خواص کششی 2542- اثر زمان عملیات زیر صفر عمیق روی ریزساختار
اثر زمان عملیات زیر صفر عمیق روی ریزساختار و خواص کششی فولاد ابزار 1.2542
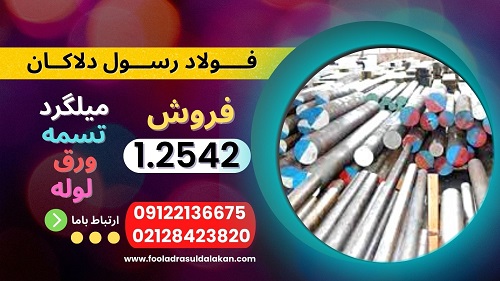
خواص کششی 2542
چکیده
برای افزایش کارآیی فولاد ابزار، دو گروه از خواص شامل سختی بالا اهمیت دارد. سختی ا چقرمگی در تقابل است. با استفاده از عملیات زیر صفر عمیق می توان برای افزایش همزمان سختی، استحکام و چقرمگی اقدام نمود. به همین منظور از 12 دسته نمونه فولاد ابزار 1.2542. 9 دسته به مدت 24، 36 و 48 ساعت در دمای 196-درجه سانتیگراد قرار گرفت. و سپس به مدت 3،2،1 ساعت در دمای 200 درجه سانتیگراد برگشت گردیدند.
و 3 دسته دیگر به عنوان نمونه استاندارد (شاهد) مد نظر قرار گرفت. در نهایت برای 12 دسته نمونه، عملیات زیر صفر عمیق مجددا تکرار شد. نتیجه آنکه برای نمونه ای که 36 ساعت در دمای 196- درجه سانتیگراد. و 1 ساعت در دمای 200 درجه سانتیگراد برگشت شده بود. (نمونه 361) به طور همزمان سختی 8/5 درصد، استحکام کششی 26/4 درصد، استحکام تسلیم 23/4 درصد و چقرمگی کششی 13/8 درصد. نسبت به نمونه استاندارد افزایش یافت.
مقدمه
خواص مطلوب برای افزایش کارآیی فولادهای ابزار شامل سختی، استحکام و مقاومت سایشی بالا و مقاومت ضربه ای بالا بطور همزمان می باشد. توانایی یک فلز برای برآوردن نیازهای فوق با خواص فیزیکی و مکانیکی آن تعیین می شود. خواص فیزیکی و مکانیکی فلز، وابستگی زیادی به ریزساختار آن دارد.
خواص کششی 2542
اغلب فولادهای ابزار نسبتاً دارای کربن زیاد می باشند. لذا عملیات حرارتی سختکاری و برگشت آنها منجر به تشکیل آستنیت باقیمانده در ریزساختار آن می شود. طی کار کرد قطعه بر اثر تنشهای مکانیکی وارده، آستنیت باقیمانده به مارتنزیت، استحاله می یابد. استحاله آستنیت باقیمانده به مارتنزیت تقریباً با 4 درصد افزایش حجم همراه می باشد. بر اثر این انبساط (به مقدار ناچیزی) ابعاد تغییر می کند. علاوه بر آن، انبساط در زمینه سبب اعوجاج و عیوب شده. که نهایتاً منجر به تشکیل ترک و نهایتاً کاهش عمر مفید مفید فولاد ابزار می گردد.
برای حل این مشکل، روشی به نام عملیات زیر صفر ابداع شد. مکانیزم اول در این عملیات، آستنیت باقیمانده به مارتنزیت تبدیل می شود. و در اثر این تبدیل یعنی انبساط ناشی از استحاله، چگالی تعداد نابجایی بالا می رود. در عملیات حرارتی برگشت، اتمهای کربن به سمت نزدیکترین نابجایی جذب می شوند. و در نتیجه غلظت بالایی از کربن در اطراف نابجایی ایجاد می شود. به این ترتیب مکان های مناسبی برای تشکیل کاربید ثانویه (Secondary Carbide) در دماهای پایین برگشت، حاصل می شود. نتیجه این عمل، کاهش مقدار آستنیت باقیمانده و افزایش تعداد ذرات کاربید ثانویه است که مقاومت سایشی و سختی کل را بهبود می دهد.
مکانیزم دوم در این عملیات، بر اثر اختلاف در ضریب انبساط حرارتی فازها، نابجایی جدید بوجود می آید. و این نابجایی جدید مکانهای مناسبی برای تشکیل کاربید ثانویه است. بطور مثال کاربیدهای اولیه (primary Carbide) بعنوان فازی با اختلاف ضریب انبساط حرارتی با زمینه مد نظر قرار می گیرد.
مکانیزم دوم در این عملیات، بر اثر اختلاف در ضریب انبساط حرارتی فازها. نابجایی جدید بوجود می آید و این نابجایی جدید مکان های مناسبی برای تشکیل کاربید ثانویه است. بطور مثال کاربیدهای اولیه (primary Carbide) بعنوان فازی با اختلاف ضریب انبساط حرارتی با زمینه در نظر گرفته می شود.
برای فولاد ابزار سردکار (Cr8Mo25iV) DIN 1.2379 حاوی 0.98 درصد کربن، 9.6 دهم درصد کروم. 2 درصد مولیبدن، 0.98 درصد سیلیسیم، و 0.5 درصد وانادیم و فولاد ابزار سردکار (Cr12MoV) DIN 1.2363. حاوی 1 درصد کربن، 12 درصد کروم و مقدار کمی مولیبدن و وانادیم. سختی نسبت به نمونه استاندارد آن، بین 1 تا 4 دردص زیاد شد. اما چقرمگی به یک سوم افت کرد. برای فولاد (815M17) DIN 1.6587 حاوی 0.17 درصد کربن، 1.9 درصد کروم. 1.05 درصد نیکل، 0.92 درصد منگنز و 0.11 درصد مولیبدن. استحکام نسبت به نمونه استاندارد آن، تقریباً تغییری نداشت. ازدیاد طول کمتر از 1 درصد (ناچیز) گزارش شد.
و سختی کل 3/4 RC زیاد شد. برخلاف سه محقق اخیر برای فولاد ابزار سردکار (Crg) DIN 1.2990 حاوی 1 درصد کربن. 8.1 درصد کروم، 2.1 درصد مولیبدن، 2.1 درصد وانادیم، 1 درصد تنگستن و 0.9 درصد سیلیسیم. در عملیات زیر صفر عمیق با کاهش دمای آستنیته، چقرمگی نسبت به عملیات مرسوم، افزایش یافت.
همچنین برای فولاد ابزار گرم کار (AISI H13) DIN 1.2344 حاوی 0.36 درصد کربن، 4.82 درصد کروم. 1.19 درصد مولیبدن، 0.96 درصد سیلیسیم و 0.86 درصد وانادیم. با 8 ساعت عملیات زیر صفر عمیق و 2 ساعت برگشت در دمای 560 درجه سانتیگراد، چقرمگی نسبت به عملیات مرسوم، 20 درصد افزایش یافت. برای فولاد مارایجینگ گروه 2800 مگاپاسکال حاوی 0.037 درصد کربن، 17.88 درصد. نیکل14.75 درصد کبالت، 6.69 درص مولیبدن و 1.1 درصد تیتانیم، با عملیات سرد در دمای 73- درجه سانتیگراد. و برگشت در دمای 470 تا 530 درجه سانتیگراد به مدت 4 ساعت، چقرمگی و استحکام بطور همزمان افزایش یافت.
نمایان شد که به هنگام تغییر شکل، در زمینه نرم فولاد، ذرات بین فلزی بیرون کشیده می شوند. علاوه بر آن، مشاهده شد که به هنگام سیاش، در زمینه نرم فولاد (AISI D2) DIN 1.2379. حاوی 1.54 درصد کربن، 11.88 درصد کروم، 0.76 درصد مولیبدن و 0.75 درصد وانادیم. ذرات کاربید ثانویه بیرون کشیده می شود. حال آنکه ذرات کاربید اولیه خرد می شوند. بنابراین ذرات کاربید ثانویه در زمینه نرم فولاد، رفتار کامپوزیتی دارند.
با توجه به مطالب اخیر، دلیل این اختلافات چیست؟ احتمالا محققینی که کاهش چقرمگی را گزارش کردند از شرایط عملیاتی مناسب برای ایجاد ریزساختار مناسب استفاده نکردند. چون دسته نمونه های آنها برای انجام شرایط عملیاتی، کافی نبوده است. در حالیکه محققینی که افزایش چقرمگی را گزارش کردند. اگرچه دسته نمونه های آنها کافی نبود اما بطور تصادفی (یا شاید آگاهانه چون در مقالات آنها دلیل انتخاب شرایط عملیاتی ذکر نشده بود). از شرایط عملیاتی مناسب برای این منظور استفاده کردند. لذا با این عملیات می توان چقرمگی، سختی و مقاومت به سایش را بطور همزمان افزایش داد. به این ترتیب یک هدف از این تحقیق، مطالعه شرایط عملیاتی و مکانیزم آن. برای ایجاد ساختار مناسب برای فولاد ابزار کم آلیاژ – کربن متوسط مورد تحقیق است.
در عملیات زیر صفر عمیق فولادهای ابزار، ریزساختار عمدتاً شامل کاربیدهای اولیه و ثانویه در زمینه مارتنزیت برگشت شده است. برای فولاد 1.2379 DIN با افزایش زمان عملیات زیر صفر مقدار کاربید اولیه ثایت باقی می ماند. در صورتیکه مقدار کاربیدهای ثانویه رو به افزایش است. با توجه به اینکه با انجام عملیات زیر صفر عمیق روی فولادهای ابزار گاها خواص مکانیکی و عمدتاً خواص سایشی بهبود می یابد. بنابراین کاربیدهای اولیه نسبت به کاربیدهای ثانویه، نقش کمتری در افزایش خواص مکانیکی دارند. لذا در این تحقیق، مطالعه روی کاربیدهای ثانویه مد نظر است. به این ترتیب، مکانیزم تشکیل و رشد کاربیدهای ثانویه، نحوه تشکیل، مکان تشکیل و سرعت رشد آنها را معین می کند. و کنترل و پیش بینی اندازه، مقدار و توزیع کاربیدهای ثانویه میسر شده. و در نهایت ساختار و در نتیجه خواص مطلوب حاصل می شود.
تاکنون تمرکز زیادی روی فولادهای ابزار پر کربن و پر آلیاژ صورت گرفته است. در حالیکه مقدار عناصر آلیاژی در فولاد ابزار مورد تحقیق کم بوده و مقدار کربن در حد متوسط است. بنابراین ریزساختار از نظر کیفی و کمی تفاوت دارد. حضور عناصر کاربید زای قوی مانند تنگستن و کروم سبب ایجاد انواع کاربید در ابعاد مختلف می شود. اندازه، شکل، چگالی تعداد ذرات و ترکیب شیمیایی این کاربیدها موضوع دیگر تحقیق است.
اگرچه در کتاب کلید فولاد برای فولاد ابزار مورد تحقیق، کوئنچ روغن و سپس برگشت در 450 درجه سانتیگراد (نمونه استاندارد) را توصیه نموده است. اما برای ایجاد نابجایی بیشتر (مکانهای بیشتر برای سهولت تشکیل کاربید ثانویه). و در نهایت برای دستیابی به خواص مطلوب تر با کوئنچ در آب و سپس عملیات زیر صفر عمیق و برگشت مقایسه می شود.
محققین زیادی تأثیر عملیات زیر صفر عمیق را روی خواص مکانیکی شامل سختی، استحکام کششی، چقرمگی و استحکام خستگی فولادهای ابزار مطالعه نموده اند. اما همه آنها بجز دو محقق، مطالعات ریزساختاری انجام نداده اند. در این تحقیق، این خلا تحقیقاتی پر می شود.
مواد و روش تحقیق
مواد فولاد ابزار 1.2542 (معادل AISI SI) عمدتاً برای ساخت تیغه برش ورق های ضخیم و همچنین بعنوان پانچ قالب برش کاربرد دارد. محدوده دمای کاری آن، با دمای کاری فولادهای ابزار گرم کار و سردکار هم پوشانی دارد. بنابراین جزو هر دو دسته محسوب می شود. که اهمیت کاربردی این فولاد ابزار را دو چندان می کند. در حال حاضر فولاد ابزار 1.2542 در کشور تولید می شود. به همین دلایل از نظر کاربردی، تعیین شرایط بهینه برای بهبود خواص مکانیکی فولاد ابزار 1.2542 در شرایط اعمال نیروی ضربه اهمیت پیدا می کند. ترکیب شیمیایی، در جدول (1) فهرست شده است.
خواص کششی 2542
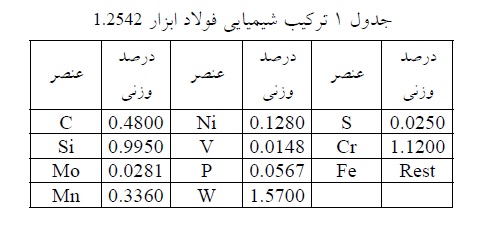
روش تحقیق، سه گروه تحقیقاتی مجزا، مجموعاً هشت متغیر برای عملیات زیر صفر عمیق معرفی کردند. که شامال زمانهای آستنیته و زیر صفر عمیق و برگشت دماهای آستنیته و زیر صفر و برگشت سرعتهای گرم و سرد کردن می باشد. در این تحقیق شش متغیر ثابت نگه داشته می شود. و فقط دو متغیر به نام های زمان زیر صفر عمیق و زمان برگشت، متغیر تحقیق در مد نظر قرار می گیرد. برای مطالعه ریزساختاری و خواص سختی، استحکام کششی و چقرمگی، 12 دسته نمونه که هر دسته شامل 3 نمونه است استفاده شد. تا برای نتیجه گیری مطلوب، اطلاعات مناسب و کافی فراهم باشد.
عملیات زیر صفر عمیق و همچنین برگشت آن با کمک دستگاه کرایو جنیک قابل برنامه ریزی انجام شد. این دستگاه در دانشکده مکانیک سازمان پژوهش های علمی و صنعتی ایران طراحی و تولید گردید. فاصله زمانی بین عملیات کوئنچ (سخت کاری) و عملیات زیر صفر عمیق، 17 دقیقه بود که با زمان سایر محققان تطابق خوبی دارد. با توجه به قابلیت این دستگاه، برگشت در خود دستگاه انجام میشود. لذا فاصله زمانی بین گرم شدن نمونه ها از دمای زیر صفر و سپس دمای محیط تا دمای برگشت (200 درجه سانتیگراد)، 2 دقیقه بود. کد گذاری نمونه ها در جدول 2 و جدول 3 شرح داده شده است.
فرایند انجام کار برای بررسی ریز ساختاری، سختی، خواص کششی و چقرمگی در شکل (1) نمایان و مشخص است.
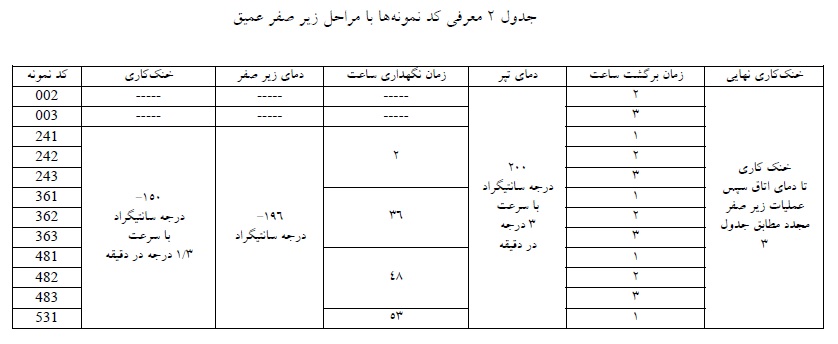
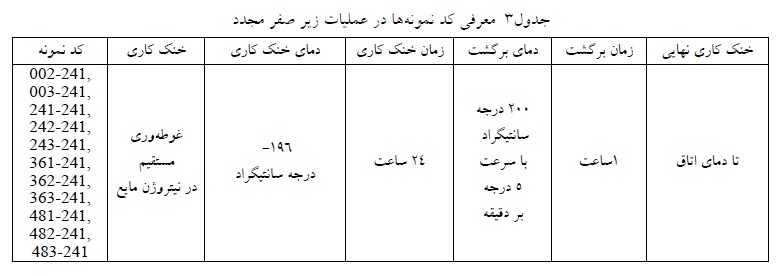
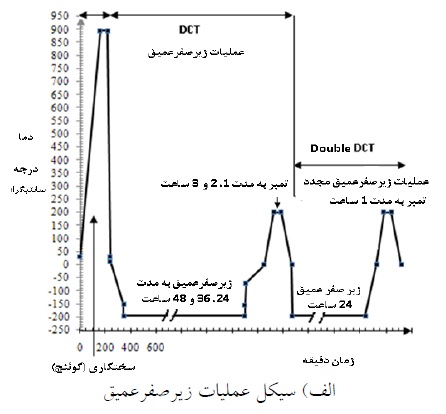

نمونه های تست کشش مطابق استاندارد BS EN 10002-1. به شکل دمبل با قطر (d) 5 میلیمتر، طول مبنا اولیه (L) 50 میلیمتر و طول کل (Lt) 15 سانتیمتر تهیه و در جدول 4 ثبت گردید. آزمون کشش با نرخ کرنش 0.00166 – بر ثانیه انجام شد. تراشکار نمونه ها با استفاده از دستگاه تراش CNC قبل از انجام عملیات زیر صفر عمیق انجام شد.
خواص کششی 2542
برای مطالعات ریزساختاری، نمونه ها استوانه ای شکل به قطر 12 میلیمتر و طول 15 میلیمتر بود. و برای بخشی از مطالعه ریزساختاری از دستگاه تفرق اشعه ایکس philips با هدف مس در ولتاژ 40 کیلو ولت (λCu, Kα) استفاده شد.
برای تهیه تصاویر میکروسکوپ الکترونی روبشی از دستگاه TESCAN MIRA II همراه با آنالیز طیف تفکیک انرژی استفاده شد. علاوه بر آن، از نرم افزار متالوگرافی OLYSIA m3 که برای 1536×2048 پیکسل کالیبره شده بود برای آنالیز فازی تصاویر استفاده شد. برای هر محاسبه فازی، حداقل از 5 تصویر میکروسکوپ الکترونی روبشی با بزرگنمایی 104 از یک منطقه، استفاده. و میانگین داده ها در جدول (5 و 6) گزارش شده است.
میکروسکوپ الکترونی عبوری روبشی، روشی مطمئن تر و با کیفیت تر از روش میکروسکوپ الکترونی روبشی است. نمونه های میکروسکوپ الکترونی عبوری روبشی بصورت دیسک های 3 میلی متری با وایرکات تهیه و تا ضخامت 100 نانومتر پولیش دستی شد. سپس با دستگاه سنگ زنی بصورت هلالی در آمد و در آخر، با بمباران یونی بهمراه خنک کننده با دستگاه Gatan pips، سوراخ شد.
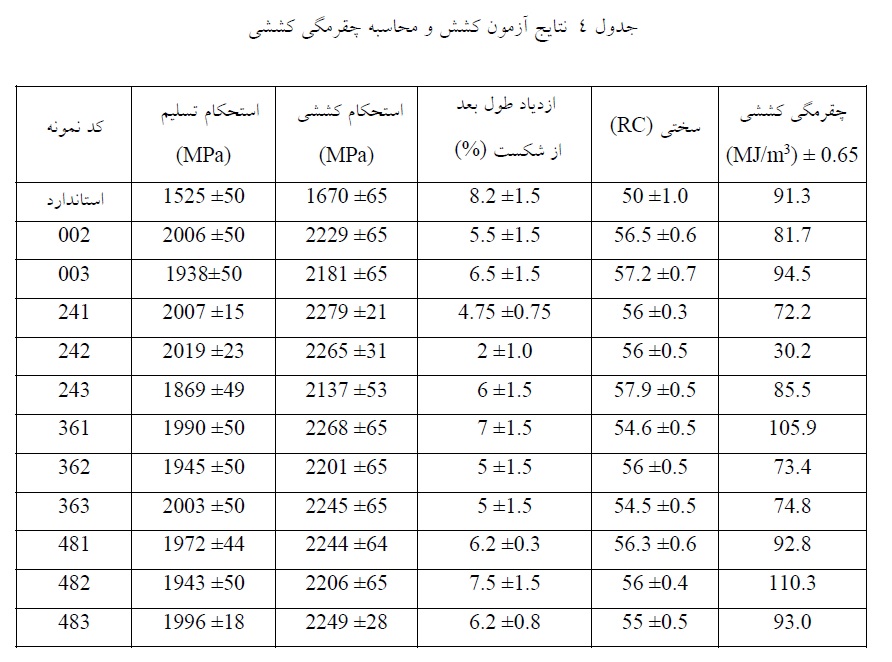
خواص کششی 2542
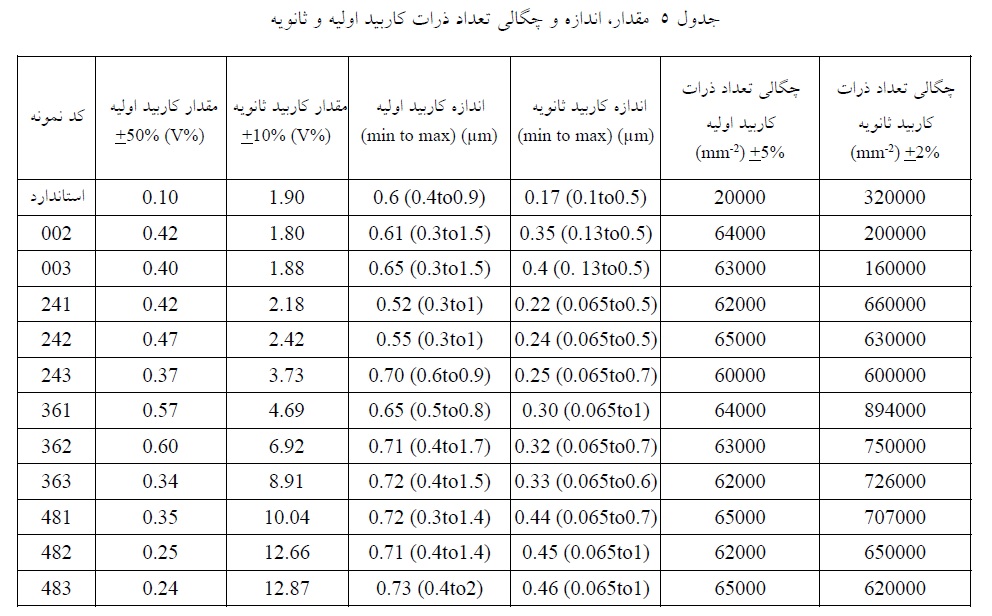
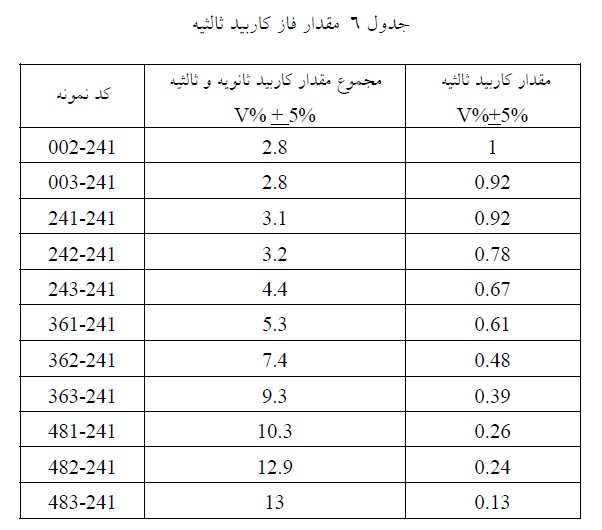
نتایج و بحث
سختی، استحکام کششی و چقرمگی کششی نتایج آزمون کشش، سختی و ریزساختاری به ترتیب در جدول (4، 5، 6) فهرست و نمایان و مشخص است.
نتایج آزمون کشش و چقرمگی کششی نمونه ها مطابق معادله 1 محاسبه و در جدول (4) فهرست و نمایان و مشخص است. UTS، استحکام کششی و ef، کرنش شکست است.

در جدول 4، برای تمام نمونه های زیر صفر عمیق، استحکام کششی و تسلیم تغییری نکرده و تقریباً ثابت بود. زیرا مطابق جدول (5 و 6)، با افزایش زمان زیر صفر عمیق یا برگشت، کاربیدهای ریز بسیار سخت در زمینه افزایش می یابد. از طرف دیگر، زمینه که از عناصر آلیاژی و کربن فقیر شده است. به نسبت نرم تر می شود. تقابل تغییرات در این دو متغیر ریزساختاری، موجب ثابت ماندن استحکام کششی و تسلیم می شود. در حالیکه نمونه استاندارد، نسبت به نمونه های زیر صفر، 32 تا 36 درصد استحکام کششی کمتر و 9 تا 12 درصد سختی کمتری دارد. زیرا نمونه استاندارد در روغن کوئنچ شده در حالیکه نمونه های زیر صفر در آب کوئنچ شده اند.
در جدول 4، سختی نمونه 242 در مقایسه با نمونه استاندارد، 12 درصد دچار افزایش شد. زیرا نمونه 242 در آب کوئنچ شده است. در حالیکه نمونه استاندارد در روغن کوئنچ شد. بنابراین سختی بیشتری دارد. همچنین نمونه 242 نسبت به نمونه های 002 و 003 تقریباً سختی یکسانی دارند. چون هر دو در آب کوئنچ شدند.
خواص کششی 2542
مشابه نمونه 243 در این تحقیق، استحکام نمونه های DIN 1.6587 در مقایسه با نمونه استانداردش تغییری نکرد. و ازدیاد طول نمونه های زیر صفر کمتر از 1 درصد است. و سختی این نمونه ها 2/4 درصد افزایش نشان می دهد. آنها فقط دو دسته نمونه داشتند. که به مدت 1 و 2 ساعت در دمای زیر صفر عمیق، 196- درجه سانتیگراد قرار گرفت. و سپس به مدت 2 ساعت در دمای 180 درجه سانتی گراد برگشت شد.
در جدول 4، نمونه های کوئنچ شده در آب نسبت به نمونه استاندارد حدود 10 درصد سختی بیشتری دارند. مطابق همان جدول، نمونه 243 بیشترین سختی و نمونه 363 کمترین سختی را بخود اختصاص داد.
خواص کششی 2542
بر اساس جدول 4، مشخص می شود با کاهش زمان عملیات زیر صفر عمیق. مدت زمان برگشت نمونه ها برای دستیابی به سختی بیشتر، افزایش می یابد. بطور مثال برای دستیابی به سختی بیشتر نمونه هایی که 1 ساعت برگشت می شوند. 48 ساعت برای عملیات زیر صفر عمیق لازم است. در حالیکه برای دستیابی به سختی بیشتر نمونه هایی که 2 ساعت برگشت می شوند. تقریباً 24 ساعت برای عملیات زیر صفر عمیق لازم است. و بیشتر از آن فایده ای ندارد. یعنی برای دستیابی به سختی بیشتر با افزایش زمان برگشت، زمان زیر صفر عمیق کمتری لازم است.
زیرا در دمای برگشت بدلیل پدیده نفوذ اتمهای کربن در کسری از فاصله اتمی به سمت نابجایی، کاربیدهای ثانویه ریز بیشتری تشکیل می شود. شاید به نظر برسد در دمای برگشت پایین مثلاً 200 درجه سانتیگراد، سرعت نفوذ اتمهای کربن قابل توجه نیست. لازم به ذکر است اگرچه سرعت نفوذ اتمهای کربن در دمای برگشت 200 درجه سانتیگراد، کم است. اما فاصله نفوذ نیز بسیار کوتاه است. و لذا مطابق جدول (5 و 6)، نانو ذرات کاربید ثانویه پدید می آید.
خواص کششی 2542
در جدول (4)، برای دستیابی به سختی بیشتر با افزایش زمان زیر صفر عمیق، زمان لازم برای برگشت نمونه ها کاهش پیدا می کند. بطور مثال برای دستیابی به سختی بیشتر نمونه هایی که 24 ساعت زیر صفر عمیق می شوند 3 ساعت زمان برای عملیات برگشت لازم است. در حالیکه برای دستیابی به سختی بیشتر نمونه هایی که 36 ساعت زیر صفر عمیق میشوندو 2 ساعت زمان برای عملیات برگشت لازم است.
و برای دستیابی به سختی بیشتر نمونه هایی که 48 ساعت زیر صفر عمیق می شوند. 1 ساعت زمان برای عملیات برگشت لازم است. زیرا با افزایش زمان زیر صفر عمیق تعداد اتمهای کربنی که منجر به آرایش نابجایی شدند. افزایش می یابد. و لذا مدت زمان لازم برای برگشت کاهش می یابد. بنابراین برای دستیابی به سختی بیشتر به منظور افزایش سرعت تولید و یا کاهش زمان تولید هر محصول بهتر است. زمان برگشت زیاد شود. تا زمان لازم برای تولید کاهش یابد.
در مرجع برای فولاد ابزار DIN 1.2379 چقرمگی شکست نمونه های زیر صفر عمیق. نسبت به نمونه با عملیات متداول حدود 7 درصد کاهش می یابد. در حالیکه در تحقیق حاضر، در جدول 4 یا معادله 1. برای نمونه های 361 و 482، 12 تا 35 درصد افزایش چقرمگی کششی مشاهده می شود.
دلیل این تفاوت بر دو دلیل استوار است. اولاً فولاد ابزار DIN 1.2379 یک فولاد ابزار پر آلیاژ و پر کربن است. در حالیکه فولاد مورد تحقیق کم آلیاژ و متوسط کربن است. این تفاوت منجر به تفاوت زیادی در ریزساختار این دو آلیاژ یعنی مقدار و اندازه ذرات کاربید و آستنیت باقیمانده می شود. مقدار و اندازه ذرات کاربید و آستنیت باقیمانده میشود. مقدار و اندازه ذرات کاربید ثانویه در نهایت روی سطح مؤثر آنها اثر می گذارد. ثانیاً آنها چقرمگی شکست را مطالعه کردند. در حالیکه در این تحقیق مدول چقرمگی (چقرمگی کششی) مطابق معادله 1 مورد بررسی قرار گرفت.
یافته های سه محقق در تطابق با یافته این تحقیق برای شرایط عملیاتی نمونه های 361 و 482 است. زیرا نمونه های 361 و 482 مطابق معادله 1، نسبت به نمونه استاندارد. و نمونه های 002 و 003 ، 12 تا 35 درصد چقرمگی کششی بیشتری دارند.
برای دستیابی به چقرمگی کششی بیشتر با افزایش زمان زیر صفر عمیق، زمان برگشت نیز افزایش یافت. به عبارت دیگر، با 36 ساعت زیر صفر عمیق به 1 ساعت برگشت نیاز بود. تا چقرمگی کششی افزایش یابد. و همچنین با 48 ساعت زیر صفر عمیق به 2 ساعت برگشت نیاز بود. زیرا تنش های باقیمانده بعد از عملیات زیر صفر عمیق نسبت به عملیات مرسوم، بیشتر کاهش می یابد. به عبارت دیگر زمان زیر صفر عمیق بیشتر، نابجایی بیشتری تولید می کند. و نابجایی بیشتر، مطابق جدول (5 و 6)، نیازمند زمان بیشتر برای تولید نانو ذرات کاربید ثانویه هستند.
ریز ساختار، دمای شروع تشکیل مارتنزیت 274/6 درجه سانتیگراد و دمای پایان آن 59/6 درجه سانتی گراد است.
زیرا با توجه به نوع و مقدار عناصر آلیاژی فولاد مورد تحقیق دمای شروع و پایان استحاله مارتنزیتی. از معادله 2 و 3 (payson and savage) بدست می آید.
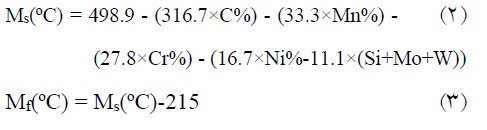
بنابراین در دمای 196- درجه سانتیگراد بایستی آستنیت باقیمانده کاملاً به مارتنزیت تبدیل شود. در شکل (2) با استفاده از دستگاه تفرق اشعه ایکس philips با هدف مس در ولتاژ 40 کیلو ولت (λCu, Kα). از نمونه های استاندارد، 483، 343، 002 مشاهده شد. که در هیچ یک از نمونه ها، آستنیت باقیمانده وجود ندارد.
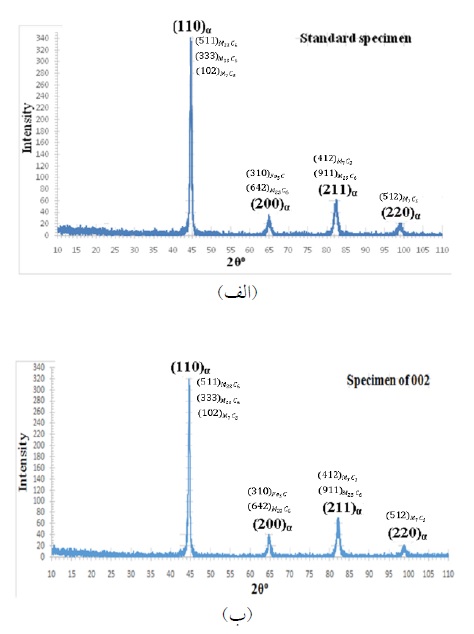
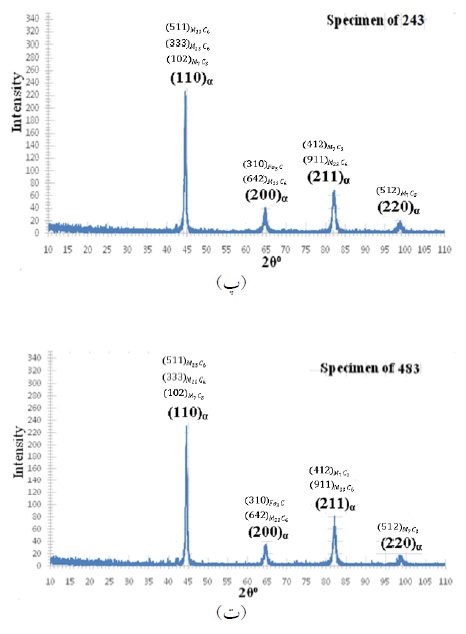
تشکیل کاربیدهایی با ترکیب شیمیایی M7C3 و M23C6 در طی عملیات زیرصفر عمیق توسط محققین زیادی گزارش شده است. اما هیچگاه بروش طیف سجنی تفکیک انرژی مورد مطالعه قرار نگرفتند. شکل (3-الف) در تصویر میکروسکوپ الکترونی روبشی کاربیدهای روشن و تیره با حروف انگلیسی A،B،C و زمینه با حروف انگلیسی D مشخص شده اند. شکل های (3 ب و 3 پ و 3 ت) نمودار طیف تفکیک انرژی این کاربیدها به ترتیب مشخص می شود.
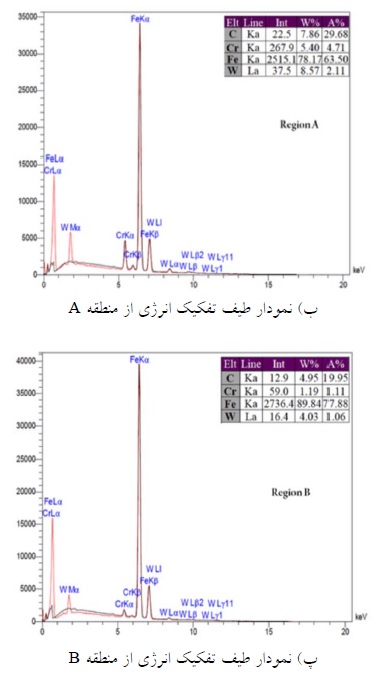
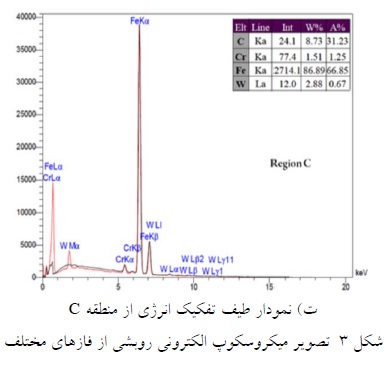
خواص کششی 2542
کاربیدهای اولیه نسبت به کاربیدهای ثانویه کربن بیشتری دارند. زیرا وقتی کاربید اولیه تشکیل می شود. زمینه غنی از کربن است. وقتی کاربید اولیه تشکیل شد مقداری از کربن زمینه را مصرف می کند. لذا برای کاربید ثانویه، کربن کمتری باقی می ماند. بنابراین منطقه B که کربن کمتری دارد. کاربید ثانویه با ترکیب شیمیایی M23C6 است. زیرا مقدار کربن در این ترکیب از نظر تئوری برابر است با 20/99 درصد اتمی

که با نتیجه ارایه شده از طیف تفکیک انرژی این منطقه در شکل (3-پ) یعنی 19/95 درصد اتمی بسیار نزدیک است. از طرف دیگر مناطق A,C که کربن بیشتری دارد. کاربید اولیه با ترکیب شیمیایی M7C3 است. زیرا مقدار کربن در این ترکیب از نظر تئوری برابر است با 30 درصد اتمی

که با نتیجه ارایه شده از طیف تفکیک انرژی این منطقه در شکل های (3ب و 3 ت). یعنی 29/68 و 31/23 درصد اتمی نزدیک است.
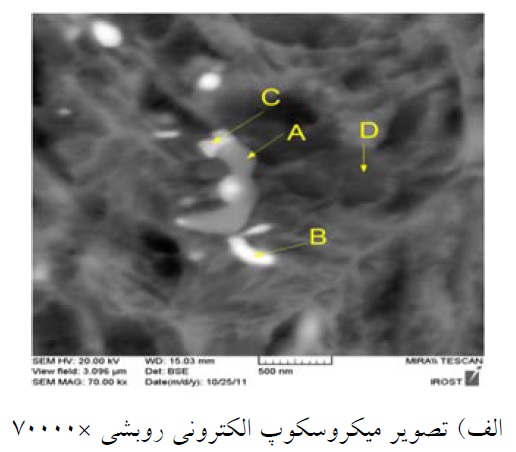
عدد اتمی هر ذره از مجموع حاصلضرب درصد اتمی عنصر تشکیل دهنده ذره (شکل های 3 ب و پ و ت). در عدد اتمی آن عنصر بصورت یک به یک بدست می آید. به این ترتیب، در شکل (3-الف)، ذرات غنی از عناصر با عدد اتمی بیشتر، روشن تر هستند. زیرا ذرات روشن یعنی ناحیه B، دارای عدد اتمی تقریباً

22.5= بیشتر حاوی تنگستن و آهن و کمتر حاوی کروم و کربن است. ذرات غنی از عناصر با عدد اتمی کمتر، تیره تر هستند. زیرا ذرات تیره تر یعنی نواحی A،C، به ترتیب دارای عدد اتمی تقریباً
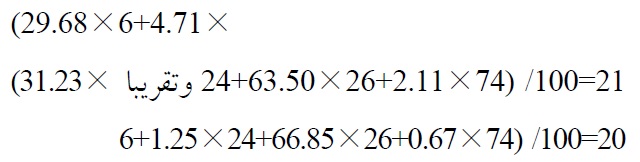
بیشتر حاوی کروم و کربن و کمتر حاوی آهن و تنگستن است.
در شکل (4) تصویر میکروسکوپ الکترونی روبشی از نقشه پراکندگی اتمهای کروم، تنگستن و سیلیسیم در یک ناحیه به نمایش گذاشته شده است. که موید توزیع یکنواخت کاربیدها است.
خواص کششی 2542
تعداد مول یک عنصر از تقسیم مقدار عنصر (بر حسب گرم) بر جرم ملکولی عنصر (بر حسب گرم بر مول) بدست می آید. لذا در 100 گرم از آلیاژ مورد تحقیق مطابق جدول (1). 0/00854 مول اتم تنگستن، 0/03571 مول اتم سیلیسیم و 0/02154 مول اتم کروم وجود دارد. در یک مساحت مشخص، تعداد اتمها با فاصله آنها از همدیگر رابطه عکس دارد. به عبارت دیگر، فاصله اتم های تنگستن نسبت به کروم برابر است با نسبت تعداد اتمهای کروم به تعداد اتمهای تنگستن یعنی 2/52 (=0/00854÷0/02154). همچنین، فاصله اتمهای تنگستن نسبت به سیلیسیم برابر است با نسبت تعداد اتمهای سیلیسیم به تعداد اتمهای تنگستن یعنی 4/18 (=0/00854÷0/03571). لذا پراکندگی اتمهای تنگستن نسبت به کروم 2/52 برابر و نسبت به سیلیسیم 4/18 برابر است.
در جدول (5)، میانگین مقدار کاربید اولیه برای نمونه های زیر صفر شده ثابت و برابر 0/2+0/4 درصد حجمی است. (زیرا برای یک آلیاژ مشخص، فقط شرایط آستنیته کردن در تشکیل کاربید اولیه دخیل است. که در این تحقیق شرایط آستنیته کردن ثابت در مد نظر قرار گرفت). در حالیکه با افزایش زمان زیر صفر عمیق یا زمان برگشت، مقدار کاربید ثانویه از 1/9 تا 12/87 درصد حجمی دائماً رو به افزایش است.
خواص کششی 2542
در جدول (5)، افزایش مقدار کاربید ثانویه با تغییر زمان زیر صفر عمیق (میانگین 500 درصد). نسبت به تغییر زمان برگشت (میانگین 50 درصد)، سرعت بسیار بیشتری دارد. زیرا عامل اصلی تشکیل کاربید ثانویه، افزایش چگالی تعداد نابجایی است که بهنگام قرارگیری در دمای زیر صفر عمیق رخ می دهد. از طرف دیگر، مقدار کاربید ثانویه در نمونه های 002 و 003 تقریباً ثابت است. زیرا بدون انجام عملیات زیر صفر عمیق شرایط برای تشکیل کاربید ثانویه مهیا نمی شود.
بمنظور صحه گذاری فرضیه دوم مکانیزم رسوب گذاری کاربید ثانویه، نمونه هایی که پس از زیر صفر شدن، آستنیت باقیمانده در آنها حذف شد. اما حاوی ذرات کاربید اولیه (M7C3) و ثانویه (M23C6) بودند. در دمای 196- درجه سانتیگراد به مدت 24 ساعت مجدداً زیرصفر میشود. و سپس در دمای 200 درجه سانتیگراد به مدت 1 ساعت برگشت شده اند.
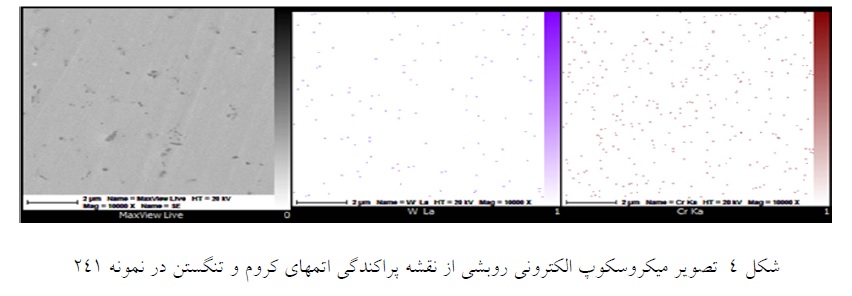
در شکل (5) تصویر میکروسکوپ الکترونی روبشی با اشغه الکترون برگشتی نمونه ها نمایان و مشخص است. و در نمونه ها مقدار زیادی ذرات کاربید ثانویه (Tertiary Carbide) با ترکیب M23C6 (ذرات سفید). در اطراف ذرات کاربید اولیه (ذرات کدر) و شاید کاربید ثانویه قبلی، تشکیل شد. با تلفیق این مطلب و با توجه به این نکته که مقدار ذرات کاربید M23C6 با عملیات زیرصفر مجدد، دچار افزایش گردید. (جدول 5 و جدول 6) فرضیه دوم مکانیزم رسوبگذاری کاربید ثانویه صحه گذاری میشود.

کاربیدهای ثالثیه با همان ترکیب کاربید ثانویه متشکل و در جدول (5 و 6). مقدار آن از تفاضل مقدار کاربید ثانویه قبل و بعد از عملیات زیر صفر مجدد بدست می آید. با افزایش زمان زیر صفر، مقدار کاربید ثانویه بیشتر میشود. لذا زمینه از عناصر آلیاژی و کربن، فقیرتر می شود. بنابراین در عملیات زیر صفر مجدد، تشکیل کاربید ثالثیه مشکلتر میشود. این مطلب به وضوح در جدول 5 و جدول 6 نمایان و مشخص است. یعنی قبل و بعد از عملیات زیرصفر مجدد با افزایش زمان زیر صفر، مقدار کاربید ثالثیه کاهش می یابد.
در جدول (5)، چگالی تعداد ذرات کاربید اولیه و ثانویه ترسیم شده است. چگالی تعداد ذرات کاربید اولیه تقریباً ثابت و میانگین آن برابر با 64000 ذره در هر میلیمتر مربع است. این مطلب بویژه در مورد نمونه هایی که 36 و 48 ساعت زیر صفر عمیق شدند، صدق می کند.
در جدول (5)، چگالی تعداد ذرات کاربید ثانویه با 36 ساعت زیر صفر عمیق به حداکثر می رسد. بعلاوه، با 1 ساعت برگشت بیشترین چگالی تعداد ذرات کاربید ثانویه حاصل شد. توجیه علمی این مطلب بر اساس دو مکانیزم ارایه شده، بصورت زیر است.
برای مکانیزم اول، وقتی زمان برگشت ثابت است با افزایش زمان زیر صفر عمیق، حجم مارتنزیت کاهش پیدا می کند. و شبکه آن منقبض می شود. بهمین دلیل کربن خارج میشود و در کنار نزدیکترین نابجایی آرایش می یابد. با افزایش زمان زیرصفر عمیق، منطقه آرایش یافته گسترش می یابد. با هم تلاقی می نماید و لذا ذرات کاربید ثانویه بزرگتر می شوند. برای مکانیزم دوم، با افزایش زمان زیر صفر عمیق، بدلیل اختلاف در انقباض فازها، چگالی تعداد نابجایی افزایش می یابد.
با افزایش چگالی تعداد نابجایی، منطقه ای که در آن چگالی تعداد نابجایی زیاد می گردد. گسترش می یابد و ذرات بزرگتر می شوند. تا زمانیکه این مناطق در حال گسترش با هم برخورد نکنند. مقدار ذرات کاربید ثانویه و چگالی تعداد آنها و اندازه آنها زیاد می شود. (این حالت تا 36 ساعت زیر صفر عمیق وجود دارد) اما پس از برخورد (شکل6). مقدار و اندازه ذرات کاربید ثانویه زیاد شده اما از چگالی تعداد آنها کاسته می گردد. (این حالت در 48 ساعت زیر صفر رخ می دهد).
خواص کششی 2542
شکل 6 الف نمونه 531 را که 53 ساعت زیر صفر و 1 ساعت برگشت شده را نشان می دهد. مشاهده می شود که حداقل 3 ذره با هم تلاقی کرده اند. شکل (6) ب نمونه 483 را نشان می دهد. در این شکل تعدادی از ذرات کاربید ثانویه با هم تلاقی کرده اند. و در برخی مکان ها در حال تلاقی هستند. لذا چگالی تعداد ذرات آنها کاهش یافت. در جدول (5)، با افزایش زمان زیر صفر عمیق، اندازه ذرات کاربید ثانویه نسبتاً بیشتر (میانگین 90 درصد) افزایش می یابد.
زیرا عامل اصلی تشکیل کاربید، افزایش چگالی تعداد نابجایی است که بهنگام قرارگیری در دمای زیرصفر عمیق رخ می دهد. در حالیکه در زمان برگشت، سرعت نفوذ بسیار کم می باشد. زیرا دمای برگشت پایین است. علاوه بر آن، مناطق کاربید اولیه نسبتاً فقیر از عناصر آلیاژی و کربن هستند. زیرا ذرات کاربید اولیه نسبتاً کربن زیاد دارند. و به نسبت از ذرات کاربید ثانویه بزرگتر هستند.
در جدول 5، با افزایش زمان برگشت، اندازه ذرات کاربید ثانویه بطور جزئی (10 درصد) افزایش می یابد. وقتی تعداد ذرات کاربید ثانویه در واحد حجم خیلی زیاد شد. فاصله ذرات از هم کم می شود. به این ترتیب پیوستن ذرات کاربید ثانویه بر اثر نفوذ ممکن می شود. که در نتیجه چگالی تعداد ذرات کاربید ثانویه مقداری کمتر می شود. و اندازه ذرات کاربید ثانویه مقدار ناچیزی بزرگتر می شود. کاووش فوق در جدول (5) با استفاده از رابطه (4)، نیز قابل پیش بینی است.

بطوریکه r شعاع ذرات، k عددی ثابت (برای ذره مشخص و در دمای ثابت) و t زمان است. بنابراین نانو ذرات بسیار ریز کاربید ثانویه، در ابتدا بسیار سریع رشد می کنند. و ذرات زیر میکرون نسبتاً بزرگتر کاربید ثانویه، نسبتاً سرعت رشد کمتری دارند.
خواص کششی 2542
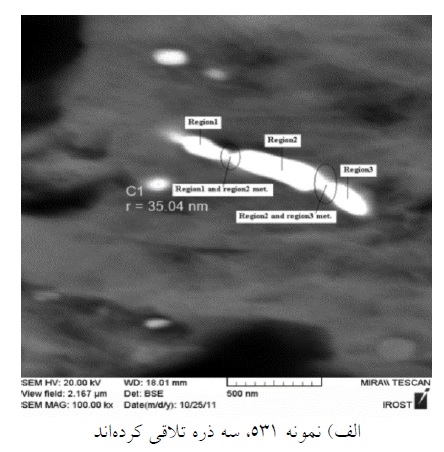
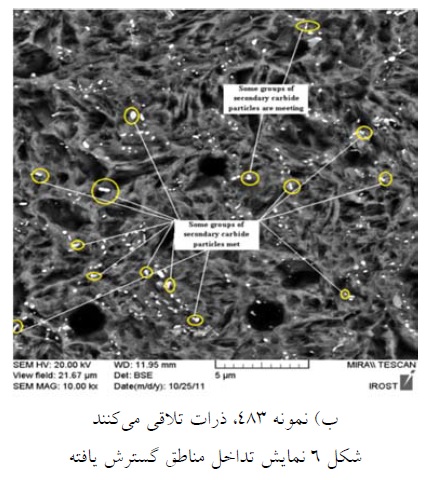
با مقایسه مشخصات ذرات کاربید ثانویه در نمونه 361 با نمونه های زیر صفر نشده. (مانند 002 یا 003 یا استاندارد) در می یابیم که مقدار ذرات کاربید ثانویه در نمونه 361. حداقل 125 درصد و چگالی تعداد این ذرات حداقل 350 درصد افزایش یافت. با توجه به کاهش حداقل 30 درصدی میانگین اندازه ذرات، با قاطعیت نتیجه حاصل می شود. که عملیات زیرصفر عمیق، کاربیدهای ثانویه را هموژن تر نموده است.
در جدول (5)، اندازه کاربید اولیه در تمام 12 دسته نمونه تقریباً ثابت است. از طرف دیگر، در جدول 5، چگالی تعداد ذرات کاربید اولیه در نمونه استاندارد، تقریباً نصف آن در سایر نمونه ها است. بنابراین مقدار آن در نمونه استاندارد باید نصف مقدار آن در سایر نمونه ها باشد. این مطلب در جدول (5) (به مقدار 0/10 درصد حجمی) صحه گذاری می شود.
خواص کششی 2542
در جدول (5)، اندازه ذرات کاربید ثانویه در نمونه استاندارد کوچکتر از (تقریباً نصف) نمونه های 002 و 003 است. در جدول (5)، چگالی تعداد ذرات کاربید ثانویه در نمونه استاندارد. بیشتر از (تقریباً دو برابر) نمونه های 002 و 003 و کمتر از نمونه های زیرصفر گردید. بهمین دلیل می توان پیش بینی کرد که مقدار این ذرات در نمونه استاندارد و نمونه های 002 و 003 تقریباً یکسان باشد. این مطلب در جدول (5) (به مقدار 1/9 درصد-حجمی) صحه گذاری می شود.
در این تحقیق با استفاده از میکروسکوپ الکترونی عبوری در دانشگاه الیالت آریزونای آمریکا. JEOL ARM Atomic Resolution Microscope در ولتاژ 200 کیلو ولت با نرم افزار AppFive Topspin. از نمونه 483 تحلیل تفرق دقیق انجام شد. برای نمونه 483، در شکل (7-الف)، با مطالعات دقیقتری که توسط میکروسکوپ الکترونی عبوری روبشی. با اسکن حداقل 1000 دانه و حدود 970000 تفرق اشعه الکترونی انجام شد. مقادیر ناچیزی (کمتر از 0/2 درصد – حجمی یعنی

آستنیت باقیمانده به رنگ سبز به شکل تیغه ای به طول حداکثر 130 نانومتر و به ضخامت حداکثر 10 نانومتر یافت شد. مطابق شکل (7-ب)، هسته 50 نانویی ذره کاربید آهن کروی شکل و در شکل (7-پ). ذرات زیرمیکرونی کاربید با ترکیب M7C3 تقریباً به شکل کروی می باشد.
در شکل (7-ت)، نقشه پراکندگی فازها با کمک میکروسکوپ الکترونی عبوری روبشی در سطحی به اندازه تقریبی 80000 نانومتر مربع آورده شده است. در این نقشه، کاربیدهای M7C3،M23C6،Fe3C،Cr3C2 و M6C. (با فلش کج) شناسایی شده است. بعلاوه، آستنیت باقیمانده (با فلش توخالی) و زمینه نیز نمایان و کاملاً مشخص است. به این ترتیب کاربیدهایی که در میکروسکوپ الکترونی روبشی شناسایی نشد. ( کاربیدهای Cr3C2،Fe3C و M6C) در میکروسکوپ الکترونی عبوری روبشی شناسایی شد.
سید ابراهیم وحدت-سعید ناطق-شمس الدین میردامادی تهرانی (نشریه مهندسی متالورژی و مواد)
فولاد رسول دلاکان
با سالها تجربۀ ارزشمند و گرانبها در عرصه تأمین و توزیع انواع ورق آلیاژی و انواع فولاد آلیاژی. و با گواهینامه ها و آنالیزهای معتبری که ضمیمه محصولاتش به مشتریان خویش میها می کند. توانسته رضایتمندی مشتریان خویش را همواره فراهم آورد.
صنعتگر شریف و گرامی از اینکه ما را جهت خرید کالا (فولاد آلیاژی) مورد نیاز خویش. انتخاب می نمایید از شما سپاسگزاریم.
ارتباط با ما
02128423820 – 09122136675
واتس آپ: 09122136675 – فکس: 02128423820
اینستاگرام: fooladdalakan
ایمیل : fooladrasuldalakan@gmail.com