تولید آلیاژ مس،کروم با میزان حلالیت بالای کروم در زمینه مس
ارائه روشی برای تولید آلیاژ مس-کروم با میزان حلالیت بالای کروم در زمینه مس
تولید آلیاژ مس،کروم
چکیده
آلیاژهای مس-کروم به دلیل داشتن هدایت الکتریکی و حرارتی بالا. استحکام و مقاومت به خستگی و خوردگی خوب و شکل پذیری نسبتاً آسان. کاربرد گسترده ای دارند. این آلیاژها جزء خانواده آلیاژهای رسوب پذیر محسوب می شوند. از این رو هرچه در هنگام تولید، کروم بیشتری در زمینه مس به صورت محلول در آید. می توان رسوبات بیتشر و پراکنده ای حین مرحله عملیات حرارتی ایجاد نمود و استحکام آلیاژ را بالا برد. به همین دلیل در پژوهش حاضر برای تولید این رده از آلیاژها از روش شکل دهی در قالب مسی آبگرد به کارگیری شد. تا علاوه بر قرار گیری به میزان خلاقیت قابل قبول عنصر آلیاژی کروم در مس، هزینه تولید نیز افزایش چندانی نداشته باشند. نتایج نشان دادند که به کمک این روش می توان به حداکثر حلالیت 1/12 درصد اتمی کروم در زمینه مسی آلیاژ دست یافت.
مقدمه
آلیاژهای مس-کروم به دلیل هدایت الکتریکی بالا و استحکام مناسب در دمای بالا، از جمله مواد مهم مهندسی در صنایع الکتریکی محسوب می شوند. کاربرد عمده این آلیاژها در ساخت الکترودهای جوشکاری مقاومتی. سوئیچ های خلأ ولتاژ بالا، قالب های ریخته گری و سیم پیچی ترانسفورماتورهاست. حداکثر حلالیت کروم در مس، در دمای یوتکتیک 0/82 درصد اتمی است (دیاگرام فازی مس – کروم، شکل1).
تولید آلیاژ مس،کروم
این مقدار کروم موجود در محلول جامد، کسر حجمی رسوبات اندکی را در مرحله پیرسازی ایجاد می کند. لذا خواص مکانیکی مناسبی را فراهم نمی آورد. از این رو دست یابی به حلالیت بالای کروم در زمینه آلیاژ اهمیت ویژه ای دارد. به همین علت برای تولید این دسته از آلیاژها بیشتر از روش های انجماد سریع استفاده می شود.
تولید آلیاژ مس،کروم
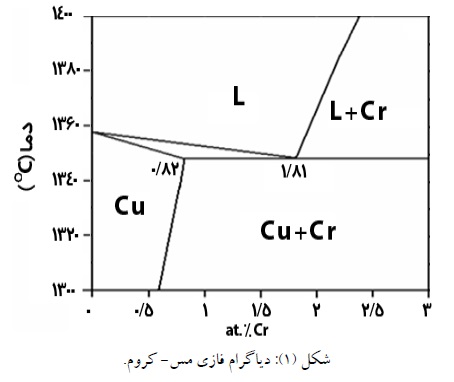
تونیک و همکارانش با به کارگیری روش انجماد سریع ذوب چرخشی توانستند حلالیت کروم را تا حداکثر 3/3 درصد اتمی در دمای محیط افزایش دهند. در حالی که کوریا و همکارانش با استفاده از روش افشانش پودر تنها به حلالیت کروم تا 2 درصد اتمی دست یافتند. فرآیند تولید نسبتاً طولانی، دشوار و بازدهی اندک این روش ها، سبب افزایش قیمت محصول نهایی می شود. برخی از محققین برای رفع این مشکلات از روش ذوب فلز معمولی استفاده کرده اند.
همتی با استفاده از روش ذوب فلز ثقلی در قالب تبریدی به این نتیجه رسید. که به علت سرعت سرمایش بالاتر این روش نسبت به حالت انجماد تعادلی، میزان کروم محلول در آلیاژ بیشتر از حالتی است. که انجماد به صورت تعادلی صورت گیرد. پارسایی برای افزایش هرچه بیشتر سرعت انجماد، پس از رساندن دمای مذاب به 1650 درجه سانتی گراد. ذوب فلز را در قالب مسی همدما با نیتروژن مایع انجام داد. به این ترتیب سرعت سرمایش به حدود 210 c/S رسید. اما به علت گرم شدن قالب در حین ذوب فلز و انجماد تا حدودی عملیات پیرسازی و تشکیل رسوبات همدوس نیز رخ داد.
این امر سبب شد که با انجام عملیات پیرسازی بعدی، رسوبات متشکل درشت تر شوند. و سختی آلیاژ تولیدی به این روش کمتر از مقدار مورد انتظار باشد. با توجه به مشکلات عملی موجود در برای تولید آلیاژ مس – کروم به روش های قبل در این تحقیق برای افزایش سرعت انجماد . و وقوع به حلالیت بیشتر عنصر کروم در زمینه مسی آلیاژ مس -کروم از روش ذوب فلز در قالب مسی آبگرد استفاده شد. نتایج بیان کرد که آلیاژ تولیدی به روش مذکور سختی و استحکام مناسبی را دارد. و تولید صنعتی این آلیاژ با این روش کاملاً اقتصادی و مقرون به صرفه است.
روش تحقیق
برای تهیه آلیاژ مس – کروم، 1000 گرم مس الکترولیتی با خلوص 99/99 درصد وزنی. به همراه 110 گرم کروم الکترولیتی با خلوص 99/98 درصد وزنی در بوته گرافیتی توسط کروه القائی ذوب شدند. دمای مذاب توسط آذرسنج دیجیتال کنترل شد. هنگامی که دمای مذاب به حدود 1650 درجه سانتی گراد رسید. ذوب فلز در قالب مسی آبگرد انجام شد. این قالب به شکل مکعب مستطیل به ابعاد 20×15×10 سانتی متر مکعب به صورت دو تکه طراحی شد. به منظور خنک شدگی قالب هشت ورودی و هشت خروجی آب در نظر گیری شد. برای گذاشت مواد مذاب. سه محفظه استوانه ای شکل به قطرهای 0/5،1،1/5 سانتی متر و به ارتفاع 10 سانتی متر درون قالب تعبیه شد. در انتهای هر محفظه نیز سوراخی 2 میلی متری جهت عبور ترموکوپل نوع k، به ضخامت 0/3 میلی متر سوراخکاری شد.
درگاه اتصال هر سه ترموکوپل به یک دستگاه ثبت اطلاعات وصل و این دستگاه به کامپیوتر متصل گردید. به کمک چنین سیستمی، اطلاعات دمایی در فواصل زمانی 0/8 ثانیه ثبت گردیدند (شکل2). سرعت های سرمایش در لحظات اولیه انجماد از روی این دیتاها استخراج شدند (شکل3). ترکیب شیمیایی آلیاژ با استفاده از دستگاه کوانتومتری تعیین شد. پس از برش عرضی نمونه ها توسط دستگاه میکرو کاتر، برای تعیین بهینه دما و زمان. عملیات حرارتی پیرسازی در سه دمای 450،500، 600 درجه سانتی گراد در زمان های مختلف بر روی نمونه ها انجام شد. سپس نمونه ها مانت و به منظور سختی سنجی توسط دستگاه الکتروپالیش اچ شدند. سختی سنجی نمونه های به کمک دستگاه ریز سختی سنج Struers مدل Duramin 20 انجام شد.
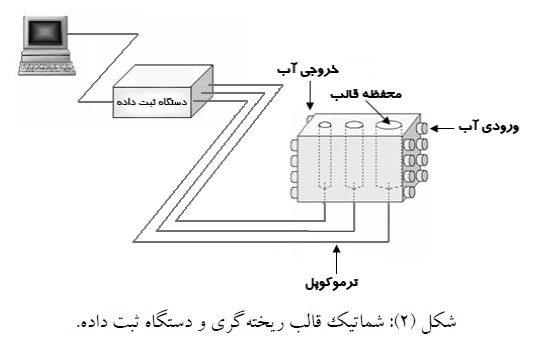
تولید آلیاژ مس،کروم
از هر نمونه ، حداقل 14 بار آزمایش با بار 245/2 میلی نیوتون و زمان 5 ثانیه حاصل آمد. و در نهایت میانگین سختی های مورد حاصل به عنوان سختی نمونه گزارش شد. حداکثر انحراف از میانگین سختی ها 10 درصد بود. به منظور تعیین میزان حلالیت کروم، پارامتر شبکه هر نمونه از روی الگوی پراش اشعه ایکس که حاصل آمد. به کمک دستگاه Advanced Bruker D8 تعیین شد. آزمایش XRD نمونه ها از زاویه 2θ =40° تا 2θ =140° و با وقفه های 8 ثانیه در هر 0/2 درجه انجام شد.
نتایج و بحث
آنالیز کوانتومتری نشان داد که آلیاژ مورد بررسی از 98/8 درصد وزنی مس و 1/2 درصد وزنی کروم متشکل است. بنابراین مابقی کرومی که اضافه شد به صورت اکسید و بخار از سیستم خارج گردید. نمونه های به قطر 1/5،1،0/5 سانتی متر به ترتیب به صورت نمونه های 1،2،3 نام گذاری شدند. شیب مماس بر منحنی سرد شدن در هر لحظه، سرعت سرد شدن در آن لحظه را نشان می دهد. با توجه به شکل (3) می توان مشاهده نمود که سرعت سرد شدن هر سه نمونه در ثانیه های اولیه انجماد بسیار زیاد است. در این لحظات ضریب نفوذ عنصر آلیاژی کروم با سرعت بیشتری کاهش می یابد. در نتیجه اتم های کروم فرصت کمتری برای جابجا شدن در مذاب و تشکیل رسوب را پیدا می کنند. و در مس جامد به صورت محلول باقی می مانند.
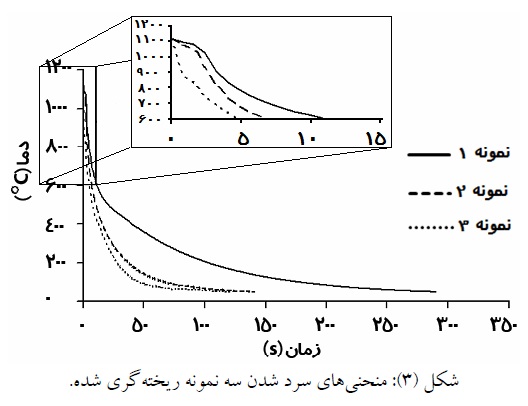
اندازه گیری شیب مماس بر منحنی های سرد شدن در لحظات اولیه انجماد نشان داد که سرعت سرد شدن نمونه های 3،2،1 150،185،292c/s است. بنابراین انتظار می رود که میزان کروم محلول از نمونه 1 به 3 افزایش یابد. حداکثر سرعت سرمایش حاصل از فرآیند ذوب فلز در قالب مسی خنک شده در نیتروژن مایع حدود 21°c/s گزارش شده است.
از آن جایی که در پژوهش حاصر سرعت سرمایش به °C/s292 نیز رسید. از این رو می توان گفت به علت تماس مداوم قالب با آب، دمای قالب به میزان زیادی افزایش نمی یابد. در حالی که اگر ذوب فلز در قالبی انجام شود. که قبلاً در نیتروژن مایع خنک شده است. به دلیل عدم تماس مداوم قالب با ماده خنک کننده. و افزایش دمای قالب در حین ذوب فلز و انجماد، سرعت سرمایش کمتری حاصل می شود.
با وارد شدن اتم های بیگانه کروم در زمینه مس. به دلیل یکسان نبودن اندازه اتم های آنها، تغییراتی در فواصل اتمی مس رخ می دهد. که تأثیر آنها به صورت افزایش پارامتر شبکه قابل اندازه گیری است. تنویک و همکارانش با اندازه گیری پارامتر شبکه آلیاژ مس-کروم تا 3/3 درصد اتمی کروم، رابطه خطی زیر را به دست آوردند:

در این رابطه [Cr]ss، میزان کروم محلول بر حسب درصد اتمی
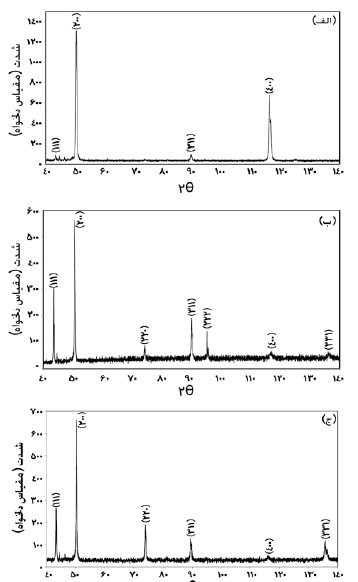
تولید آلیاژ مس،کروم
شکل (4): نمودار پراش اشعه x نمونه (الف)1، (ب)2 و (ج)3، در این نمودارها پیک های مربوط به فاز مس اندیس گذاری شدند.
و δa اختلاف بین پارامتر شبکه آلیاژ مس-کروم و مس خالص آنیل گردید. در پژوهش حاضر برای تعیین پارامتر شبکه آلیاژ، از روش کوهن استفاده شد. طبق این روش با استفاده از رابطه برگ (λ = 2dsinθ). و رابطه بین پارامتر شبکه و فاصله بین صفحه ای در شبکه های مکعبی (dhkl = a/(h2+k2+l2)1/2). به ازای هر پیک مربوط به فاز مس در نمودار پراش اشعه x (شکل4) یک پارامتر شبکه حاصل آمد. از طرفی با توجه به رابطه سینوسی بین زاویه اندازه گیری شده (θ). و پارامتر شبکه (a)، هر چه θ به 90 درجه نزدیک تر باشد. خطا در اندازه گیری آن تأثیر کمتری در دقت اندازه گیری a خواهد داشت.
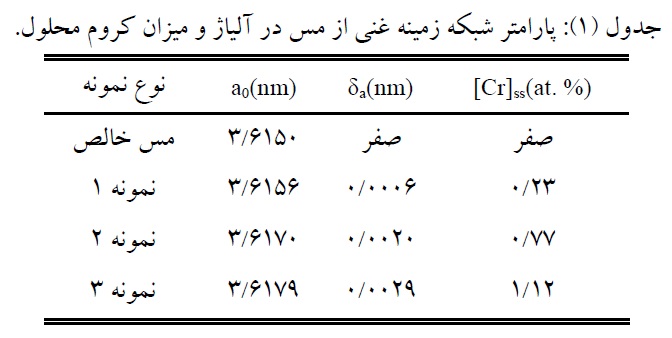
بنابراین برای بدست آوری دقیق انداره پارامتر شبکه بهتر است. از پیک هایی که نزدیک به 90=θ یا 180 =θ هستند استفاده شود. با توجه به اینکه نمودار پارامترهای شبکه مورد حاصل بر حسب عبارت cosθ.cotθ خطی است. با برونیابی نمودار خطی مذکور به سمت صفر (0→cosθ.cotθ یا 90→θ) میزان دقیق پارامتر شبکه حاصل خواهد آمد. (در مرجع 7 جزئیات روش کوهن برای اندازه گیری دقیق پارامتر شبکه نمایان و مشخص است).
بعد ازاندازه گیری پارامترهای شبکه نمونه ها، با استفاده از رابطه (1) میزان کروم محلول محاسبه شد. با توجه به اینکه پارامتر تجربی مورد حاصل از آزمایش پراش اشعه x، زاویه تفرق است. هرچه میزان خطا در به دست آوری این پارامتر کمتر باشد. محاسبات در به دست آوری پارامتر شبکه با استفاده از رابطه برگ کمتر است. از آنجا که طبق فرمول برگ، رابطه فاصله بین صفحات (و بالطبع پارامتر شبکه) و زاویه پراش، سینوسی است. هرچه زاویه مذکور به 90 درجه نزدیک تر باشد.
(یعنی 2θ=180)، خطا در اندازه گیری آن، به میزان کمتری در دقت فاصله بین صفحات و پارامتر شبکه مورد محاسبه اثر می گذارد. از سوی دگیر با رسم پارامترهای شبکه مورد حاصل با ازای هر پیک بر حسب cosθ.cotgθ، نموداری خطی به دست می آید. با برون یابی این نمودار به سمت مقادیر cosθ.cotgθ=0 (یا 180=2θ) میزان دقیق پارامتر شبکه به دست می آید. نتایج به دست آمده در جدول (1) آورده شده اند. از این جدول پیداست که میزان حلالیت کروم در مس در نمونه 3 با سرعت سرمایش 292C/s برابر با 1/12 درصد اتمی است. در حالی که طبق گزارش پارسایی، میزان حلالیت کروم در آلیاژ تولیدی به روش شکل دهی ذوب فلز در قالبی که خنک است. که در نیتروژن مایع با سرعت سرمایش 210C/s، تنها در حدود 0/41 درصد اتمی است.
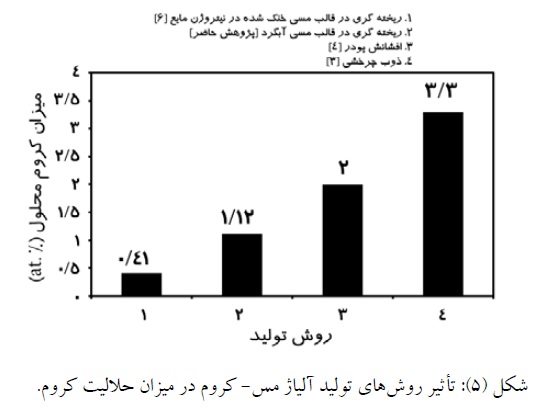
در شکل (5) حداکثر حلالیت کروم در آلیاژ مس-کروم تولیدی به روش های مختلف، با همدیگر مقایسه شدند. با توجه به این که سرعت سرمایش در روش افشانش پودر 10 کلوین بر ثانیه. و در روش ذوب چرخشی 10 کلوین بر ثانیه تخمین و محاسبه گردید. (به کمک روابط ریاضی و بدون استفاده از ترموکوپل)، می توان مشاهده کرد که به طور کلی با افزایش سرعت سرمایش. میزان حلالیت کروم در آلیاژ مس- کروم افزایش می یابد.
لازم به ذکر است که با توجه به اینکه روش مستقیمی برای اندازه گیری سرعت سرمایش در مواد تولیدی. به روش های افشانش پودر و ذوب چرخشی وجود ندارد. تعیین رابطه ای دقیق بین سرعت سرمایش و میزان حلالیت کروم در آلیاژهای تولیدی به این روش ها امکان پذیر نیست.
تولید آلیاژ مس،کروم
در شکل (6) رابطه بین سرعت سرمایش و میزان حلالیت کروم در آلیاژهای شکل دهی ذوب فلز است. در قالبی که خنک است در نیتروژن مایع و قالب مسی آبگرد نمایان و مشخص است. با خطی سازی دیتاهای شکل (6) به روش حداقل مربعات تا سرعت سرمایش 292C/s، رابطه زیر به دست می آید:
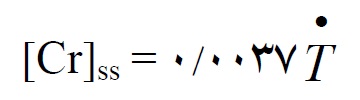
در این رابطه [Cr]ss میزان کروم محلول بر حسب درصد اتمی T• سرعت سرمایش است.
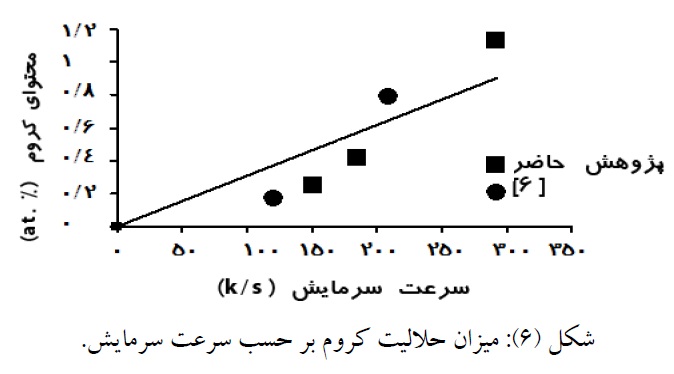
در شکل (7) منحنی های عملیات حرارتی پیرسازی نمونه ها در سه دمای 450،550،600 درجه سانتی گراد نمایان و مشخص است. مشاهده می شود که با افزایش دمای عملیات حرارتی، به علت افزایش ضریب نفوذ عنصر آلیاژی، سختی حداکثر در زمان های کمتری رخ می دهد. به طوری که در دمای 450 درجه سانتی گراد، حتی با گذشت 240 دقیقه نیز سختی همچنان سیر صعودی دارد. اما در دمای 600 درجه سانتی گراد و بعد از گذشت فقط 2 دقیقه سختی حداکثر ایجاد می شود. از سوی دیگر به علت این که در دمای بالا تعداد جوانه ها کمتر از رسوبات حاصل درشت تر هستند. با افزایش دمای عملیات حرارتی، حداکثر سختی کاهش می یابد.
اساساً هدف از مقاله حاضر بررسی ارتباط بین میزان سرعت سرمایش در مرحله انجماد. و میزان کروم محلول در زمینه آلیاژ مس-کروم و سختی آلیاژ بعد از مرحله عملیات حرارتی است. بنابراین پیگیری بحث مذکور نیاز جندانی به اشاره به تغییرات ریزساختاری در حین عملیات حرارتی و نمایش شکل های میکروسکوپی ندارد. بحث های مفصل در مورد ارتباط بین سرعت سرمایش و ریزساختارهای حاصل شده از آلیاژ مس-کروم در مقاله دیگر نگارندگان انجام شده است.
سختی نمونه 3 در تمامی دماها و زمان های عملیات حرارتی بیشتر از سایر نمونه هاست. سختی این نمونه بعد از عملیات حرارتی در دمای 450 درجه سانتی گراد به مدت 240 دقیقه به HV 161 رسید. با توجه به این که، این نمونه بیشترین سرعت سرمایش را دارد.
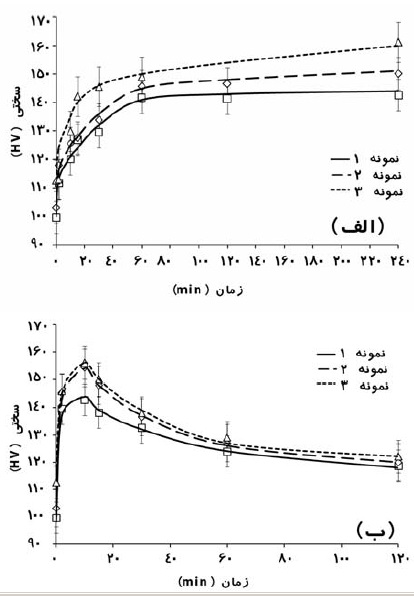
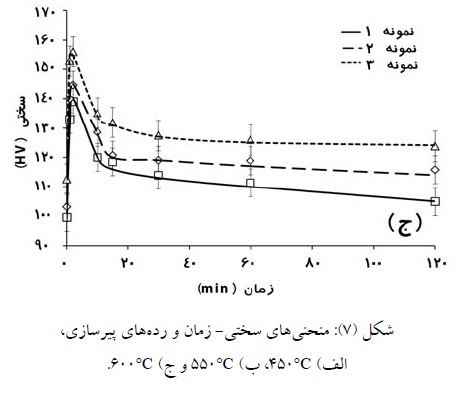
به نظر می رسد علت این امر به غلظت بالای عنصر محلول کروم در زمینه آلیاژ مربوط است. و به طوری که در حین عملیات حرارتی پیرسازی، رسوبات همدوس بیشتری در زمینه ایجاد می شوند. به عبارت دیگر کسر حجمی رسوبات استحکام بخش افزایش می یابد.
جدول (2): سختی نمونه های خالص بلافاصله پس از ریخته گری. حداکثر سختی و کسر حجمی رسوبات در نمونه های پس از عملیات حرارتی 450 درجه سانتی گراد.
تولید آلیاژ مس،کروم
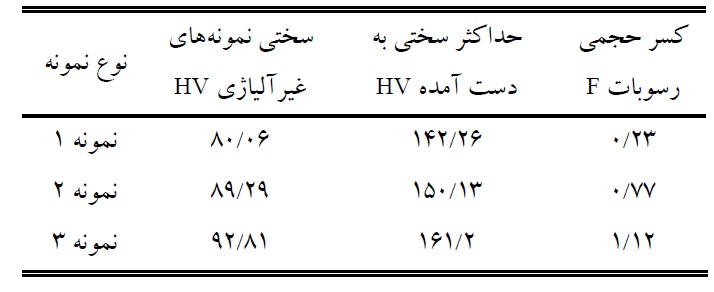
تولید آلیاژ مس،کروم
در همین رابطه کوریا و همکارانش توانستند. با تولید آلیاژ مس با حدود 2 درصد اتمی کروم، بعد از ساعت عملیات حرارتی در دمای 450 درجه سانتی گراد. به سختی HV 257 دست یابند. این امر مؤید اهمیت حلالیت عنصر آلیاژی کروم و زیاد بودن کسر حجمی رسوبات در دست یابی به سختی حداکثر در این آلیاژ است.
به منظور دست یابی به رابطه بین کسر حجمی رسوبات و تأثیر آن در افزایش سختی آلیاژ، ابتدا لازم است مقدار آن معلوم باشد. باید به این نکته توجه کرد که نسبت وزن اتمی به دانسیته مس و کروم بسیار به همدیگر نزدیک است. به عبارت دیگر حجم مولی مس و کروم تقریباً با همدیگر برابرند. بنابراین می توان این گونه در نظر گرفت که مقدار درصد اتمی کروم در محلول جامد که توسط آزمایش XRD به دست می آید. تقریب نسبتاً خوبی از کسر حجمی رسوبات کروم است.
در جدول (2) حداکثر سختی مورد حاصل از نمونه های مختلف بعد از عملیات حرارتی در دمای 450 درجه سانتی گراد. به مدت زمان 1 ساعت و همچنین سختی مس غیر آلیاژی بلافاصله پس از ریخته گری نشان داده شده است. علت افزایش سختی مس غیر آلیاژی از نمونه 1 به نمونه 3، افزایش سرعت انجماد و به تبع آن ریزتر شدن اندازه دانه هاست.
در شکل (8) نمودار ΔHVN (میزان افزایش سختی آلیاژ بعد از عملیات حرارتی به مدت 1 ساعت در دمای 450 درجه سانتی گراد. نسبت به مس خالص) بر حسب f1/2 (مجذور کسر حجمی رسوبات کروم) نشان داده شده است.
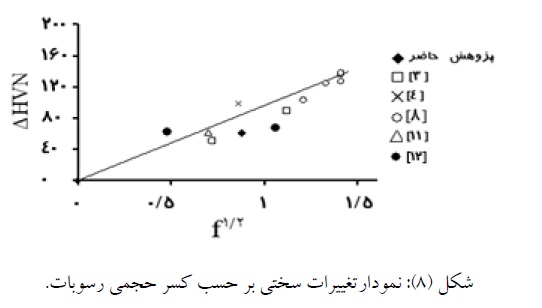
بر دست یابی به رابطه ای هر چه دقیق تر بین میزان افزایش سختی و کسر حجمی رسوبات. از دیتاهای مربوط به محققین دیگر [12,11,8,4,3] که در شرایط مشابه که حاصل گردید نیز بکارگیری شد. با خطی سازی دیتاهای مورد حاصل به روش حداقل مربعات می توان به رابطه زیر دست یافت:
ΔHVN = 96 f1/2
ضریب ثابت رابطه فوق از اندازه گیری شیب نمودار ΔHVN بر حسب f1/2 حاصل شده است.
نتیجه گیری
1-به کمک روش ذوب فلز در قالب مسی آبگرد به علت تماس مداوم قالب با آب، دمای قالب به میزان اندکی افزایش می یابد. و می توان به سرعت سرمایش 292C/s دست یافت.
2- با افزایش سرعت سرمایش، میزان حلالیت کروم در آلیاژ مس-کروم افزایش می یابد. به طوری که معادله
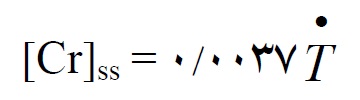
رابطه بین سرعت سرمایش و میزان حلالیت کروم در آلیاژ مس-کروم را نشان می دهد.
3- با افزایش دمای عملیات حرارتی پیرسازی از 450 به 600 درجه سانتی گراد. سختی حداکثر آلیاژ مس-کروم در مدت زمان کوتاه تری حاصل می شود لی مقدار آن کمتر است.
تولید آلیاژ مس،کروم
4- میزان افزایش سختی آلیاژ مس-کروم نسبت به حالت غیر آلیاژی از رابطه ΔHVN = 96 f1/2 تبعیت می کند.
5-روش ریخته گری در قالب مسی آبگرد، به عنوان روشی مناسب برای تولید آلیاژ مس-کروم با محتوای نسبتاً بالا قابل استفاده است.
فاطمه مجیدی، غلامحسین اکبری و سید محمد حسین حجاری
دانشگاه شهید باهنر کرمان،گروه مهندسی مواد دانشکده فنی دانشگاه شهید باهنر کرمان-پژوهشکده صنایع معدنی دانشگاه شهید باهنر کرمان
فولاد رسول دلاکان
با سالها تجربۀ ارزشمند و گرانبها در عرصه تأمین و توزیع انواع ورق آلیاژی و انواع فولاد آلیاژی. و با گواهینامه ها و آنالیزهای معتبری که ضمیمه محصولاتش به مشتریان خویش میها می کند. توانسته رضایتمندی مشتریان خویش را همواره فراهم آورد.
صنعتگر شریف و گرامی از اینکه ما را جهت خرید کالا (فولاد آلیاژی) مورد نیاز خویش. انتخاب می نمایید از شما سپاسگزاریم.
ارتباط با ما
02128423820 – 09122136675
واتس آپ: 09122136675 – فکس: 02128423820
اینستاگرام: fooladdalakan
ایمیل : fooladrasuldalakan@gmail.com