کنترل خوردگی عبارتند از. انتخاب مواد و طراحی مناسب دستگاهها، حفاظت کاتدی، حفاظت آندی، استفاده از باز دارندهها و استفاده از پوششها [1و3].
1-1-2-1- انتخاب مواد و طراحی مناسب دستگاهها
هر فلزی خواص مکانیکی، شیمیایی و فیزیکی خاص خود را دارد. و میزان سرعت و رفتار خوردگی آن در محیطها و شرایط معین با دیگری متفاوت است. در نتیجه در انتخاب مواد بایستی خواص و مشخصات آن و عملکرد آن در برابر عوامل محیطی مدنظر قرار گیرد. به عنوان مثال فولاد زنگ نزن در اغلب محیطهای خورنده مقاومت بالایی دارد. در صورتی که مقاومت آن در محیط حاوی کلرید کمتر از فولاد معمولی است. از دیگر فاکتورهای مهم در انتخاب مواد، قیمت مناسب و قابلیت دسترسی آن است. بعد از انتخاب مناسب مواد، طراحی مناسب تجهیزات هم میتواند باعث کاهش خوردگی شود [4 و 5].
1-1-2-2-حفاظت کاتدی
حفاظت کاتدی همهی نواحی آندی روی سطح فلز را به کاتد تبدیل کرده و مانع خوردگی آن میشود. در این تکنیک با دادن الکترون به فلزی که بایستی محافظت شود. انحلال آن تقلیل مییابد و تصعید هیدروژن (به دلیل احیاء یون هیدروژن و یا احیاء اکسیژن در حضور آب) انجام میشود. به عبارت دیگر در حفاظت کاتدی فلز محافظت شونده نقش کاتد را داشته. و آند میتواند فلز خورنده، فلز قربانی شوند یا هر الکترود به اثر با اعمال جریان DC باشد [5].
1-1-2-3- حفاظت آندی
بر عکس حفاظت کاتدی، حفاظت آندی نسبتاً جدید است. حفاظت آندی براساس تشکیل یک لایه سطحی محافظ روی فلزات با اعمال جریانهای آندی میباشد. با اعمال جریانهای آندی به یک فلز نرمال، قاعدتاً سرعت انحلال فلز بایستی افزایش و سرعت واکنش احیاء کاهش یابد. ولی در مورد فلزات رویین شوند مثل آهن،کروم و تیتانیوم مورد استفاده، اعمال جریان آندی مناسب باعث تشکیل لایه محافظ اکسیدی و رویینگی فلز میگردد. به نحوی که غیر فعال شده و سرعت انحلال آن کاهش مییابد [5].
1-1-2-4-بازدارندهها
بازدارندهها مواد شیمیایی هستند که با افزودن آنها به میزان خیلی کم در محیطهای خورنده، خوردگی به میزان قابل ملاحظهای کاهش مییابد. در واقع بازدارندهها را میتوان یک کاتالیزور منفی فرض کرد. تأثیر بازدارندهها به علت کند کردن واکنش آندی یا کاتدی یا هر دو میباشد. در استفاده از بازدارندهها بایستی به غلظت و نوع بازدارندهی مورد استفاده در محیط خورنده توجه کرد [5].
1-1-2-4-بازدارندهها
بازدارندهها مواد شیمیایی هستند که با افزودن آنها به میزان خیلی کم در محیطهای خورنده، خوردگی به میزان قابل ملاحظهای کاهش مییابد. در واقع بازدارندهها را میتوان یک کاتالیزور منفی فرض کرد. تأثیر بازدارندهها به علت کند کردن واکنش آندی یا کاتدی یا هر دو میباشد. در استفاده از بازدارندهها بایستی به غلظت و نوع بازدارنده مورد استفاده در محیط خورنده توجه کرد [5].
خوردگی و اهمیت آن
1-1-2-5- پوششها
پوششدهی به فلزات عنوانی است مشتمل بر تعدادی فرآیند. که با هدف بهبود خواص سطح یک فلز نظیر ترسیب یک لایه از یک فلز، یک لایه پلیمر یا یک لایه اکسید صورت میگیرد. قسمت اعظم اشیای فلزی که در زندگی روزمره با آنها تماس داریم. به عنوان مثال اکثر قطعات سازنده، وسایل نقلیه موتوری، وسایل آشپزخانه، قوطیهای کنسرو. پنجرههای فلزی، قطعات وسایل الکترونی نظیر مدارهای چاپی، خازنها و غیره. یک نوع فرآیند پوششدهی ار متحمل شدهاند.
به عبارت دیگر شاید کمترین فعالیت صنعتی را بتوان یافت که به یک فرآیند پوششدهی نیاز نداشته باشد. پوششهای محافظتی با ایزوله کردن فلز بستر مانع تماس آن با محیط خورنده شده. و از آن محافظت میکنند [7,6] عملکرد حفاظتی پوششها به چهار روش کلی صورت میگیرد:
1-پوششهای سدی که مانع تماس فلز و محیط خورنده میشوند. این پوششها با مقاومت بالای خود باعث کاهش انتقال جریان بین نواحی آندی و کاتدی میشوند. یا با از بین بری نفوذ اکسیژن و ممانعت از انجام واکنش کاتدی از فلز بستر محافظت میکنند [4].
2-پوششهای فداشونده که خورده شده و از فلز بستر به صورت کاتدی محافظت میکنند، مانند رنگدانههای غنی از روی.
3-پوششهای بازدارنده که واکنش الکترود را کند میکنند.
4-پوششهای مقاومتی الکتریکی که مانع تشکیل پیل خوردگی الکتروشیمیایی میشوند، مانند رنگها [1].
پوششها از دیدگاه جنس به سه دسته پوششهای آلی، معدنی و فلزی تقسیم میشوند.
الف) پوششهای آلی
پوششهای آلی مشتمل بر مانع نسبتاً نازکی بین فلز و محیط آن میباشند. کارآمدی این پوششها به خواص مرتبط با شبکه پلیمری آنها و نواقص احتمالی در این شبکه. ویژگیهای فلز بستر، آمادهسازی سطح و روشهای مورد استفاده برای اعمال پوشش بستگی دارد. پوششهای آلی به سه دستهی لاکها1،جلاها2 و رنگها3 تقسیم میشوند [6].
ب) پوششهای معدنی
پوششهای معدنی یا پوششهای تبدیلی شیمیایی دستهای از پوششها میباشند. که از طریق تبدیل شیمیایی سطح مورد نظر در محلولهای الکترولیت مناسب و اغلب بدون استفاده از جریان برق اعمال میشوند. ترکیب شیمیایی پوششهای تبدیلی، ترکیبی از یونهای موجود در حمام آبکاری و ترکیبات مربوط به خود فلز بستر میباشد. این پوششها جهت بالا بری مقاومت خوردگی، ارتقاء چسبندگی پوششهای متعاقب و همچنین در برخی موارد برای بالا بردن درجه سختی سطح اعمال میشوند.
پوششهای تبدیلی معمول شامل پوششهای فسفاته، کروماته، اکسید و آندایزینگ هستند [6 و 7].
ج) پوششهای فلزی
فرآیند پوششدهی به فلز بستر با لایهای از فلز محافظ، پوشش فلزی نامیده میشود. پوششهای فلزی نه تنها از سطح فلز در مقابل خوردگی محافظت میکنند. بلکه از جنبههای دیگر از جمله افزایش سختی و جنبه تزئینی هم اهمیت زیادی دارند. علاوه بر آن این پوششها خواص فیزیکی و مکانیکی فلز از جمله خواص عایقسازی گرمایی. خواص الکتریکی، مقاومت فرسایشی و غیره را هم تحت تأثیر قرار میدهند. پوششهای فلزی به دو دسته پوششهای فلزی آندی و کاتدی تقسیم میشوند.
-پوشش فلزی آندی
پوشش فلزی که نسبت به فلز بستر آندی باشد، آنرا پوشش فلزی آندی مینامند. در این روش به منظور حفاظت از فلز در مقابل خوردگی، فلزی که در سری گالوانیک بالاتر است. مثل منیزیم، روی و غیره بر روی سطح فلز بستر اعمال میشود. این فلزات فعال نسبت به فلز بستر آندی هستند. پوشش روی بر روی سطح فولاد نرم مثالی از این نوع پوشش است. در این مثال فلز روی آند و آهن به عنوان کاتد عمل میکنند. در صورت تماس با محیط خورنده، آند (روی) خورده میشود و از فلز بستر (آهن) محافظت میکند. مزیت این روش این است که تا زمانی که فلز فعال (آند) به طور کامل خورده شود از فلز بستر محافظت میکند.
-پوشش فلزی کاتدی
در این نوع پوشش، سطح فلز بستر با فلزی پوشش دهی میشود که تمایل به خوردگی آن کمتر است. پوشش کاتدی به دلیل مقاومت بالایی که نسبت به فلز بستر دارد، از آن محافظت میکند. یک پوشش نازک از فلزاتی مثل قلع، مس و نیکل روی آهن مثالی از این روش است. درصورتی که پوشش کاتدی بدون نقص و پیوسته باشد، میتواند به خوبی از فلز بستر محافظت کند. در صورت وجود نقص در پوشش، آسیب خوردگی وارده بر فلز بستر که نقش آند را دارد به دلیل اثرات گالوانیک تشدید مییابد [9].
خوردگی و اهمیت آن
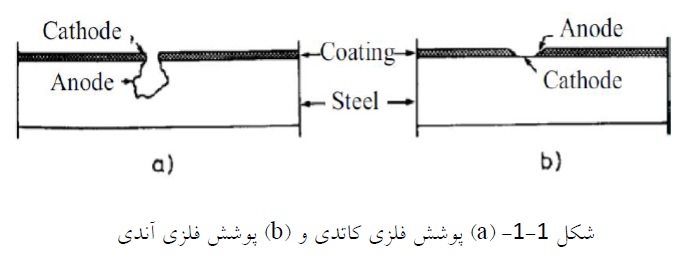
به منظور اعمال یک پوشش فلزی تکنیکهای زیر مورد استفاده قرار میگیرند.
-غوطهوری گرم1
این روش با فرو بری فلزات در داخل حمام مذاب فلزاتی. مثل روی، قلع، سرب و آلومینیوم که بایستی پوشش داده شوند، انجام میشود. این فرآیند سادهترین روش اعمال پوشش حفاظتی به فلز بستر میباشد. ولی محدودیتهایی دارد مثلاً نقطه ذوب فلز پوشش بایستی پایینتر از فلز بستر باشد [3و5].
-پاشش گرمایی2
این فرآیند که متالیزه کردن نیز نامیده میشود. عبارت است از هدایت سیم فلزی یا پودر فلزی از طریق یک مشعل که باعث ذوب آن میشود. و به صورت ذرات ریز مذاب به سطح فلزی که بایستی پوشش دهی شود، پاشش میشود [5].
-نورد کردن3
در این روش ورقه نازکی از فلز روکش با نورد گرم یا سرد، فشار گرمایی یا اتصال فشاری به فلز بستر متصل میشود. فلز روکش معمولاً نازکتر از فلز زمینه است. از جمله میتوان به آلیاژ Al/Al ،Ni/Cu ، Au/Cu ، Sn/Ni ، Ag/Cu ، Sn/Cu و Au/Ni اشاره کرد [1و5].
-ترسیب بخار و خلأ4
این کار در یک محفظه یا خلأ نسبتاً بالا انجام میشود. فلز پوشش به وسیله جریان الکتریکی حرارت دهی میشود. و بخار حاصل از آن روی سطح قطعهای که بایستی پوشش دهی شود، مینشیند. این روش اغلب برای تشکیل پوشش فلزی روی قطعه غیر هادی مورد استفاده قرار میگیرد. اغلب پوششهای ترسیبی با این روش شامل پوشش آلومینیوم روی پلاستیک و پوشش رودیم روی آینه است.
-روش نفوذی1
این روش شامل عملیات حرارتی برای به وجود آوری آلیاژ روی سطح در اثر نفوذ یک فلز به داخل فلز دیگر میباشد. این روش به آلیاژسازی سطحی نیز معروف است. قطعاتی که بایستی پوشش دهی شوند در مواد جامد یا محیط گازی مناسب قرار میگیرند. گالوانیزه خشک (پوشش روی روی آهن در اثر نفوذ) فولادی که کرومایز میگردد (فولاد با پوشش کروم) مثالهایی از این مورد میباشند [1و5].
خوردگی و اهمیت آن
-آبکاری الکتریکی2
آبکاری الکتریکی یا آبکاری با برق فرآیندی است که در آن یونهای فلزی از محلول توسط جریان برق به سمت قطعه مورد آبکاری حرکت میکنند. در این فرآیند از جریان برق برای احیای کاتیونهای فلزی از محلول استفاده میگردد. و فلز بستر با لایه نازکی از فلز نجیبتر پوشش دهی میشود. اجزای اصلی یک فرآیند آبکاری الکتریکی به طور شماتیک در شکل (2-1) نمایان و مشخص است که در زیر به معرفی آنها میپردازیم.
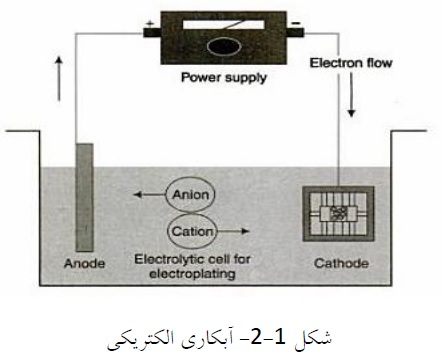
-الکترولیت
الکترولیت شامل یک هدایت کننده و نیز نمک فلزی میباشد که باید به صورت رسوب در سطح شیء مورد نظر کاهش کاتدی یابد. نمک انتخابی از فلز بایستی قابلیت انحلال کافی داشته باشد.
-کاتد
کاتد شیئی است که ترسیب الکترولیتی در سطح آن مورد میپذیرد. این الکترود منفی بوده و بایستی هدایت الکترونی دارا باشد.
خوردگی و اهمیت آن
-آند
آند از فلزی متشکل است که بایستی روی سطح قطعه مورد نظر ترسیب شود. که آند الکترود مثبتی بوده و میتواند تأثیر پذیر یا تأثیر ناپذیر باشد. در صورت استفاده از آند تأثیر ناپذیر، بایستی یونهای فلزی مصرفی به صورت نمک جامد انتخاب شود. انتخاب آند بیاثر بستگی کامل به نوع فرآیند دارد. استفاده از آند پوشیده شده از آندهای بیاثر، در محیطهای اسیدی و استفاده از فولاد زنگ نزن در محیطهای قلیایی رایج است.
-منبع جریان
منبعی است که جریان مستقیم را از آند به کاتد عبور میدهد. این منبع الکترونهای مورد نیاز برای احیای فلز را فراهم میکند.
فاکتورهای تأثیرگذار بر آبکاری با برق
کیفیت رسوبات فلزی مورد حاصل به روش آبکاری با برق به عوامل زیادی بستگی دارد. از جمله ترکیب محلول الکترولیت، PH، دما، شکل هندسی آند و کاتد، شرایط انتقال مواد (بهم خوردگی محلول) و دانسیته جریان است.
برای افزایش هدایت الکترولیت، از الکترولیتهای حامل (که بر روی قطعه راسب نمیشوند) استفاده میشود. هر قدر هدایت الکتریکی محلول بیشتر باشد، میزان افت اهمی کمتر دو در نتیجه اختلاف پتانسیل در مورد کاتدهایی که سطح پیچیدهای دارند، کمتر میشود. بدین ترتیب ترسیب یکنواخت و سرعت آن در کلیه نقاط سطح یکسان میباشد. این الکترولیتها ممکن است دارای نقش کنترل کننده PH باشند. تا از آزاد شدن هیدروژن یا اکسیژن، به ترتیب در کاتد و آند، به علت تغییر PH حمام در اثر الکترولیز جلوگیری کنند.
دانسیته جریان هم عامل هم تأثیرگذار است. در دانسیته جریان پایین نفوذ محلول و انتقال الکترون آهسته است. اتمها فرصت کافی برای حرکت به سمت محلهای مناسب جهت هستهزایی دارند و این منجر به تشکیل پوششی خوب میشود. در دانسیته جریان بالا انتقال الکترون غالب بوده و نفوذ محلول آهسته میباشد. در نتیجه تعداد هستههای متشکل افزایش مییابد و احتمال اینکه اتمها به سمت محلهای مناسب حرکت کنند کمتر است.
این منجر به تشکیل پوششهای نامنظم میشود. نفوذ سطح کم بوده و این منجر به تشکیل پوشش غیر چسبنده، زبر و پودری میشود. در دانسیته جریان بالاتر از مقدار حدی، آزاد شدن گاز هیدروژن منجر به کاهش غلظت یونهای آزاد *H در اطراف کاتد میشود. بنابراین هیدروکسیدها یا اکسیدهای فلزی راسب شده و پوشش کدر و اسفنجی به دست میآید [7].
آبکاری با برق فلزاتی مانند روی، مس، نیکل، کروم، طلا و نقره معمول است. آلومینیوم، تیتانیوم، سدیم، منیزیم و کلسیم فلزاتی هستند که نمیتوانند از محیط آبی با روش آبکاری با برق ترسیب شوند. به دلیل اینکه واکنش کاتدی رقابتی

به لحاظ ترمودینامیکی مطلوبتر بوده و پیشتر از احیای یون فلزی صورت میگیرد. برای ترسیب الکترولیتی این فلزات بایستی از محلولهای آلی هادی یا محلول نمک مذاب که غلظت یون *H در آنها قابل صرفنظر کردن است. استفاده نمود [6]. پیش از انجام آبکاری، به منظور بدست آوردن پوششهایی با کیفیت مطلوب. بایستی سطح مورد نظر با استفاده از حلالهای آلی یا آبی قلیایی تمیز شود. این عمل میتواند با اعمال جریان یا بدون اعمال جریان انجام شود. به عنوان مثال، به معرفی محتویات حمام آبکاری نیکل معروف به حمام واتس1 میپردازیم.
خوردگی و اهمیت آن
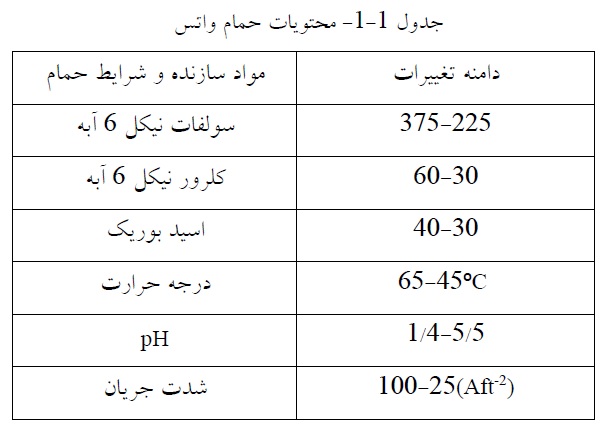
سولفات نیکل منبع اصلی یونهای نیکل در حمام واتس بوده و غلظت آن حدود شدت جریان را در تهیه رسوبات نیکل مناسب تعیین میکند. معمولاً با افزایش غظت، میزان جریان بالاتری اعمال شده و آبکاری سریعتر انجام میشود. اسید بوریک در بدست آوردن رسوباتی سفیدتر، صافتر و نرمتر مؤثر است. آب اکسیژنه هم در بعضی موارد به حمام اضافه میشود. آب اکسیژنه در جلوگیری از تخلخل رسوبات در حمام واتس بسیار مفید است اما غلظت آن باید تحت کنترل باشد. در صورتی که غلظت آب اکسیژنه در حمام زیاد باشد به اختصاصات رسوبات نیکل صدمه میزند.
انتخاب PH پایینتر عبور جریان شدیدتری از محلول را امکانپذیر کرده و هدایت حمام افزایش مییابد در نتیجه قدرت روکش بهتر میشود.
درجه حرارت را تا حد امکان بالا انتخاب میکنند زیرا که درجه حرارت بیشتر، این امکان را میدهد. در ازای مصرف ولتاژ کمتر، شدت جریان بیشتری از محلول عبور کند. از سوی دیگر سختی رسوبات کمتر و قابلیت خم شدن آنها بیشتر میشود. به هم زدن محلول هم باید در حد مطلوب باشد. زیرا که مقدار حد مجاز جریان را در تهیه رسوبات مناسب افزایش میدهد و درجه حرارت محلول را در کل محلول یکسان نگه میدارد [7].
خوردگی و اهمیت آن
-آبکاری شیمیایی
این نوع آبکاری ترتیب شیمیایی فلز از محلول آبی نمک آن، بر روی سطح مورد نظر میباشد. که ماهیت الکتروشیمیایی داشته و واکنشهای اکسیداسیون و احیاء شامل انتقال الکترون بین گونههای در حال واکنش میباشد. در آبکاری شیمیایی از جریان برق استفاده نمیشود. این فرآیند به دو دسته کلی تقسیم میشود که به شرح آنهای میپردازیم.
الف) ترسیب جایگزینی
ترسیب جایگزینی فرآیند گالوانیک هتروژنی است که در آن یک واکنش جانشینی بین فلز M1 (فلز پستتر). و فلز دیگر M1 (فلز نجیبتر) صورت میگیرد که منجر به ترسیب فلز M در سطح فلز M1 میشود.

به عنوان مثال در صورتیکه فلز روی در محلول سولفات مس غوطهور شود. اتمهای فلز روی که فلز پستتر است به صورت خود به خودی با اتمهای مس از محلول جایگزین میشوند.
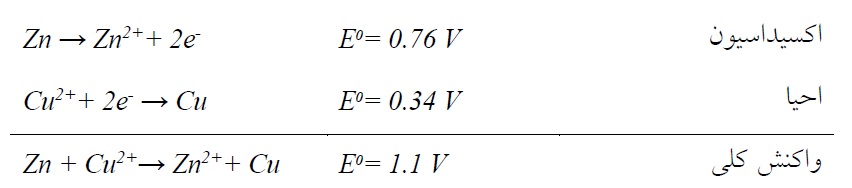
این فرآیند، آبکاری غوطهوری نیز مینامند. این نوع آبکاری به محض پوشیدگی سطح فلز غوطهور میشود.(فلز منفیتر) با فلز احیاء شده (فلز مثبتتر)، متوقف میشود. به عبارت دیگر، سرعت واکنش به تدریج کاهش مییابد چون سطح فلز مورد نظر به دلیل پوشش با فلز M. به تدریج از دسترس محلول حاوی یونهای +Mn دور میشود. ضخامت پوششهای مورد حاصل، از این روش بسیار کم و در حدود 1 تا 3 میکرومتر میباشد. به همین دلیل این نوع آبکاری کاربرد بسیار محدودی دارد. علاوه بر آن، رسوبات حاصل از این روش معمولاً متخلخل بوده و چسبندگی ضعیفی دارند.
ب) آبکاری الکترولس یا خودکاتالیزوری
امروزه آبکاری الکترولس اهمیت قابل توجهی را در تکنولوژی مدرن به ویژه در ساخت مواد جدید برای کاربرد در صنایع الکترونیک. مواد مقاوم در برابر خوردگی و فرسایش، وسایل پزشکی، تکنولوژی باتریها و غیره دارد. آبکاری خود کاتالیزوری مشهور به آبکاری الکترولس، رایجترین روش شیمیایی است. که برای ترسیب لایه فلزی از محلول آبی و بدون اعمال جریان الکتریکی خارجی مورد استفاده قرار میگیرد. الکترونهای مورد نیاز برای احیای گونههای فلزی توسط اکسیداسیون عامل احیاء کننده فراهم میشود. واکنش کلی آبکاری بدون برق به صورت زیر میباشد.
خوردگی و اهمیت آن

OX محصول اکسیداسیون عامل احیاء کننده است. سطح کاتالیزوری ممکن است خود فلز بستر یا هستههای کاتالیزوری از فلز ′M توزیع شده روی سطح فلز بستر غیر کاتالیزوری باشد. در این نوع آبکاری گونه احیاکننده الکترونهای خود را به سطح کاتالیزوری و یونهای فلز +Mz در سطح میدهد. پتانسیل تعادلی عامل احیاکننده (Eeq,Red) بایستی منفیتر از پتانسیل تعادلی فلز (Eeq,M) باشد تا بتواند الکترونهای مورد نیاز برای فلز را فراهم کند.
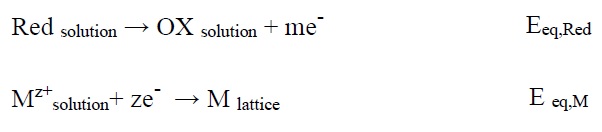
توسعه آبکاری الکترولس عمدتاً مربوط به ترسیب مس و نیکل میباشد. ولی فلزات دیگری همچون طلا، نقره و کبالت وجود دارند که به دلیل اهمیت کاربردی که دارند، به این روش ترسیب میشوند. اولین مطالعه علمی در زمینه فرآیند الکترولس توسط ون لیبیگ1 در سال 1835 به احیای نمک Ag(I) به فلز Ag. با استفاده از آلدهیدها مربوط میشود. بعدها در سال 1844 ورتز2 مشاهده کرد که یونهای +Ni2 توسط یونهای هیپوفسفیت احیا میشوند. با وجود تحقیقات بعدی که در سالهای 1911 تا 1931 به عمل آمد. تنها از سال 1946 به بعد بود که برنر و ریدل3 توانستند شرایط مناسبی برای ترسیب الکترولس Ni. از محلول آبی محتوی نیکل و هیپوفسفیت معرفی کنند [11-13].
- مزایای آبکاری بدون برق
آبکاری بدون برق نسبت به آبکاری با برق دارای مزایایی میباشد که از جمله آن میتوان به موارد زیر اشاره نمود.
-در این روش نیازی به استفاده از منبع جریان نمیباشد لذا در این روش مشکلات ناشی از توزیع غیریکنواخت جریان. بر روی سطح قطعه که منجر به آبکاری غیر یکنواخت میشود، وجود ندارد.
-ضخامت پوشش در قطعات آبکاری شده به روش بدون برق، بدون توجه به شکل هندسی آن. یکنواخت میباشد؛ در حالیکه در آبکاری با برق ضخامت در نقاط فرورفته نازکتر و در نقاط برجسته ضخیمتر است.
-تخلخل پوششهای الکترولس کمتر میباشد و در نتیجه میتواند محافظت خوردگی خوبی را برای فلز بستر فراهم کند.
خوردگی و اهمیت آن
-پوششهای الکترولس متراکمتر و سختتر بوده و چسبندگی خوبی دارند.
-آبکاری الکترولس بر روی اجسام نیمه هادی و غیر هادی مانند شیشه، سرامیک و پلیمر انجامپذیر است [9].
- معایب آبکاری بدون برق
از معایب این روش میتوان به آزاد شدن گاز هیدروژن در حین فرآیند آبکاری اشاره نمود. که منجر به تشکیل حفراتی در پوشش و در نتیجه کاهش مقاومت خوردگی آن میشود. عیب دیگر آن کوتاه بودن عمر حمام آبکاری است که از جنبه اقتصادی و زیست محیطی مسئلهای جدی میباشد [10].
- دامنههای کاربرد انواع آبکاریها
پوششدهی به فلزات به منظر یک یا چند هدف از نقطه نظر تغییر خواص سطح فلز صورت میگیرد. از مهمترین کاربردهای آبکاری بدون برق میتوان به حفاظت در برابر خوردگی، ترمیم یا ساخت مواد. هدفهای تزئینی، مقاومت در برابر سایش، افزایش سختی، انعکاس بهتر نور یا بازگشت گرما. افزایش هدایت الکتریکی، ایجاد قابلیت لحیمپذیری و افزایش قابلیت هدایت حرارتی شاره نمود [7].
- ماهیت الکترولیت در حمام آبکاری
حمام الکترولس عمدتاً شامل نمک تأمین کننده یون فلزی، عامل احیاء کننده، مواد کمپلکس کننده و افزودنیهای مختلف میباشد که در ادامه شرح دهی میشوند.
خوردگی و اهمیت آن
-منبع یون فلزی
منبع یون فلزی میتواند هر نمک قابل انحلال در آب مانند سولفاتها، کلریدها، استاتها، سیانیدها و غیره باشد. ماهیت منبع یون فلزی اغلب با پایداری محلول، خواص پوشش حاصل میگردد و شرایط محیطی تعیین میشود [11].
-عامل کمپلکس کننده
مهمترین عاملهای کمپلکس کننده که در آبکاری بدون برق استفاده میشود. اغلب اسیدهای آلی یا نمکهای آنها مانند اسید استیک، اسید سیتریک، اتیلن دی آمین، دی اتیل تری آمین و غیره میباشند. در بعضی موارد یونهای معدنی مثل

هم به عنوان کمپلکس کننده استفاده میشود.
انتخاب عامل کمپلکس کننده به ماهیت یونهای فلزی مورد استفاده جهت آبکاری بستگی دارد. عامل کمپلکس کننده با اهداف جلوگیری از ترسیب هیدروکسیدها و نمکها، به عنوان بافر برای ثابت ماندن PH. و برای کاهش غلظت یونهای فلزی آزاد در محلول مورد استفاده قرار میگیرد. علاوه بر آن، عامل کمپلکس کننده بر سرعت کاهش و خواص رسوبات فلزی تأثیر میگذارد.
خوردگی و اهمیت آن
-عامل احیاکننده
انتخاب عامل احیاکننده به شرایط آبکاری بدون برق و خواص فیزیکی و شیمیایی فلز مورد آبکاری بستگی دارد. چهار عامل احیاکننده که معمولاً در آبکاری بدون برق مورد استفاده قرار میگیرند. سدیم هیپوفسفیت (NaH2PO2.H2O)، سدیم بوروهیدرید (HaBH4)، دی متیل آمین بوران
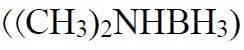
و هیدرازین (H2H4.H2O) میباشند. ممکن است اجزای مربوط به عامل احیاکننده نیز در ساختار پوشش ایجاد شده ظاهر میگردد. مثلاً فسفر در حین استفاده از هیپوفسفیت سدیم در آبکاری نیکل [13].
-مواد افزودنی آلی
تعداد بسیاری از مولکولهای آلی با غلظت اندک را به حمام آبکاری اضافه مینمایند. تا ساختار، شکل و خواص فلزات به دست آمده در سطح مورد نظر بهبود یابد. این افزودنیها به چند دسته تقسیم میشوند.
- براق کنندهها: موادی هستند که به تشکیل پوششهای براق و منعکس کننده نور کمک میکنند. هرچه اندازه ذرات پوشش کوچکتر و میزان زبری سطح کمتر باشد، انعکاس نور توسط پوشش بهتر میشود. بنابراین براق کنندهها برای ایجاد پوششهایی با دانههای ریز به کارگیری میشوند. سولفونها، سولفاتهای آروماتیک، مولکولهای حاوی گروههای عاملی
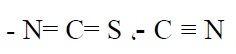
کربونیل، تیواوره و کومارین به عنوان براق کننده استفاده میشوند.
- مسطح کنندهها: موادی هستند که باعث ایجاد رسوبات صاف و یکنواخت میشوند. این مواد در نقاطی جذب میشوند که در صورت عدم حضور، تشکیل رسوبات فلزی در نقاط مورد بیان سریعتر از نقاط دیگر صورت میپذیرد. در واقع جذب مواد مسطح کننده در نقاطی از سطح که جابهجاییهای ناخواسته صورت گرفته. راحتتر است زیرا این نقاط دارای انرژی آزاد جذب بیشتری دارند. جذب مواد مسطح کننده سرعت انتقال الکترون را کاهش میدهد. سدیم الکیل سولفونات به عنوان مسطح کننده مورد استفاده قرار میگیرد.
- مواد مرطوب کننده: این مواد رها شدن حبابهای هیدروژن از سطح مورد آبکاری را تسریع میبخشند. در صورت عدم حضور این مواد، حبابهای هیدروژنی در سطح قطعه باقی مانده و فرصت مییابند. تا در لایههای دانههای اتمی فلز پوشش باقی مانده و باعث شکنندگی پوشش میشوند. این پدیده تردی هیدروژنی نامیده میشود.
- بهبود دهندههای ساختار شبکه فلزی: همهی فرآیندهای آبکاری به دلیل قرار گرفتن غیرطبیعی شبکههای بلوری، متحمل تنش داخلی میشوند. این تنش باعث آسیب دیدگی در پوشش میشود و ایجاد ترک در آن میکند. این مواد فشار داخلی رسوبات فلزی را کاهش میدهد و باعث بهبود خواص سطح میشوند [9,7].
- پایدار کنندهها: پایدارکنندهها ترکیبات شیمیایی هستند که به منظور جلوگیری از تجزیه محلول به حمام آبکاری بدون برق اضافه میشوند. اضافه کردن این ترکیبات به حمام آبکاری تحت شرایط مناسب، باعث پایداری حمام برای مدت زمان نسبتاً طولانی میشود. تجزیه محلول در نتیجه ترسیب ذرات فلزی در توده محلول میباشد. این ذرات فلزی به دلیل مساحت سطح بالایی که دارند به عنوان کاتالیزورهایی مؤثر برای احیای بیشتر فلز عمل میکنند. انتخاب عامل پایدار کننده به فلز مورد آبکاری و سازگاری آن با فرآیند بستگی دارد. پایدارکنندههای مورد استفاده برای آبکاری الکترولس به دستههای زیر تقسیم میشوند.
خوردگی و اهمیت آن
الف) ترکیبات محتوی عناصری از جمله Te,Se,S
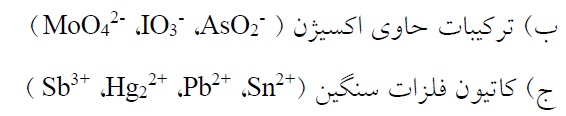
خوردگی و اهمیت آن
د) اسیدهای آلی غیر اشباع (مالئیک، ایتاکونیک و غیره) [13].
- آمادهسازی سطح
مهمترین مرحله در اعمال هر پوششی، مرحله آمادهسازی سطح است. آمادهسازی سطح شامل تمیز کردن و عملیات پیش تیماری سطح میباشد. بسته به فرآیندی که بر روی سطح انجام میشود، میزان و نوع آمادهسازی سطح متفاوت خواهد بود. به عنوان مثال: میزان تمیز بودن سطح در فرآیند فسفاتهکاری به اندازهی آبکاری حساس و مهم نیست. چون در فرآیند فسفاتهکاری واکنش شیمیایی محلول فسفاته با سطح فلز، باعث تمیز شدن سطح میشود.
همچنین فرآیند تمیزکاری سطح و محیط شستشو به اجزاء خواص فیزیکی و شیمیایی فلز بستر بستگی دارد. سختی، تخلخل، ضریب گرمایی، ضریب انبساط، هدایت، نقطه ذوب و گرمای ویژهی فلز بستر بایستی مورد توجه قرار گیرد. به عنوان مثال فرآیند تمیزکاری برای فولاد با تعداد کربن بالا و فولاد با تعداد کربن کم متفاوت است. و یا اینکه فلزات با نقطه ذوب پایین را نبایستی در محلولهای با دمای بالا تمیز کرد.
سطح قطعات فلزی معمولاً آلوده به گردوخاک، گریس، چربی و پوستههای اکسیدی است. به منظور تأمین چسبندگی مناسب بین پوشش و فلز بستر و داشتن پوششهای با کیفیت. بایستی هر گونه آلایندهای که از تماس مستقیم محلول حمام با سطح فلز جلوگیری میکند، پاک گردد. علاوه بر آن، بایستی قبل از آبکاری، شیارها، خراشها و محصولات زنگ از سطح حذف شوند. برای این منظور میتوان از سمباده استفاده کرد. بعد از عمل سمباده زنی، به روشهای مختلفی میتوان سطح قطعه را تمیز کرد از جمله:
1-تمیزکاری با حلال
2-تمیزکاری با امواج التراسوند
3-شستشوی بازی
4-اسیدشویی [15,14].
- فعالسازی سطوح غیر کاتالیزوری
سطوح غیر کاتالیزوری مثل غیر هادیها، فلزات غیر کاتالیزوری و نیمه هادیهای غیر کاتالیزوری قبل از ترسیب الکترولس بایستی فعالسازی شوند. فعالسازی با ایجاد هستههای کاتالیزوری روی سطح یک جسم غیر کاتالیزوری انجام میشود. دو فرآیند کلی برای ایجاد هستههای کاتالیزوری مورد استفاده قرار میگیرد.
-فعالسازی الکتروشیمیایی
-فعالسازی فتوشیمیایی
- فعالسازی الکتروشیمیایی
در روش الکتروشیمیایی ممکن است هستههای کاتالیزوری فلز M روی سطح غیر کاتالیزوری S در واکنش الکتروشیمیایی اکسیداسیون-احیا ایجاد شود.
Mz++ Red → M + OX
که +Mz یونهای فلزی و M کاتالیزور فلزی است. بهترین کاتالیست Pd و در نتیجه بهترین عامل هسته زایی +Pd2 (حاصل از PdCl2) است. مناسبترین عامل احیا کننده یون +Sn2 (حاصل از SnCl2) میباشد. در این مورد واکنش کلی فعالسازی به صورت زیر میباشد:

پتانسیل استاندارد
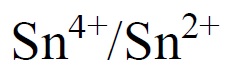
برابر 0/15V و پتانسیل استاندارد Pd2+/Pd برابر 0/987V است در نتیجه +Sn2 میتواند باعث ایجاد احیای یونهای +Pd2 شود.
فعالسازی الکتروشیمیایی با استفاده از PdCl2 و SnCl2 ممکن است به صورت یک مرحلهای یا دو مرحلهای صورت میگیرد.
مرحله اول فرآیند فعالسازی دو مرحلهای، حساسسازی نامیده میشود. یونهای +Sn2 روی سطح غیر هادی مورد نظر (S) جذب میشوند:
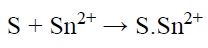
خوردگی و اهمیت آن
که +S.Sn2 نشان دهنده +Sn2+ جذب شده در سطح S میباشد. محلول حساسسازی شامل محلولی از SnCl2 و HCl است. حساسسازی ممکن است با غوطهوری نمونه در محلول یا اسپری کردن نمونه با محلول مورد نظر صورت گیرد. مرحله دوم در فرآیند دو مرحلهای هستهزایی است. رایجترین محلول هستهزایی که در صنعت مورد استفاده قرار میگیرد، حاوی PdCl2 و HCl است. هستهزایی با غوطه نمونه حساسسازی شده در محلول هستهزایی انجام میشود. واکنش بین یونهای +Sn2 جذب شده روی سطح و یونهای +Pd2 موجود در محلول هستهزا به صورت زیر میباشد:

میزان پالادیمهای جذب شده در سطح متناظر با یونهای +Sn2 اکسید شده است.
در فرآیند فعالسازی یک مرحلهای، حساسسازی و هستهزایی در یک محلول انجام میشود. فرض میشود که محلول محتوی کمپلکسهای قلع-پالادیم کلرید است. سپس این کمپلکسها به ذرات کلوئیدی Pd فلزی یا آلیاژ فلزی Sn/Pd تبدیل میشوند تا توزیع کلوئیدی صورت گیرد. این توزیع ناپایدار بوده و ممکن است با اضافه کردن یونهای +Sn4 پایدار شود. در این مورد ذرات Pd جذب شده روی سطح غیر هادی توسط یونهای قلع احاطه میشوند. به منظور قرار گرفتن یونهای پالادیم در معرض حمام آبکاری. کلوئیدها بایستی در محلول انحلال ناپذیری مانند مخلوطی از اسید فلوروبوریک و اگزالیک یا فقط NaOH یا HCI حل شوند [12].
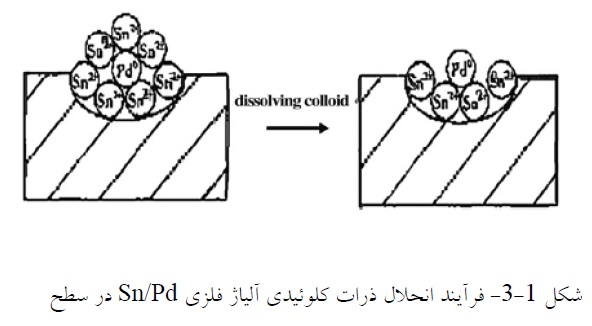
خوردگی و اهمیت آن
-فعالسازی فتوشیمیایی
در فرآیندهایی فتوشیمیایی برای تولید هستههای فلزی کاتالیزوری از دو روش با سینتیک متفاوت شامل فتوالکتروشیمیایی و فتو الکترون استفاده میشود.
سینتیک فتوالکتروشیمیایی شامل واکنشهای فتوشیمیایی همراه با یک واکنش الکتروشیمیایی میباشند. به عنوان مثال الکترونهای مورد نیاز جهت احیای +Fe3 به +Fe2 از فتولیز ردوکس زیر فراهم میشود.
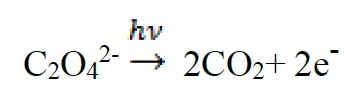
سپس یونهای +Fe2 در یک واکنش الکتروشیمیایی برای تولید هستههای کاتالیزوری پالادیم مصرف میشوند.
در روش فتوالکترون، الکترونهای مورد نیاز برای تشکیل هستههای فلزی کاتالیزوری M. از کاتیونهای فلزی +M2 حاصل از فرآیند جذب مستقیم یک فوتون توسط یک کریستال نیمه هادی ایجاد میشود. که منجر به تشکیل الکترون حفره میشود. به عنوان مثال جذب فوتون توسط TiO2 باعث ارتقای الکترون از نوار ظرفیت پر به نوار هدایت خالی میشود. نتیجه این جذب ایجاد یک الکترون آزاد در نوار هدایت و یک حفره خالی در نوار ظرفیت است.
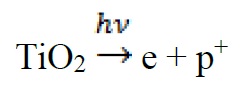
الکترونهای تولید شده در این فرآیند توسط یونهای فلزی جذب شده و باعث احیای آنها میشوند [12].
- آبکاری الکترولس نیکل
از زمان اعمال شرایط مناسب جهت انجام آبکاری الکترولس نیکل توسط برنر و ریدل در سال 1946. این فرایند کاربرد گستردهای در زمینه حفاظت از خوردگی، افزایش مقاومت فرسایشی و فلزکاری مواد غیر هادی. مثل سرامیکها، شیشه و پلاستیکها داشته است [16]. مهمترین دلیل برای استفاده گسترده صنعتی و تجاری فرآیند آبکاری الکترولس نیکل، خواص منحصر به فرد آن است. خواص فیزیکی و شیمیایی پوششهای نیکل به ترکیبات حمام و شرایط اعمال پوشش بستگی دارد.
مهمترین منبع یون نیکل، سولفات نیکل میباشد. نمکهای دیگر مثل کلرید نیکل، استات نیکل و هیپوفسفیت نیکل کاربرد کمتری دارند. این آبکاری با استفاده از عاملهای احیا کنندهای همچون بوروهیدرید، DMAB، هیدرازین و هیپوفسفیت انجام میشود. فرآیند ترسیب با استفاده از این عاملهای احیا کننده کاتالیزوری است. به عبارت دیگر، نیکل کاتالیزوری برای اکسیداسیون عامل احیا کننده است.
عامل احیا کننده بوروهیدرید شامل هر ترکیب بوروهیدرید محلول در آب میباشد. سدیم بوروهیدرید به دلیل فراوانی، بیشتر مورد استفاده قرار میگیرد. یون بوروهیدرید احیا کننده قوی بوده و پتانسیل احیای آن E=1/24V میباشد. این عامل احیا کننده به دلیل هیدرولیز در محیطهای اسیدی و خنثی، در این محیطها ناپایدار بوده و تجزیه میشود. برای جلوگیری از هیدرولیز آن، ترسیب الکترولس نیکل با استفاده از این عامل بایستی در محیط بازی (PH~12.5) انجام شود.
خوردگی و اهمیت آن
که استفاده از عاملهای کمپلکس کننده قوی مثل اتیلن دی آمین و EDTA را برای حفظ یونهای نیکل در محلول ایجاب میکند. از آن جایی که یکی از محصولات اکسیداسیون بوروهیدریدها، بور است. پوشش نیکل حاصل آلیاژ نیکل-بور (Ni-B) میباشد. ترکیب درصد این آلیاژ بستگی به شرایط ترسیب دارد.
در مقایسه با بوروهیدرید، DMAB عامل احیا کننده ضعیفتری است. اگرچه DMAB هم در محیط اسیدی تجزیه میشود ولی پایدارتر از بوروهیدرید است. از DMAB در محیطهای خنثی یا بازی ضعیف استفاده میشود. در این مورد هم بور همراه با نیکل بر روی سطح ترسیب میشود.
ترسیب نیکل با استفاده از هیدرازین منجر به پوششهایی از نیکل خالص میشود. زیرا که محصولات اکسیداسیون هیدرازین، نیتروژن و آب میباشد. PH محلول در این فرآیند بایستی بازی باشد (PH~11).
هیپوفسفیت رایجترین عامل احیا کننده برای ترسیب نیکل به روش الکترولس است. با استفاده از این عامل احیا کننده، محدوده وسیعی از PH میتواند مورد استفاده قرار گیرد (10-4). مکانیسم دقیق ترسیب نیکل توسط هیپوفسفیت هنوز مشخص نیست. گرچه چنین فرض شده که فرآیند ترسیب شامل ایجاد رادیکالهای هیدروژن و احیا یونهای نیکل توسط رادیکالهای هیدروژن بر روی سطح کاتالیزوری میباشد. این واکنشها را میتوان به صورت زیر نمایش داد.
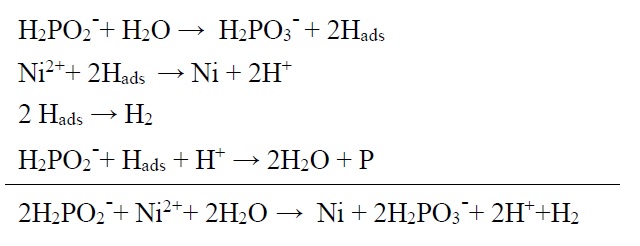
خوردگی و اهمیت آن
میزان فسفر در پوشش به شرایط حمام مثل غلظت نیکل، هیپوفسفیت و PH بستگی دارد. افزایش غلظت یونهای نیکل باعث کاهش میزان فسفر در پوشش میشود. در حالی که کاهش PH محلول باعث افزایش میزان فسفر میشود. با تغییر میزان فسفرُ میکروساختارهای پوشش تغییر میکند.
پوششهای محتوی میزان فسفر کم، ساختار کریستالی و پوششهای محتوی میزان فسفر بیشتر، ساختار آمورف دارند. علاوه بر آن، میزان فسفر خواص فیزیکی و شیمیایی پوشش را تعیین میکند. پوششهای با میزان فسفر بالا در محیطهای خورنده اسیدی مقاومت بسیار خوبی نشان میدهند. در حالی که پوششهای با میزان فسفر کم در محیطهای خورنده بازی مقاومتر هستند.
خوردگی و اهمیت آن
همچنین پوششهای با میزان فسفر کمتر مقاومت الکتریکی کمتر و لحیمپذیری بهتری دارند. از عاملهای کمپلکس کنندهی مورد استفاده در این آبکاری میتوان به آنیونهای یک دندانه استات. سوکسینات و پروپیونات، آنیونهای دو دندانه مالونات، پورفسفات و هیدروکسی استات. آنیون سه دندانه مالات و آنیونهای چهار دندانه سیترات اشاره کرد. عاملهای کمپلکس کننده بعضی خواص یونهای نیکل از جمله رنگ، پتانسیل احیا و حلالیت را تغییر میدهند [13].
خوردگی و اهمیت آن
1-2-منیزیم و آلیاژهای آن
1-2-1- خواص منیزیم
منیزیم هشتمین عنصر و ششمین فلز فراوان در پوسته زمین است. که حدود 1/93% از جرم پوسته زمین و 0/13% از جرم اقیانوسها را به خود اختصاص داده است. منیزیم فلزی بسیار سبک با دانسیته 1/74g/cm3 (حدود دو سوم آلومینیوم و یک چهارم آهن) است. نقطه ذوب آن 650 درجه سانتیگراد، نقطه جوش آن 1091 درجه سانتیگراد با ساختار بلوری هگزاگونال فضا پرکن میباشد.
منیزیم فلزی نقره رنگ، نرم، چکش خوار، قابل مفتول شدن و قابل بازیافت است [17]. این فلز خواص منحصر به فردی دارد که استفاده از آن را در بسیاری از کاربردها گسترده ساخته است. از دیگر ویژگیهای آن میتوان به نسبت سختی و وزن بالا، هدایت الکتریکی و حرارتی بالا، پایداری دیمانسیونی بالا. حفاظت الکترومغناطیسی خوب و قابلیت ماشینکاری خوب آن اشاره نمود [18].
1-2-2-آلیاژهای منیزیم
از ترکیب منیزیم با عناصری مانند آلومینیوم، روی، منگنز، مس و عناصر کمیاب آلیاژ تشکیل میشود. آلیاژهای منیزیم را میتوان به دو دسته کلی تقسیمبندی کرد:
الف) آلیاژهایی که بین 2 تا 10 درصد آلومینیوم و مقدار کمی روی و منگنز دارند مانند AZ91,AZ61,AZ31 و غیره.
آلومینیوم باعث سختی، قالبپذیری و مقاومت خوردگی آلیاژ در آب نمک میشود. روی باعث افزایش سیالیت میشود. این آلیاژها در دمای 95 تا 120 درجه سانتیگراد خواص مکانیکی خوبی نشان میدهند، در دماهای بالاتر از این خاصیت از بین میرود.
خوردگی و اهمیت آن
ب) دسته دوم آلیاژهایی هستند که شامل عناصر مختلفی به جز آلومینیوم مانند: تنگستن، زیرکونیوم و غیره میباشند. این آلیاژها ساختار دانهای ریزتری داشته و باعث بهبود خواص مکانیکی میشوند. این دسته از آلیاژها در دمای بالاتر خواص بهتری نسبت به دسته اول از خود نشان میدهند مانند: ZM6,WE43و… [17].
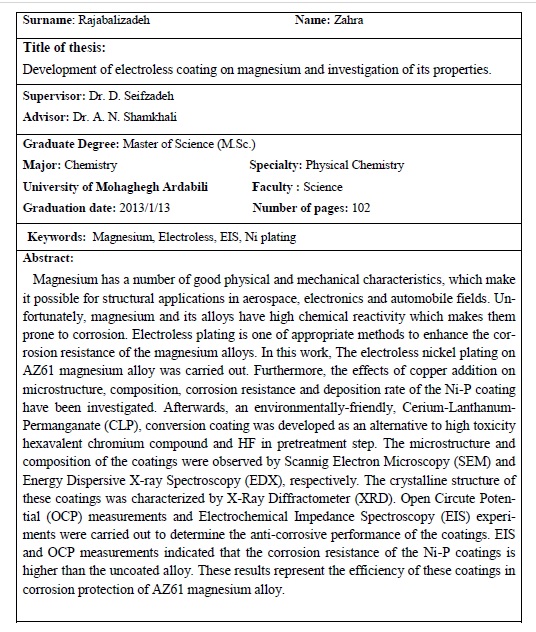
دانشگاه محقق اردبیلی
گروه شیمی