انتقال مواد (material handeling) و توزیع بار کوره ، احیاء به روش پرد-ورق آلیاژی
انتقال مواد (material handeling)
انتقال مواد (material handeling)-در این قسمت به چگونگی انتقال مواد در کارخانه احیاء بروش پرد. و همچنین چگونگی توزیع بار کوره مورد بررسی قرار می گیرد.
انتقال مواد (material handeling)
این بخش به چهار قسمت عمده تقسیم می شود:
1- محل بارگیری و تخلیه (Loading & Unloading)
2-انتقال اکسید های آهن (گندله) به کوره (Oxide Material)
3-توزیع بار در کوره
4-حمل و نقل محصول (آهنی اسفنجی) (Product Material)
در این بخش ها به کلیاتی در زمینه انتقال مواد و توزیع بار کوره. و همچنین شرح سیستم ها و دستگاه ها مرتبط بررسی می شود. که در همه کارخانه های پرد مشترک می باشد.
بارگیری و تخلیه
اکسید آهنی که بصورت گندله از واحد گندله سازی و کارخانه احیاء پرد ارسال می شود. باید دارای مشخصات مناسب با اهداف پروسس باشد تا محصولی مناسب و منطبق با پروژه بدست آید.
گندله مصرفی باید دارای ویژگی های زیر باشد:
انتقال مواد (material handeling)
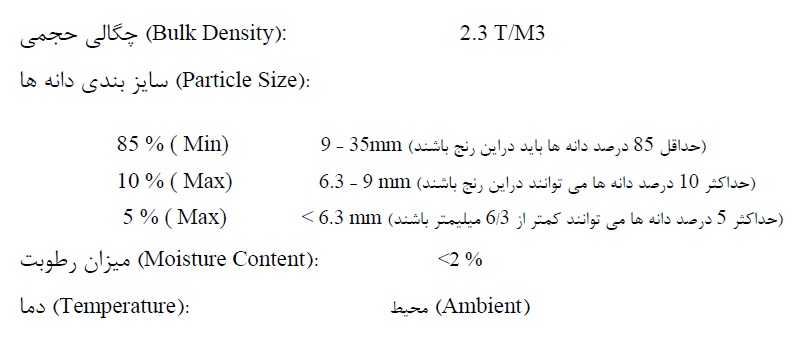

انتقال گندله از کارخانه سازنده به کارخانه احیاء، بوسیله کامیون ها، تریلرها و یا از طریق خطوط ریلی و واگن ها امکان پذیر است.
بار ارسالی از کارخانه گندله سازی به محل تخلیه بار (Unloading Station) در کارخانه احیاء می رود و بار در محل تخلیه می گردد.
کامیون ها و تریلرهایی که برای تخلیه بار دارای سیستم هیدرولیکی می باشند. با خود را به وسیله جک به داخل سیلوهای تعبیه میشود و در محل تخلیه بار (Truck Discharge Bin)، می ریزند.
آن دسته از کامیون ها و تریلرهایی که دارای سیستم تخلیه نمی باشند. بارشان توسط تجهیزی به نام Truck Tipper به درون سیلوها تخلیه می شوند.
دستگاه Truck Tipper شامل یک Plat Form فولادی بوده که در یک انتها بصورت لولایی به زمین متصل گردیده است. و با فشار دو جک در قسمت میانی آن زاویه 35 درجه. نسبت به سطح زمین پیدا می کند تا بتواند بار تریلی را تخلیه نماید.
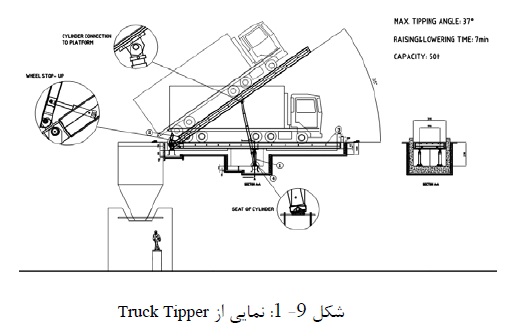
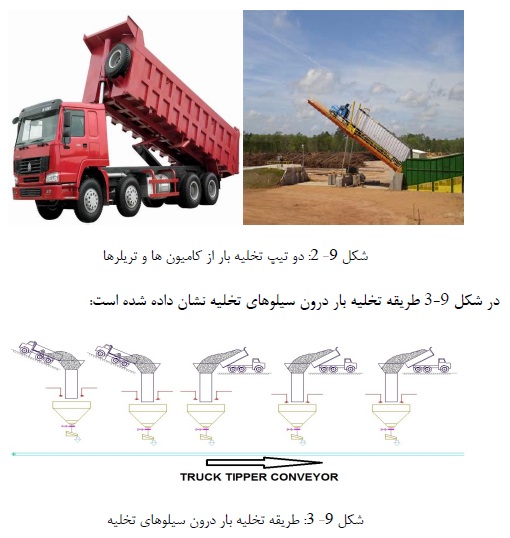
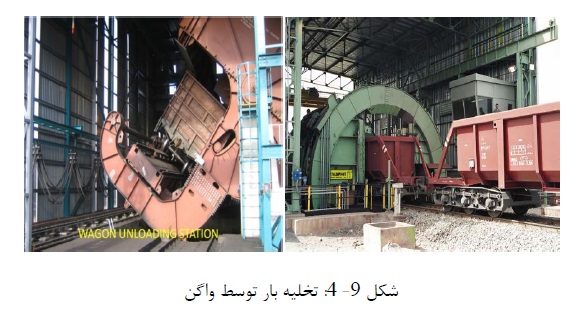
همانطور که در شکل نیز مشخص است سیلوهای تخلیه در مکانی پایین تر از کامیون ها قرار می گیرند. تا به راحتی درون آنها تخلیه گردد.
در زمان تخلیه بار میزان قابل توجهی گرد و غبار به هوا بلند می شود. که برای ممانعت از این امر، مقداری آب درون سیلوها همزمان با تخلیه باز پاشیده می شود.
گندله ها از پایین سیلوها توسط تغذیه کننده ها (Truck Discharge Feeder9 بر روی کانوایر تخلیه مواد (Tipper Discharge Conveyor) می ریزند. کنترل ریزش مواد به درون تغذیه کننده ها توسط دریچه های دستی (Truck Discharge Manual Gate) کنترل می شوند.
کانوایرها مواد را جهت ذخیره به واحد انباشت و برداشت (Stacker & Reclaimer) و یا مخزن ذخیره روزانه (Day Bin9 منتقل می کنند.
گندله ها توسط استکر که دارای یک کانوایر بر روی بازوی خود می باشد. در کپه های موازی (Piles) و در ابعاد مشخص انباشته می شوند.
برداشت گندله ها از محل انباشت توسط دستگاه ریکلایمر انجام می گیرد. این کار را توسط پاکت هایی که بر روی درام انتهایی خود دارد (Bucket Wheel) انجام می دهد. این دستگاه با استکر در یک ترکیب می باشند. به این صورت که در زمانی که بار مازاد باشد توسط کانوایر ها برای ذخیره به محل انباشت ارسال می شوند. در زمان انباشت ریکلایمر غیر فعال بوده و بار توسط بازوی استکر در محل تخلیه می شود. در زمانی که نیاز است از محل انباشت گندله برای احیاء ارسال شود. جهت حرکت کانوایر بازوی استکر برعکس میشود. و بار توسط پاکت های ریکلایمر بر روی کانوایر ریخته شده. و به سمت سیلوی تغذیه روزانه کوره (Day Bin) ارسال می شود.
در شکل های 9-5 و 9-6 طریقه انباشت و برداشت گندله نمایان و مشخص است.
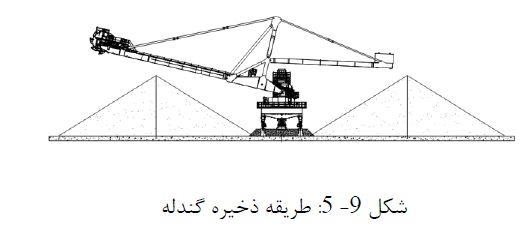
انتقال مواد (material handeling)
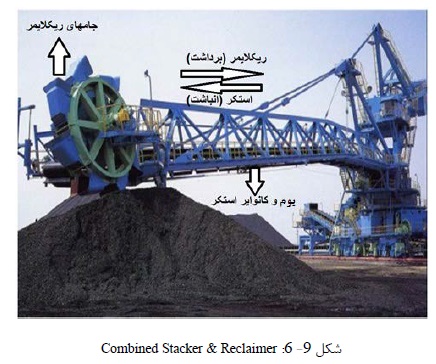
همانطور که ذکر شد گندله هایی که برای احیاء به کوره ارسال می شوند. در دی بین که سیلوی ذخیره روزانه می باشد. ذخیره می گردند. قبل از فرستادن به دی بین برای جدا کردن گندله هایی که خیلی بزرگتر از سایز مورد نیاز می باشند. و همچنین بر طرف نمودن سنگها و آشغال هایی که در طول مسیر وارد بار شده اند. گندله ها را درون یک سرند درشت دانه (Oversize Grizzly) ریخته و مواد درشت از خط انتقال به بیرون ریخته می شوند. و بقیه گندله ها از زیر سرند بر روی کانوایر ریخته و به دی بین انتقال داده می شوند.
انتقال مواد (material handeling)
در بین یک مخزن فولادی بزرگ است که گندله ها از قسمت بالا وارد آن می شوند. این مخزن جهت شارژ روزانه کوره می باشد. برای جلوگیری از خرد شدن مواد در هنگام ریزش درون دی بین از تجهیزی بنام راک لدر (Rock Ladder) استفاده می شود. این تجهیز با ساختمان پله ای که دارد. جلوی سقوط آزاد مواد درون دی بین را می گیرد و از خرد شدن مواد جلوگیری می کند.
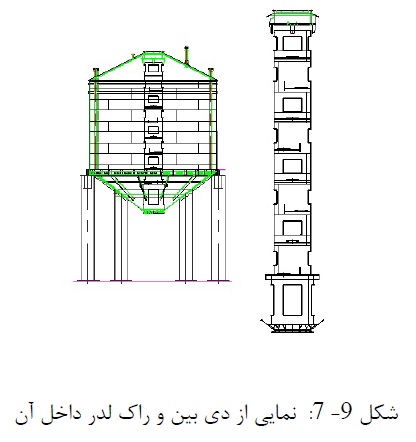
مواد از پایین دی بین توسط دو تغذیه کننده (Daybin Discharge Feeders). بر روی نوار نقاله می ریزند که ریزش مواد توسط یک دریچه دستی (Day Bin Discharge Slide Gate) تنظیم می شود.
در شکل 9-8 نمایی کلی از قسمت بارگیری و تخلیه گندله در کارخانه احیاء نمایان و مشخص است.
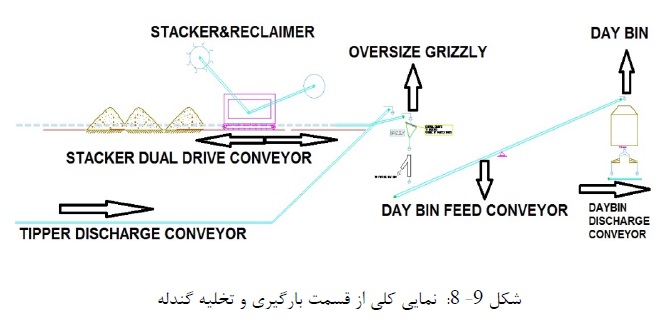
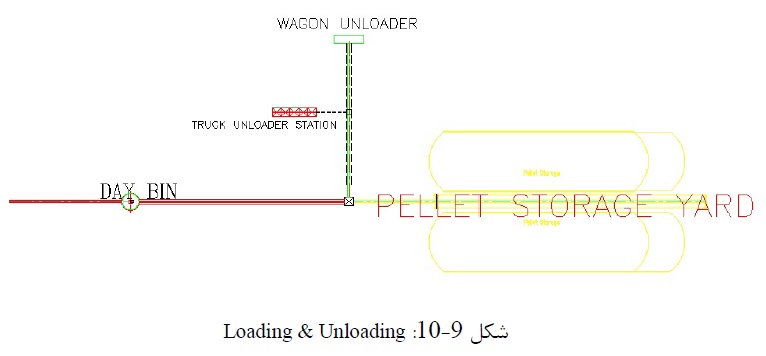
انتقال اکسیدهای آهن (گندله) به کوره (Oxide Material)
این واحد از سیستم انتقال مواد دارای 4 قسمت اصلی به شرح زیر می باشد.
Remet Feed .I
Oxide Screen .II
Lime Coating System .III
Oxide Sampler .IV
در ادامه به توصیف مختصری در مورد این واحدها می پردازیم.
Remet Feed
این واحد بعد از دی بین قرار دارد. در زمان راه اندازی کارخانه، چون درجه احیاء محصول به میزان مورد نظر نمی رسد. لازم است که محصول خروجی از کوره دوباره برای انجام عملیات احیاء به مسیر شارژ باز گردد. بار بازگشتی از کوره در این محل تخلیه می گردد. این عمل (تخلیه کوره و بازگشت مواد به خط شارژ) تا زمانی انجام می شود که محصول به درجه مناسبی از احیاء برسد.
در مواقعی که دی بین به دلایلی مثل خراب بودن تغذیه کننده های زیر آن، توانایی شارژ خط را ندارد. تا زمان رفع عیب، از این واحد جهت شارژ اضطراری نیز استفاده می شود.
این واحد دارای یک قیف تغذیه کننده (Remet Feed Hopper) می باشد. که گندله توسط کامیون درون آن ریخته می شود. گندله ها توسط ناودانی از پایین قیف روی نوار نقاله می ریزند. ریزش مواد توسط یک دریچه واقع در زیر قیف کنترل می شود.
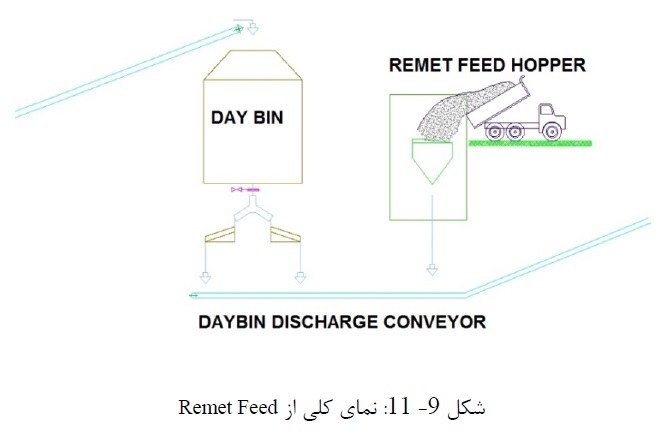
Oxide Screen
در اثر نقل و انتقالات صورت گرفته، مقداری از گندله ها خرد می شوند. که نه تنها برای احیاء مناسب نیستند. بلکه باعث کاهش کیفیت احیاء نیز می شوند. بعضی از گندله ها نیز بزرگتر از سایر مناسب (8-16mm) برای احیاء می باشند.
مجموع این گندله ها باید از مسیر شارژ کوره خارج شوند. برای این منظور، گندله ها وارد یک یا دو غربال (Oxide Screen) می شوند. در این غربالها گندله ها در سه سایز، ریز دانه، دشت دانه و دانه های مناسب دسته بندی می شوند. درشت دانه ها توسط نیروی ثقلی از بالای غربال به بیرون ریخته می شوند. دانه هایی که دارای سایز مناسبی برای احیاء می باشند. از قسمت وسط غربال بر روی نوار نقاله می ریزند و به سمت کوره هدایت می شوند.
دانه های ریز از پایین غربال روی یک نوار نقاله مجزا (Oxide Fines Conveyor) ریخته شده. و داخل یک سیلو (Oxide Fines Bin) ذخیره می شوند. تا به کارخانه گندله سازی برای استفاده مجدد فرستاده شوند.
در شکل 9-12 نمای کلی از این قسمت نمایش داده شده است.
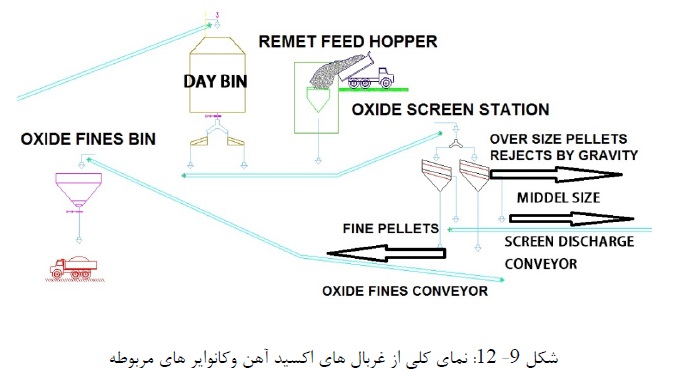
Lime Coating System
همانطور که قبلاً نیز ذکر شد بالا بودن دمای گاز احیاء باعث افزایش راندمان فرآیند احیاء می شود. ولی این دمای بالا باعث ذوب سطحی گندله ها میشود که در نتیجه آن، گندله ها به هم می چسبند و تشکیل خوشه می دهند. این امر باعث کاهش کیفیت احیاء در آنها می شود.
برای جلوگیری از ذوب سطحی گندله ها و افزایش دمای ذوب آنها. لایه نازکی از آب آهک شامل 0/5 تا 2/5 کیلوگرم به ازای یک تن گندله بر روی مواد پاشیده می شود. این کار توسط واحد آب آهک پاشی (Lime Coating System) واقع در قبل از کوره انجام می شود.
آب آهک توسط یک سیستم پنوماتیکی درون مخزن ذخیره وارد می شود. و توسط دریچه تغذیه کننده بر روی گندله ها پاشیده می شود.
برای جلوگیری از ناپایداری آب آهک درون مخزن، یک همزن در قسمت خروجی مخزن قرار دارد.
در زیر تصاویری از تجهیزات این واحد نمایان است.
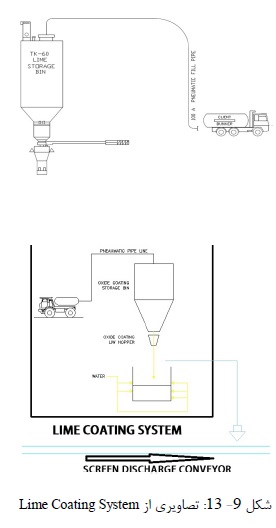
Oxide Sampler
قبل از اینکه گندله ها وارد کوره شوند از آنها بوسیله دستگاه Oxide Sampler. جهت بررسی ترکیبات شیمیایی و خواص فیزیکی و مکانیکی و همچنین دانه بندی بصورت ادواری نمونه برداری می شود.
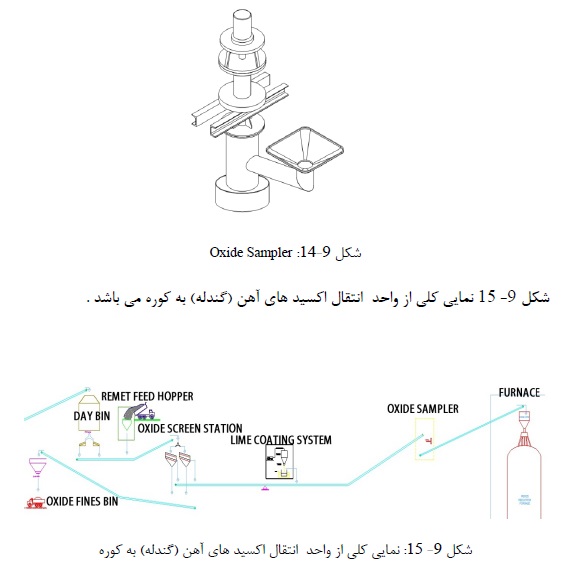
توزیع بار در کوره
گندله هایی که که بعد از عبور از مراحل مختلف دارای شرایط مناسب برای احیاء می باشند. به سمت کوره هدایت می شوند. قبل ورود به کوره، گندله ها وارد یک مخزن ذخیره (Charge Hopper) واقع در بالای کوره می شوند. شارژ هاپر یک مخزن استوانه ای بزرگ می باشد. که در انتها به یک قیف متصل است. این تجهیز جهت نگهداری مقداری گندله جهت شارژ در کوره و ایجاد یک جریان پایا و یکنواخت در کوره مورد استفاده قرار می گیرد.
گندله ها از قیف پایین شارژ هاپر به سمت کوره شارژ می شوند. در قیف شارژ هاپر به دلیل متراکم شدن جریان گندله ها در اثر کاهش سطح مقطع. احتمال تشکیل سازه گنبدی شکل و مسدود شدن مسیر شارژ توسط گندله ها وجود دارد. در صورت ایجاد این انسداد مقداری آب با فشار بالا توسط نازلهای تعبیه شده درون قیف شارژ هاپر پاشیده می شود. این آب حرکت گندله ها را روان میسازد و از مسیر رفع گیر می نماید.
لازم به ذکر است آبی که در شارژ هاپر مصرف می شود نیاز نیست سرد شود و یا از پروسس آب تمیز باشد. پرد از خروجی پروسس آب گرم در شارژ هاپر استفاده می کند. که این خود نشان دهنده یک طراحی دقیق برای کاهش هزینه های ناشی از بهسازی و سرد کردن آب پروسس می باشد.
جریان مواد پس از عبور از شارژ، هاپر، وارد لوله و پایۀ انتقال مواد بنام تاپ سیل لگ (Top Seal Leg) می شود.
در مسیر سیل لگ، جهت کنترل شارژ مواد به درون کوره. از دریچه ای لغزان و کشویی به نام تاپ اسلاید گیت (Top Slide Gate) استفاده می شود. این دریچه توسط بازوی هیدرولیکی باز و بست می شود.
کار اصلی که در سیل لگ انجام می شود. تزریق گاز عایق جهت عایق کردن بالای کوره و ممانعت از خروج گازهای احیایی از بالای کوره می باشد. در صورت اینکه سیستم عایق بندی که مشکل روبرو شود. مسیر خروج گاز توسط اسلاید گیت بست می شود و شارژ کوره تا رفع عیب متوقف می شود.
گاز عایق درون یک مخروطی پس از اسلاید گیت (Seal Gas Cone) تزریق می شود.
شکل 9-16 نمای کلی از تجهیزات مورد بیان را تا این قسمت را نشان می دهد.
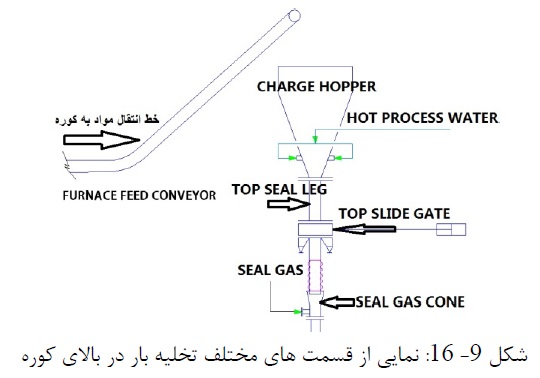
گندله ها پس از عبور از سیل لگ وارد یک توزیع کننده (Oxide Distributor) می شوند. این توزیع کننده دارای چندین پایه (Distributor) می باشد. که از بالای کوره وارد کوره شدند و باعث می شوند. که جریان یکنواختی از گندله درون کوره بوجود آید.
به دلیل شکل خاصی که این تجهیز دارد به آن اختاپوسی هم می گویند.
در شکل 9-17 نمایی از این تجهیزات نمایان و مشخص است.
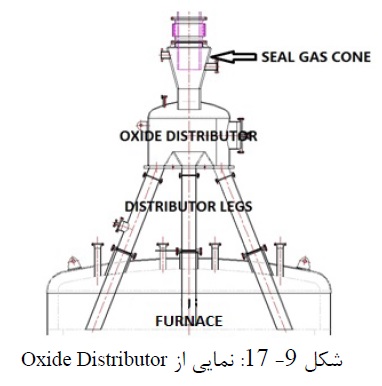
مواد به صورت یکنواخت وارد کوره می شوند. این جریان یکنواخت باعث می شود. که فرآیند احیاء با کیفیت بالا و بصورت یکنواخت انجام پذیرد.
مواد پس از عبور از ناحیه های احیاء و انتقال کوره و تبدیل به محصول. برای سرد شدن وارد ناحیه خنک کننده کوره (Cooling Zone) می شوند. تجهیزی که ناحیه خنک کننده کوره را از ناحیه انتقال کوره جدا می کند. کلاه چینی (China Hat) نام دارد. این تجهیز جریان محصول را به چهار قسمت مساوی تقسیم کرده و به سمت دیواره کوره هدایت می کند. تراکم مواد باعث می شود که فضای خنک کننده کوره از قسمت بالای آن جدا شود.
در شکل 9-18 تصاویری از این تجهیز نمایان و مشخص است.

همانطور که قبلاً نیز بیان شد. چون فرایند احیاء در دمای بالا و نزدیک به ذوب انجام می شود. ممکن است که تعدادی از محصولات بهم بچسبند و تشکیل کلوخه (Cluster) بدهند. برای این منظور در روش پرد از دو ردیف کلوخه شکن (Burden Feeders9. در وسط و پایین ناحیه خنک کننده کوره برای شکست کلوخه ها و جدا سازی محصولات بهم چسبیده مصرف می شود.
انتقال مواد (material handeling)
کلوخه شکن هایی که در یک ردیف قرار می گیرند. به کمک یک هیدرو موتور حول محورشان می چرخند. این شفتها بصورت مجزی دوران می کنند. و این امر باعث می شود وقتی که هر یک از شفت ها. به دلیلی در حرکتش خللی ایجاد شد بقیه به حرکت خود ادامه دهند.
کلوخه شکن ها باعث ایجاد حرکت دقیق و منظم بار در کوره می شوند.
شکل 9-19 تصویر و جانمایی کلوخه شکن ها در کوره به روش پرد را نشان می دهد.
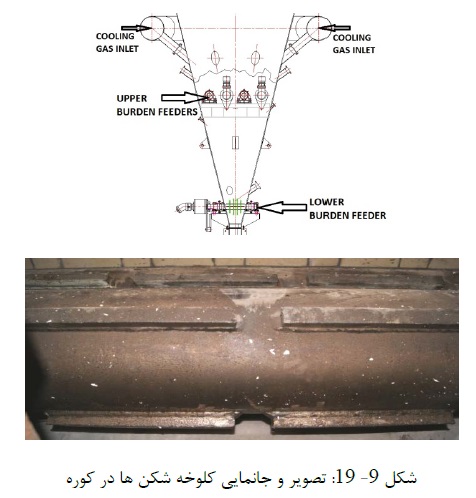
محصول کوره احیاء که همان آهن اسفنجی است بعد از عبور از ناحیه خنک کننده و سرد شدن. توسط لوله انتقال مواد پایین کوره (Bottom Seal Leg) وارد یک مخروط (Seal Gas Cone) میشود. گاز عایق به داخل این مخروط تزریق می شود. و مانع از خروج گاز احیاء از پایین کوره می گردد.
بعد از این مخروط یک دریچه (Lower Slide Gate) در مسیر حرکت محصول قرار دارد. این دریچه وظیفه کنترل خروج مواد از کوره را بر عهده دارد. در روش پرد مواد در حدود 8 ساعت درون کوره می مانند.
در زمانی که سیستم عایق بندی پایین کوره دچار مشکل شود این دریچه مسیر خروج محصول را تا رفع مشکل بطور کامل مسدود می کند.
و در نهایت محصول توسط لوله های رابط درون یک تغذیه کننده (Discharge Feeder) واقع در زیر کوره ریخته می شود. این تغذیه کننده مواد روی نوار نقاله (Furnace Discharge Conveyor) برای انتقال به مراحل بعد می ریزد.
در شکل 9-20 نمایی از این تجهیزات معلوم و مشخص است.
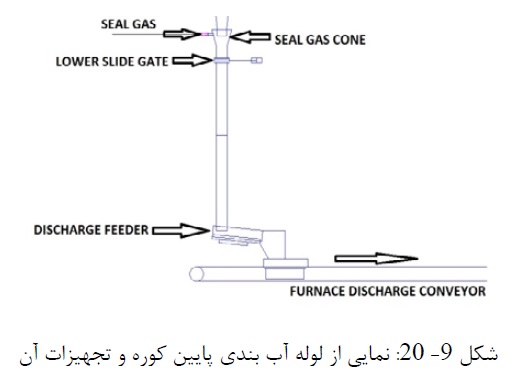
شکل 9-21 نمایی کلی از قسمت ها و تجهیزات مختلف کوره می باشد.
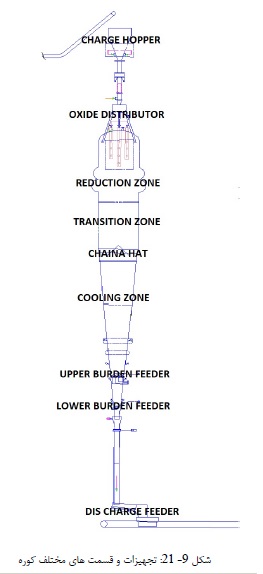
حمل و انتقال محصول (آهن اسفنجی) (Product Material)
بعد از خروج محصول از کوره توسط دستگاه نمونه گیر (Product Sampler) از آن نمونه برداری می شود.
به دلیل بالا بودن دما در کوره مقداری از محصولات به هم می چسبند. و تشکیل خوشه (Chuster) می دهند. که برای جدا نمودن آنها از محصول، مواد به یک واحد غربال (Product Grating Feeder) هدایت می شوند. در این واحد مواد به هم چسبیده به دلیل بزرگ بودن. از سرند غربال عبور نمیکند و از دیگر مواد جدا می شوند. و بصورت کپه (Cluster Pile) انباشته می شوند. این مواد پس از خردایش به فرآیند احیاء باز گردانی می شوند.
موادی که از غربال عبور می کنند برای انتقال به سیلوهای انباشت (Storage Bins). بر روی نوار نقاله مربوطه (Grizzly Discharge conveyor) ریخته می شوند.
لازم به ذکر است در صورت پر بودن سیلوهای تغذیه و یا بروز اشکال در سیستم انتقال. محصولات بصورت کپه (Remet/Emergency Piling) در محل غربال انباشته می شوند. و در صورت لزوم مورد استفاده قرار می گیرند. این کار توسط یک دوراهه (Tow Way Diverter Gate) انجام می شود.
در شکل 9-22 نمایی از این تجهیزات آمده است.
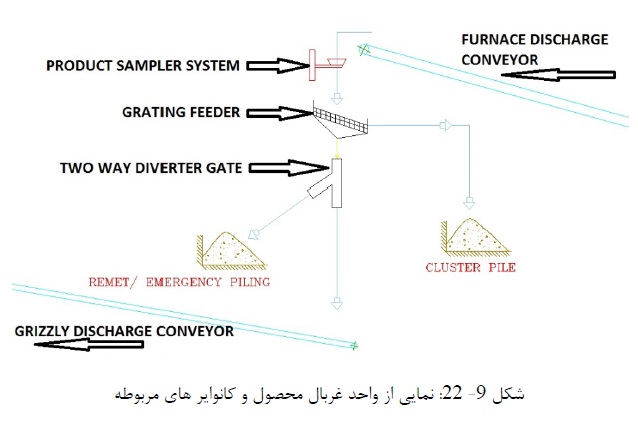
ساختمان سیلوهای ذخیره آهن اسفنجی (Storage Bin) شبیه به دی بین است.
مواد از زیر این سیلوها توسط تغذیه کننده ها (Silo Discharge Feeders) بر روی نوار نقاله (Silo Discharge Conveyor) ریخته می شوند. و به یک واحد غربال نهایی (Product Screen) ارسال می شوند.
در کنار سیلوهای ذخیره محصول، سازه ای شامل یک قیف (Emergency Charge Hopper) وجود دارد که از آن جهت شارژ اضطراری خط استفاده می شود.
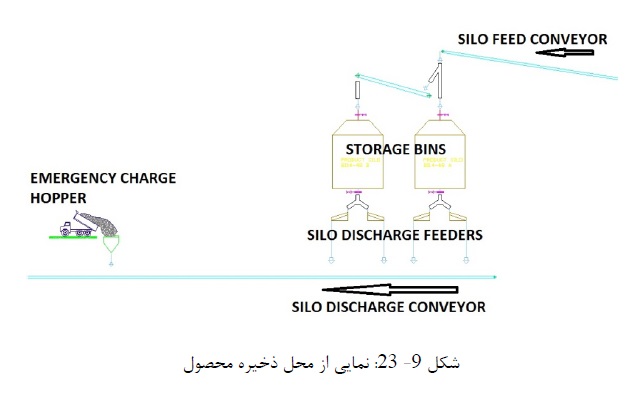
در واحد غربال نهایی، محصولاتی که دارای سایز مناسبی جهت ذوب می باشند. به واحد ذوب قوس الکتریکی (S.M.P)ارسال می شوند. و یا بصورت کپه (Pile) انباشته میشود تا بعداً به واحد ذوب ارسال شوند.
ریزدانه هایی که جهت ذوب مناسب نیستند از غربال عبور نموده. و توسط کانوایر مربوطه (Product Fines Conveyor9 به محل ذخیره (Product Fines Bin). جهت استفاده در واحد بریکت سازی سرد (Cold Briquette) ارسال می شوند.
در شکل 9-24 تصویری از تجهیزات این قسمت نمایان است.
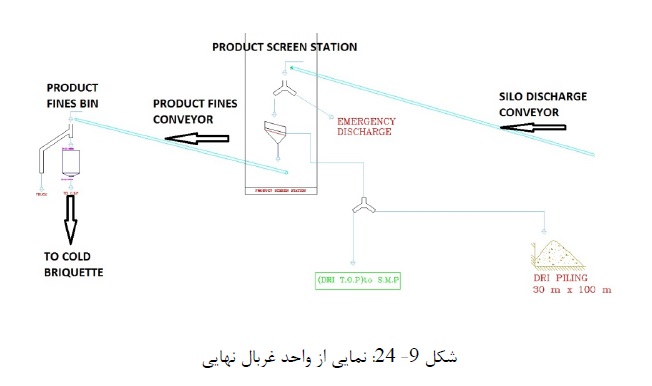
شکل9-25 نمایی کلی از تجهیزات حمل و نقل محصول می باشد.
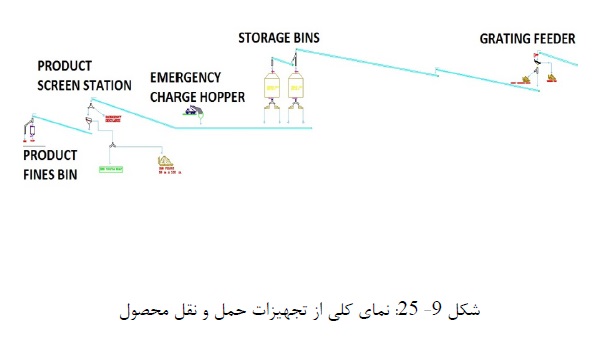
انتقال مواد (material handeling)
بریکت سازی سرد
ریزدانه های محصول که سایز آنها از 5 میلیمتر کوچکتر باشد. برای استفاده در واحد ذوب مناسب نمی باشند. به منظور استفاده از این مواد آنها را به واحدی نام بریکت سازی (خشته سازی( انتقال می دهند.
در این واحد با تحت فشار قرارگیری ریزدانه ها آنها را به خشته هایی مناسب برای ذوب تبدیل می نمایند. به همین دلیل به این واحد، بریکت سازی سرد (Cold Briquette) گویند.
تجهیزات این اوحد عبارت اند از:
- Fine Bin (مخزن ریزدانه)
- Binder Mixer (مخلوط کننده چسب)
- Belt Conveyer For Fine & Briquette (نوار نقاله برای ریزدانه ها و بریکت)
- Briquetting Machine (ماشن بریکت سازی)
- Dedusting System (سیستم غبارگیر)
- Belt Weigher (نوار توزین)
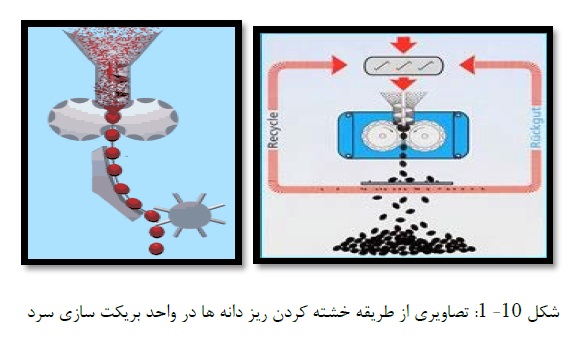
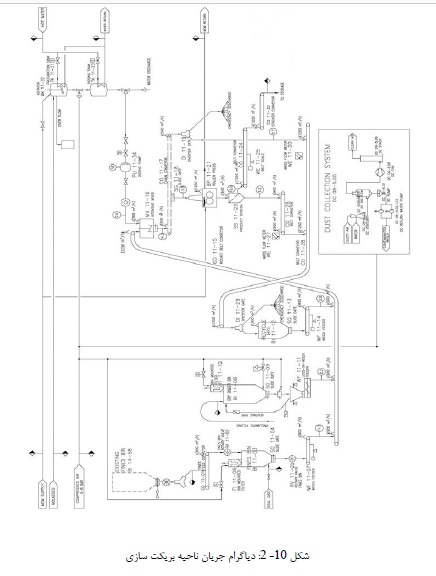
تجهیزات مورد استفاده در کارخانه احیاء به روش پرد
در این فصل به شرح و وصف بعضی از تجهیزات و سازه های مورد استفاده در پروسس احیاء که پر کاربرد می باشند. (مثل کمپروسورها) و یا کمی نا آشنا (مثل رطوبت گیرها و برج های خنک کننده) پرداخته شده است. تا از این طریق درک بهتری به خواننده منتقل گردد.
انتقال مواد (material handeling)
جدا کننده ها (Separators)
در خطوط فرایند، گاهی اوقات سیال دارای فازهای گوناگون می باشد. و نیاز است تا آن فازها از یکدیگر جدا گردند. عملیات جداسازی فازها توسط جداکننده ها انجام می پذیرد.
عملیات جداسازی براساس خواص فیزیکی و شیمیایی مثل اندازه ذرات معلق در سیال. سرعت سیال، میل ترکیبی فازی از سیال با ماده دیگر، خاصیت چسبندگی سطحی، نقطه بخار و نقطه شبنم صورت می پذیرد.
رطوبت گیرها
آب متداولترین و نامناسب ترین ناخالصی موجود در گاز است. حضور آب در جریان گاز سبب بروز برخی مشکلات در عملیات مربوط به تولید می شود. بسته به دما و فشار موجود در تأسیسات، آب ممکن است. به مایع تبدیل میشود و منجر به تشکیل هیدارت ها. ترکیبات جامد یا در صورت حضور سازنده ای اسیدی در گاز، منجر به خوردگی شدید شود. تشکیل هیدارت چه در فرآیند و چه در حمل و نقل و انتقال صورت گیرد. باعث گرفتگی در شیرها و مسیر خطوط لوله ارتباطی گاز میشود. و سبب از کار اندازی و خرابی دستگاه های ارزشمند می شود. لذا جداسازی آب از گاز، فرایندی ضروری به شمار می رود.
رطوبت گیرها جداکننده هایی هستند که رطوبت مضر موجود در سیال را برطرف می کنند.
- افزایش کارایی گاز (افزایش راندمان گاز)
- افزایش خلوص محصول
- کاهش هزینه های عملیات
- کاهش آلودگی هوا (چون رطوبت گیرها آلودگیهای همراه با سیال را نیز می گیرند.)
- کاهش خوردگی مجراها و افزایش طول عمر تجهیزات
- افزایش بازیافت مایعات مفید می شود.
انتقال مواد (material handeling)
روشها و مکانیزم های زیادی برای رطوبت زدایی وجود دارد که می توان به موارد زیر اشاره نمود.
1- جدا کننده های گرانشی (Gravity Separators)
2- جدا کننده های گریز از مرکزی (Centrifugal Separators)
3- برطرف کننده های رطوبت (Mist Eliminator)
4- Filter Vane Separators
5-L/G Coalescers
Mist Eliminators
این نوع رطوب گیرها ذرات بخار موجود در سیال را که قطر آنها بین 0/01 تا 10 میکرومتر. ( μm1 = 0.001mm) است را از سیال می زدایند.
این رطوبت گیر بطور عمده در 2 نوع زیر ایجاد می شوند.
I. توری (Mesh)
II. پره ای (Vane)
اساس کار این رطوبت گیرها تفاوت اندازه و وزن ذرات معلق در گاز و همچنین چسبندگی سطحی سطوح آنها می باشد.
Mesh
مش شبکه ای است که از رشته های بهم بافته شده ساخته میشود. و جنسشان از فلز، پلاستیک و یا شیشه می باشد.
جریان گاز از بین این تارها عبور می نماید. قطرات درشت تر بخار آب موجود در گاز، به تارهای مش برخورد می کنند. و بهم می چسبند. قطرات گرفتار شده یکی می شوند. و در نهایت سقوط می کنند.
قطرهای کوچکتر همراه با جریان گاز از اطراف رشته ها عبور می نمایند.
برای حذف قطرات ریزتر از 1 میکرون طنابهای چند رشته ای پلاستیکی یا شیشه ای، درون شبکه مش بافته می شوند. محصول یک شبکه کامپوزیتی یا چند بافته می باشد.
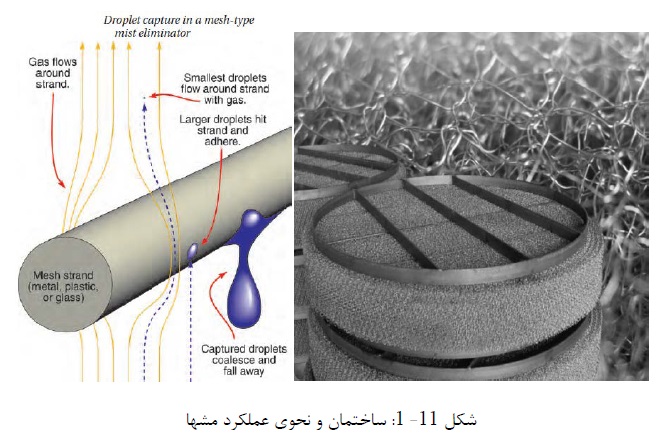
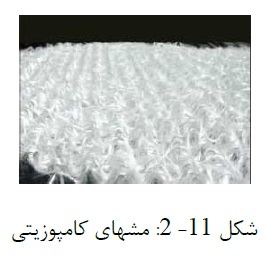
پرکاربردترین شکل این شبکه های بهم تابیده شده (مش). بصورت پدهایی (تشک مانند) با رشته های پیچیده شده با ضخامت 4 یا 6 اینچ می باشد. که صلبیت (استحکام) آنها بوسیلۀ یک قاب معمولا فلزی تأمین می شود.
پدها می توانند به هر شکلی تولید شوند. اما عمدتاً دایره ای یا مستطیلی می باشند.
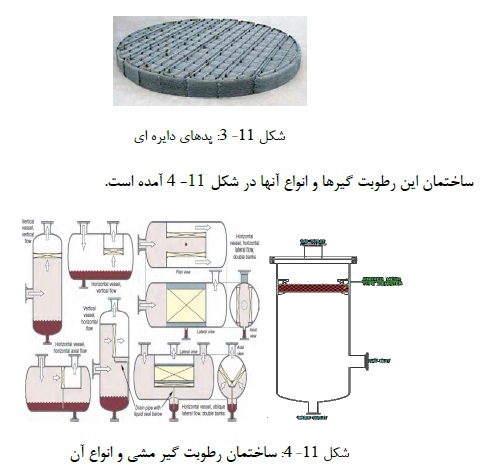
Vane
این نوع از رطوبت گیرها متشکل از دسته پره های ثابت و مواج با فضای کمی هستند که در جهت جریان گاز قرار می گیرند.
این ابزار عمدتاً برای ذرات ریزتر از 20 میکرون مناسب نمی باشند. اما نسبت به پدهای شبکه ای مقاوم تر بوده و افت فشار کمتری را ایجاد می کننند.
آرایه های پره ای می توانند افقی یا عمودی قرار گیرند. گاهی اوقات برای بهینه سازی می توانند در ترکیب با پدهای شبکه ای قرار گیرند.
پوشش جلوی پره ها می تواند از فلز یا پلاستیک باشد.
انتقال مواد (material handeling)
گاز از میان پره های رطوبت گیر عبور می نماید. ممنتوم (اندازه حرکت) قطرات بزرگتر، باعث می شود. که آنها در مسیر مستقیم حرکت کنند و با چرخش گاز، از گاز جدا شوند و روی پره ها بچسبند.
قطرات گیر افتاده بهم می پیوندند. و در نهایت وقتی که سنگین شدند سقوط می کنند. گاز و قطرات ریزتر از بین صفحات عبور کرده و از رطوبت گیر خارج می شوند.
ساختمان و نحوۀ عملکرد رطوبت گیرهای پره ای در شکل 11-5 نمایان و مشخص است.
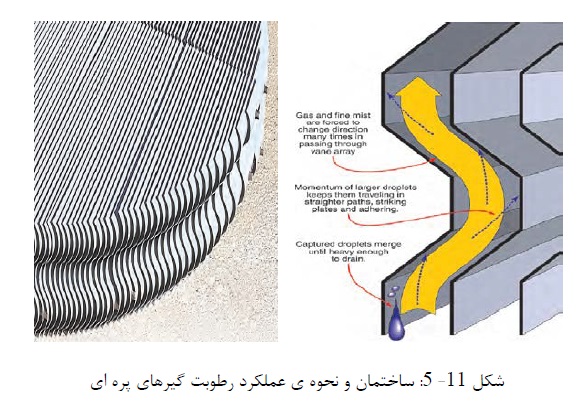
ساختمان رطوبت گیرهای پره ای شبیه رطوبت گیرهای مشی می باشد. با این تفاوت که در این نوع بجای بکارگیری از بسته های مش از بسته های پره ای استفاده می شود.
رطوبت گیرهایی که در روش پرد جهت احیاء اکسید آهن مورد استفاده می باشد. از نوع مش می باشد. در رطوبت گیر شوینده ها از نوع پره ای آنها بکارگیری شد.
Inlet Mist Eliminator
این نوع از رطوبت گیرها ذرات گرد و غبار و همچنین رطوبت، که اندازه آنها بزرگ تر از 5 میکرون (5 μm) می باشند. را از جریان گاز جدا می کنند. و توان جدا کردن ذرات کوچکتر را ندارند. به همین دلیل معمولاً آنها را بعد از شوینده های گاز (Gas Scrubbers) و قبل کمپرسورها قرار می دهند. تا ذرات بزرگ گردوغبار و رطوبتی که برای کمپرسورها و کارایی آنها مصر می باشند بر طرف گردند.
از لحاظ ساختمانی شبیه دیگر رطوبت گیرها می باشند. با این تفاوت که داخل آنها آب نیز پاشش می شود.
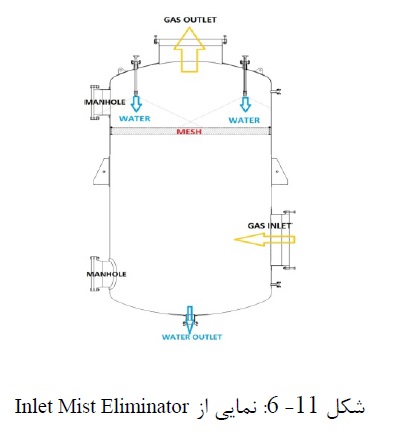
در فرایند احیاء چون کمپرسورهای گاز پروسس و گاز خنک کننده از نوع سانتریفیوژ می باشند. برای جلوگیری از ایجاد آسیب به آنها، از این نوع رطوبت گیر در ورودی کمپرسورها نصب می شود.
کولرها (Coolers)
از این تجهیزات جهت خنک کردن گاز استفاده می شود.
عملکرد کلی آنها به این شکل است که گاز از پایین وارد تجهیز میشود. و آب سرد از بالا توسط یکسری دوش روی گاز پاشش می شود. و گاز سرد میشود از قسمت بالای کولر خارج می شود. چون معمولاً گازی که برای خنک سازی به کولر ارسال می شود. یک گاز تمیز و یا با آلودگی کم است. آب خارج میشود و از کولرها بعد از خنک سازی پروسس آب تمیز بر می گردد.
انتقال مواد (material handeling)
برای بالا روی عملکرد این تجهیزات از عدل هایی شامل موادی از جنس استنلس استیل بکار می رود. که باعث افزایش سطح تماس گاز با آب میشود و در نتیجه دمای گاز بیشتر کاهش می یابد. عملکرد این عدلها به این این شکل است که آب از بالا روی این عدل ها پاشش می شود. و آنها را کاملاً خیس می نماید. سپس گاز از قسمت پایین وارد بسته ها میشود و دمایش کاهش می یابد.
در بعضی موارد نیاز است که گاز خروجی از کولر دارای رطوبت کمی باشد. (مثلاً خروجی کولر گاز عایق در پروس احیاء). در این موارد در قسمت خروجی گاز کولر از عدل های مش و یا پره جهت رطوبت گیری استفاده می شود.
در شکل 11-7 نمایی از این تجهیز نمایان و مشخص است.
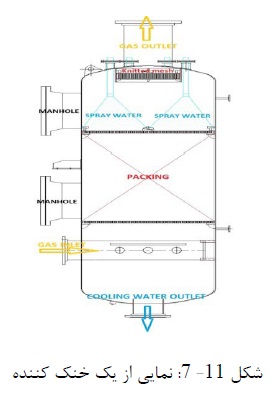
شستشو دهنده گازها (Gas Scrubbers)
غبارگیرهایی که از مایعات استفاده می کنند. به عنوان اسکرابر شناخته می شوند. در این سیستم ها مایع پاک کننده (معمولاً آب) وارد تماس با جریان گاز حاوی ذرات غبار می شود. افزایش سطح تماس گاز با مایع موجب افزایش راندمان جداسازی می شود.
دامنه گسترده ای از اسکرابر وجود دارد اما تمامی این سیستم ها از سه بخش اصلی تشکیل می شوند.
الف) رطوبت زن
فرایند رطوبت زنی موجب تجمع ذرات ریز و افزایش توده های بزرگتر خواهد شد. و جمع آوری غبارات را آسان تر می سازد.
ب) تماس مایع و گاز
این بخش از جمله مهم ترین مسائلی است که راندمان غبارگیری را تحت تأثیر قرار می دهد. ذرات و قطرات به وسیله چهار مکانیزم رایج در تماس با هم قرار می گیرند.
اول- جداسازی به کمک اینرسی
زمانی که قطرات در مسیر جریان هوای غبار آلود قرار می گیرند. جریان هوا شکافته میشود و دور قطرات جریان می یابد. به سبب وجود اینرسی، ذرات غبار بزرگ حرکت خود را در مسیر مستقیم ادامه خواهند داد. و یا قطرات آب برخورد کرده و به دام می افتند.
دوم-جداسازی به کمک حائل
انتقال مواد (material handeling)
ذرات غبار ریز به همراه جریان هوا عبور کرده و با قطرات آب به صورت مستقیم برخورد نمی کنند. اما با عبور از روی ذرات بزرگتر به آنها می چسبند.
سوم – جداسازی به کمک نفوذ
زمانی که قطرات آب در میان ذرات غبار دچار پراکندگی می شوند. ذرات غبار بر روی سطوح قطره به سبب وجود حرکت براونی و یا نفوذ ته نشین می شوند. این روش اساس فرآیند جمع آوری ذرات غبار با ابعاد پایین تر از میکرون است.
چهارم- جداسازی به کمک کندانس کردن
اگر جریان گاز عبور کننده در اسکرابر تا یک حد مشخص سرد شود. رطوبت بر روی ذرات غبار کندانس میشود. و باعث افزایش وزن و اندازه ذرات می گردد. که این امر منجر به سهولت در جمع آوری آنها خواهد شد.
ج) جداسازی مایع از گاز
بدون در نظرگیری روش تماس مورد بکار گیری، باید تا حد ممکن مایعات و غبارات موجدو جداسازی شوند. در ابتدا تماس به وقوع می پیوندد و ترکیب قطرات آب و غبارات به وجود می آید. با افزایش ابعاد، این ذرات در غبارگیر به سکون خواهند رسید. ذراتی که به حد کافی سنگین شدند. به پایین سقوط می کنند. برای جداسازی ذرات بزرگ تر به گاز حرکت چرخشی ایجاد می شود. قطرات آب و غبار در اثر نیروی گریز از مرکز، از گاز جدا شد و به بدنه اسکرابر برخورد نموده و سقوط می کنند. آب کثیف خارج میشود و از اسکرابر نیز یا پاکسازی میشود و تخلیه می شود و یا دوباره به اسکرابر باز گردانی میشود.

در بعضی از انواع اسکرابرها از یک رطوبت گیر پره ای و یا مش برای جذب ذرات رطوبت در خروجی بکارگیری می شود.
انتقال مواد (material handeling)


رطوبت گیری که در این نوع شوینده استفاده می شود. از نوع پره ای می باشد. که همزمان با چرخش آب رطوبت را از گاز می گیرد.
برای آغشتگی بهتر ذرات غبار با آب از عدلهایی (Packing) شامل موادی از جنس پلی پروپیلن بکارگیری می شود. آب روی این بسته ها ریخته می شود. و گاز از پایین وارد این بسته ها شده و با آب مخلوط می شود.
سیستم های غبارگیر (Dust Collection Systems)
غبارگیر سیستمی است که به منظور افزایش کیفیت هوای خارج شده. از پروسس های صنعتی و تجاری، از طریق جمع آوری غبارات و یا سایر آلوده کننده های محیطی. و از جریان هوا و یا گاز، مورد استفاده قرار می گیرد.
از این تجهیزات در صنایع چاپ و گاغذ، نساجی، چوب بری و نجاری، رنگ، شیمیایی. پتروشیمی، نفتی، کارخانه های احیاء اکسید آهن و صنایع فولاد سازی استفاده می شود.
غبارگیرها ار می توان به دو نوع کلی خشک و تر تقسیم نمود:
1- غبارگیر خشک (Bsg Filter):
این دستگاه در صنایع مختلف معدنی نظیر کاشی، چینی ، پودرهای میکرونیزه، صنایع سیمان، فولاد و… کاربرد دارد.
در این دستگاه غبار ایجاد شده از دستگاه های مختلف توسط هودها و کانال ها از منافذ غبارخیز جمع آوری. و به صورت شناور در بستر سیال عامل به سمت دستگاه غبارگیر منتقل می شوند. که این انتقال توسط یک دستگاه فن با ایجاد فشار منفی در داخل شبکه و دستگاه ها انجام می گیرد. سرعت انتقال در داخل کانالها تابع از خواص فیزیکی ذرات غبار می باشد. ولی محدوده مجاز طراحی بین 10-20 متر بر ثانیه در نظر می گیرند.
غبار به همراه هوا وارد محفظه اصلی دستگاه (اتاق کثیف) می گردد. و سپس از کیسه هایی که از جنس الیاف با خواص و دانسیته متفاوت تولید شدند. عبور کرده و غبار روی کیسه ها به جای می ماند. و هوایی که تصفیه میشود پس از عبور از محفظه تمیز وارد فن و از اگزوز خارج می گردد.
کیسه ها پس از مدت زمان خاصی توسط غبار پوشش خواهند شد. و در این زمان سنسور اختلاف فشار که اختلاف فشار هوا قبل و بعد از کیسه را کنترل می نماید. فرمان تمیز کاری را صادر می کند. سیستم تمیزکاری شامل یک دستگاه میکروکنترلر منبع هوای متراکم. شیرهای برقی جهت عبور هوای تمیزکاری، شبکه لوله های هوای متراکم و ونتوری های مربوطه می باشد. به این ترتیب وقتی که میزان افت فشار قبل و بعد از کیسه ها به مقدار مشخصی برسد.
میکروکنترلر فرمان باز شدن به شیر برقی را صادر می نماید. و شیر برقی در زمانی حدود 100 تا 250 هزارم ثانیه باز و هوای متراکم. با فشار 6 بار از طریق لوله ها به دهنه کیسه که ونتوری می باشد. هدایت می گردد که باعث ایجاد یک موج ضربه روی کیسه ها و تخلیه غبار کیسه ها می گردد.
این عمل آنقدر ادامه پیدا می کند. که اختلاف هد کیسه ها به میزان دلخواه برسد. و کیسه ها تمیز گردد. کیسه ها در این دستگاه معمولاً دارای ابعاد 120×2500 و 160×3000 و160×3500 میلی متر می باشند. که به صورت ردیفی در مجموعه 8 تایی و 12 تایی چینش می شوند. و هر ردیف را یک شیر برقی تغذیه می نماید.
محدوده مجاز سرعت تصفیه روی کیسه ها از 5/0 الی 5/4 متر بر دقیقه می باشد. که سرعت فوق بستگی به قطر ذره و خواص فیزیکی و میزان خورنده بودن ذره غبار دارد.
میزان افت فشار داخل دستگاه نیز تابعی از سرعت تصفیه جنس پارچه ها است. که در محدوده 100-250 میلی متر آب می باشد.
جرم غبار معلق در هر متر مکعب هوای قبل از فیلتر معادل 120 گرم در متر مکعب می باشد. که پس از تصفیه به 5 میلی گرم در یک متر مکعب می رسد.
در صورتی که جرم غبار بیش از مقدار فوق باشد. نیاز به استفاده از سیکلون قبل از فیلتر می باشد.
سرعت مجاز هوا در کانالهای ورودی دستگاه (شبکه غبارگیری) معمولاً بین 10 -m/s20 طراحی می گردد. که این نیز به دانسیته و سایز ذرات غبار بستگی دارد.
ظرفیت دستگاه معمولاً بر اساس متر مربع سطح فیلتراسیون بیان می گردد. که پارامتری که بیان شد تابعی از حجم هوای مکشی و میزان غبار موجود می باشد.
انتقال مواد (material handeling)

غبارگیر تر:
در دستگاه غبارگیر تر، غبار مکش شده توسط فن وارد قسمت ابتدایی دستگاه (ونتوری) می گردد. خود مجموعه ونتوری از سه قسمت اصلی ورودی، گلویی و خروجی تشکیل گردیده است.
هوای غبار آلوده در سطح گلویی سرعتی نزدیک به 70 تا 120 متر بر ثانیه پیدا خواهد کرد. و از طرف دیگر آب توسط نازل در گلویی نیز به روی غبار پاشش می گردد. آب در مقطع گلویی به دلیل فشار و سرعت بالا اتمایز می گردد. و ری ذرات غبار می نشیند. غبار خیس که در اثر آب پاشیده شده سنگین تر شده است. به صورت مماسی وارد محفظه اصلی دستگاه می گردد.
و پس از تماس با سطح، آب غبارها را در مخزن آب به جای می گذارد. و هوای تمیز که همراه با مقداری آب و غبارهای سوپر فاین (بسیار ریز) می باشد. به سمت بالا حرکت می نماید. که از آنجا وارد واحد سپراتور (جدا کننده) می گردد. که در این واحد هوا و غبار و آب در معرض یک میدان چرخش شدید قرار می گیرد. و غبار و آب به سمت جداره حرکت کرده و هوای تمیز از اگزوز خارج می گردد. میزان افت فشار در خود دستگاه با توجه به افزایش و یا کاهش سرعت در گلوگاه ونتوری متغیر می باشد. که در محدوده 200 تا 400 میلی متر آب متغیر می باشد.
سرعت در گلوگاه نیز تابعی از دانسیته و قطر ذرات غبار می باشد.
این دستگاه جهت تصفیه گاز محلول در آب نیز مورد استفاهد قرار می گیرد.

غبا
غبارگیرهای سیکلون دار:
سیکلون ها از مهمترین وسایلی هستند. که بر اساس خاصیت گریز از مرکز به جمع آوری ذرات می پردازند. مکانیزم آنها یکی از مؤثرتین روش های جداسازی و جمع آوری ذرات درشت محسوب شده. و به همین دلیل در مقیاس صنعتی به طور وسیعی در سیستم های کنترل ذرات مورد استفاده قرار می گیرند.
انتقال مواد (material handeling)
سیکلون مخروط ناقص فلزی یا پلاستیکی وارونه ای است. که هوا حاوی ذرات از روزنه ای در جدار آن وارد شده و پس از حرکت مارپیچ به طرف پایین. سرانجام بواسطه تغییر مسیر در انتهای سیکلون از قسمت بالای آن خارج می شود. هنگام چرخش هوا در سیکلون، ذرات درشت (غیر قابل استنشاق) به دلیل نیروی گریز از مرکز. از جریان هوا جدا شده و در قسمت پایین وسیله جمع می شوند.
ریزتر (قابل استنشاق) نیز همراه جریان هوا به طرف مجرای خروجی حرکت کرده. و در صورت قرار دادن فیلتر در مسیر جریان هوا، بر روی فیلتر بدام می افتند. از مزایای این وسیله می توان به قیمت مناسب، سهولت استفاده. بی نیازی به مواد خاص و عدم احتمال ورود مجدد ذرات به جریان هوا اشاره کرد.
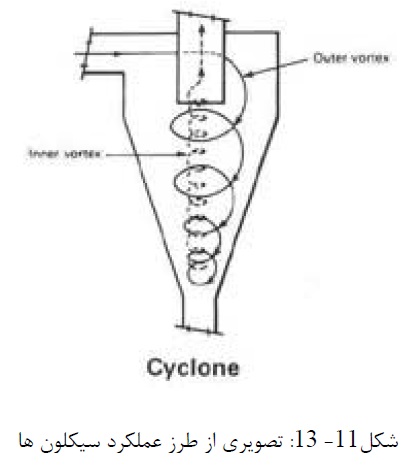
عموماً از این تجهیز در موارد ذیل در ورودی غبارگیرها استفاده می شود.
1- در مواقعی که بار غبار هوای ورودی به فیلترهای کیسه ای بیش از ظرفیت آنها باشد. قبل از غبارگیر کیسه ای از سیکلون برای کاهش بار غبار استفاده می شود.
انتقال مواد (material handeling)
2- زمانی که ذرات معلق در هوا دارای جرم حجمی بالا باشند.
3- در مواقعی که ذرات معلق درشت باشند.
غبارگیرهای سیکلونی بیشتر قابلیت جذب ذراتی را دارند که ابعاد آنها حداقل 20 میکرون باشد. و ذرات کوچکتر معمولاً همراه هوای خروجی از سیکلون خارج می شود. در شرایط معمولی راندمان سیکلون ها حدود اً 85% می باشد. که بستگی به شرایط مختلفی از جمله میزان و ابعاد ذرات معلق، سرعت هوا و ابعاد و طرح سیکلون دارد. در مواردی که حجم هوای مورد تصفیه بالا باشد. جهت افزایش دبی هوای عبوری از غبارگیر، بدون اینکه فشار افت زیادی داشته باشد. از چند سیکلون بصورت موازی استفاده میشود.
افت فشار در این دستگاه ها حدوداً 80 الی 150 میلی متر آب می باشد. که بستگی به نوع سیکلون و سرعت تصفیه در سطح مقطع سیکلون دارد.
سرعت تصفیه در سطح مقطع (مؤلفه عمودی جریان هوا) معمولاً بین 2 تا 5/4 متر بر ثانیه انتخاب می گردد. افزایش این مؤلفه با افزایش راندمان و افت بیشتر فشار همراه است.
سرعت جریان هوا در داخل سیکلون که برابر با سرعت ورودی آن فرض می شود. معمولاً بین 20 الی 25 متر بر ثانیه انتخاب می گردد. افزایش این سرعت به بیش از 30 متر بر ثانیه. و یا کاهش آن به کمتر از 15 متر بر ثانیه باعث افت قابل ملاحظه راندمان می گردد.
غبارگیری که در فرآیند احیاء اکسید آهن به روش پرد مورد استفاده قرار می گیرد. از نوع مرطوب و دارای سیکلون در ورودی آن می باشد.
هوای غبار آلوده از قسمت های مختلف مثل خروجی کوره، مخزن ذخیره روزانه. مخازن ذخیره محصول و محل استقرار غربالها، توسط هود جمع آوری شده و برای غبار زدایی وارد غبار گیرها می شوند. و از پایین سیکلون، جهت بارگیری به درون یک مخزن (Dust Bin) می ریزند. هوا از بالای سیکلون توسط داکت های رابط به درون یک ونتوری وارد می شود. آب توسط نازل های تعبیه شده در ونتوری طی دو مرحله متفاوت بر روی هوا پاشیده می شود. شایان ذکر است که آب مصرفی از پروسس آب گرم می باشد. که این خود یک صرفه جویی و کاهش مصرف آب تمیز در روش پرد به شمار می آید.
هوای مرطوب پس از خروج از ونتوری وارد یک اسکرابر می شود. و در اثر حرکت چرخشی، ذرات غبار همراه با آب از هوا جدا میشود. و هوای تمیز از بالای اسکرابر خارج می گردد. که توسط یک فن از طریق دودکش به هوای آزاد ارسال می شود.
آب خروجی از اسکرابر درون یک حوضچه ریخته و توسط پمپ هایی به کلاریفایر فرستاده می شود.
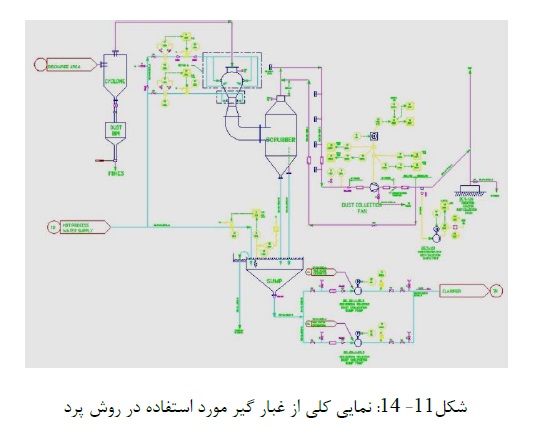
خشک کن ها (Dryers)
همانطور که قبلاً در قسمت رطوبت گیرها نیز ذکر گردید. وجود آب در سیکل گازی باعث بروز مشکلات زیادی برای کیفیت و میزان تولید (کاهش راندمان) و همچنین کاهش عمر تجهیزات مربوط می گردد.
در بعضی مواقع لازم است که از رطوبت و بخار موجود در گاز. بخاطر حساسیت بالای موضوع، تا میزان قابل توجهی کم شود. (برای مثال در فرآیند احیاء مستقیم آهن، در گاز عایق (Seal Gas) که در ارتباط با محصول می باشد. و برای جلوگیری از اکسید شدن دوباره محصول لازم است گاز بطور قابل قبولی آب زدایی گردد.)
انتقال مواد (material handeling)
برای این منظور باید گاز را آب زدایی نمود.
روش های مختلف فرایند آب زدایی گاز عبارتند از:
- روش جذب در مایع بوسیله مایعات نمگیر
- روش جذب جامد بوسیله جامدات نمگیر
- میعان بوسیله فشرده کردن یا سرد کردن گاز
انتخاب روش اب زدایی بستگی به شرایط گاز (اجزای تشکیل دهنده، فشار، دما و دبی) و میازن آب زدایی دارد. مقدار آب موجود در گاز را می توان با نقطه شبنم گاز در فشار و دمای مورد نظر مشخص کرد.
1- آب زدایی به روش جذب در مایع
جذب توسط حلال، رایج ترین فرآیندی است که به منظور آب زدایی گاز طبیعی در صنعت بکار می رود. در حالت کلی در یک فرایند جذب، گازی که باید فرآوردی شود. در یک برج سینی دار یا پر میشود با حلالی که خاصیت جذب انتخابی دارد. به طور غیر همسو در تماس قرار می گیرد. اگر حلالی که از بالای برج وارد آن می شود، خالص باشد. مقدار گردش حلال و تعداد سینی ها و یا ارتفاع پرکن ها را در برج می توان به گونه ای تنظیم کرد.
تا میزان خلوص گاز در هنگام خروج از برج، منطبق با معیارهای مشخص شده باشد. حلالی که از برج جذب خارج می شود. جهت بازیابی به یک ستون تقطیر که اغلب در فشار پایینتری نسبت به برج قبلی عمل می کند، ارسال می شود. پس از بازیابی، حلال دوباره به سمت برج جذب برگردانده می شود.
برخی مایعات قابلیت جذب آب از گاز را دارا می باشند. اما تعداد کمی از آنها از نظر اقتصادی مناسب هستند. به طور کلی حلالی برای آب زدایی مناسب است. که دارای خصوصیات زیر باشد.
گرایش شدید نسبت به آب
قیمت کم
غیر خورنده
گرایش کم نسبت به هیدروکربن ها و گازهای اسیدی
انتقال مواد (material handeling)
پایداری حرارتی
بازیافت آسان
گرانروی پایین
فشار بخار پایین در دمای تماس
حلالیت کم در هیدروکربن ها
تمایل کم برای تشکیل کف و معلق شدن
جهت نم زدایی، هر یک از محلول های زیر می توانند مورد استفاده قرار گیرند:
کلسیم کلراید
انتقال مواد (material handeling)
لیتیم کلراید
متانول
اتیلن گلایکول با علامت اختصاری EG و فرمل شیمیایی H6O2 C2
دی اتیلن گلایکول با علامت اختصاری DEG و فرمول شیمیایی H10O3 C4
تری اتیلن گلایکول با علامت اختصاری TEG و فرمول شیمیایی H14O4 C6
2- روش جذب جامد به وسیله جامدات نمک گیر
در این روش علاوه بر بخار آب ناخالصیهای دیگر نیز توسط مواد جاذب جدا می شوند. مکانیزم جذب به سه طریق انجام میشود.
جذب سطحی
ایجاد اب هیدارته با مواد جامد
واکنش شیمیایی با جامد
روش جذب سطحی بیشترین کاربرد را برای آبگیری در پالایش گاز دارد.
به طور کلی یک ماده جاذب باید دارای خصوصیات زیر باشد:
دارای سطح زیاد بر واحد وزن باشد.
نسبت به اجزاء قابل جذب، فعال باشد.
میزان انتقال جرم در آن زیاد باشد.
احیاء آن آسان بوده و از نظر اقتصادی مقرون به صرفه باشد.
مدت قابل ملاحظه ای مواد جذب شده را در خود نگه دارد.
در مقابل جریان گاز مقاومت کم ایجاد کند.
خرد نشده و به صورت پودر در نیاید.
ارزان، غیر خورنده و غیر سمی باشد. و ترکیب شیمیایی ایجاد نکند.
تغییر حجم قابل ملاحظه در موقع جذب و احیاء ایجاد ننماید.
در اثر مرطوب شدن مقاومت آن کم نشود.
هر گرم از مواد جاذبی که کاربرد صنعتی دارند. سطحی در حدود 500 تا 600 مترمربع ایجاد می کنند. چنین سطحی در صورتی امکان پذیر است. که جسم به علت موئینگی دارای سطح داخلی زیاد باشد. و یا کریستالی در جسم بوجود آید.
متداولترین و مناسب ترین مواد جاذب که در صنعت کاربرد دارند عبارتند از:
بوکسیت (Al2O3) که به طور طبیعی یافت می شود.
آلومینا که عبارت است از Al2O3 فعال شده که بوکسیت تهیه می شود.
سیلیکاژل که قسمت اعظم آن شامل Al2O3 و SiO3 است. به طور طبیعی یافت می شود.
غربالهای مولکولی که شامل سیلیکات کلسیم و سدیم و آلومینیم است.
کربن فعال
در شکل 11-15 سک خشک کن با روش جذب جامد نمایان و معلوم است.
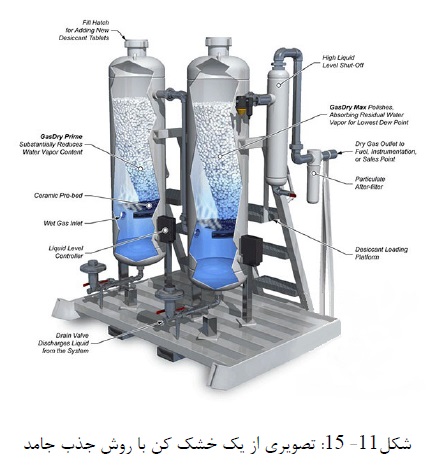
3-میعان بوسیله خشک کردن یا سرد کردن گاز (Refrigeration Compressed Gas Dryer)
در این نوع خشک کن از یک سیل تبریدی برای آب زدایی استفاده می شود.
عملکرد آنها به این صورت است که گاز مرطوب برای خشک شدن. در یک مبدل حرارتی در مجاورت گازی که در یک سیکل تبریدی سرد میشود، قرار می گیرد. بخار آب موجود در گاز با سرد شدن گاز و رسیدن به نقطه شبنم، بصورت قطرات آب تقطیر می شود. هر چه درجه حرارت سرمایش پایین تر آید (تقطیر در دمای پایین تری انجام گیرد)، گاز بیشتر خشک می شود.
انتقال مواد (material handeling)
گاز بعد از سرد شدن وارد یک مخزن جدایش رطوبت می شود. در آنجا آب تقطیر شده جدا می شود.
از گاز خشک خروجی که دارای دمای پایینی است. برای پایین آوردن دمای گاز مرطوب ورودی استفاده می شود. این عمل باعث بالا روی راندمان می شود.
شکل 11-16 اجزاء و چگونگی عملکرد خشکن های تبریدی را نشان می دهد.
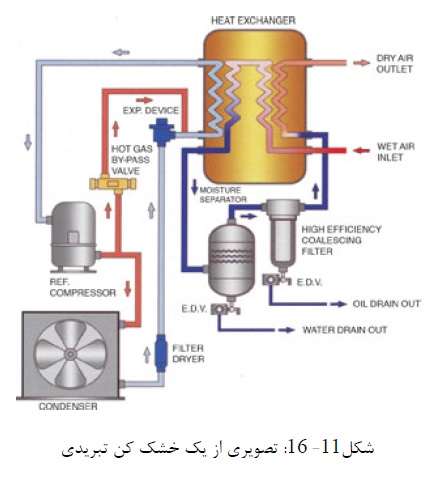
خشک کن هایی که در احیاء مستقیم به روش پرد برای خشک کردن گاز آب بندی (Seal Gas) استفاده می شوند. از نوع جذب در جامد و برای خشک نمودن گاز پاک کننده (Purge Gas) از نوع تبریدی می باشند.
کمپرسورها
کمپرسورها دستگاهی است که برای بالا بردن فشار گاز و یا انتقال آن از نقطه ای به نقطه دیگر. در طول پروسس به کارگیری می شود. در واقع کمپرسور با افزایش سرعت گاز و تبدیل آن به فشار، جریان گاز را در سیستم راحت تر می کند. البته افزایش فشار در نوعی از کمپرسورها به وسیله کاهش حجم صورت می گیرد.
انتقال مواد (material handeling)
آنچه که در کمپرسورها حائز اهمیت است، نسبت فشار خروجی به ورودی کمپرسور می باشد. در کمپرسورها با افزایش فشار، دمای گاز نیز بالا می رود. و این امر باعث ایجاد اختلال در کار قطعات مختلف آن و سیستم روغن کاری می شود.
برای خنک کاری کمپرسورها می شود از یک سیکل بسته سیال سرد (مثل آب) و یا جریان هوا به کار گیری نمود.
همانطور که ذکر شد در کمپرسورها افزایش فشار به دو صورت انجام می گیرد. بر حسب این مورد دو نوع اساسی کمپرسور نیز وجود دارد که عبارتند از:
کمپرسورهای دینامیکی که فشار گاز را با زیاد کردن سرعت آن و سپس، گرفتن سرعت گاز افزایش می دهند.
کمپرسورهای جابجایی مثبت که با کاهش حجم گاز، فشار آن را افزایش می دهند.
البته هر کدام از این کمپرسورها به حسب شکل ساختمانی و نحوه عملکرد، تقسیم بندی می شوند. که در زیر به طور خلاصه بیان میشود.
1- کمپرسورهای دینامیک Compressors Dynamic
سانتریفیوژ Centrifugal Compressor
جریان محوری Axial Flow Compressor
2- کمپرسورهای جابجایی مثبت Positive Displacement Compressor
رفت و برگشتی Reciprocating
دورانی Rotary Compressor
از بین کمپرسورهای نامبرده، کمپرسورهای رفت و برگشتی، سانتریفوژ و جریان محوری بیشتر از سایر کمپرسورها مورد استفاده قرار می گیرند.
کمپرسورهای رفت و برگشتی Recipricating Compressor
این کمپرسورها را می توان به هر اندازه که مورد احتیاج باشد. ساخت در نوع یک مرحله ای آنها، با حرکت رفت پیستون فشار گاز از مکش تا خروجی بالا می رود. اساس کار این کمپرسورها حرکت یک پیستون داخل یک سیلندر است. که با کاهش حجم گاز، فشار آن را بالا می برند.

کمپرسورهای رفت و برگشتی یک مرحله ای را بیشتر برای فشار بین 100 تا 150 Psig به کار می برند. از کمپرسورهای دو یا چند مرحله ای زمانی استفاده می شود. که فشار خیلی بالا (مثلاً 100 Psig) مورد احتیاج باشد. اما با توجه به افزایش درجه حرارت گاز به هنگام و حالت متراکم. در کمپرسورهای چند مرحله ای، بعد از هر مرحله از یک خنک کننده استفاده می شود. تا درجه حرارت گاز را برای مرحله بعدی پایین بیاورد. چون حرکت گاز در خروجی این کمپرسورها به طور یکنواخت صورت نمی گیرد. در هر حرکت رفت پیستون، به خروجی کمپرسور ضرباتی وارد می گردد. برای جلوگیر از این ضربات و یکنواخت کردن جریان تدابیر مختلفی به کار می رود که مهمترین انها عبارتند از:
در ضربه ای کردن پیستون، یعنی اینکه پیستون هم در حرکت رفت و هم در حرکت برگشت مقداری گاز متراکم به خروجی مشترکی وارد نماید.
به کار بردن ضربه گیر یا خفه کن: (Pulsation Damper)
ضربه گیر مخزنی است که به طور وارونه در خروجی کمپرسور (اگر چند مرحله ای باشد در خروجی هر مرحله یک ضربه گیر). کار گذاشته می شود. اساس کار ضربه گیر بر پایه انبساط و انقباض گازی که وارد آن میشود استوار است. یعنی اینکه در حرکت رفت پیستون گاز درون ضربه گیر متراکم می شود. و در حرکت برگشت پیستون به علت افت فشار در خروجی کمپرسور. گاز منقبض شده درون ضربه گیر، منبسط شده، از آن خارج شدن وارد لوله خروجی کمپرسور می شود.
مزایای کمپرسورهای رفت و برگشتی:
هنگامی که احتمال تغییر وزن مولکولی گاز ورودی به تأسیسات وجود دارد. از این کمپرسورها استفاده می شود. به این علت که در این کمپرسرها عمل تراکم حساسیت زیادی به وزن مولکول ندارد. این کمپرسورها در مورد گازهای همراه با نفت (Associate Gas)، مناسب می باشند. این کمپرسورها راندمان بالاتری نسبت به کمپرسورهای سانتریفوز دارند. اما دارای سرعت کمتری نسبت به سایر کمپرسورها هستند. لذا بدون احتیاج به جعبه دنده به طور مستقیم می توانند به موتور الکتریکی متصل گردند. برای شروع حرکت نسبت به سایر انواع کمپرسورها توان کمتری لازم دارند. همچنین زمانی که میزان گاز کم باشد. نسبت به انواع دیگر ارجح هستند.
کمپرسورهای سانتریفوژ Centrifugal Compressor
در این کمپرسورها افزایش فشار گاز بر اثر افزایش سرعت آن صورت می گیرد. به این صورت که سرعت گاز بر اثر حرکت پروانه (Impeller) زیاد شده. پس از آن سرعت گاز با برخورد با پخش کننده ها کاهش پیدا می کند. و در عوض فشارش بالا می رود.
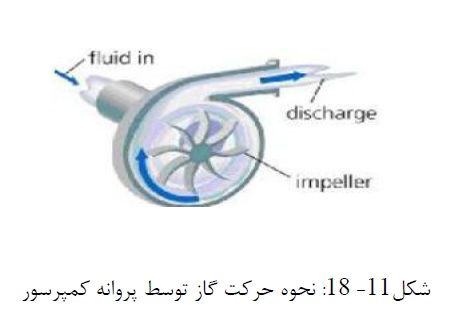
کمپرسورهای سانتریفوژ تشکیل شده اند از یک پروانه که داخل پوسته ای می چرخد. اساس کار این کمپرسورها بر پایه نیروی گریز از مرکز طراحی شده است. در کمپرسورهای سانتریفوژ فاصله بین پوسته و پروانه خیلی کم است. بنابراین جنس محور کمپرسور باید از فلز یا آلیاژی باشد. که در دورهای بالا حداقل انحنا را داشته باشد.
تا پروانه با پوسته تماس پیدا نکند. همچنین گاز ورودی به کمپرسور باید کاملاً خشک باشد. و هیچ مایعی به همراه نداشته باشد. برای همین، قبل از هر کمپرسور یک مخزن آبگیر (Knock Drum Out) قرار می دهند. تا اگر احیاناً قطرات مایعی در گاز موجود است. توسط این مخازن گرفته شود. چون قطرات مایع به پره های کمپرسور ضربه وارد کرده و آسیب می رساند.
اگر فشار خیلی بالا مد نظر باشد. باید از کمپرسورهای سانتریفوژ چند مرحله ای استفاده کرد به خاطر اینکه با افزایش فشار گاز دمای آن نیز زیاد می شود. و این افزایش دما اگر از حد معینی بیشتر شود. باعث آسیب رسانی به قطعات کمپرسور و اختلال در سیستم می شود. همچنین ممکن است با افزایش فشار، قسمتی از گاز تبدیل به مایع شود. و در این قطرات مایع ایجاد میشود و گاز باعث از بین بردن پره های کمپرسور می شود.
به دلایل مورد بیان از کمپرسورهای چند مرحله ای بکارگیری می شود. و به این ترتیب که پس از هر مرحله فشردگی، گاز را خنک کرده و مایع احتمالی در آن را توسط Intercooler. به وسیله مخازنی در بین راه گرفته سپس گاز خشک (بدون مایع) و خشک شده را به مرحله دوم می فرستند. و به این ترتیب می توان پس از چند مرحله فشردن به فشار نسبتاً بالایی دست یافت.
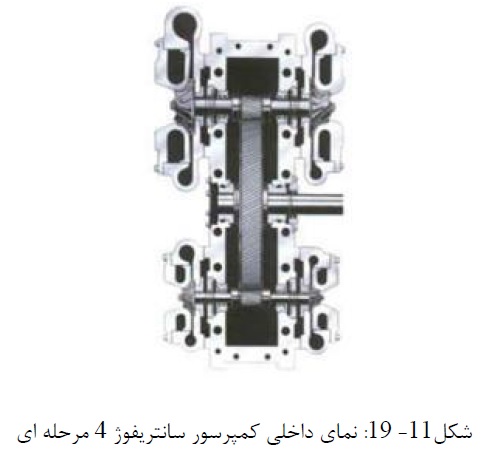
مزایای کمپرسورهای سانتریفوژ
کمپرسورهای سانتریفوژ نیاز به تعمیر کمتری دارند. و می توانند مدت زیادی را بدون وقفه در سیستم کار کنند. علاوه بر آن، این کمپرسورها اندازه کوچکتری نسبت به کمپرسورهای رفت و برگشتی دارند.
زیرسازی کمپرسورهای سانتریفوژ کوچکتر از انواع دیگر است. و نیاز به آب یا روغن خنک کننده ندارد. چون به طور کلی محفظه این نوع کمپرسورها با هوا خنک می شود.
انتقال مواد (material handeling)
جریان خروجی از این نوع کمپرسورها یکنواخت است. و ضربه ای به بخش تخلیه کمپرسور وارد نمی کند. مزیت دیگری که این نوع کمپرسورها دارند این است که استهلاک کمتری نسبت به انواع دیگر دارند. و این به خاطر کم بودن قطعات متحرک این کمپرسور است.
معایب کمپرسورهای سانتریفوژ
کار کرد این کمپرسورها وابستگی شدید به وزن مخصوص، جرم مولکولی و نسبت Cp/Cv گاز ورودی دارد. کاهش وزن مخصوص و وزن مولکولی گاز باعث افزایش توان مصرفی کمپرسور خواهد شد. همچنین متراکم کردن گازهای با وزن مولکولی کم باعث افزایش تعداد مراحل در این کمپرسورها می شود.
با وجود مزایایی که کمپرسورهای سانتریفوژی نسبت به کمپرسورهای رفت و برگشتی دارند، دارای راندمان کمتری نسبت به آنها هستند. موتورهای محرک کمپرسورها به دو صورت الکتریکی و توربینی است. اما با توجه به سرعت زیاد کمپرسورهای سانتریفوژی اگر برای این نوع کمپرسورها از موتورهای الکتریکی استفاده شود.
برای تغییر سرعت دوران برای گازهای متفاوت نیاز به جعبه دنده می باشد. که این امر احتمال لرزش و ارتعاش را بالا می برد. و باعث افزایش هزینه های تعمیرات و استهلاک خواهد شد. در نتیجه کنترل جریان در این کمپرسورها با سهولت کمتری انجام می شود.
کمپرسورهای جریان محوری Axial Flow Compressor
این کمپرسورها نیز مانند کمپرسورهای سانتریفوژ یک قسمت چرخان (Rotor) دارند. که سرعت سیال را بالا می برد. اما بر خلاف کمپرسورهای سانتریفوژ که جریان به صورت شعاعی می باشد. جریان به صورت موازی با محور کمپرسور حرکت می کند. ساختمان این نوع کمپرسورها به صورتی است.
انتقال مواد (material handeling)
که نصف فشار گاز در قسمت جریان (Rotor) و نصف دیگر در قسمت ثابت (Stator) تولید می شود. پره های ثابت شده. بر محور چرخان به ترتیب از قسمت مکش تا خروجی کمپرسور کوچکتر میشود. و باعث بالا رفتن فشار ساکن (Pressure Static) و انرژی جنبشی (Kinetic Energy) گاز می شود. سیستم روغن زنی و سیستم کنترل جریان در سرعت های مختلف در این کمپرسورها دقیقاً شبیه کمپرسورهای سانتریفوژ است.
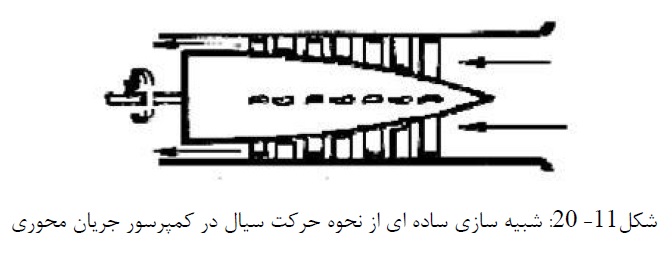
مزایای کمپرسور جریان محوری:
این نوع کمپرسورها اخیراً مصرف صنعتی زیادی پیدا کرده. و برای حجم های خیلی بالا حتی تا 860000 فوت مکعب در دقیقه مناسب ترین کمپرسور می باشد. در مقام مقایسه با کمپرسورهای سانتریفوژ برای فشردگی یک حجم معین گاز قطر چرخان (Rotor) کمپرسور جریان محوری نصف قطر پروانه کمپرسور سانتریفوژ خواهد بود. اگر کمپرسور جریان محوری خوب طراحی و تولید شود. سرعت گاز می تواند ft/s 400 در خروجی برسد.
انتقال مواد (material handeling)
هزینه اولیه تولید یک کمپرسور جریان محوری با هزینه اولیه تولید یک کمپرسور سانتریفوژ برای انجام کار معین برابر است. ولی هزینه نیروی محرکه کمپرسور جریان محوری کمتر از هزینه نیروی محرکه کمپرسور سانتریفوژ می باشد. یعنی اینکه برای یک کار معین، کمپرسور جریان محوری توربین یا موتور برقی کوچکتری نیاز دارد. که این خود باعث کم شدن هزینه های بعدی می گردد.
معایب کمپرسور جریان محوری:
اگرچه این کمپرسورها برای جریانهای بالاتری نسبت به کمپرسورهای سانتریفوژ استفاده می شود. اما ارتفاع ارسال گاز در این کمپرسورها خیلی پایین است. و تقریباً کمتر از نصف کمپرسورهای سانتریفوژ می باشد. که به معنی این است که فشار خروجی در این نوع کمپرسورها خیلی کمتر از کمپرسورهای سانتریفوژ است.
مثلاً برای رسیدن به فشار psig 65 در دوازده مرحله فشرده کردن گاز نیاز است. که این خود باعث افزایش حجم اشغال شده توسط کمپرسور و سایر هزینه ها می شد. با توجه به موارد ذکر شده نتیجه می شود. این کمپرسورها راندمان کمتری نسبت به کمپرسورهای سانتریفوژ دارند.
پمپ ها
پمپ وسیله ای مکانیکی برای انتقال مایعات است. که با افزایش فشار جریان آن، امکان جا به جایی مایعات را به ارتفاعی بالاتر (با افزایش هد). یا حتی پایین دست (معمولاً حوضچه یا مخزن) فراهم می آورد.
به طور کلی پمپ دستگاهی است. که انرژی مکانیکی را از یک منبع خارجی اخذ و به سیال مایعی که از آن عبور می کند، انتقال می دهد. در نتیجه انرژی سیال پس از خروج از این دستگاه (پمپ) افزایش می یابد. از پمپ ها برای انتقال سیال به یک ارتفاع معین. و یا جا به جایی آن در یک سیستم لوله کشی و یا هیدرولیک استفاده می نمایند.
به عبارت کلی تر از پمپ برای انتقال سیال از یک نقطه به نقطه دیگر استفاده می کنند. پمپ ها دارای انواع مختلفی هستند. که هر کدام دارای کاربرد خاصی می باشند. مهم ترین پمپ هایی که مورد استفاده قرار می گیرند عبارتند از:
1- پمپ های سانتریفوژ
2- پمپ های رفت و برگشتی
3- و پمپ های چرخ دنده ای
پمپ های سانتریفوژ
این پمپ ها از نوعی می باشند. که انتقال انرژی از آنها به سیال به طور دائمی انجام می پذیرد. پمپ های سانتریفوژ معمولاً نیروی محرکه خود را از طریق یک الکتروموتور (موتور الکتریکی) دریافت می کنند. انتقال نیروی محرکه از موتور به پمپ از طریق یک محور به نام شفت منتقل می شود. شفت موتور به وسیله نوعی تجهیزات مکانیکی به نام کوپلینگ به شفت پمپ متصل است. به این ترتیب انتقال نیرو به راحتی از طریق شفت موتور الکتریکی به شفت پمپ منتقل می گردد.
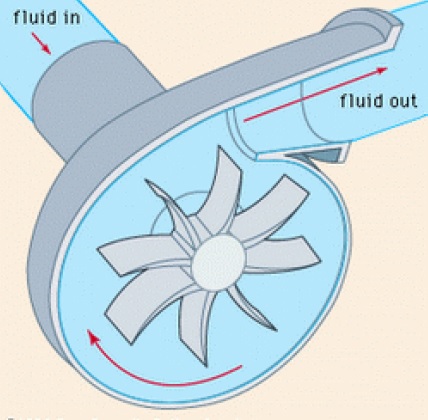
پمپ های سانتریفوژ دارای یک محفظه هستند. که حلزونی شکل است. و پوسته (Casting) معروف است. و درون آن یک یا چند چرخ قرار دارند. که روی یک محور (شفت) نصب شده اند. هر چرخ مجهز به تعدادی پره می باشد. انتقال انرژی به سیال در این قسمت انجام می شود. برای اینکه از محل خروج شفت از کیسینگ پمپ سیالی خارج نشود. و اصطلاحاً نشتی به خارج نداشته باشیم. از ابزاری به نام مکانیکال سیل استفاده شده است. نکته بسیار مهم در مورد این نوع پمپ ها هواگیری یا پرایم کردن پمپ پیش از روشن کردن آنها می باشد. یعنی پس از لاین آب نمدن پمپ اطمینان حاصل نمود. از این نوع پمپ ها در ابعاد و اندازه های مختلف برای مصارف گوناگون تولید می شوند.
پمپ های رفت و برگشتی:
این نوع پمپ ها وسایلی هستند. که انتقال انرژی از آنها به سیال به صورت پریودیک و دوره ای می باشد. نیروی محرکه این نوع پمپ ها نیز غالباً توسط موتورهای الکتریکی تأمین می گردد. در این نوع پمپ ها حرکت چرخشی میل لنگ تبدیل به حرکت رفت و آمدی پیستونی در یک سیلندر می شود.
با عقب رفتن پیستون در سیلندر ایجاد مکش میشود و در نتیجه مایع از طریق یک شیر ورودی داخل سیلندر می گردد. با حرکت پیستون به طرف جلو دریچه ورودی بسته. و مایع از طریق شیر خروجی به خارج هدایت می گردد. شیرهای ورودی و خروجی یک طرفه هستند و طوری تولید میشوند. که در مراحل رفت و آمد پیستون، از ورود مایع داخل سیلندر به قسمت کم فشار و بالعکس ممانعت شود. اگر به جای پیستون، پلانجری در داخل سیلندر رفت و آمد کند.
در این حالت به آن پمپ پلانجری می گویند. در ضمن چنانچه پلانجر دیافراگمی را حرکت دهد. پمپ از نوع دیافراگمی است. فرق میان پیستون و پلانجر در این است که طول سر پیستون کوتاه تر از مسافتی است که پیستون درون سیلندر طی می نمایند. در حالی که طول پلانجر بیشتر از طول مسافتی که طی میشود توسط آن در داخل سیلندر می باشد. از طرفی در پمپ های پیستون از حلقه یا رینگی جهت آب بندی پیستون و سیلندر بکاری گیری میشود. که روی بدنه پیستون قرار میگیرد و همراه آن حرکت می کند.
در حالی که در پمپ های پلانجری این رینگ روی سیلندر قرار دارد، و ثابت است. این پمپ ها معمولاً کم ظرفیت هستند ولی فشار خروجی سیال را می توانند تا مقدار زیادی افزایش دهند. بنابراین از این پمپ ها در جاهایی که. نیاز به جا به جا کردن سیالی با حجم کم ولی فشار بالا می باشد، استفاده می کنند. در ضمن باید به این نکته نیز توجه داشت. که جریان سیال در این پمپ ها به صورت غیر یکنواخت می باشد. نکته بسیار مهم در مورد این پمپ ها آن است. که هرگز نباید آنها را در حالی که شیر خروجی پمپ بسته است روشن نمود.
پمپ های چرخ دنده ای:
این پمپ ها نوعی از پمپ های گردشی یا روتاری می باشند. پمپ های چرخ دنده ای از دو قسمت متمایز تشکیل میشوند. یکی قسمت جداره ثابت و دیگری قسمت دوار که شامل یک محور گردان با چرخ دنده می باشد. در پمپ های چرخ دنده ای مقداری مایع بین دنده های چرخ دنده پمپ به اصطلاح به تله می افتد. و در اثر چرخیدن چرخ دنده ها این مایع به قسمت خروجی پمپ رانده می شود.
این پمپ ها به گونه ای تولید می شوند. که در آنها فاصله میان اجزاء گردنده و جداره ثابت بسیار کم می باشد. کاربرد این پمپ ها برای جا به جایی مایع یا حجم کم و فشار متوسط می باشد. نکته مهم در مورد این پمپ ها آن است که هرگز نباید آنها را در حالی که شیر خروجی پمپ بسته است روشن نمود. چرا که در این حالت، اگر هیچ شیر اطمینانی در مسیر تخلیه پمپ وجود نداشته باشد. یا خود پمپ از بین می رود و یا اینکه لوله تخلیه می شکند.
انتقال مواد (material handeling)
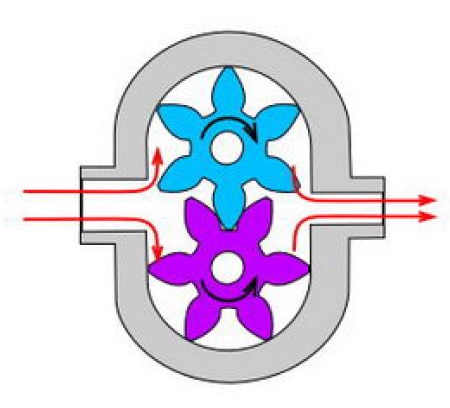
می توان پمپ ها را بر اساس نحوه عملکردشان به گونه ای دیگر نیز دسته بندی کرد:
- پمپ های سانتریفوژ (جریان شعاعی)
- پمپ های محوری
- پمپ های نیمه سانتریفوژ (یا با جریان مختلط)
1- پمپ های سانتریفوژ (شعاعی):
عملکرد این پمپ به این صورت است که در آن سیال موازی محور وارد چرخ پمپ میشود. و عمود بر آن از چرخ خارج می گردد. این پمپ ها معمولاً برای ایجاد فشارهای بالا در دبی های کم به کار می روند. بنابراین اغلب پمپ های سانتریفوژ توانایی خوبی در ایجاد فشارهای بالا دارند. پمپ های سانتریفوژ شایع ترین نمونه از پمپ ها هستند.
2- پمپ های محوری:
سیال موازی محور وارد پمپ می گردد و به طور موازی نسبت به محور از چرخ خارج می گردد. این پمپ ها برای ایجاد فشارها و دبی های متوسط به کار می روند.
3-پمپ های نیمه سانتریفوژ (مختلط):
سیال موازی محور وارد چرخ پمپ می گردد و به طور مایل نسبت به محور از چرخ خارج می گردد. این پمپ ها برای ایجاد فشارها و دبی های متوسط به کار می روند. این پمپ ها نسبت به پمپ های سانتریفوژ توانایی بیشتری در استفاده و به کارگیری دبی های بالا را دارند.
مبانی و کاربرد پمپ های گریز از مرکز (Centrifugal Pump):
اصول کار کلیه این پمپ ها بر اساس استفاده از نیروی “گریز از مرکز” پایه گذاری میشوند. هر حجمی که در یک مسیر دایره ای یا منحنی شکل حرکت کند. تحت تأثیر نیروی گریز از مرکز واقع می شود. جهت نیروی مذکور طوری است. که همواره تمایل دارد که جسم را از محور یا مرکز دوران دور سازد.
قسمت های اساسی یک پمپ گریز از مرکز عبارتند از:
الکتروموتور: که شامل قسمت الکتریکی پمپ است.
کوپل یا هم محور سازی: که متصل کننده الکترومتر به شافت (محور) پمپ است.
انتقال مواد (material handeling)
هوس برینگ: که محل قرارگیری برینگ ها می باشد.
مکانیکال سیل: که محل آب بندی پمپ و جدا کننده سیال پمپاژ میشود و قسمت مکانیکی پمپ می باشد.
پره های پمپ: که با توجه به نوع کاربرد دارای انواع مختلفی می باشد.
مواد:
پمپ های سانتریفیوژ که معمولاً به بازار عرضه می شوند . دارای ترکیبات برنزی، تمام برنزی، یا دارای ترکیب آهنی می باشند. در ساختار نیمه برنزی، پروانه خلاف شافت (اگر به کار برده شده باشد). و رینگ های سایشی برنزی خواد بود. و محفظه از چدن است. این مواد ساختمانی برای قسمت های از پمپ می باشد. که در تماس با پمپاژ شده می باشد.
کاویتاسیون:
این پدیده یکی از خطرناک ترین حالت هایی است. که ممکن است برای یک پمپ به وجود آید. آب یا هر مایع دیگری، در هر درجه حرارتی به ازای فشار معینی تبخیر می شود. هرگاه در حین جریان مایع در داخل یک پمپ، فشار مایع در نقطه ای از فشار تبخیر مایع در درجه حرارت مربوطه کمتر شود. حباب های بخار یا گازی در فاز مایع به وجود می آیند. که به همراه مایع به نقطه ای دیگر با فشار بالاتر حرکت می نمایند. اگر در محل جدید فشار مایع به اندازه کافی زیاد باشد. حباب های بخار در این محل تقطیر میشود و در نتیجه ذراتی از مایع از مسیر اصلی خود منحرف میشود. و با سرعت های فوق العاده زیاد به اطراف و از جمله پره ها برخورد می نمایند. در چنین مکانی نسبت به شدت برخورد، سطح پره ها خورده میشود و متخلخل می گردد.
این پدیده مخرب در پمپ ها را کاویتاسیون می نامند. پدیده کاویتاسیون برای پمپ بسیار خطرناک بوده و ممکن است پس از مدت کوتاهی پره های پمپ را از بین ببرد. بنابراین باید از وجود چنین پدیده ای در پمپ جلوگیری گردد. کاویتاسیون همواره با صداهای منقطع شروع میشود و سپس در صورت ادامه کاهش فشار در دهانه ورودی پمپ، بر شدت این صداها افزوده می گردد. صدای کاویتاسیون مخصوص و مشخص بوده و شبیه برخورد گلوله هایی به یک سطح فلزی است. هم زمان با تولید این صدا پمپ نیز به ارتعاش در می آید. در انتهای این صداهای منقطع به صداهایی شدید و دائم تبدیل می گردد. و در همین حال نیز راندمان پمپ به شدت کاهش می یابد.
دمنده ها (Blowers)
دمنده ها نوع خاصی از کمپرسورها بوده که فشار نسبتاً کم و دبی نسبتاً زیاد دارند. حداکثر فشار قابل دسترس توسط آنها (2-1/5 بار) می باشند. دمنده های با فشار کم و دبی زیاد از نوع گریز از مرکز تولید می شوند. حال آنکه برای فشارهای بالا (نزدیک به 2 بار) و دبی کمتر نوع دورانی (Rorary) متداول تر می باشد. ساخت دمنده های از نوع تناوبی (رفت و برگشتی) عملاً منتفی است.
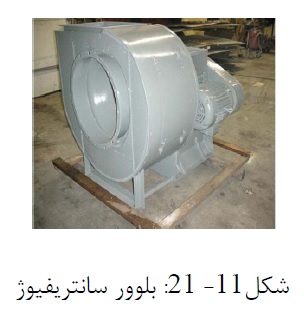
هواکش ها (Fans)
این نوع کمپرسورها عموماً برای دبی زیاد و فشار کم (تا 1-0 بار) ساخته شده و عموماً از خانواده گریز از مرکز می باشند.
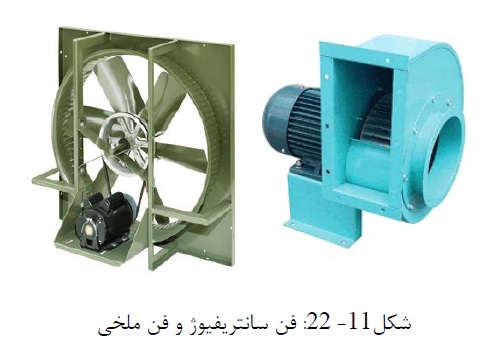
کمپرسورهای اصلی (گاز پروسس و گاز خنک کننده). و همچنین اغلب پمپ ها، بلورها و فن های مورد استفاده در احیاء مستقیم از نوع سانتریفیوژ می باشند.