کوپلینگ- انواع کوپلینگ
کوپلینگ ها، ارتباط بین دو محور را برقرار می سازند و در یک محدوده زمانی یا بطور دائم کار انتقال قدرت را انجام می دهند. کوپلینگ ها بین منبع انرژی (موتور) و ماشین کار یا جعبه دنده قرار می گیرند. و وظیفه خود را در چارچوب چهار گروه اصلی به پایان می رسانند. مثلاً در دستگاه ماشین تراش سه نظام، ماشین کار است.
کوپلینگ
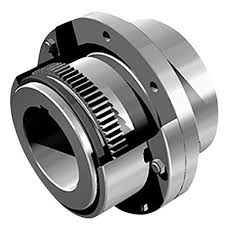
وظایف کوپلینگ
نیروها و گشتاورها را منتقل می کنند.
تغییرات طولی، عرضی یا زاویه ای محورها نسبت به یکدیگر را ممکن می سازندن.
اتصال و جداسازی محورها را نسبت به هم میسر می کنند.
ضربه ها و ارتعاشات را کاهش می دهند و یا از بین می برند.
لازم به یادآوری است که اگر بخواهیم ارتباط دو محور را وصل یا قطع کنیم. این عمل با باز و بسته کردن اجزاء مکانیکی کوپلینگ انجام می پذیرد. در این صورت محور محرک بایستی از حرکت بایستد.
کلاچ ها نوعی از کوپلینگ ها هستند. با این تفاوت که ضمن کار، امکان قطع و وصل شدن انتقال قدرت دو محور را ممکن می سازند. اتصال به یک عمل مکانیکی یا فیزیکی وابسته است که معمولاً اصطکاک است. قطع و قصل کلاچ به دلایل زیر لازم است.
تغییر سرعت و تغییر جهت را در حین حرکت ممکن می سازد.
در مواقع نیاز و یا خطر، انتقال قدرت را در ماشین به سرعت قطع می کند.
از انتقال حرکت غیر ضروری ماشین جلوگیری می کند.
در مصرف انرژی صرفه جوی می کنند.
ترمزها به منظور تنظیم سرعت و ساکن کردن قطعات یا دستگاه های در حال حرکت به کار می روند. ترمزها معمولاً در تمامی وسایل نقلیه، انواع دستگاه های بالابر و جرثقیل و در بیشتر ماشین آلات به کار می روند.
کوپلینگ ها
گوپلینگ ها، محورها را در جهت محوری به یکدیگر ارتباط می دهند و انواع مختلفی دارند. در تعیین نوع کوپلینگ ها، ماهیت اساسی آنها را وضعیت قرار گیری محورها نسبت به هم و در یک امتداد نبودن آنها مشخص می کند. این غیر هم محوری در نتیجه مونتاژ و ساخت و ازدیاد طول در اثر حرارت پدید می آید. در شکل 1-7 چهار مورد از ارتباط دو محور مشاهده می شود.
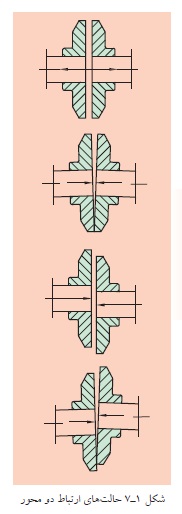
کوپلینگ هایی که نمی توانند ناهماهنگی میان محورها را از بین ببرند و ارتباط برقرار کنند. کوپلینگ های صلب (سخت) نام دارند. ولی کوپلینگ هایی که پاسخ گوی این ناهماهنگی هستند. به کوپلینگ های ارتجاعی معروفند. اگر در کوپلینگ های ارتجاعی، ارتباط سینماتیکی برقرار گردد. آنها را سینماتیکی یا مفصلی می گویند. ولی اگر به وسیله اجزاء الاستیکی انجام گیرد. کوپلینگ های الاستیکی نام می گیرند.
کوپلینگ های صلب (خشک)
برای استفاده از این نوع کوپلینگ ها، دو محور باید کاملاً در امتداد هم متصل شوند. و به شکل یک تکه عمل کنند. تا گشتاور و تعداد دور بدون هیچ گونه افتی منتقل گردد. لازم به یادآوری است که در این کوپلینگ ها در امتداد هم قرارگیری محورها، بسیار دشوار است. و اگر این دو محور در یک امتداد قرار نگیرند. در محل ارتباط، گشتاور و نیروی ضربه ای ایجاد می گردد. به همین دلیل، در هنگام برقراری ارتباط، دقت خاصی لازم است. از این کوپلینگ ها، اغلب در ارتباط های با دور کم و یا در محورهایی با هم راستایی جزئی، استفاده می شود. متداولترین آنها دو دسته هستند. الف) کوپلینگ های پوسته ای. ب) کوپلینگ های فلانچی (دیستکی).
7-2-1 کوپلینگ پوسته ای
ویژگی این نوع کوپلینگ ها، ساده بودن آنهاست. که دو محور را به صورت خودکار، هم مرکز می سازند. و خیلی راحت باز و بسته می شوند. اینها نیز از نظر ساختمان دارای شکل های گوناگونی هستند. که یک نوع آن در شکل 2-7 نمایان است.
پوسته این کوپلینگ ها دو تکه است. و محور داخل این دو نیمه قرار می گیرد. هر دو پوسته به وسیله پیچ هایی بر روی محورها بسته می شوند. در نتیجه این بسته شدن، بین محور و کُوپلینگ در سطح داخلی فشار ایجاد می شود. و گشتاور چرخشی به وسیله اتصال اصطکاکی انتقال می یابد. به خاطر اهمیت مسئله اطمینان، اغلب بین محور و پوسته از خارهای انطباقی نیز استفاده می شود. بدین ترتیب در صورت نیاز، گشتاور به وسیله این خار منتقل می شود. در چنین شرایطی هرگز از گوه استفاده نمی شود. زیرا نیروهای بستن در خلاف جهت نیروی گوه اثر می کنند. همچنین پیچ های مربوط، به صورت متناوب (یک در میان) و برعکس همدیگر بست می شوند تا از لنگی وزن جلوگیری شود.
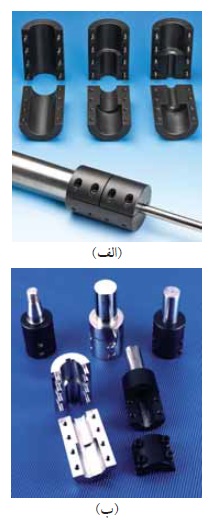
پوسته این کوپلینگ ها از جنس چدن (GG-20) یا از فولاد ریختگی (GS-45) تولید می شود. برای انتخاب آنها می توانیم از کاتالوگ های مختلف کارخانه ها کمک بگیریم.
جدول 1-7، نمونه ای از کوپلینگ های پوسته ای که مربوط به DIN 115 است و قطر سوراخ (D) را نشان می دهد
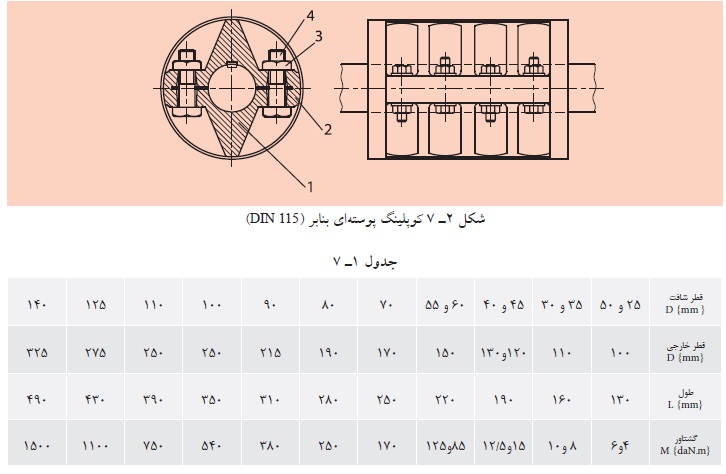
کوپلینگ فلانچی
در این کُوپلینگ ها نیز باید دو محور کاملاً در یک امتداد باشند. این کُوپلینگ ها نیروی خمشی زیادی را تحمل نمی کنند. ولی می توانند قدرت پیچشی زیادی را انتقال دهند. (شکل 3-7). اساساً کوپلینگ های فلانچی دو تکه هستند. و هر یک به انتهای یک محور مونتاژ می شوند. و آنها را به وسیله پیچ ها می بندند. اتصال فلانچ ها بر روی محور، به وسیله خارهای انطباقی صورت می گیرد. معمولاً سطح دو فلانچ را به شکل برجستگی و فرورفتگی می سازند که دو محور بدین وسیله کاملاً هم محور می شوند (شکل 3-7 ب).
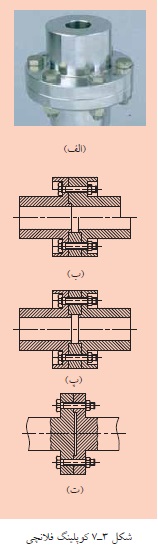
تنها عیب این روش این است که در هنگام باز کردن آنها، فلانچ، سیستم فلانچ و محور را در جهت محوری حرکت می دهد. و از هم جدا می سازد. به همین خاطر در بعضی مواقع بین دو فلانچ، یک حلقه قرار می دهند (شکل 3-7-ت). این نوع کوپلینگ ها از جنس چدن 20-GG و GG-25 و یا فولاد ریختگی 45-GS هستند. که مشخصات آنها را از کاتالوگ های کارخانه های مختلف می توان انتخاب کرد.
ان کوپلینگ ها به راحتی می توانند حرکت و گشتاور را در بین محورهایی با قطرهای مختلف انتقال دهند. فقط عملیات فرم دادن قسمت های داخلی و خارجی آنها دشوار است.
کوپلینگ های ارتجاعی
هرگاه نتوانیم محور محرک و متحرک را در یک امتداد قرار دهیم. یعنی این دو محور، انحراف محوری، شعاعی و زاویه ای جزیی نسبت به هم داشته باشند. از کوپلینگ های ارتجاعی استفاده می شود. که حرکت دورانی الاستیکی ندارند. و گشتاور چرخشی را مانند کوپلینگ های ثابت منتقل می سازند. بنابراین، این کوپلینگ ها نسبت به کوپلینگ های ثابت، مصرف بیشتری دارند. در انحرافات زاویه ای که ارتعاشاتی به وجود می آید. این کوپلینگ ها نمی توانند آن را از بین ببرند. به همین دلیل نسبت به کوپلینگ های الاستیکی که از این خانواده هستند. حرکت های دینامیکی کاملاً متفاوتی دارند. این کوپلینگ ها به دو دسته تقسیم می شوند: الف) کوپلینگ متحرک ب) کوپلینگ های الاستیکی
کوپلینگ های متحرک
گوپلینگ های پنجه ای متغیر طولی (منبسط شونده طولی)
ساده ترین نوع کوپلینگ های متغیر غیرالاستیکی هستند که به کوپلینگ پنچه ای معروف اند. زمانی که در محورها، در مقابل حرارت زیاد، انبساط طولی بیشتری پدید آید. از این نوع کوپلینگ ها استفاده می شود (مثل توربین های بخار). در شکل 4-7 نمونه این کوپلینگ نمایان است.
از این کوپلینگ ها به عنوان کلاچ های با قابلیت قطع و وصل نیز استفاده می شود. یک نیمه آن به وسیله یک خار لغزنده می تواند در انتهای یکی از محورها، حرکت کشویی انجام دهد. و با نیمه دوم که در روی محور دیگر ثابت شده، درگیر و یا از آن جدا گردد. و بدین ترتیب انتقال حرکت را قطع و وصل کند. برای این منظور هر دو محور باید در حالت سکون باشند.
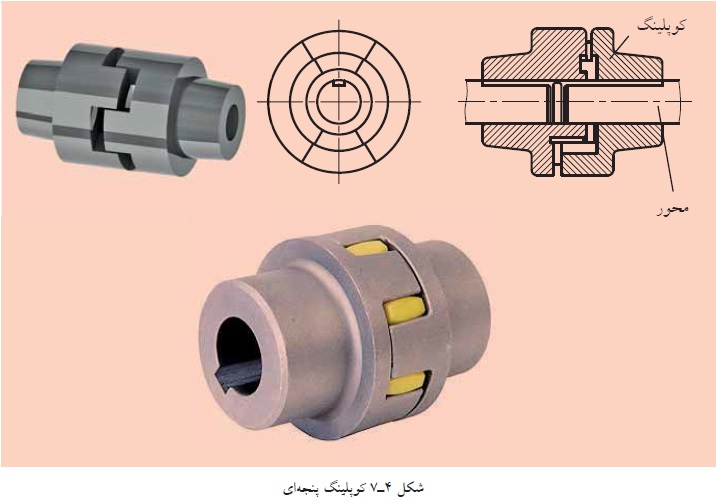
کوپلینگ اولدهام (متغیر مقطعی)
کوپلینگ های اولدهام از سه قسمت جداگانه تشکیل شده اند. نمونه های مختلف آن در شکل 5-7 دیده می شود. در شکل 5-7 الف این نوع کوپلینگ را در حال درگیری مشاهده می کنیم. کوپلینگ ها به ترتیب به محورهای 1 و 2. با استفاده از خارهای انطباقی، متصل شده اند. و دیسک میانی A که دارای دو باریکه برجسته در دو پیشانی طرفین با زاویه 90 درجه نسبت به هم است. با آنها درگیر است.
این اجزاء به صورت جدا از هم در شکل 5-7 پ مشخص و معلوم است. این درگیری در امتداد محور، مثل سطوح لغزنده صورت می گیرد. و لقی های موجود در برجستگی و فرو رفتگی های آنها، این عمل را ساده تر می کند. و اگر محورها نسبت به هم انحراف محوری یا شعاعی داشته باشند. در موقع دوران محورها، با نوسانات مناسب دیسک میانی، حالت تعادل برقرار می شود. همچنین با جلوگیری از تأثیر نیروهای اضافی، حرکت و گشتاور منتقل می شود.

انحراف های شعاعی بین محورها، می تواند تا a = 0/05d باشد (شکل 5-7-الف). و انحراف زاویه تا ° 1 ≥ φ را می تواند تحمل کند. همچنین نوع دیگر این کوپلینگ، مطابق شکل 5-7 ت. زاویه انحراف را تا ° 3 ≥ φ و کوپلینگ شکل 5-7 ت تا ° 4 ≥ φ می تواند، تحمل کند.
φ (فی) زاویه انحراف دو محور است. کوپلینگ های اولدهام در هنگام دوران، می توانند در روی دیسک میانی به فاصله دایره ای به قطر a حرکت کنند. این حرکت بسته به وزن دیسک میانی، نیروی گریز از مرکز ایجاد می کند. به همین دلیل حتی الامکان سعی می شود. وزن دیسک میانی کم در نظر گرفته شود. و در نتیجه دیسک میانی را جنس نایلون سخت می سازند.
نوع کوپلینگ را معمولاً با توجه به نیاز، از کاتولوگ های کارخانجات انتخاب می کنند. فقط در موقع انتخاب، فشارهای سطحی مربوط به سطوح تماس کنترل می شود. این رابطه های h=0.03d و D=(3,4)d مقادیر h و D به دست می آیند. که d قطر محور، و h ارتفاع برجستگی دیسک میانی است. فشارهای سطح تماس در شکل 5-7 ب مشخص و نمایان است. درجه سختی برجستگی دیسک میانی باید 55 الی 60 درجه سختی راکول باشد. و پس از 100 ساعت کار، گریس کاری شود.
راکول چیست؟ راکول دستگاه سختی سنج فلزات است. که درجه سختی فلزات را با آن اندازه می گیرند.
کوپلینگ گاردان (متغیر زاویه ای)
در انتهای دو محور، دو چنگال متصل می شود. و یک عضو میانی به شکل صلیب، ارتباط محورها را برقرار می سازد. گاه با مفصل های کروی نیز تولید می شود. که در صنعت موارد کاربرد زیادی دارند. در انتقال حرکت بین دو محوری که امتداد آنها نسبت به هم تحت زاویه باشد. مورد استفاده قرار می گیرند. شکل (6-7) برای انتقال نیروهای پیچشی بین دو محوری که در یک امتداد نیستند و یا با زوایای مختلفی نسبت به یکدیگر قرار دارند. از مفصل استفاده می کنند. مفصل بندی این نوع کوپلینگ ها را در شکل (7-7) می بینیم.
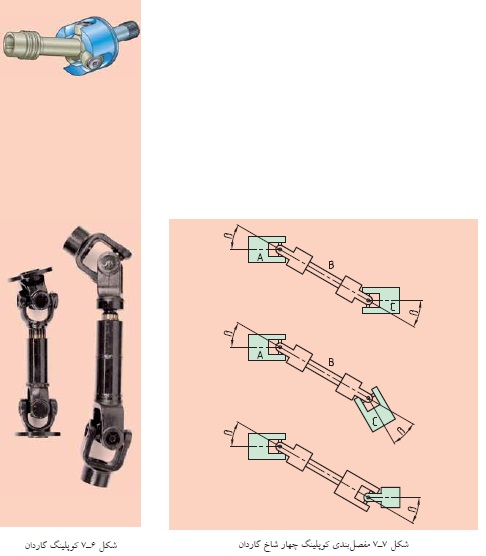
در صورتی که زاویه انحراف بین دو محور زیاد باشد. از چهار شاخ گاردان استفاده می شود. توصیه می شود که زاویه انحراف بین دو محور °5 تا °15 در نظر بگیرند.
البته در دورهای خیلی پایین، حرکت را تا زاویه °45 می توان منتقل کرد. در این حالت معمولاً بین دو محور، یک محور واسطه قرار می گیرد. که وجود چنین محوری سبب می شود. تا دو محور محرک و متحرک به صورت موازی قرار گیرند. بدین ترتیب می توانیم سرعت دو محور محرک و متحرک را یکسان سازیم و در صورت نیاز می توانند زاویه دار نیز باشند. در شکل (8-7) استفاده از محور واسطه را در حالت های مختلف مشاهده می کنیم.
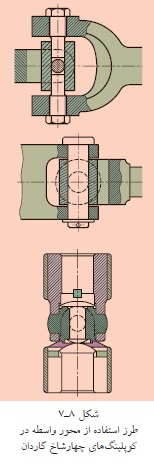
البته دلیل دیگر بکارگیری از دو شاخ گاردانی، از بین بری خطاهای احتمالی موجود در مفاصل است. برای اینکه گاردان ها اصولی کار کنند. شرایط زیر لازم است.
الف) همه قطعات محورها بر روی یک صفحه قرار خواهند گرفت.
ب) هر دو مفصل نسبت به هم با حالت Z به خود می گیرند. و یا با زاویه کار خواهند کرد.
پ) در هر دو حالت (ب) زوایای گاردان یکی خواهد شد.
ت9 چنگال های هر دو سر میله میانی در یک صفحه قرار خواهند داشت.
گاردان ها در صنعت خودروسازی، لکوموتی و ماشین سازی ابزار کاربرد زیادی دارند.
در شکل 9-7 یک نمونه پرکاربرد آنها را مشاهده می کنید.
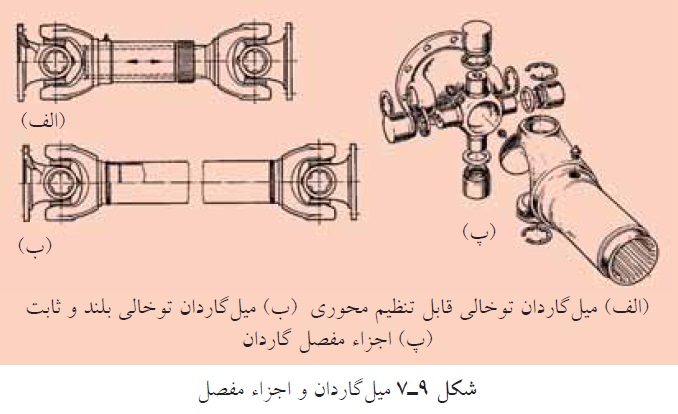
چنانچه بیان شد خیلی مواقع در مفاصل از ساچمه استفاده می کنند. نمونه این محور را در شکل 10-7 مشاهده می کنید.
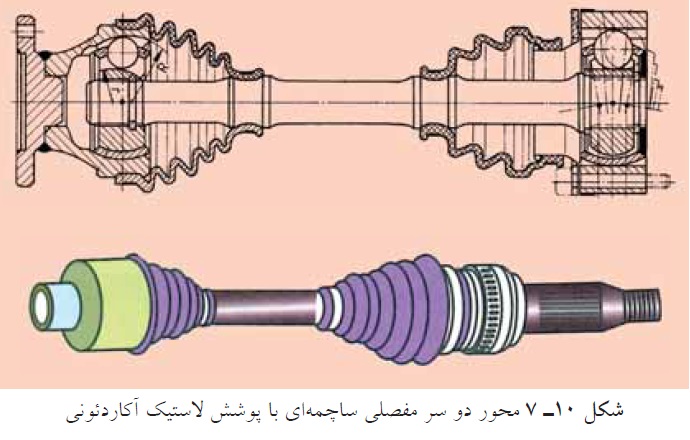
کوپلینگ های دنده ای:
از پر مصرف ترین انواع کوپلینگ ها، کوپلینگ های دنده ای هستند.
سیستم هایی وجود دارد که در آنها چرخ دنده، فقط روی یک محور سوار می شود. در شکل 11-7 الف در قسمت فوقانی و بغل دنده های کوپلینگ که شکل کروی دارد و لقی ایجاد می کنند، نمایان است. که انحراف های محوری، شعاعی و زاویه ای بین دو محور را بر طف می سازد (شکل 11-7 ب و 11-7پ). در موقع انتخاب این نوع کوپلینگ از کاتالوگ، باید دقت کرد که هر چه زاویه انحراف افزایش یابد. به همین اندازه نیروی انتقالی کمتر می شود.
برای انتقال گشتاورهای کوچک و متوسط، نوع ارزان آن ها که به نام کوپلینگ متغیر همه جانبه معروف است. به کار می رود که از پلاستیک خیلی سخت تولید می شود.
کوپلینگ های دنده ای
دو چرخ (1) و (2) به وسیله خارهای انطباقی به دو انتهای محورهای محرک و متحرک مونتاژ می شود. یک پوسته (3) که دارای دنده های داخلی است. ارتباط این دو محور را برقرار می سازد. این پوسته به صورت دو قطعه ساخته میشود. و با پیچ و مهره به هم متصل می شود. چنانچه بخواهند گشتاورهای کوچک را انتقال دهند. به صورت یکپارچه ساخته می شود. که بوسیله پیچ های (5) جمع شده، به هم بسته می شوند.
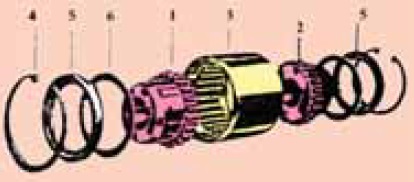
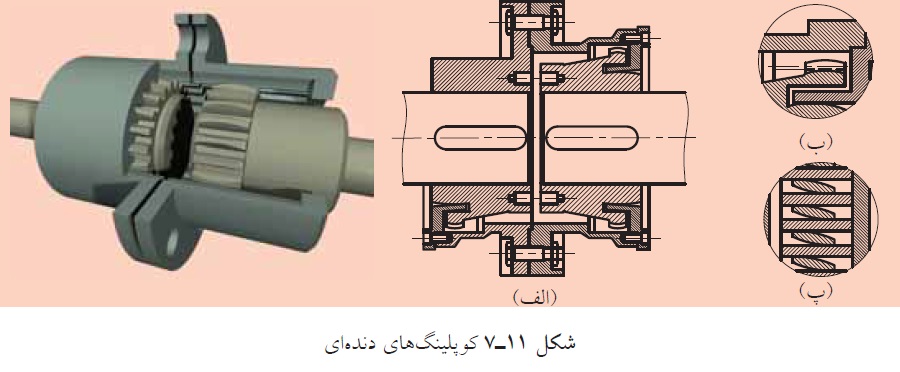
کوپلینگ توربو فلکس
این کوپلینگ ها مطابق شکل 12-7 الف از دو توپی فلانچ دار a و b و قطعه میانی c. که عمدتاً بصورت شفاف توخالی فلانچ دار است، تشکیل می شوند. گشتاور توسط المان فنری d منتقل می شود. و به کمک آن جابه جایی محوری و زاویه ای میسر است. نصب این کوپلینگ، بین یک الکتروموتور و یک پمپ در شکل 12-7 ب نشان داده شده است.
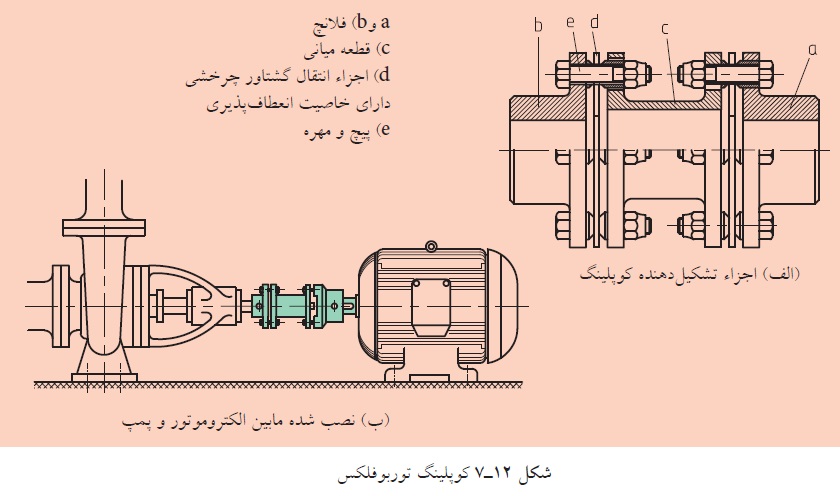
کوپلینگ های الاستیکی
کوپلینگ های الاستیکی، انحرافات محوری، شعاعی و زاویه ای بین دو محور محرک و متحرک را تنظیم می کنند. و حرکت را به نرمی انتقال می دهند. این کوپلینگ ها در اثر حرکت، ارتعاشات و ضربه های ایجاد شده را از بین می برند. و مستهلک می کنند. در این کوپلینگ ها معمولاً دو فلانچ برروی دو محور محرک و متحرک مونتاژ شده است. و بین آنها، اجزاء الاستیکی از نوع حلقه ها و صفحات لاستیکی و فنرهای نواری و فشاری قرار گرفته اند. که ارتباط بین دو محور را بر قرار می سازند. در شکل 13-7 دو نیمه کوپلینگ با تغییرات ممکن این دو نیمه نسبت به هم نشان داده شده است. همچنین در اثر گشتاور انتقالی، هر دو نیمه کوپلینگ، نسبت به یکدیگر می چرخند. در یک چرخش ضربه ای، زاویه چرخش بزرگ تر می شود. و لاستیک میانی، ضربه را جذب و مستهلک می کند.
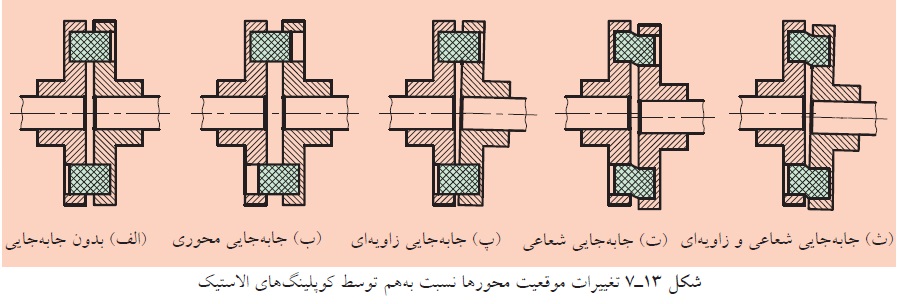
کوپلینگ های الاستیک، انواع مختلفی دارند. که در این جا به سه نوع خیلی مهم آنها اشاره می کنیم.
الف) کوپلینگ های الاستیکی با نواز فنری
ب) کوپلینگ های بسیار الاستیک پری فلکس
پ) کوپلینگ های بسیار الاستیک کِگِل فلکس
کوپلینگ های الاستیکی با نوار فنری
انتقال حرکت و گشتاور در این کوپلینگ ها به کمک یک نوار فنری فولادی انجام میشود. در شکل 14-7 نوعی از این کوپلینگ را می بینیم. که فنر به صورت مارپیچ در داخل شیارهای فرعی در محیط دو نیمه کوپلینگ قرار گرفتند. برای این که فنر بر اثر نیروی گریز از مرکز از درون شیار خارج نشود از یک پوشش فلزی استفاده می شود.
چون نیروهای ضربه ای وارد بر نیمه محرک کوپلینگ، موجب تغییر نرم الاستیکی بازوهای پیچشی فنر می شود. و بر اثر سختی و خاصیت فنرها،ضربات را خنثی می کند. همچنین نیمه محرک کوپلینگ و نیمه متحرک را به آرامی به دنبال خود می کشد. و با خود هماهنگ می سازد، لذا از این کوپلینگ ها برای انتقال گشتاورهای زیاد، مثل دستگاه های نورد استفاده می کنند. در حالی که محورها باید در یک امتداد باشند. زیرا امکان تصحیح انحراف محوری وجود ندارد.
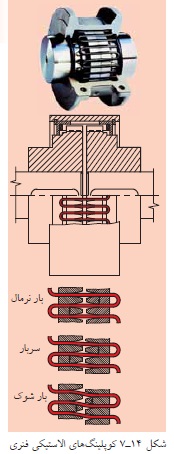
کوپلینگ بسیار الاستیک پری فلکس
در این کوپلینگ ها، دو نیمه کوپلینگ با لاستیک به هم متصل می شوند. و بر اثر خاصیت الاستیکی خیلی زیاد، ضربه ها و ارتعاشات شدید، کاملاً مستهلک می شوند.
اثرات ناشی از انحرافات زیاد شعاعی، زاویه ای و جابه جایی محوری، خنثی می شوند. چنان چه در شکل 15-7 مشاهده می کنید. هر دو گلویی به کمک لاستیک U شکل رشته وار، با استفاده از حلقه های فشاری توسط پیچ ها به همدیگر متصل می شوند. بدین ترتیب انحرافات خیلی بزرگ تنظیم می شود و باعث انتقال گشتاورهای بزرگ می شود.
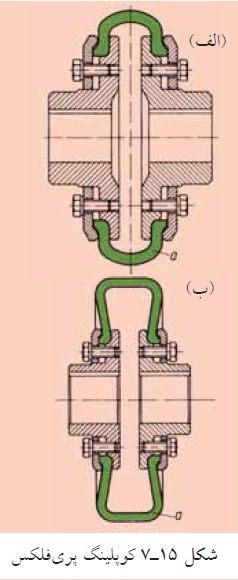
کوپلینگ بسیار الاستیک کِگِل فلکس
این کوپلینگ ها با خاصیت بالای الاستیک و مطابق شکل 16-7 دارای عضو رابط مخروطی شکل (a) هستند. حداکثر گشتاوری که می توانند منتقل کنند 3500 نیوتن متر است. و قطر شفاف آن می تواند ماکزیمم 450 میلی متر باشد.
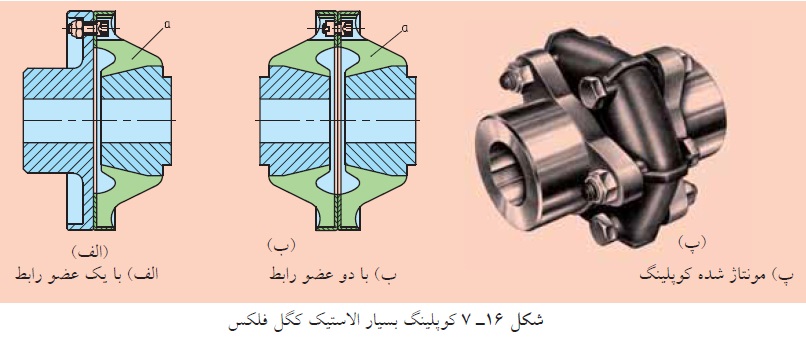
کلاچ ها
کلاچ ها، اجزایی از ماشین هستند که در هنگام نیاز، ارتباط یک محور را به محور دیگری برقرار یا قطع می کنند. و سرعت های آن دو محور را به یک سرعت واحد می رسانند. همچنین با گشتاور ایجادی، انرژی را منتقل می سازند.
ابعاد کلاچ ها متناسب با قطر محورها به صورت استاندارد تولید می شود. و مکانیزم ارتباطی آنها دارای اهمیت زیادی است. در موقع درگیری، حتماً باید محورها به صورت هم مرکز قرار گیرند. در کلاچ ها معمولاً ارتباط به صورت مکانیکی یا الکترومغناطیسی برقرار می شود. به همین دلیل آنها در کلاچ های مکانیکی و الکترومغناطیسی می نامند. در کلاچ های مکانیکی، ارتباط بسیار ساده است. و به صورت تماسی یا اصطکاکی برقرار می شود. به همین دلیل، کلاچ های مکانیکی به دو گروه خشک و اصطکاکی تقسیم می شوند.
کلاچ های متغیر، علاوه بر فراهم سازی امکان انتقال حرکت و گشتاور، وظیفه دارند حرکت را نیز به دلخواه قطع و وصل کنند. از برخی کلاچ ها به منظور ضامن ایمنی نیز استفاده می شود. بدین صورت که در موقع افزایش غیر مجاز نیرو، ارتباط حرکت را قطع می کنند. و مانع از آسیب دیدگی سایر اجزاء ماشین می شوند. ضمناً به وظیفه اصلی خودشان نیز عمل می کنند. حال بعضی از کلاچ ها را به اختصار شرح می دهیم.
کلاچ های مکانیکی
این کلاچ ها در مواقع دلخواه، حرکت بین دو محور محرک و متحرک را قطع و وصل می کنند. این ارتباط با عمل مکانیکی یا الکترومغناطیسی اتفاق می افتد و به همین دلیل کلاچ های مکانیکی یا الکترومغناطیسی وجود دارند.
در شکل 17-7 ب نیمه a کلاچ بر روی محور محرک ثابت شده است. و نیمه b آن روی محور متحرک قرار می گیرد. به طوری که بتوانیم نیمه b کلاچ را در جهت محور بلغزانیم. در نتیجه لغزش، با نیمه a ارتباط برقرار می کند. حرکت محور محرک به محور متحرک منتقل می شود. و ارتباط ان دو برقرار می شود. و در صورت جدا شدن نیمه b از نیمه a، حرکت دو محور از همدیگر جدا می شود.
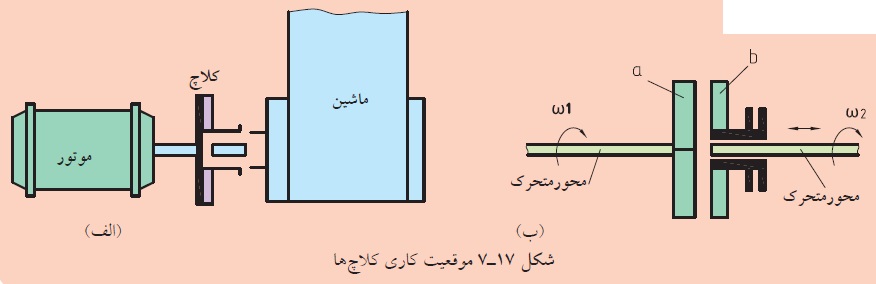
ارتباط در کلاچ های مکانیکی به وسیله اجزای تماسی آنها و یا به کمک اصطکاک برقرار می شود. ضمناً تمامی این کلاچ ها در نوع اتوماتیک نیز موجود هستند. در شکل 18-7 سیستم قطع و وصل کننده مکانیکی ساده ای را مشاهده می کنید. که با عمل دو طرفی، حرکت کلاچ ها را قطع و وصل می کند. این سیستم در وسایل نقلیه موتوری زیاد کاربرد دارد.
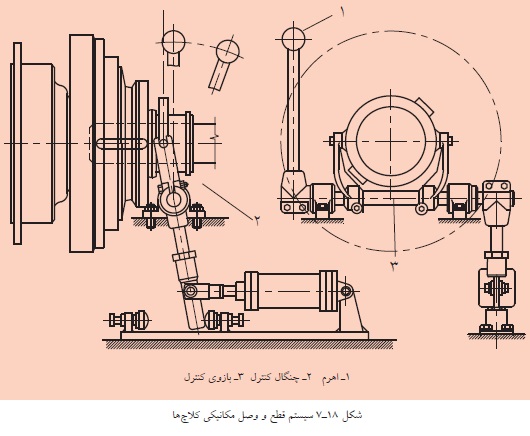
کلاچ ها ی خشک قفلی
مکانیزم این نوع کلاچ ها خیلی ساده است. و به شکل های پنجه ای و دنده ای ساخته می شوند. همانطور که در شکل 19-7 می بینید. در سطح پیشانی این نوع کلاچ ها، پنجه هایی وجود دارد. که در هنگام درگیری، با پنجه های نیمه دیگر کلاچ ارتباط برقرار می کنند.
در نتیجه ارتباط سطوح پنجه ها به یکدیگر، گشتاور انتقال می یابد. پنجه ها معمولاً به شکل های مکعب مستطیل (19-7الف)، فرم دار (19-7ب) و دنده ای (19-7پ) ساخته می شوند.
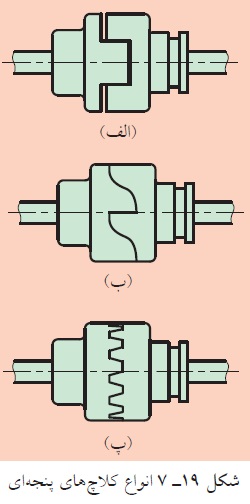
معمولاً کلاچ های قفلی، در سرعت های مختلف، می توانند ارتباط دو محور محرک و متحرک را قطع کنند. اما در حالت بی حرکت یا در سرعت های کم نیز می توانند. ارتباط را برقرار سازند. کلاچ هایی که پنجه های شیب دار (زاویه ای) دارند تا RPM 150 می توانند، درگیر شوند. فقط کلاچ های پنجه ای فرم دار (شکل 19-7 ب) گشتاور را در یک جهت تغییر می دهند.
کلاچ های دارای پنجه مکعب مستطیل (شکل 19-7 الف) می توانند گشتاور را در هر دو جهت منتقل کنند. در مواردی که محور محرک در حال حرکت نیست، یا هر دو نیمه کلاچ دارای یک سرعت و در حال حرکت باشند.. می توانند ارتباط را برقرار سازند (شکل 20-7 الف).
کلاچ های دارای پنجه مکعب مستطیل (شکل 19-7الف) می توانند گشتاور را در هر دو جهت منتقل کنند. در مواردی که محور محرک در حال حرکت نیست. یا هر دو نیمه کلاچ دارای یک سرع و در حال حرکت باشند. می توانند ارتباط را برقرار سازند (شکل 20-7 الف).
در کلاچ های دنده ای، دندانه ها، یا در سطح جانبی نیمه کلاچ ها (شکل 20-7). و یا در سطح پیشانی آنها قرار دارند (شکل 20-7پ).
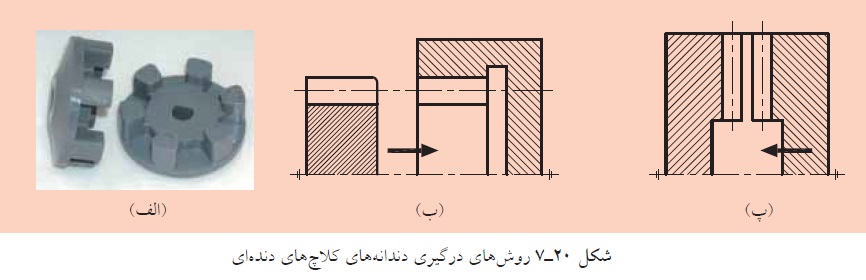
این کلاچ ها تا 300 دور بر دقیقه می تواند درگیر شوند. معمولاً کلاچ ها صلب در ابعاد کوچک می توانند گشتاورهای بسیار بزرگی را منتقل کنند. فقط در موقع ارتباط، دو نیمه کلاچ با ضربه (ضربه های کلاچی) رو به رو می شوند. به همین دلیل باید نیمه های کلاچ به طور کامل هم مرکز باشند.
کلاچ اصطکاکی
برای ارتباط دو نیمه کلاچ، نیمه کلاچ موجود بر روی محور محرک، با یک نیروی محوری بر روی نیمه کلاچ دیگر نیرو وارد می کند. در روی دو سطح تماس، یک نیروی اصطکاکی و همچنین گشتاور اصطکاکی حاصل می شود. و با این فرآیند حرکت منتقل می شود.
کلاچ های اصطکاکی
در کلاچ های اصطکاکی، حرکت محور محرک به محور متحرک، از طریق نیرو، با اصطکاک امکان پذیر است. مزیت مهم کلاچ های اصطکاکی این است که در حین حرکت می توانند. درگیر و یا آزاد شوند و گشتاور چرخشی آنها به واسطه نیروی اصطکاک محدود است. به همین خاطر بسیار نرم کار می کنند. و هم زمان به عنوان کلاچ های ایمنی به کار می آیند.
سیستم های کنترل انواع ماشین های ساخت و تولید امروزی دارای کلاچ های اصطکاکی هستند. به خصوص بعضی از آنها که از راه دور قطع و وصل می شوند. جایگاه بالایی در صنعت امروز پیدا کرده اند. نیروی قطع و وصل این کلاچ ها به کمک هوای فشرده، روغن پرسی و یا به صورت مغناطیسی ایجاد می شود. در شکل 21-7 یک نوع کلاچ اصطکاکی دیده می شود.
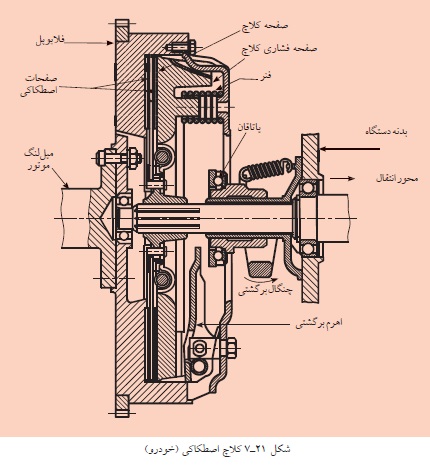
این کلاچ ها ویژگی هایی به شرح زیر دارند.
الف) در زمان شروع ارتباط دو نیمه کلاچ و تماس آنها، در سطوح اصطکاک یک لغزش به وجود می آید. بعد از درگیر شدن دو نیمه کلاچ، این لغزش از نظر تئوری صفر می شود. و هر دو محور با یک سرعت شروع به حرکت دورانی می کنند.
ب) در نتیجه این لغزشف اتلاف انرژی و به دنبال آن ازدیاد گرما ظاهر می شود. عمل قطع و وصل هرچه بیشتر تکرار شود. باعث به وجود آمدن ساییدگی و ایجاد خراش می شود.
پ) گشتاور به راحتی از محور محرک به محور متحرک (بدون ضربه) انتقال می یابد.
ت) عمل قطع و وصل در هر زمان خیلی ساده و راحت انجام می گیرد. با توجه به بند پ و ت، کلاچ های اصطکاکی در عمل، بیشترین مصرف را دارند. در صنایع اتومبیل و ماشین سازی افزار مورد مصرف زیادی دارند.
کلاچ های اصطکاکی با در نظر گرفتن شکل سطح تماس آنها به صورت های دیسکی، مخروطی، کفشکی و نواری ساخته می شوند.
در شکل 22-7 نمونه ساده این نوع کلاچ ها را مشاهده می کنیم. کلاچ های اصطکاکی به صورت های اتوماتیک نیز زیاد ساخته می شوند. که نمونه هایی از آنها را شرح خواهیم داد.
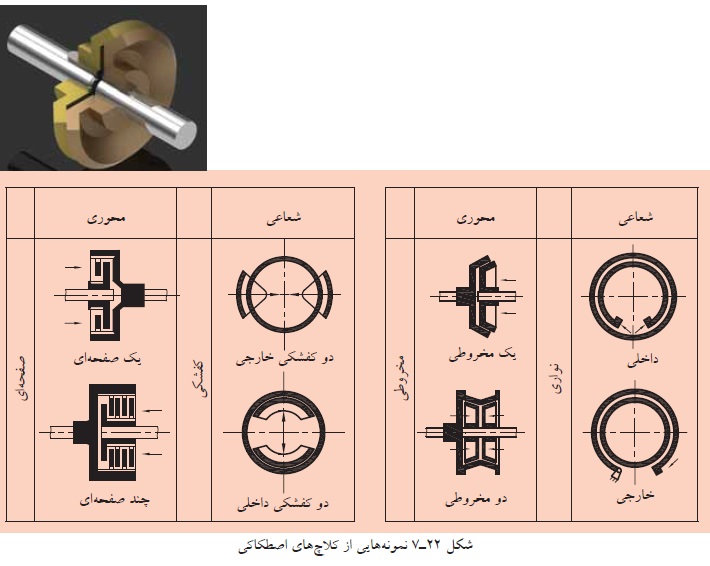
کارکرد
گشتاور چرخشی در هر دو جهت توسط اصطکاک لنت کلاچ که به صفحه فولادی متصل است. منتقل می شود. این صفحه قابل لغزش روی هزارخار امتداد محور شماره (2) جعبه دنده و قابل جابه جا شدن در امتداد محور است. لنت کلاچ به وسیله فنرهای فشاری (3) بین دو صفحه فشار (4) فشرده می گردد. و با محفظه کلاچ (5) اتصال اصطکاکی به وجود می آید. با لغزش غلاف (6) به کمک اهرم کلاچ (7) سمت چپ انتقال حرکت قطع می شود. بنابراین عمل حلقه متصل به بلبرینگ (8) قسمت کروی انتهای اهرم های (9) را فشار می دهد..و سر دیگر اهرم، موجب حرکت صفحه کلاچ به راست و جمع شدن فنرهای فشار و قطع اتصال کلاچ می شود.
کلاچ های یک صفحه ای
در شکل 23-7 یک کلاچ دیسکی یک صفحه ای که برای قطع و وصل حرکت در وسایل نقلیه موتوری مناسب است، مشاهده می شود.
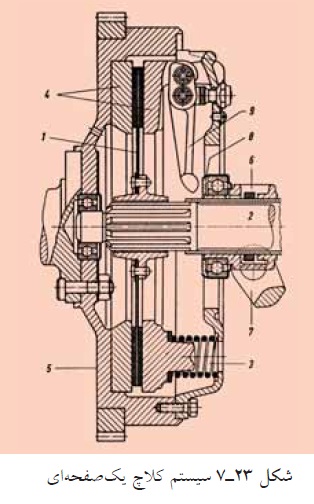
طرز کار کلاچ صفحه ای را در شکل 24-7 می بینیم. با دقت در این شکل، کلاچ های صفحه ای را در حالت کار کردن و همچنین در حالت آزاد مشاهده می کنیم. اگر اهرم را در جهت فلش بکشیم (شکل 24-7الف) کلاچ درگیر می شود و کار انجام می دهد. ولی اگر آن را به جای اول خود برگردانیم (شکل24-7ب) کلاچ آزاد می شود.
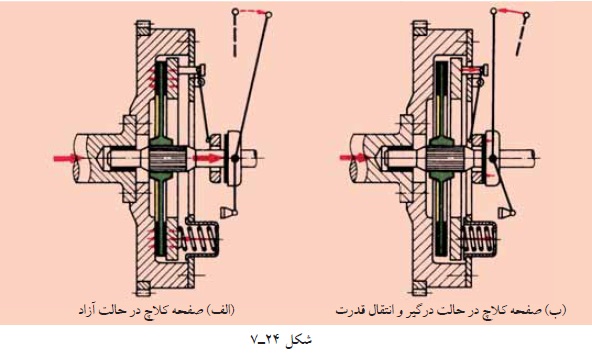
در شکل 25-7 نیز کلاچ صفحه ای نوع دیگری را مشاهده می کنیم. که در شکل 25-7 در حالت درگیر و در شکل 25-7 پ در حالت آزاد، نمایان و مشخص است.
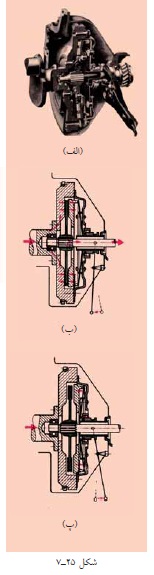
کلاچ های چند صفحه ای
یک کلاچ چند صفحه ا، در شکل 26-7، نمایان و مشخص است. این نوع کلاچ ها از نظر ساختمان نظیر کلاچ های یک دیسکی هستند. با این تفاوت که در اینجا به بدنه محور محرک و همچنین به گلویی محور متحرک، دیسک های زیادی بست می شوند. از طرف دیگر دیسک ها بدون پوشش هستند. و از فولادهای مورد سخت کاری تولید می شوند. در این صورت، سطوح اصطکاکی فولاد-فولاد هستند. این کلاچ ها به کلاچ های سینوسی نیز مشهورند. و بین دیسک ها، ورق های فنری خیلی نازکی مورد کاربرد می باشد (شکل 26-7 ب).
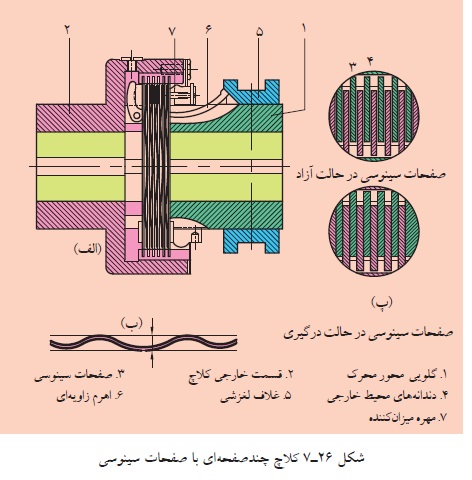
این فنرها باعث می شوند. تا کلاچ تدریجاً و به راحتی قطع و وصل شود. فنرها در هنگام برقراری ارتباط، باعث می شوند. که در سطوح تماس، فشار افزایش یابد. این فشار باعث می شود گشتاور اصطکاکی نیز به تدریج زیاد شود. در کلاچ هایی که سطوح تماس آنها فولاد -فولاد معمولی تولید شدند. روغن موجود بین دیسک ها باعث چسبیدگی آن دو به یکدیگر می شود. در این شرایط هرگاه نیروی فشار را برداریم. صفحات به راحتی از هم جدا نمی شوند. به همین دلیل وجود فنرها در لابه لای صفحات، سبب می شود. که دیسک ها به راحتی از هم جدا شوند.
کلاچ های مخروطی
در شکل 27-7، کلاچ مخروطی یک صفحه ای ساده را مشاهده می کنیم. با کلاچ های مخروطی یک صفحه ای می توانیم گشتاورهای کوچک را انتقال دهیم. برای انتقال گشتاورهای چرخشی بزرگ که نیروی محوری نیز افزایش می یابد. از کلاچ های مخروطی دوبل استفاده می شود. کلاچ مخروطی شکل 27-7 در سیستم ترمز نیز به کار می رود.
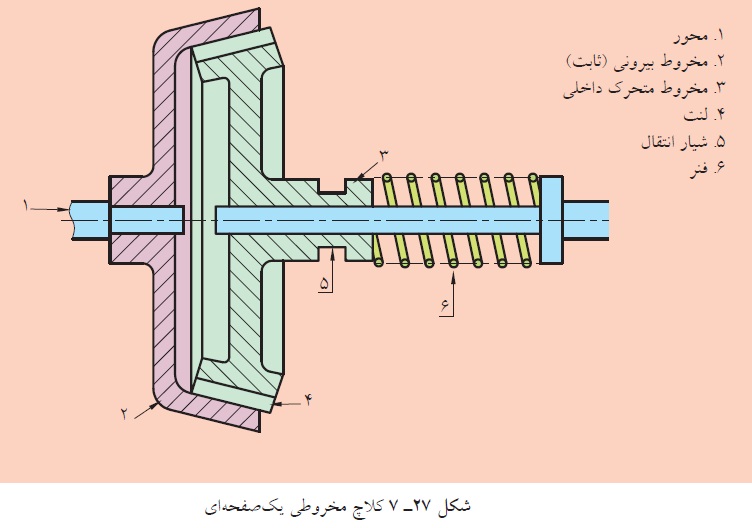
کارکرد
کلاچ مخروطی دوبل
در این کلاچ، حرکت از طریق اصطکاک دو سطح مخروطی (2) و (3) منتقل می شود. پین (4) در روی گلویی (1) تثبیت شده است. و در دو سطح نیز روی همین پین در امتداد محوری لغزش می کنند. در اثر لغزش غلاف (5)، عمل قطع و وصل صورت می گیرد.
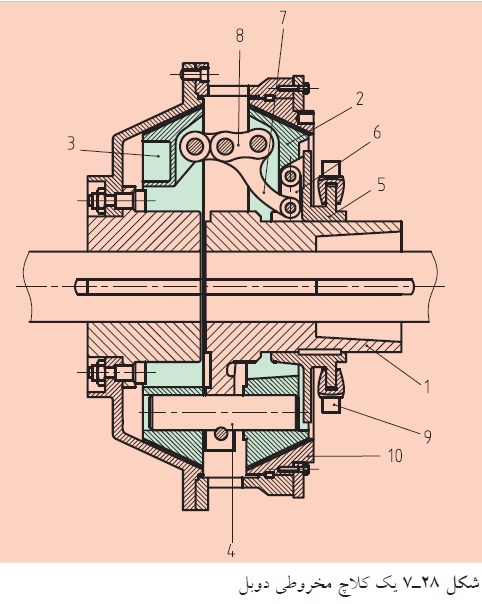
ترمزها
ترمزها اجزایی از ماشین هستند که سرعت حرکت اجسام را کم کرده، یا آنهارا به طور کلی از حرکت باز می دارند. و برای این کار انرژی جنبشی یا انرژی پتانسیل را در طی مراحل کاهش سرعت یا توقف کامل قطعه متحرک جذب می کنند. این انرژ جذبی به صورت حرارت تلف می شود. انجام هرچه بهتر عمل ترمز، به فشار ایجادی در واحد سطح ترمز. ضریب اصطکاک و قابلیت ترمز اتلاف حرارت که معادل انرژی جذبی می باشد، بستگی دارد. ترمزها مشابه کلاچ ها هستند. با این تفاوت که کلاچ ها دو جزء در حال حرکت را به هم وصل می کنند. در حالی که ترمزها یک جزء متحرک را به قاب متصل می سازند.
ترمزها با توجه به عملکردشان انواع مختلفی دارند. رایج ترین آنها ترمزهای مخروطی، یک صفحه ای، دو صفحه ای، چند صفحه ای، کفشکی یا کفشک های داخلی یا خارجی، دیسکی و نواری هستند.
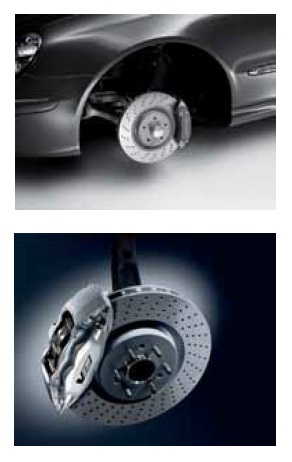
همچنین سیستم های کنترل آنها مانند کلاچ ها به صورت مکانیکی، پنوماتیکی، هیدرولیکی و الکترومغناطیسی تولید می شوند. ترمزها را برای منظورهای مختلفی به کار می برند. مثلاً برای پایین آوری جسمی که سیستم ترمز آن انرژی پتانسیل را حذف کرده و به صورت انرژی حرارتی تبدیل می کند. و یا در جسمی مانند خودروها، انرژی جنبشی را به صورت انرژیی حرارتی تلف می کند. و باعث توقف آن می شود. یا جسمی مثل آسانسورر و جرثقیل را در حالت آویزان نگه می دارد. در شکل 29-7 یک مدل از ترمزهای مخروطی را مشاهده می کنید. که یک موتور روتور کشویی با ترمز مخروطی مربوط است.
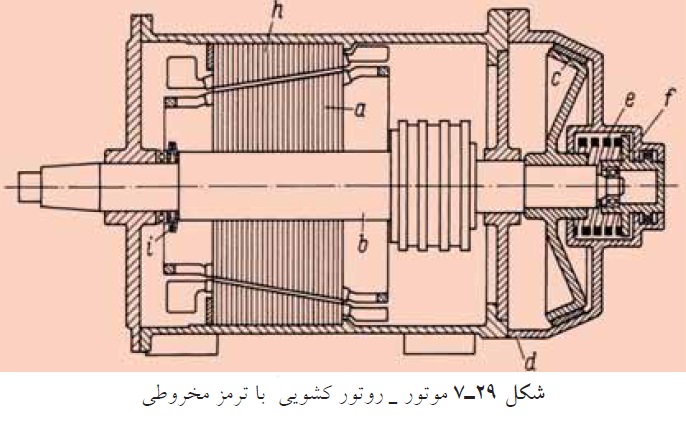
کارکرد
در حالت سکون، فنر (e) از طریق بلبرینگ (f) و دیسک (c) ترمز را به مخروط ترمز در محفظه (d) فشار می دهد. و در نتیجه شافت b محکم نگه داشته می شود.
با جریان برق، روتور (a) در اثر نیروی مغناطیسی به درون استاتور مخروطی h کشیده می شود. و بدین ترتیب ترمز رها می شود. در اثر قطع جریان برق، فنر ترمز را به کار می اندازد. و فنرهای بشقابی (i) ضربات محوری را مستهلک می کنند.
ترمزهای کفشکی
در ترمزهای کفشکی که موارد استفاده زیادی دارند. کفشک های ترمز مجهز به لنت های خیلی با دوام هستند. در شکل 30-7 یک نمونه از این ترمزها که یک کفشکی داخلی و خارجی هستند. و در صنعت خودروسازی کاربرد زیادی دارند، نمایان و مشخص است.
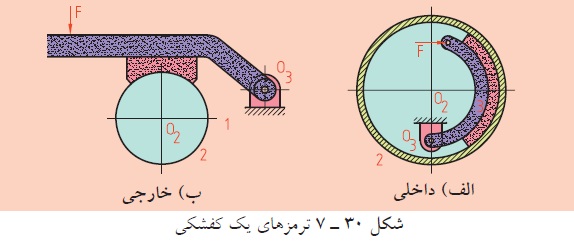
کارکرد
ترمزهای کفشکی: به طور کلی از سه قسمت تشکیل می شوند. لنت ترمز (1) که روی قطعه فولادی به فرم نیم دایره نصب است. کفشک (3) نام دارد. چرخ (2) مربوط به ترمز است. و در نتیجه ایجاد فشار کفشک از داخل و یا خارج به چرخ عمل ترمز صورت می گیرد. بازوی ترمز، وظیفه وارد کردن نیرو به کفشک را به عهده دارد (شکل 30-7 الف).
ترمزهای دو کفشکی، به ویژه در شرایط کاری سخت، مثلاً در جرثقیل هاف سیستم های انتقال مواد و سیستم های نوردکاری به کار می روند. در شکل 31-7 یک ترمز دو کفشکی را مشاهده می کنید که در جرثقیل به کار می رود.
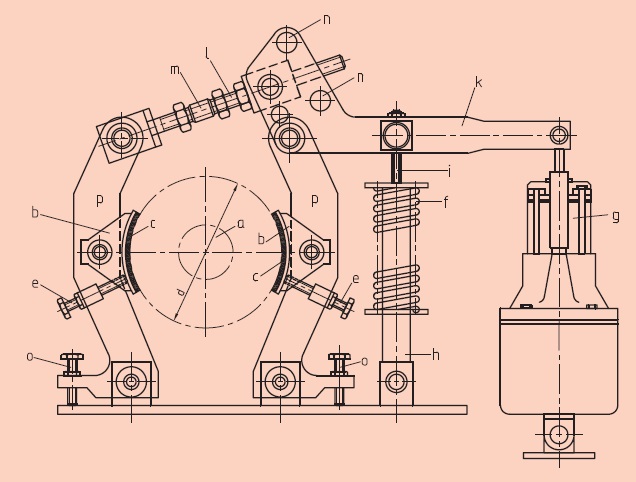
(a) شافت موتور، (b) کشفک های ترمز (c) لنت ترمز است. کفشک ها با پین در اهرم ترمز (p) یاتاقان بندی می شوند. و پیچ های تنظیم (e) از واژگون شدن کفشک ها در اثر وزنشان، در حالتی که ترمز آزاد است، جلوگیری می کنند. فنر فشاری (f) اهرم ترمز را همراه با کفشک ها از طریق میله های (K,i,h,l) به طبلک ترمز فشار می دهد. (g) دستگاه هیدرولیک یا آهنربای کششی است. برای خلاصی ترمز از طریق (k,l) عمل می کند. (m) مهره تنظیم نیروی فنر است. (n) سوراخ تنظیم درجه تبدیل اهرم است. نهایت (o) پیچ تنظیم (فنر تنظیم) حد اهرم در هنگام خلاصی ترمز و به منظور قرار گیری یکسان کفشک ها به کار می رود. پیچ های تنظیم نباید در کورس آهنربا مانع ایجاد کنند.
ترمزهای طبلکی که در گذشته در چرخهای خودرو به کار می رفتند. ترمزهایی با کفشک های داخلی هستند. که در آنها کفشک های ترمز از داخل به طبلک ترمز (کاسه ترمز) فشرده می شوند. امروز به جای آنها از ترمزهای دیسکی استفاده می شود. که ساختمان ساده تری دارند. ترمزهای دیسکی گرما را بهتر هدایت می کنند. و به خصوص در برابر ضریب اصطکاک حساس نیستند. در شکل 32-7 ترمز دیسکی با زین ثابت نمایان و مشخص می باشد. که به انبر نیز معروف است.
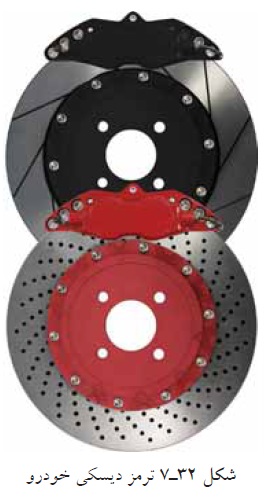
در دیسک ترمز یک کاسه ترمز با کفشک های داخلی قرار دارد. این ترمز طبلکی به عنوان ترمز دستی عمل می کند. در داخل زین دو سیلندر ترمز مقابل یکدیگر قرار می گیرند. یکی از سیلندرها در محفظه فلانچ و دیگری در محفظه درپوش زین قرار دارد. زمانی که دیسک ترمز همراه با چرخ خودرو دوران می کند. زیر ترمز در حالت سکون خواهد ماند.
اجزاء یک زین را در شکل 33-7 مشاهده می کنید.
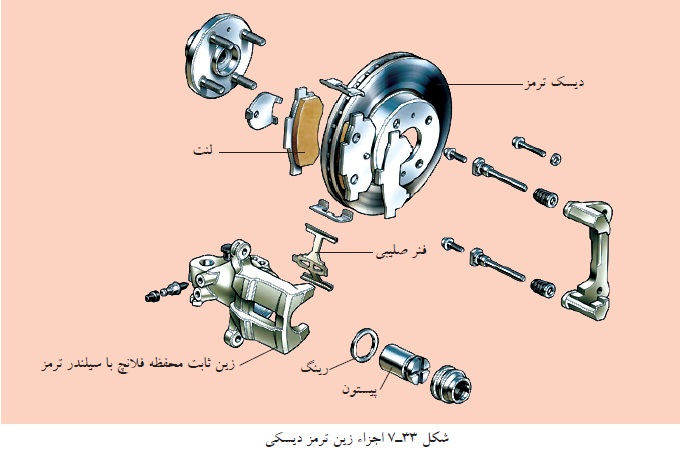
پیستون های هر دو سیلندر به اجزاء حامل لنت های ترمز اثر می کنند. و آنها نیز از دو طرف برعکس یکدیگر به دیسک ترمز فشار وارد می آورند. لنت ها در این ترمزها کوچک تر از لنت های ترمزهای طبلکی هستند. و به همین دلیل دماهای موضعی به وجود آمده، بالاترند. با وجود این هوای خنک می تواند به قسمت های پوشانده نشده دیسک ترمز از هر دو طرف جریان یابد. نیروی کاراندازی از ترمزهای طبلکی بزرگ تر است. از این رو در این ترمزها اغلب تقویت کننده های نیروی ترمز پیش بینی می شود.
اما ترمزهای دو کفشکی داخلی از نظر کارکرد مشابه ترمزهای کفشکی خارجی هستند. در خودروهای سواری و کامیون ها، از این ترمزها استفاده می شود. که بیشتر هیدرولیکی کار می کنند. به دلیل گشتاور اینرسی خودرو در زمان ترمز گرفتن. 55% الی 60% وزن خودرو به لاستیک های جلو گشتاور وارد می شود. در نتیجه، لاستیک های جلوی ماشین همیشه نسبت به لاستیک های عقب به اندازه 55% الی 60% به گشتاور نیروی اصطکاکی نیاز دارد. ترمزها بر مبنای مشخصات بالا و سیستم هیدرولیک آنها مطابق شکل 34-7 طراحی می شود. که به لاستیک های جلوی ماشین فشار زیادی را انتقال می دهند. از نظر عمل کردن، به صورت هماهنگ کار می کنند.
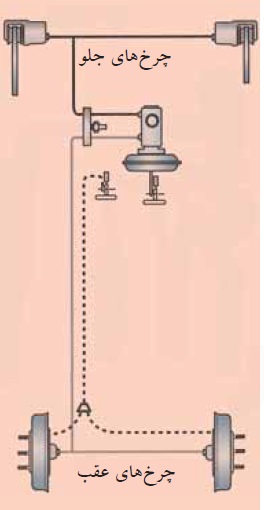
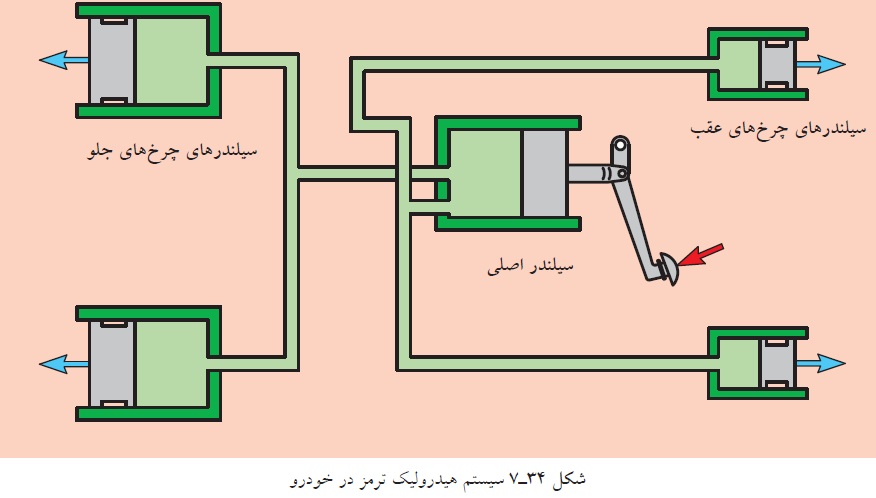
در شکل 35-7 مدار هیدرولیکی سیستم ترمز را می بینیم. در این تصویر نیروی وارد بر پدال ترمز به پیستون سیلندر اصلی منتقل می شود. پیستون، روغن را به فشار لازم به سیلندر داخل چرخ می فرستند و در آنجا فشار روغن باعث می شود. که کفشک ها از هم باز شوند. به کاسه چرخ بچسبند و در اثر اصطکاک به وجود آمده، سیستم ترمز کند.
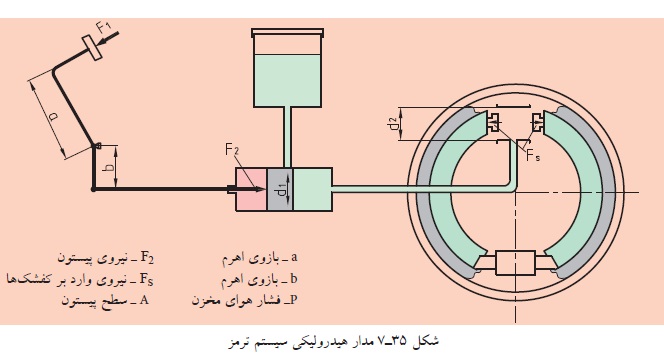
البته این ترمزها با سیستم پنوماتیکی نیز موجود هستند. در این سیستم به جای روغن از هوای فشرده استفاده می شود. و کارکرد آن، مطابق عمل سیستم هیدرولیکی است. در شکل 36-7 مدار پنوماتیکی سیستم ترمز را مشاهده می کنید.
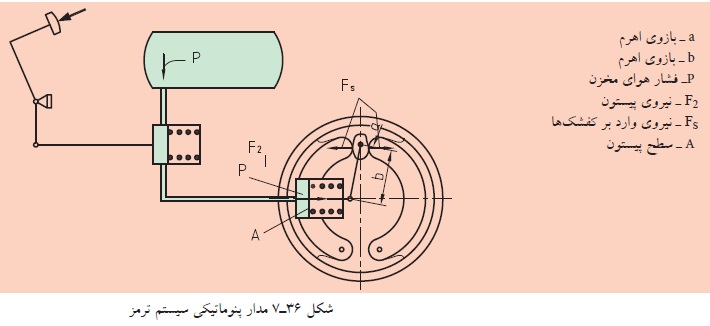
ترمزهای نواری
در این ترمزها یک نوار فلزی در اطراف فلکه قرار دارد. که اصطکاک ایجاد شده بین این نوار و چرخ، باعث توقف سیستم می شود. راندمان عمل ترمز، به زایه پیچش نوار در اطراف چرخ، ضریب اصطکاک و تنش موجود در نوار بستگی دارد.
یک ترمز نواری ساده در شکل 37-7 دیده می شود. این نوار طوری کشیده شده و به شاسی متصل شده که به حالت کاملاً کشیده درآمده است. یک نوع دیگر ترمز نواری در شکل 38-7 نشان داده شده است. در این ترمزها، چرخ در هر دو طرف می تواند حرکت و عمل کند. زیرا بازوهای گشتاور در هر دو طرف چرخ با هم برابر هستند.
لنت ها
لنت ها، در کلاچ ها و ترمزها کاربرد دارند. در ترمزها، پوشش کفشک ها را لنت ها تشکیل می دهند (شکل39-7).
جنس لنت ها با توجه به این که همیشه با اصطکاک و گرما رو به رو هستند. از اهمیت خاصی برخوردار است. لنت ها با توجه به اهمیت نوع کارشان، باید دارای ویژگی هایی باشند که چند مورد آنها را بیان می کنیم.
الف) ضریب مالشی بالا و یکنواختی داشته باشند.
ب) نفوذناپذیری آنها نسبت به شرایط محیط (رطوبت) در نظر گرفته شود.
پ) در برابر گرمای زیاد، توانایی پایداری داشته باشند و بتوانند گرما را به خوبی هدایت کنند.
ت) برگشت پذیری آنها خوب باشد.
ث) در مقابل سایش، خراش، ور آمدن یا باد کردن، مقاومت زیادی داشته باشند.
چنانچه ملاحظه می شود. ساخت مواد مالشی، یک فرآیند کاملاً تخصصی است. بنابراین لازم است که به انتخاب آنها توجه لازم را داشته باشیم. از بهترین نوع آنها و همچنین از استانداردهای موجود استفاده کنیم. لنت ها را در بیشتر ترمزها از مواد آزبست، بعنوان مواد اصطکاکی، می سازند. زیرا این مواد در مقایل اثرات حاصل از حرارت، مقاومت خوبی دارند.
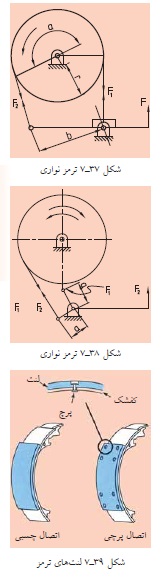
آزبست را به صورت الیاف تاپ می دهند، و می بافند. سپس آن را به یک نوع ماده چسبی آغشته می کنند، حرارت می دهند. و تحت فشار به صورت یکپارچه در می آورند. کفشک های ریخته شده و لنت ها نیز بدون یافتن، مستقیماً از آزبست و ماده چسبی ساخته می شوند.
ضمناً لنت ها را از چوب، چرم، پنبه کوهی نسوز نیز می سازند. که به وسیله پیچ های سر خزینه ای یا پرچ به کاسه چدنی یا فولادی بسته می شوند. و یا آنها را با چسب های مخصوص می چسبانند. جنس چرخ ها علاوه بر چدن بر حسب احتیاج، از فولاد زنگ نزن و آلومینیوم نیز ساخته می شود.
شکل 40-7 سیستم ترمز یک ماشین را نشان می دهد. که لنت در داخل کاسه چرخ بر روی کفشک ها نصب شده است.
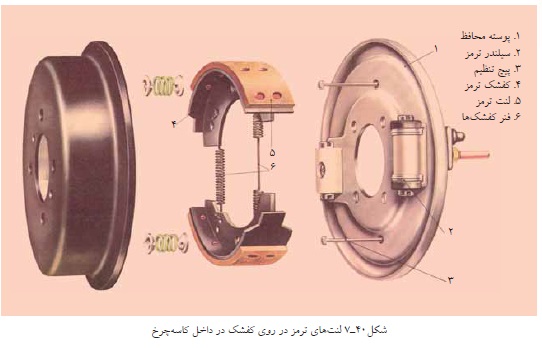
با سالها تجربۀ ارزشمند و گرانبها در عرصه تأمین و توزیع انواع ورق آلیاژی و انواع فولاد آلیاژی. و با گواهینامه ها و آنالیزهای معتبری که ضمیمه محصولاتش به مشتریان خویش میها می کند. توانسته رضایتمندی مشتریان خویش را همواره فراهم آورد.
صنعتگر شریف و گرامی از اینکه ما را جهت خرید کالا (فولاد آلیاژی) مورد نیاز خویش. انتخاب می نمایید از شما سپاسگزاریم.
ارتباط با ما
02128423820 – 09122136675
واتس آپ: 09122136675 – فکس: 02128423820
اینستاگرام: fooladdalakan
ایمیل : fooladrasuldalakan@gmail.com