آهن اسفنجی-تولید آهن اسفنجی-Direct Reduced Iron
آهن اسفنجی-تولید آهن اسفنجی-Direct Reduced Iron
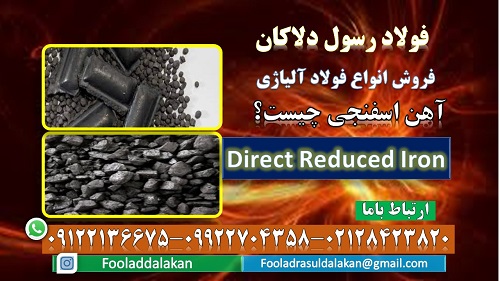
آهن اسفنجی محصول عملیات احیای مستقیم سنگ آهن و کالای جایگزین قراضه. برای ذوب در کوره های قوس و کوره های القایی است. به دو روش پایه گذاری و پایه زغالی تولید می شود. فرآیند تولید فولاد از سنگ آهن تا فولاد. با ضرایبی که به طور معمول و به طور استاندارد در دنیا عنوان می شود متغیر است. برای تولید یک کیلو فولاد به 2/56 کیلوگرم سنگ آهن نیاز است. هرچند که با توجه به خواص مختلف تغییر پیدا می کند.
اما موضوع بحث ما کوره های تونلی است. این کوره ها در واقع پایه زغال هستند و یکی از تفاوت های عمده این روش. با روش پایه گذاری در این است که نیاز به تولید گندله در کوره های تونلی وجود ندارد. یعنی بدون این که ما گندله سازی انجام دهیم می توانیم کنستانتره را به آهن اسفنجی تبدیل کنیم. که این از جمله مزایای این طرح به علت سرمایه بر بودن و هزینه بر بودن تولید گندله می باشد.
تفاوت روش پایه گازی و پایه زغالی
روش پایه زغالی به گندله سازی نیازی ندارد. نسبت سرمایه گذاری روش های زغالی کوره های تونلی پایین تر از روش پایه گذاری است. آن هم به دلیل سطح اتوماسیون و تکنولوژی به کار رفته است. در این کوره ها است که طبیعتاً به دلیل سادگی این روش ارزان تر بوده و یک شاخصی است. که در حقیقت 170 دلاربه ازای هر تن در سال می باشد. اگر کسی بخواهد 100 هزار تن آهن اسفنجی در سال با کوره های تونلی تولید کند. در حدود 17 میلیون دلار به سرمایه گذاری نیاز دارد.
البته این عدد تقریبی است که شامل زمین، سوله، زیر ساخت، آب، برق، گاز. و تمامی هزینه های سرمایه گذاری نصب و راه اندازی می شود. از دیگر مزایای این روش امکن استفاده از اکسید خطوط ذوب و نورد. باطله ریز معادن و ریزدانه های گندله سازی است. که اساساً یکی از دلایلی که این روش در کشور چین هم بسیار توسعه، یافته این است. که در کوره های بلند که پایه اصلی تولید فولاد در این کشور است. از ریزدانه های گندله سازی برای تبدیل به آهن اسفنجی. و ایجاد ارزش افزوده به منظور ذوب آهن اسفنجی استفاده می کنند.
در ایران در چند سال اخیر چینی ها خریدار اکسیدهای خطوط ذوب و نورد و پوسته های اکسیدی بودند که در حال حاضر بازار آن راکد است. در صورتی که در گذشته که ایران این مواد را به چین و سایر کشورها صادر می کرد. یکی از اصلی ترین کاربرد این اکسیدها در کشور چین، تولید آهن اسفنجی بود. یعنی ماده ای که ما در کشور می توانستیم به آهن اسفنجی تبدیل کنیم. با صرف هزینه زیادی چینی ها می بردند و در آنجا به آهن اسفنجی و سپس فولاد تبدیل می کردند. و در نهایت به خودمان می فروشند و حتی دامپینگ هم می کنند.
یکی دیگر از تفاوت های این دو روش نیروی انسانی است. که روش های پایه گذاری به دلیل سطح اتوماسیون بالایی که دارد. به نیروی انسانی با مهارت بالاتری نیاز دارد. در حالی که در روش پایه زغالی به دلیل ساده تر بودن این روش. از نیروی انسانی با مهارت پایین تر استفاده می کنند.
اگر بخواهیم یک کارخانه پایه گازی را به روش معمول که میدرکس است. در ایران راه اندازی کنیم به طور معمول بین 2 تا 3 سال. اگر در دست بخش خصوصی باشد زمان می برد. اما در بحث تولید خط کوره تونلی قطع به یقین. می توان در کمتر از یک سال آن را راه اندازی کرد. و حتی در کشور چین زمانی که یک پروژه آغاز می شود 7 تا 8 ماه زمان می برد. تا پروژه به بهره برداری برسد.
یکی دیگر از تفاوت های این دو روش این است. که اساساً روش پایه زغالی در سایزها و ظرفیت های کوچک در نظر گرفته شده است. در صورتی که در روش پایه گازی به علت هزینه بر بودن روش و خصوصیات آن در ظرفیت های پایین به طور معمول ساخته نمی شود معمولاً در ایران هم 800 هزار تنی، یک میلیون تنی و … ساخته می شود. اما در روش کوره تونلی می توان در ظرفیت پایین کوره را راه اندازی نمود و آهن اسفنجی تولید کرد.
از دیگر تفاوت های این روش این است. که در روش کوره تونلی می توان به متالیزاسیون 96 درصد رسید که البته این به صورت معمول است. که در چین هم این اتفاق در حال وقوع است. اما یکی از ضعف هایی که روش پایه زغالی دارد این است. که امکان تولید آهن اسفنجی داغ و یا بریکت گرم وجود ندارد. چرا که محصولی که از کوره خارج می شود. پایین تر از 200 درجه و معمولاً 70 تا 80 درجه است تا به دمای محیط برسد.
در نتیجه امکان تولید آهن اسفنجی داغ و امکان استفاده از آن به طور مستقیم. جهت کاهش هزینه های انرژی در کوره های قوس و القایی وجود ندارد. که این انز نقاط منفی این روش در کنار نقاط مثبت آن است. اما در مورد مصارفش، مصرف آب بسیار کمی دارد طبق جدول 1 نیم متر مکعب مصرفی که دارد. هم می تواند به مراتب کاهش یابد که طبیعتاً بستگی به مکانی که پروژه می خواهد در آنجا انجام شود. دمای هوا، برج های خنک کنی که جهت خنک کاری استفاده می شود. باز یا بسته بودن آن و سطح تکنولوژی که استفاده می گردد دارد. اما میزان مصرف کمتر از نیم متر مکعب است.
در مقابل روش گازی که به طور معمول در روش های میدرکس و … حداقل 1/3 متر تن آهن اسفنجی را داریم البته اگر ما گندله سازی را به روش پایه گذاری اضافه کنیم. طبیعتاً هزینه ها و مصارف این شاخص ها افزایش می یابد. اگر بخواهیم این دو را با هم مقایسه کنیم بهتر است. که گندله سازی و مصارفت گندله سازی را به این شاخص اضافه کنیم. مصرف برق روش پایه زغالی در حالت استاندارد 90 کیلو وات ساعت است. اما در روش پایه گازی 150 کیلو وات ساعت است. مصرف گاز آن کمتر است و مصرف اکسیژن و نیتروژن هم ندارد.
مزایای تولید آهن اسفنجی به روش پایه زغالی
مزایای تولید آهن اسفنجی به روش پایه زغالی نسبت به روش پایه گازی
- سرمایه گذاری کم
- توجیه برای واحدهای کوچک که می خواهند در ظرفیت های کوچک کار کنند.
- تأثیرات مخرب زیست محیطی کمتر
- فرآیند تولید بسیار ساده و کنترل پذیر
- عدم نیاز به نیروی انسانی متخصص
دلایل اهمیت این روش برای ایران
چرا این روش در ایران اهمیت دارد و ما به عنوان یک شرکت که بیشتر در حوزه فولاد فعال بوده. این روش را در ایران توصیه می کنیم؟ طبق مطالعاتی که در گذشته در بحث های مختلف در خصوص کاهش هزینه ها و ایجاد زنجیره تولید. برای کارخانه های بخش خصوصی صورت گرفت، این مسأله حایر اهمیت بود. که بتوانیم سراغ روشی برویم که از عهده آن برآییم و در عین حال اقتصادی باشد. و در نهایت بتوانیم با آن به تولید دست یابیم. اگر بخواهیم به کوره های تولیدی روش پایه زغالی فکر کنیم باید این نکته را در نظر داشته باشیم.
که این روش برای ظرفیت های پایین مناسب است. یعنی اگر کسی می خواهد یک میلیون تا دو میلیون تن تولید کند ما به هیچ وجه توصیه نمی کنیم. که از روش پایه زغالی استفاده کند. به دلایل پیچیدگی هایی که ایجاد می کند و راندمان را کاهش می دهد. این روش با ظرفیت های مختص خودش مناسبت دارد. به طور مثال فرض کنید که بخواهیم چرخ یک کامیون را به جای چرخ یک دستگاه پیکان ببندیم. این عملاً امکان پذیر نیست و باید تناسب آن را حفظ کنیم. اما دلایل اهمیت آن عبارتند از:
-وجود معادن متعدد و پراکنده سنگ آهن با عیارها و ذخیره های متفاوت. مناسب برای معادن، با ظرفیت ها و عیار پایین است.
-ضعف زیرساختی برای پروژه های بزرگ به روش گازی: با توجه به این که ما در ایران با مشکلات زیرساختی نظیر تأمین برق، گاز و … مواجه هستیم.
-وجود معادن زغال سنگ حرارتی. با توجه به این که زغال سنگ از مواد اولیه مورد نیاز. برای تولید آهن اسفنجی در کوره های تونلی است.
-وجود معادن آهن متعدد در کشور
-مناسب بودن این روش برای واحدهای کوچک فولادسازی
-عدم اجبار به خام فروشی سنگ آهن در معادن کوچک و حداکثرسازی ارزش افزوده بر روی سنگ آهن
ویژگی های متمایز شرکت HZK
یکی از قدیمی ترین و بزرگترین شرکت تأمین کننده، طراح و سازنده تجهیزات تونلی است. که در ظرفیت های مختلف از 5 هزار تن تا 300 هزار تن در سال این شرکت تجربه دارد. و دفتر آن در شهر ووهان چین است. این شرکت بزرگترین سازنده خط تولید آهن اسفنجی با کوره تونلی است. و سابقه ساخت بیش از 100 کوره تونلی در چین. هند، کره جنوبی، کره شمالی، کشورهای آفریقایی و ایران را دارد. دارای توان مهندسی بسیار بالا، کارخانه ساخت تجهیزات، بتنت های طراحی مختلف در ساخت کوره تونلی است. شرکت HZK سازنده خط تولید آهن اسفنجی با کوره تونلی برای یک سرمایه گذار چینی در ایران نیز است.
جمع بندی
با توجه به مزایای تولید آهن اسفنجی در ایران و نیز ارزان تر بودن قیمت سنگ آهن،گاز. زغال سنگ حرارتی و با توجه به نبود زیرساخت های لازم جهت تولید. با ظرفیت های زیاد و سرمایه گذاری های بالایی که جهت تولید در ظرفیت های بالا مورد نیاز است. و همچنین برنامه های دولت جهت افزایش تولید محصولات فولادی. و با توجه به کمبود قراضه (ضایعات) می توان به سادگی نتیجه گرفت:
-آهن اسفنجی مورد نیاز کشور است.
-از نظر اقتصادی تولید آن در ایران قاعد تا باید توجیه بالایی داشته باشد.
-کوره تونلی چه از نظر ظرفیت (مقیاس) و چه از نظر سرمایه گذاری. و چه از نظر ریسک سرمایه گذاری گزینه بسیار مناسبی برای سرمایه گذاران است.
تولید آهن اسفنجی
فرآیند تولید آهن اسفنجی با روش تونلی
به طور کلی دو روش برای تولید آهن اسفنجی با کوره تونلی وجود دارد.1- روش دستی (سنتی) 2- روش خودکار
در روش دستی سیستم خودکار پر کردن بوته ها وجود ندارد و این کار با دست انجام می شود. همچنین تخلیه آهن اسفنجی از بوته ها نیز با دست صورت می پذیرد. در این روش جهت سهولت شارژ سنگ آهن در بوته ها، آن را قبل از شارژ پرس (بریکت) می کنندن. این کار در روش خودکار حذف می گردد و پودر کنستانتره شارژ می شود.
در هر صورت در هر دو روش ماده اولیه (سنگ آهن، زغال و آهک) بایستی خشک شود. و لذا از خشک کن یا Dryer استفاده می شود. تفاوت دیگری که در خطوط تولید آهن اسفنجی با کوره تونلی وجود دارد. تولید یا عدم تولید بریکت آهن اسفنجی است. به این صورت که به طور معمول کارخانجاتی که خود آهن اسفنجی را مصرف می کنند. آن را به همان صورتی که تولید می شود مصرف می کنند. اما شرکت هایی که تمایل به فروش محصولات خود دارند. پس از تولید آهن اسفنجی آن را پودر و پرس (بریکت) می کنند. بریکت سازی منجر به افزایش دانسیته (و نه آنالیز آهن اسفنجی). و کاهش سطح تماس با هوا جهت جلوگیری از اکسیداسیون می گردد.
مواد اولیه تولید آهن اسفنجی
سنگ آهن ایده آل برای تولید بهترین آهن اسفنجی
-مگنتیت ترجیحاً 67/5 درصد
-هماتیت ترجیحاً 65/5 درصد
-مجموع SiO2 و Al2O3 زیر 3 درصد و حداکثر 5 درصد
-سایز: 50% زیر 5 میلیمتر، 30% زیر 1 میلیمتر و 20% تا 14 میلیمتر (0 تا 1 میلیمتر)
پوسته اکسیددی خط نورد یا ریخته گری:
-به جای سنگ آهن امکان استفاده از پوسته اکسیدی وجود دارد.
(مزیت مهم)
زغال سنگ:
-خاکستر زیر 15% و حداکثر تا 20%
-مواد فرار زیر 8% و حداکثر تا 15%
-کربن فیکس بالای 60% و ترجیحاً 65%
-گوگرد زیر 0/5 % و حداکثر 0/7 %
-رطوبت زیر 3% و حداکثر زیر 7%
-سایز: زیر 3 میلی متر
-نقطه ذوب خاکستر بالای 1250 درجه سانتی گراد
-ارزش حرارتی حداقل 5500 کیلو کالری بر کیلوگرم
آهک:
-با خلوص بالای 50%
-سایز: زیر 3 میلی متر
ویژگی های محصول
در صورت نیاز به بریکت سازی. دانسیته بریکت 4 تن بر متر مکعب و سختی: 500 نیوتون بر سانتی متر مربع
محاسبات اقتصادی تولید آهن اسفنجی
سرمایه گذاری برای تولید 70 هزار تن در سال آهن اسفنجی:
-نرخ دلار مبادلاتی 30 هزار ریالی در نظر گرفته شده است (در حال حاضر ارز مبادله ای نرخ کمتری دارد)
-قیمت زمین در هزینه ها دیده نشده است.
-هزینه های ثابت سرمایه گذاری برای ظرفیت های مختلف تقریباً به صورت خطی تغییر می کند.
-هزینه ها دست بالا در نظر گرفته شده اند.
نکته: در محاسبه سود، با توجه به تورم موجود، هزینه استهلاک در نظر گرفته نشده است اما هزینه های نگهداری و تعمیرات در نظر گرفته شده است.
اصطلاح فولاد و یا پولاد برای آلیاژهای آهن. که بین 0/2 درصد تا حدود 2 درصد کرین دارند بکار می رود. فولادهای آلیاژی غالباً با فلزهای دیگر در ارتباط هستند. خواص فولاد به درصد کربن موجود در آن، عملیات حرارتی انجام شده. بر روی آن و فلزهای آلیاژ دهنده موجود در آن بستگی دارد.
دو روش کلی برای تهیه فولاد خام مورد استفاده قرار می گیرد.
روش کوره بلند(BOF) – Basic Oxygen Furnace
روش کوره های قوس الکتریکی (EAF)- Electric Arc Furance
ساخت اولین کوره بلند (Blast Furnace) در مقیاس صنعتی بر پایه استفاده از کُک توسط ابراهام داربی (Abraham Darby) در سال 1735 میلادی صورت گرفت. در روش کوره بلند سنگ آهن پس از خردایش و دانه بندی. بصورت ترکیبی از آگلومره و سنگ آهن دانه بندی شده. و پس از شارژ در کوره بلند بطور غیر مستقیم. و از طریق کُک به آهن خام یا چدن مذاب (pig Iron) احیاء میشود. سپس از کوره های اکسیژنی (BOF) جهت تولید فولاد از آهن استفاده می شود.
این تکنولوژی مهمترین شیوه تولید فولاد خام در جهان به شمار می آید. و شیوه ای سنتی تولید است که از احیای غیر مستقیم آهن استفاده می شود. چون بزرگترین تولید کننده فولاد خام سال های اخیر در جهان. نیز 90/2 درصد از کل فولاد خام خود در سال 2010 را به روش کوره بلند تولید کرد. در ایران نیز بالغ بر 12 درصد آن در کوره های اکسیژن تولید می شود. و کارخانه ذوب آهن اصفهان نیز از این تکنولوژی استفاده می کند. با توجه به وجود گاز طبیعی فراوان و ارزان در ایران. و مشکلات ناشی از کمبود کُک متالورژیکی و افزایش قیمت صادراتی آن. به نظر می رسد باید فرآیند تولید فولادسازی در ایران در راستای آهن اسفنجی و کوره قوس الکتریکی رشد کند. از دیگر معایب کوره بلند می توان به آلودگی بیشتر آن نسبت به روش احیای مستقیم اشاره نمود.
اما روش دوم بر پایه احیای مستقیم سنگ آهن می باشد. به صورتی که پس از فرآوری و تولید کنستانتره و نهایتاً گندله، عملیات احیاء در کوره های میدرکس. با عبور گازهای حاصل از شکست گاز طبیعی. از لا به لای گندله شارژ شده در کوره احیاء انجام می گیرد. آهن اسفنجی محصول این روش می باشد. همانطور که گفته شد. در این روش گاز طبیعی (ch4) عامل احیای سنگ معدن آهن است. و به همین دلیل در کشورهایی با منابع غیر گاز طبیعی مانند ایران مورد توجه است.
در ایران به طور مثال، فولاد خوزستان و فولاد مبارکه از گاز به عنوان ماده احیا کننده استفاده می کنند. شناخته شده ترین روش های احیای مستقیم گازی روش های میدرکس و hyl هستند. آهن اسفنجی تولید شده سپس به منظور تولید فولاد در کوره های (EAF) قرار می گیرد. قابل ذکر است که هزینه راه اندازی یک واحد کوره بلند نسبت به یک واحد احیای مستقیم. و کوره الکتریکی در ظرفیت های متناظر، بالا تر است.
به صورت کلی مبانی احیای مستقیم سنگ آهن شامل:
Fe2O3-Fe3O4-FeO-Fe
می باشد که در آن درصد آهن نسبت به ترکیب (درجه فلزی شدن) طی هر مرحله طبق شکل زیر افزایش می یابد و آهن اسفنجی طی فرآیند احیای مستقیم ( روش دوم) به دست می آید.
Fe2O3 %69.9 Fe
Fe3O4 %72.4 Fe
FeO %77.7 Fe
Fe %100 Fe
اساس نامگذاری آهن اسفنجی به دلیل کم شدن مقدار اکسیژن موجود در هر مرحله می باشد. در نتیجه بوجود آمدن حفره در ترکیب می باشد. به صورتیکه در مرحله اول طبق فرمول از تعداد 9 عدد اکسیژن به 8 عدد تقلیل یافته. و در مرحله بعد طی فرآیند تبدیل FeO4 به FeO تعداد اکسیژن از یک واحد کمتر شده. و به 3 عدد می رسد و در مرحله آخر تمامی اکسیژن در ترکیب از بین می رود.
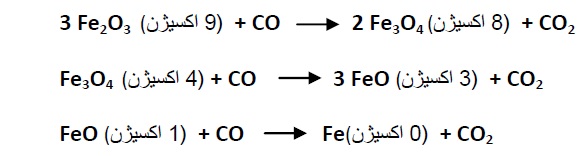
بر اساس اطلاعات رسانی هندوستان این کشور بزرگترین تولید کننده آهن اسفنجی در دنیا می باشد. این کشور از مجموع تولید 70.4 میلیون تن آهن اسفنجی دنیا. در سال 2010 حدود 23.4 میلیون تن در حدود 33 درصد از کل تولید را به خود اختصاص داده است.
فولاد رسول دلاکان
با سالها تجربۀ ارزشمند و گرانبها در عرصه تأمین و توزیع انواع ورق آلیاژی و انواع فولاد آلیاژی. با گواهینامه ها و آنالیزهای معتبری که ضمیمه محصولاتش به مشتریان خویش ارائه داده است. توانسته رضایتمندی مشتریان خویش را همواره فراهم آورد.
صنعتگر شریف و گرامی از اینکه ما را جهت خرید کالا (فولاد آلیاژی) مورد نیاز خویش. انتخاب می نمایید از شما سپاسگزاریم.
ارتباط با ما
09122136675 – 02128423820-09922704358
واتس آپ: 09122136675
اینستاگرام: fooladdalakan
ایمیل : fooladrasuldalakan@gmail.com