اثر فلز پر کننده بر خواص مکانیکی و تریبولوژیکی اتصال فولاد AISI 1/6959
اثر فلز پر کننده
اثر فلز پر کننده بر خواص مکانیکی و تریبولوژیکی اتصال فولاد AISI 1/6959 با استفاده از فرایند جوشکاری تیگ
چکیده
در این پژوهش خواص مکانیکی و تریبولوژیکی جوش حاصل از چهار نوع فلز پر کننده مختلف. بر روی فولاد AISI 1/6959 از طریق جوش تیگ مورد بررسی قرار گرفت. فلزهای پرکننده مورد استفاده در این تحقیق شامل ER 70S-6,ER 80S-G,ER 80S-Ni1,ER 80S-B2 بوده و ترکیبات شیمیایی نزدیک به فلز پایه دارند. به منظور بررسی خواص جوش و کیفیت اتصال، آزمون های کشش، ضربه، سختی و سایش. با استفاده از دستگاه های کشش و ضربه و سایش انجام گردید. و ساختار میکروسکوپی نیز توسط میکروسکوپ نوری مورد مطالعه قرار گرفت.
اثر فلز پر کننده
نتایج حاصل حاکی از آن است که تغییرات فازی و حضور عناصر آلیاژی مولیبدن و کروم، منجر به تغییر در خواص اتصال جوش دهی شد. بیشترین و کمترین مقاومت به سایش به ترتیب در جوش حاصل از فلز پرکننده ER 80S-Ni1 و ER 70S-6. و بهترین کیفیت جوش و خواص مکانیکی با استفاده از فلز پر کننده ER 80S-B2 حاصل گردید. و استحکام کششی نیز تا حدود 38 درصد نسبت به فلز پایه بهبود یافت.
1- مقدمه
جوشکاری یکی از مهمترین فرایندهای ساخت و تولید در صنعت می باشد. و در صنایع مختلف نظیر خودروسازی، نفت و گاز، پتروشیمی، تأسیسات، ساختمان و پل ها، حمل و نقل. کشتی سازی، صنایع ریلی، نیروگاه ها، صنایع دفاعی و هوافضا، محصولات پزشکی. الکترونیکی و تجهیزات دقیق و غیره کاربردهای فراوانی دارد. اتصال فلزات با ترکیب شیمیایی، خواص فیزیکی و مکانیکی متفاوت باعث پیدایش مشکلات زیادی در طول فرایند جوشکاری یا بعد از آن می گردد.
این اختلاف ترکیب شیمیایی می تواند بین دو فلز پایه یا بین فلزات پایه با فلز پر کننده باشد. که در نتیجه ترکیب فلز جوش متأثر از تمامی اجزا تشکیل دهنده آن خواهد بود. این ترکیب شیمیایی با توجه به طراحی اتصال، نوع فرایند جوشکاری و فلز پرکننده و میزان اختلاط و دستورالعمل جوشکاری تغییر می کند. در نتیجه این عوامل و همچنین هرگونه عملیات حرارتی فلز جوش باید از قبل مشخص بشود. و قبل از تولید به طور صحیحی ارزیابی و اجرا شود. هدف اصلی از جوشکاری فلزات غیر هم جنس نیز ایجاد اتصالی است که الزامات شرایط کاری را برآورده می کند.
اثر نوع فلاکس فعال کننده سطحی بر عرض گرده و عمق جوش و پیچیدگی زاویه ای در روش تیگ. توسط امینی و همکاران مورد بررسی قرار گرفت و دو نوع فلاکس ZrO2 و TiO2. مورد بررسی قرار گرفت و بیشترین سختی را در حالت استفاده از 90 درصد اکسید تیتانیوم. و کمترین سختی در حالت استفاده از 90 درصد ZrO2 حاصل گردید. مشخص شد که فلاکس می تواند بر عمق و عرض جوش و اندازه دانه و سختی اثر بگذارد [1]. یکی از روش های رسوب جوش بر روی یک فلز دیگر از طریق عملیات روکش کاری بر روی قطعات انجام می گیرد.
اثر فلز پر کننده
تا ضمن بهبود خواص سطح مورد سائیدگی، ابعاد آن نیز بزرگتر می شود و به مقدار اولیه خود می رسد. و مقاومت سطح در مقابل سائیدگی، ضربه، حرارت و محیط های خورنده بهبود یابد. روش های گوناگونی از قبیل پر کردن یا بازسازی، لایه دهی توسط جوشکاری و فلز پاشی برای عملیات پوشش سطح وجود دارد. که غالباً یکی از اقتصادی ترین روش ها برای بازسازی قطعات مستهلک و افزایش عمر قطعات تازه به کار گرفته شده می باشد. عواملی از قبیل میزان رقت، ناخالصی ها و آلودگی ها، عملیات حرارتی، ظاهر سطح و تنش های حرارتی باید در عملیات سطحی کنترل شوند [2].
در پژوهشی توسط دهملایی و همکاران در جوشکاری قوسی تنگستن-گاز با جریان پالسی [3]. اثر فلزات پر کننده مختلف بر خواص اتصال غیر مشابه فولاد APISI-X80 به فولاد DSS-2205، بررسی شد. بدین منظور از فلزات پر کننده ER309L,ER2209 و KJS-124 استفاده شده است.
نتایج نشان می دهد که ریزساختار در نمونه های مورد جوشکاری تابع نوع الکترود می باشد. و انرژی ضربه ای و مقدار فریت با تغییر الکترود تغییر کرده و بالاترین انرژی ضربه ای مربوط به الکترود ER-2209 و ER-309 می باشد.
نصیری و همکاران [4] تأثیر حالت جوش و فلز پر کننده بر ریزساختار. و خواص مکانیکی اتصالات غیر مشابه فولاد ترمومکانیکی S900MC به فولاد کربنی ST52. با روش جوشکاری تیگ را مورد بررسی قرار دادند. جوشکاری در دو طرح مختلف مهیاسازی نمونه ها با شیار V و مربعی شکل. به ترتیب با و بدون استفاده از فلز پر کننده ER70S انجام شد. یک ریزساختار بینیتی در فلز جوش نمونه های متصل شده در حالت جریان پیوسته مشاهده گردید. در حالی که ریزساختار فلز جوش در حالت جریان پالسی. و استفاده از فلز پر کننده از فریتی به مارتنزیتی مورد تمپر در طراحی شیار V تغییر یافت.
در نرخ کرنش های عادی، هیچ تمایز قابل توجهی بین استحکام تسلیم و استحکام کششی اتصالات مختلف. با تغییر نوع جریان و نوع مهیا سازی نمونه ها وجود نداشت. با این حال، میزان تغییر طول نسبی اتصالات با جریان متداوم بهتر از اتصالات با جریان پالسی بود. افزایش نرخ کرنش منجر به بهبود شدید استحکام تسلیم و کششی اتصالات جوش دهی گردید. در حالت پیوسته و بدون استفاده از فلز پر کننده شد.
اثر فلز پر کننده
در تحقیقی دیگر رفتار سایشی جوش حاصل از فرایند مختلف جوشکاری GMAW,SMAW و FCAW. مورد بررسی قرار گرفت و فرایند تیگ یا GMAW کمترین میزان مقاومت به سایش. و سختی 200 ویکرز را از خود نشان داد. در نهایت، پوشش کاری مجدد با استفاده از فرایند FCAW بهترین نتیجه را برای قطعه ای به شکل محور. و از جنس فولاد AISI 4140 ایجاد کرد که این گزینه در طول عمر محور نیز بسیار تأثیر گذار بود [5].
تأثیر فلز پر کننده بر ریزساختار و عملکرد مکانیکی با روش جوشکاری با الکترود تنگستن با گاز محافظ (تیگ). روی نمونه اینکونل 625 در دمای اتاق و دمای بالا توسط عباسی و درخشنده حقیقی [6] مورد بررسی قرار گرفتند. هدف آنها ارزیابی تأثیر فلزات پر کننده ER321 و ERNiCr-3 بر عملکرد مکانیکی اتصالات جوش داده شده بود. نشان می دهد که فلز پر کننده ER321 در مقایسه با ERNiCr-3 از خواص کششی و ضربه ای قابل توجهی برخوردار نیست. ازدیاد طول در اثر کشش برای جوش های ERNiCr-3 که (13.1 درصد) بیشتر از اتصالات ER321 یعنی (10.2 درصد) بود. و میانگین چقرمگی ضربه جوش های ERNiCr-3 حدود دو برابر بیشتر از ER321 گزارش شد.
تأثیر سایش ضربه ای و مکانیزم تخریب اتصالات ایجادی در ریل راه آهن. با روش جوشکاری جرقه ای لب به لب مورد بررسی قرار گرفت و نتایج نشان می دهد. که مقاومت به سایش ضربه ای جوش ریل بالاتر از مواد خود ریل می باشد. میزان حجم مواد حاصله در این نوع تست سایش تابع تعداد سیکل و نیروی ضربه ای بوده. و بدلیل ساختار متفاوت جوش با ساختار خود ریل، مسیر رشد ترک نیز متفاوت خواهد بود [7].
تأثیر پارامترهای جوشکاری بر خواص مکانیکی و متالورژیکی جوشکاری فولاد زرهی. با استفاده از جوشکاری تیگ با دو فلز پر کننده AWS A5.18 ER90S-6 و AWS A5.9 ER307. توسط مورسی و همکاران [8]، مورد مطالعه قرار گرفته است. در حالی که شیارهای اعمالی شده به شکل V و مخروطی بودند. مشاهدات نشان می دهد که فلز پایه ساختار مارتنزیتی دارد. اما ریزساختارهای فلز جوش به فلز پر کننده فولاد کربنی یا فولاد آستنیتی، یک ریزساختار مارتنزیتی/آستنیتی را نشان می دهد. و این با نمودار شفلر مطابقت دارد.
و درصد رقت بالا بوده و حدود 35 درصد را نشان می دهد. بنابراین منجر به افزایش قابل توجهی در استحکام اتصال و مقاومت بالا در برابر ضربه خواهد شد.
اثر ترکیب فلز پر کننده بر ریزساختار و خواص مکانیکی فولاد API 5L X65 مورد جوش دهی. با قوس زیرپودری با چهار الکترود توسط بیدختی و پورمنش [9]، مورد بررسی قرار گرفت. مشاهدات ریزساختاری نشان می دهد که هر چه فریت سوزنی شکل بیشتری در ریزساختار تشکیل شود، خواص مکانیکی بهتری حاصل می گردد. نمونه های حاوی مقادیر بیشتری از تیتانیوم و بور دارای انرژی ضربه و استحکام بالاتری بودند. و دمای انتقال نرم به ترد نیز با افزایش مقدار فریت سوزنی کاهش می یابد. افزودن تیتانیوم، باعث ایجاد اجزای اکسیدی ریز شده و جوانه زایی فریت سوزنی را در ریزساختار تسهیل می نماید.
اسداللهی و همکاران [10] به بررسی اثرات فلزات پر کننده 25Cr-35Ni-35Cr-45Ni بر جوش پذیری. ریزساختار و خواص مکانیکی فولاد مقاوم در برابر حرارت 25Cr-35Ni پرداخته اند. نتایج نشان می دهد که ریزساختار در ناحیه تحت تأثیر حرارت در هر دو مورد. تا حد زیادی تحت تأثیر گرمای ورودی بر طول فرایند جوشکاری قرار می گیرد. انحلال کاربید به طور قابل توجهی در هر دو مورد مشاهده شد. و در هیچ یک از فلزهای پر کننده نشانه ای از تشکیل فاز سیگما در جوش وجود نداشت. که بدلیل نیکل بالای فلزات پر کننده است. همچنین نتایج نشان داد که خواص مکانیکی در هر دو مورد توسط ناحیه تحت تأثیر حرارت کنترل می شود.
تأثیر فلزات پر کننده بر خواص مکانیکی جوش های غیر مشابه بین سوپر آلیاژ اینکونل 625. و فولاد زنگ نزن سوپر آستنیتی AISI 904L با استفاده از جوش قوسی تیگ با جریان مداوم. با استفاده از فلزهای پر کننده ERNiCrMo-4 و ERNiCrCoMo-1 توسط پارابو و همکاران [11] انجام گردید. خواص مکانیکی و قابلیت جوشکاری نتایج آزمایش کشش تأیید کرد که شکستگی در فلز پایه AISI 904L. صرف نظر از فلز پرکننده مورد استفاده برای همه آزمایش ها رخ داده است. مقادیر سختی در سمت جوش اینکونل 625 برای پر کننده ERNiCrMo-4 به دلیل وجود عناصر تقویت کننده مانند Cr,Ni,Mo,W بیشتر مشاهده شد.
آزمایش ضربه تأکید کرد که جوش هایی که از فلز پر کننده ERNiCrMo-4 استفاده می کنند. چقرمگی ضربه ای بهتری را در دمای اتاق ارائه می دهند. نتایج آزمایش خمش نشان داد که جوش هایی که از این پرکننده ها استفاده می کنند. شکل پذیری خوبی را بدون ترک از خود نشان می دهند.
هدف از این مقاله، بررسی جوش پذیری فولاد کم آلیاژ AISI 1/6959 می باشد. در این راستا لازم است آزمون های متالورژیکی و مکانیکی متعددی از جمله آزمون کشش، آزمون ضربه، سختی سنجی و آنالیز شیمیایی به کارگیری شود. تا صحت پارامترهای انتخابی، مورد ارزیابی قرار گیرند. در بسیاری از موارد در حین فرایند تولید و با سرویس دهی قطعات، آسیب های سطحی به قطعات وارد می شود. که تعمیر آنها با استفاده از فرایند جوشکاری و حصول خواص مکانیکی نزدیک به قطعه اصلی. منجر به جلوگیری از صرف هزینه و زمان مازاد می شود که در این مقاله بررسی می شود.
2- مواد و روش تحقیق
برای انجام عملیات جوشکاری، قطعه ای از جنس فولاد 1/6959 که به DIN 35NiCrMoV12-5 نیز معروف است، انتخاب گردید. که در دسته فولادهای کم آلیاژ قرار دارد. این فولاد کاربرد زیادی در محور ژنراتورها و روتور توربین ها دارد. عمده ساختار این فولاد بعد از عملیات آهنگری، مارتنزیت و بینیت پایینی بوده و دارای استحکام تسلیم حدود 1500 مگاپاسکال می باشد. و این ناشی از میکروساختار مارتنزیت و بینیت و ریزدانگی ناشی از عملیات فورج است. در این فولاد انواع کاربیدهای مختلف از نوع M6C,M3C,M23C6,M7C3,M2C. از عناصر Cr,Fe,V,Ni,Mo تشکیل می شود.
همین طور نیتریدهای تیتانیوم، وانادیم و آلومینیوم نیز تشکیل می گردد. این کاربیدها و نیتریدها باعث متوقف شدن مرزها در حین تبلور مجدد و رشد دانه های آستنیت می شوند. این فولادها به طور معمول در حالت کوئنچ و تمپر با ساختار مارتنزیتی و بینیتی. در مصارفی نظیر مخازن تحت فشار، مته های حفاری ، لوله های توپ و غیره مورد استفاده قرار می گیرند. و در کاربردهای نظامی و تلوید اجزاء سلاح کاربرد ویژه ای دارند [12].
در این تحقیق از 8 ورق با ابعاد 10×50×100 میلی متر از جنش فولاد 1/6959. و همچنین از 4 دیسک با قطر 55 میلی متر و ضخامت 10 میلی متر از همین جنس استفاده گردید. ورق ها جهت تهیه نمونه های تست کشش، ضربه و سختی سنجی و نمونه های دیسکی شکل. جهت تهیه نمونه های تست سایش مورد استفاده قرار گرفتند. برای انجام تست کشش و ضربه بر روی نمونه ها و استفاده از هر فلز پر کننده جوشکاری. 2 ورق با ابعاد مذکور با استفاده از فرایند تیگ به صورت لب به لب جوش دهی شدند.
اثر فلز پر کننده
با توجه با اینکه به طور معمول فولاد DIN 35NiCrMoV12-5 در حالت فورج تولید می شود. و این غیر یکنواختی ساختار آثار منفی بر کیفیت جوش خواهد داشت. پیش از انجام مراحل جوشکاری، ورق ها تحت عملیات حرارتی نرمالیزه کردن قرار گرفتند. تا ساختاری کاملاً یکنواخت در آنها حاصل شود. عملیات حرارتی نرمال کردن این فولاد در دمای 850 درجه سانتی گراد و به مدت 2 ساعت انجام شد.
برای انجام تست سایش بر روی نمونه ها، ورق های یک سمت دیسک ها با استفاده از فرایند تیگ. و فلزهای پر کننده ER80S-Ni1,ER80S-B2,ER80S-G,ER70S-6 جوشکاری به صورت پوششی انجام شدند. برای سادگی و اختصار از این پس از این فلزهای پر کننده به عنوان Ni1,B2,S-G,S6 در متن یاد می شود. در این پژوهش، به منظور مقایسه جوش پذیری، خواص مکانیکی و مقاومت به سایش جوش، از فلزهای پر کننده با جنس مختلفی استفاده گردید.
فلزهای پر کننده مورد استفاده در این پژوهش با توجه به نزدیک بودن ترکیبات شیمیایی و خواص مکانیکی آنها. به فلز پایه و همچنین در دسترس بودن در بازار و صنعت ایران انتخاب شدند. هر چهار نوع فلز پر کننده مورد استفاده در دسته کم آلیاژی قرار می گیرند. اما درصد عناصر آلیاژی آنها محدود است و در عملیات جوشکاری با فرایندهای حفاظتی. با گاز (تیگ و میگ) یکی از پرکاربردترین فلزهای پر کننده محسوب می گردند.
قابلیت جوشکاری این فلزهای پر کننده با توجه به درصد کربن پائین و عدم وجود عناصر آلیاژی، مطلوب است. البته همین عدم وجود عناصر آلیاژی در این فیلرها باعث می شود، که قابلیت مطلوب نباشد. اما استفاده از آنها جهت جوشکاری فولادهای کربنی بسیار توصیه می شود. حضور عناصر منگنز و سیلیسیم در فلزهای پر کننده باعث می شود. تا از ایجاد تخلخل در حین جوشکاری جلوگیری به عمل آید. خواص مکانیکی و ترکیبات شیمیایی فلزهای پر کننده به ترتیب در جدول (1 و 2) ارائه شده است.
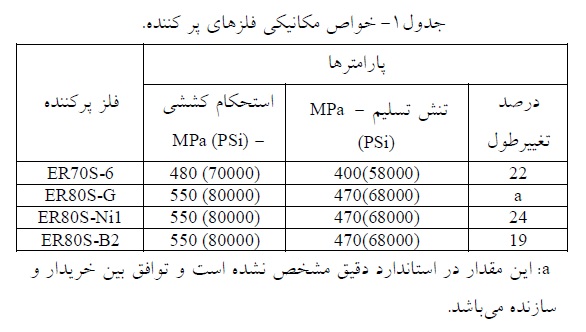
متغیرهای مورد استفاده در این تحقیق اعم از نوع فلز پرکننده و ولتاژ و جریان و سرعت جوشکاری در جدول (3) ارائه شده است. پیش گرم نمودن قطعه در دمای 200 درجه سانتی گراد با توجه به ترکیب شیمیایی فلز پایه مد نظر قرار گرفت. پس از اتمام عملیات جوشکاری، عملیات حرارتی برای تنش زدایی مطابق چرخه شکل (1) انجام گردید. و جهت اطمینان از وجود هرگونه عیوب ناشی از فرایند جوشکاری، بر روی آن تست غیر مخرب بازرسی چشمی انجام گردید.
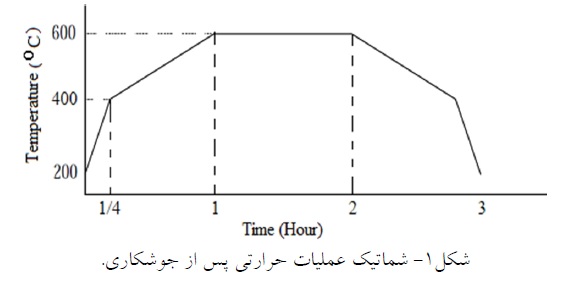
آزمون های کشش، ضربه، سختی، سایش و متالوگرافی به منظور بررسی مقاومت به سایش. و خواص مکانیکی جوش انجامی بر روی نمونه هایی از جنس فولاد 1/6959 انجام گرفت. در خصوص سختی با توجه نیاز به بدست آوردن نمودار سختی. و همچنین سختی سنجی در نقاط با فاصله کم، روش سختی سنجی ویکرز انتخاب گردید. در مورد تست کشش، تهیه نمونه استاندارد مطابق استاندارد ASTM A370 صورت پذیرفت.
اثر فلز پر کننده
متالوگرافی ساختار به کمک میکروسکوپ نوری و اچ کردن سطح توسط محلول نایتال 2 درصد صورت پذیرفت. با توجه به سختی مورد پیش بینی و شکل نمونه ها بهترین روش و در دسترس ترین روش. تست سایش پین بر روی دیسک می باشد که در این پژوهش بکار گیری شد.
3- بررسی و تحلیل نتایج
در این پژوهش، خواص مکانیکی و مقاومت به سایش جوش فولاد DIN 35NiCrMoV12-5 با استفاده از فلزهای پر کننده Ni1,B2,S-G,S6 مورد ارزیابی قرار گرفت.
1-3- تست کشش
به منظور بررسی خواص مکانیکی اتصال جوش حاصل از فلزهای پر کننده مورد بیان آزمون کشش انجام شد. از هر کدام از جوش های مورد حاصل 2 نمونه تست کشش مطابق استاندارد ASTM A370 تهیه گردید. ابعاد نمونه های مورد تهیه با توجه به محدودیت ابعادی نمونه های اولیه، از نوع اندازه کوچک انتخاب گردید. نتایج آزمون کشش برای فلزهای پر کننده جوشکاری مختلف در جدول (4) نمایان و مشخص است. همانطور که در جدول (4) و شکل (2) نمایان است. بیشترین استحکام در جوشکاری با فلز پر کننده B2 حاصل شده است.
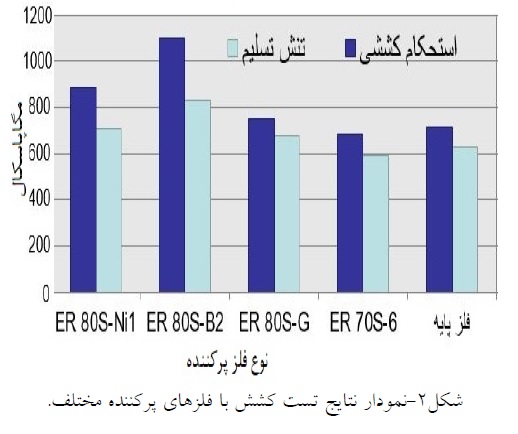
این فیلر استحکام تسلیم و کششی را نسبت به فلز پایه به ترتیب به اندازه 32 و 48 درصد افزایش داده است. علت این استحکام
اثر فلز پر کننده
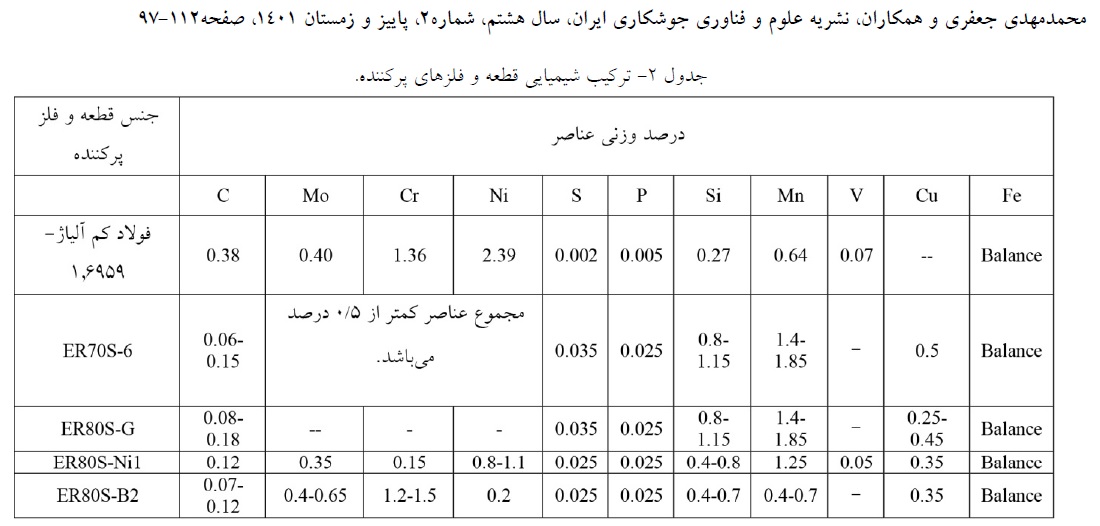
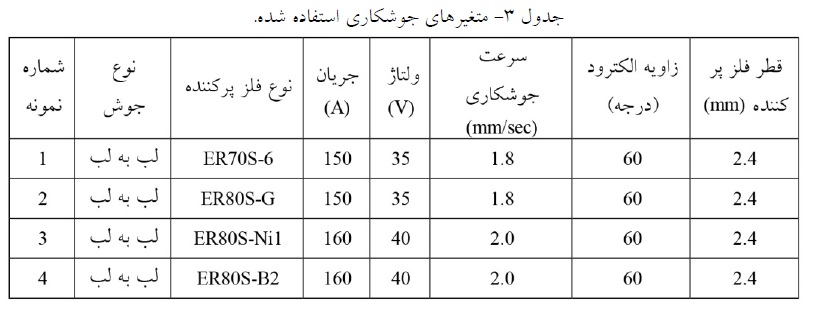
حضور عناصر آلیاژی کروم و مولیبدن موجود در این فلز پرکننده و در آلیاژ فلز پایه است. زیرا این دو عنصر جزء عناصر استحکام بخش در فولاد هستند. که حضور آنها استحکام جوش را افزایش می دهد.
جوش استحکام از فلز پرکننده Ni1 نیز استحکام خوبی دارد که می توان این استحکام مطلوب را ناشی از حضور عنصر استحکام بخش نیکل دانست. در نمونه های مورد جوشکاری با این الکترود استحکام تسلیم و کششی به ترتیب 12 و 25 درصد نسبت به فلز پایه بیشتر شده اند. در سه نمونه ای که حداقل استحکام کششی فلز پر کننده به صورت اسمی 80Ksi است. شکست در ناحیه تحت تأثیر حرارت رخ داده است.
اثر فلز پر کننده
در صورتی که فلز پر کننده جوشکاری مناسب انتخاب شده و قابلیت جوشکاری مطلوب باشد. باید شکست در فلز جوش رخ ندهد. چنانچه ملاحظه می شود نتایج تست کشش فلز پایه بدون جوشکاری نیز در جدول (4) نمایان و مشخص است[13]. به منظور انطباق این نتایج با ترکیب شیمیاییی و صحه گذاری نتایج فوق، ترکیب شیمیایی فلز جوش. در دو نمونه مورد جوشکاری با فلزهای پر کننده B2 و Ni1 در جدول (5) نمایان و مشخص است.
علت تفاوت ترکیب شیمیایی فلز جوش با فلز پایه، مربوط به ترکیب شیمیایی فلزهای پر کننده. تعداد پاس جوشکاری و درجه رقت بالای مربوط به روش جوشکاری است. درجه رقت به مفهوم درصد فلز پایه در جوش تقسیم بر درصد فیلر در جوش در روش جوشکاری تیگ بزرگ بوده. و در نتیجه حوضچه جوش از نظر ترکیب شیمیایی کمتر تحت تأثیر فلز پرکننده قرار می گیرد. کمترین استحکام کششی و تسلیم هم مربوط به حالت جوشکاری با فیلر S6 بود، که در حد فلز پایه است.
از نظر میزان تغییر طول نسبی نیز نمونه های فلز پایه و S6 بیشترین قابلیت انعطاف را داشتند. نمونه مرتبط با B2 تغییر طول نسبی متوسطی داشته ولی نمونه S-G که استحکام متوسطی داشت. حداقل تغییر طول نسبی را از خود نشان داده است. می توان یک ارزیابی تقریبی با استفاده از دیتاهای جدول (4) برای مقایسه انرژی شکست بین 4 نمونه انجام داد.
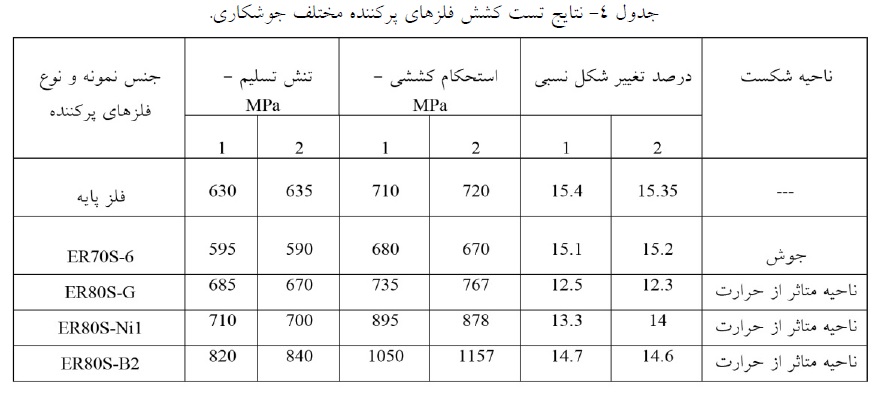
اثر فلز پر کننده

انرژی شکست در واقع سطح زیر منحنی تنش-کرنش است. ولی اگر با تقریب آن را در معادل استحکام کششی متوسط ضربدر تغییر طول نسبی متوسط. از جدول (4) در نظر بگیریم انتظار داریم که در 4 الکترود بیشترین انرژی مربوط به B2 و سپس S-G,S6,Ni1 باشد.
2-3- تست ضربه
به منظور بررسی مقاومت به ضربه و چقرمگی یا انرژی شکست فلزهای پر کننده مختلف. آزمون ضربه بر روی نمونه های جوش مورد انجام با ابعاد 55 و مقطع 10×10 انجام گرفت. برای بدست آوری انرژی شکست در منطقه تحت تأثیر حرارت شکاف در نمونه ضربه در این ناحیه ایجاد شد.
برای این منظور از هر نمونه مورد جوشکاری، 2 نمونه تست ضربه با شکاف در مرکز جوش و 2 نمونه. با شکاف در ناحیه مجاور جوش تهیه شد. نتایج تست ضربه در جدول (6) و نمودارهای مربوطه در شکل (3) نمایان و مشخص است.
اثر فلز پر کننده
اگر متوسط نتایج 4 آزمایش ضربه مربوط به هر نمونه را به عنوان انرژی متوسط شکست محاسبه کنیم. خواهیم دید که اولاً بیشترین انرژی جذبی مرتبط با ضربه مربوطه به نمونه فلز پایه است. بعد از پایه بیشترین انرژی ضربه ای یا چقرمگی مربوط به نمونه جوش شده با فیلر B2. و سپس Ni1 و در نهایت S-G,S6 می باشد. که در تطابق دقیق با پیش بینی مربوط به تست کشش می باشد. یادآوری می شود که تست های کششی عمود بر خط جوش تهیه شده. و در بر دارنده خواص منطقه تحت تأثیر حرارت و منطقه جوش بصورت توام بوده. و خواص کلی جوش انجامی را نشان می دهد.
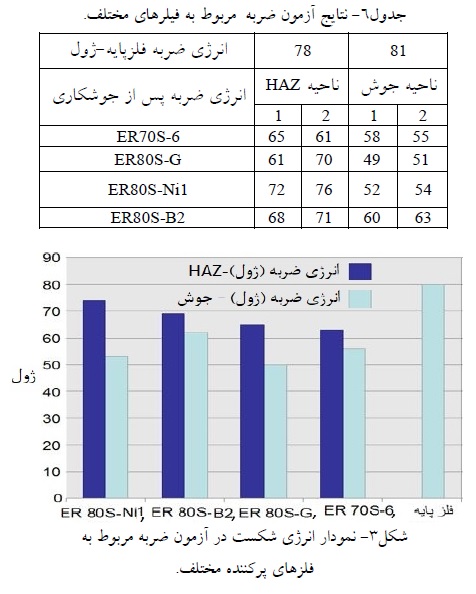
بطور کلی اگر متوسط نتایج 4 آزمایش ضربه مربوط به هر نمونه را به عنوان انرژی متوسط شکست محاسبه کنیم. خواهیم دید که اولاً بیشترین انرژی جذبی مرتبط با ضربه مربوط به نمونه فلز پایه است. بعد از فلز پایه بیشترین انرژی ضربه ای یا چقرمگی مربوط به نمونه جوش شده با فیلر B2. و سپس Ni1 و در نهایت S-G,S6 می باشد. که در تطابق دقیق با پیش بینی مربوط به تست کشش می باشد.
یادآوری می شود که تست های کششی عمود بر خط جوش تهیه شده. و در بر دارنده خواص منطقه تحت تأثیر حرارت و منطقه جوش بصورت توام می باشد و خواص کلی جوش انجامی را نشان می دهد. بطور کلی انرژی شکست در تمامی نمونه ها در منطقه HAZ بالاتر از منطقه جوش است. در منطقه تحت تأثیر حرارت کمترین انرژی شکست مربوط به نمونه S-G می باشد. زیادتر بودن انرژی شکست در نمونه های ضربه با شیار ایجادی در منطقه تحت تأثیر حرارت. نشان دهنده تغییرات فازی مطلوب در اثر جوشکاری و عملیات حرارتی بعدی در این منطقه. و ساختار ضعیت موجود در منطقه جوش می باشد.
اثر فلز پر کننده
وجود کمترین انرژی ضربه ای و تغییر طول نسبی در نمونه مورد جوشکاری با فیلر S-G. نشانه وجود فاز سخت و احتمالاً غیر یکنواخت و استعداد زیاد ساختار به توسعه ترک می باشد.
بالاترین انرژی ضربه ای و استحکام کششی و تغییر طول متوسط در نمونه B2. نشانه فاز سخت و در عین حال توزیع یکنواخت فازی می باشد.
تغییرات زیاد در اعداد انرژی ضربه ای در نمونه S-G (نه واحد اختلاف ) در دو نمونه تهیه شده از ناحیه متأثر از حرارت. نشانه عدم یکنواختی ساختار در مناطق مختلف در طول جوش در این نمونه می باشد. نتایج تقریبی حاصل از تست کشش نیز در تطابق با نتایج تست ضربه است. در خصوص نمونه های مورد جوشکاری، بیشترین انرژی ضربه مربوط به نمونه مورد جوشکاری با فلز پر کننده B2 است. که بدلیل تلفیق اثر سازنده تنش تسلیم، استحکام کششی و میزان تغییر شکل شکست بالا در این نمونه. نسبت به نمونه های جوشکاری دیگر می باشد [13].
3-3- سختی سنجی
یکی از متغیرهای تعیین کننده در خواص مکانیکی اتصالات حاصل از جوش. سختی نواحی مختلف جوش از جمله سختی فلز پایه، ناحیه تحت تأثیر حرارت و فلز جوش است. که باید یک ارتباط منطقی بین سختی، استحکام و ساختار این نواحی به دست آورد. میزان و نحوه تغییرات سختی در مناطق مرتبط با جوش می تواند در ارائه یک مدل از تغییرات فازی هم کمک کند. با همین صدف سختی نواحی مختلف جوش در نمونه های مورد جوشکاری با فلزهای پر کننده مختلف. مورد بررسی و اندازه گیری قرار گرفت که نتایج آن در نمودارهای شکل (4) نمایان و مشخص است. کلیه فاصله ها بر حسب میکرومتر و سختی ها بر واحد ویکرز می باشد.
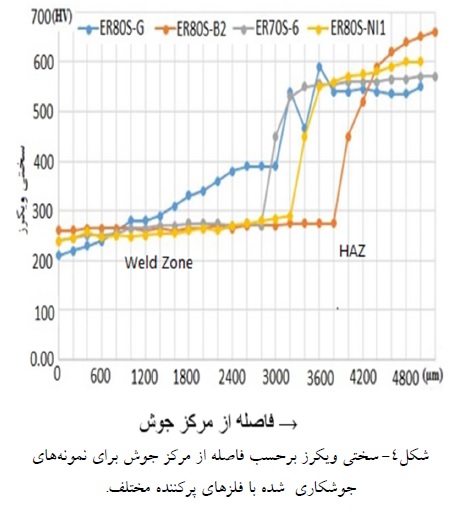
نمودار سختی ویکرز بر حسب فاصله از مرکز جوش برای نمونه های مورد جوشکاری. تا فاصله خاصی بدون تغییر بوده و بعد از آن رشد ناگهانی کرده. و در نهایت به منطقه سوم با تغییرات سختی کم با سختی میانگین حدود 550 تا 650 ویکرز می رسد. در نمونه جوش شده S-G منطقه پایدار اولیه از نظر سختی وجود ندارد.
اثر فلز پر کننده
بنابراین انتظار داریم که در منطقه جوش نمونه S-G ساختار میکروسکوپی متفاوت با بقیه نمونه ها بوده. و در سه نمونه دیگر ساختار مشابهی را در منطقه ذوب داشته باشیم. افزایش سختی ناشی از تغییرات ساختار نمونه در ناحیه تحت تأثیر حرارت و فلز جوش می باشد. ایجاد ساختارهای سخت نظیر مارتنزیت و بینیت و ویدمن اشتاتن در فلز جوش، افزایش سختی را در پی خواهد داشت [5].
نمونه مورد جوشکاری با فیلر B2 بیشترین سختی در ناحیه تحت تأثیر حرارت را نشان می دهد. یادآوری می شود که بیشترین استحکام کششی و تسلیم و بیشترین انرژی ضربه ای هم مربوط به همین نمونه بود. سختی زیاد در کنار انرژی ضربه ای زیاد نشانه وجود یک فاز قوی با توزیع یکنواخت و مقاوم در برابر توسعه ترک است. افزایش سختی در نمونه ها همچنین ناشی از تغییرات ساختار نمونه در ناحیه تحت تأثیر حرارت و فلز جوش می باشد.
ترتیب حداکثر سختی در 4 نمونه الکترود به ترتیب S-G,S6,Ni1,B2 است. که دقیقاً همان ترتیب مورد بیان برای انرژی ضربه ای جذبی و مطابق با افزایش استحکام کششی و تسلیم است. هر چند در ترتیب S-G,S6 معکوس می شود. که بدلیل تأثیرگذاری توأم استحکام و میزان تغییر شکل بر چقرمگی است. سختی حداقل در فیلر S6 می تواند به دلیل عدم حضور عناصر آلیاژی در این فیلر باشد. لیکن تغییرات سختی با فیلر S-G می تواند ناشی از تغییرات فازی باشد.
اثر فلز پر کننده
تنها در این نمونه در منطقه جوش سختی ثابت نداشته و سختی با دور شدن از مرکز جوش در حال افزایش است. سختی یکسان در مرکز جوش 3 نمونه دیگر ناشی از ساختار یکسان جوش در این نمونه هاست. کمتر بودن سختی جوش نسبت به مناطق خازج از جوش نیز بدلیل تغییر فازها به فاز نرم تر در اثر جوشکاری می باشد.
که در جوشکاری های ذوبی امری متداول است. در یک جمع بندی کلی، چنانچه در نمودارها معلوم و مشخص است. سختی فلز جوش در 3 نمونه تقریباً نزدیک به هم است. و به محص ورود به ناحیه تحت تأثیر حرارت، سختی به شدت افزایش می یابد. در اکثر تحقیقات مشابه نیز سختی ناحیه تحت تأثیر حرارت بالاتر از فلز پایه و فلز جوش بوده است [5].
4-3-تست سایش
یکی از اهداف اصلی این پژوهش تعیین مقاومت به سایش جوش با استفاده از فلزهای پر کننده مختلف می باشد. که در واقع در انتخاب فلز پرکننده بهینه جهت کاربردهای صنعتی مختلف حائز اهمیت است. تست سایش با استفاده از دستگاه پین بر روی دیسک با نیروهای 2 و 4 کیلوگرم برای تمامی نمونه ها انجام شد. یکی از خروجی های اصلی تست سایش، تعیین کاهش وزن نمونه ها و ضریب اصطکاک می باشد. که در واقع تعیین کننده مقاومت به سایش نمونه ها است.
نمودارهای شکل (5 و 6) به صورت تجمعی کاهش وزن فلزهای پر کننده مختلف در مسافت های تا 1000 متر. را به ترتیب برای نیروهای 2 و 4 کیلوگرم ارائه می نماید. تست سایش نشان دهنده مقاومت سایشی منطقه جوش می باشد. و نمونه های تهیه شده دیسک شکل بوده و قطر 50 و ضخامت 5 میلی متر داشتند. که از روی یک میله جوش شده با فیلر مربوطه خارج شده و سپس ماشین کاری و سنگ زده شد. تا حدی که 2 میلی متر از جوش باقی مانده و صافی سطح 0/8 ایجاد شود.
همانگونه که مشاهده می گردد افزایش نیرو به 4 کیلوگرم بشدت بر میزان کاهش وزن اثر می گذارد. بیشترین کاهش وزن با بار اعمال شده 2 و 4 کیلوگرم. مربوط به فلز پایه و نمونه جوشکاری شده با فلز پر کننده S6 می باشد. و بیانگر این است که کمترین مقاومت به سایش را دارا می باشد. همچنین کمترین کاهش وزن و بیشترین مقاومت به سایش در استفاده از فلز پر کننده Ni1 حاصل شده است.
در مرحله دوم و سوم از نظر مقاومت سایشی فیلر S-G و سپس B2 قرار دارد. در حالت کلی می توان گفت جوش اعمالی بر روی فولاد کم آلیاژ 1/6959. با استفاده از فلز پر کننده Ni1 دارای بیشترین مقاومت به سایش منطقه جوش است. و در طراحی اتصالات جوشی و در تعمیر قطعات با هدف مقاومت به سایش و با کمک فرایند جوشکاری. بهترین گزینه این فلز پر کننده خواهد بود.
نتایج نمودارهای شکل (6) به طور کامل تأیید کننده نمودارهای شکل (5) میباشد. تنها با افزایش نیروی اعمالی فاصله بین منحنی های مربوط به Ni1 و S-G بشدت کم می شود. ولی ترتیب و توالی منحنی ها بهم نمی خورد. با نیروی 4 کیلوگرم نیز کمترین کاهش وزن و بیشترین مقاومت به سایش مربوط به فلز پر کننده Ni1 است. و در طراحی های مهندسی باید به اثر نیرو بر میزان سایش نمونه ها و ترتیب و توالی آنها توجه کرده. و در استفاده از فلزهای پر کننده مختلف، این نتایج مد نظر قرار گیرد [14].
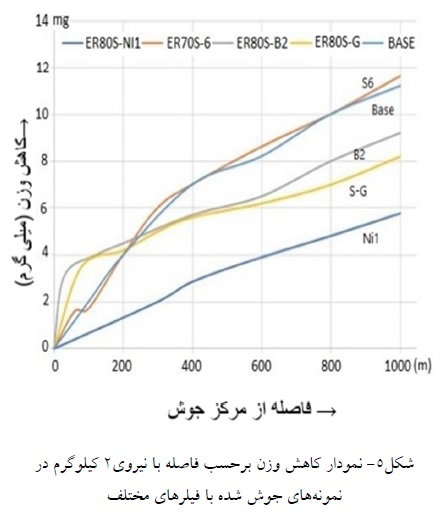
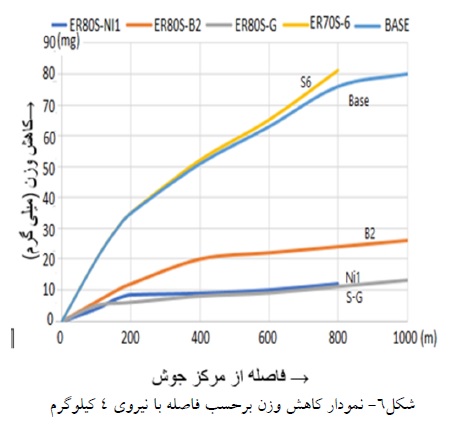
دیده شد که ترتیب نمونه ها از نظر سختی و مقاومت ضربه ای مشابه بودند ولی ترتیب مقاومت سایشی کاملاً متفاوت است.
تغییرات سختی و ضربه مربوط به کل نمونه است. ولی مقاومت سایشی تنها منعکس کننده منطقه جوش می باشد. بعلاوه مقاومت سایشی نه تنها به سختی بلکه به عوامل متعدد دیگری از جمله اندازه. و نحوه توزیع رسوبات و اندازه دانه و اندازه و مقدار فازها نیز بستگی دارد. به همین دلیل ارتباط دقیقی بین سختی و مقاومت سایشی بر قرار نمی باشد.
مقادیر میانگین ضریب اصطکاک با توجه به مسافت. براساس کاهش وزن مربوط به نمونه های مورد جوشکاری با فلزهای پر کننده مختلف. و با دو نیروی 2 و 4 کیلوگرم نیز در جدول (7) ارائه شده است.
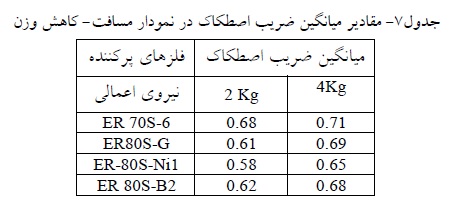
نتایج ضریب اصطکاک در تأیید کامل نتایج کاهش وزن در اثر سایشی است. کمترین ضریب متوسط اصطکاک مربوط به نمونه Ni1 با بیشترین مقاومت سایشی. و بیشترین ضریب متوسط اصطکاک مربوط به نمونه S6 با کمترین مقاومت سایشی است. مقادیر میانگین ضریب اصطکاک برای فلز پرکننده Ni1 در دو نیروی 2 و 4 کیلوگرم حدود 0/615 است. که در مقایسه با سایر فلزهای پر کننده، ضریب اصطکاک پائینی محسوب می گردد. و در واقع مقاومت به سایش عالی این فلز پرکننده را نشان می دهد.
اثر فلز پر کننده
میانگین ضریب اصطکاک فلز پرکننده B2 و S-G حدود 0/65 است. که مقاومت به سایش متوسطی را نشان می دهد. میانگین ضریب اصطکاک فلز پرکننده S6 حدود 0/695 است. که نسبت به سایر فلزهای پر کننده مقدار بالایی است. و در واقع این فلز پرکننده کمترین مقاومت به سایش را از خود نمایان می کند [15و 16] [17]. ترتیب و توالی فیلرها از نظر مقاومت سایشی از زیاد به کم به ترتیب S6,B2,S-G,Ni1 می باشد.
که در تطابق دقیق با میزان سایش این نمونه ها است. تفاوت در مقاومت سایشی نمونه های مختلف در منطقه جوش. بدلیل اثر عناصر آلیاژی و تغییرات فازی در اثر جوشکاری. و استفاده از فیلرهای با ترکیب شیمیایی متفاوت می باشد.
4-ساختار میکروسکوپی
فولاد 1/6959 AISI معادل فولاد 4340 می باشد. فولاد 4340 با توجه به دیاگرام فازی CCT نشان داده شده در شکل (7). و سرعت سرد کردن می تواند ساختارهای متفاوتی را پس از جوشکاری و سرد شدن منطقه جوش داشته باشد. این ساختار می تواند از مخلوط فریتی-پرلیتی تا ساختارهای حاوی فاز بینیت و مارتنزیتی کامل تغییر کند.
فریت کمترین سختی را داشته ولی به ترتیب از پرلیت به بینیت و سپس مارتنزیت سختی افزایش پیدا می کند. البته تأثیر حرارت می تواند بشدت این سختی ها را تعدیل کند. به نحوی که مثلاً سختی مارتنزیت تمپر شده در دماهای بالا بشدت کم شود.
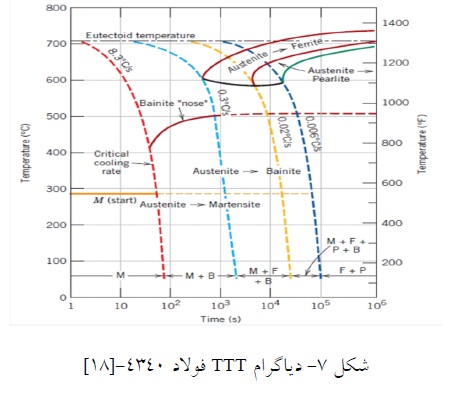
در سرعت های بینابین برای سرد کردن جوش تا دمای محیط فاز بینیت نیز میتواند. در کنار یک یا چند تا از فازهای پرلیت، فریت و مارتنزیت ظاهر شود. هرچند فولاد کاربردی معادل 4340 است. منتها فلز جوش با توجه به ترکیب متفاوت فیلرها و میزان اختلاط آنها با فلز پایه. می تواند ترکیب شیمیایی را تا حدی تغییر و محدوده ظهور فازها و همچنین مقدار و حتی نوع و تعداد فازها را عوض کند.
اثر فلز پر کننده
عناصر آلیاژی مهم در فیلرها نیکل، منگنز، مولیبدن و کروم هستند. نیکل و منگنز آستنیت زا بوده و محدوده این فاز را بزرگ می کنند. این دو عنصر باعث افزایش چقرمگی و انرژی ضربه ای می شوند. در مقابل کروم و مولیبدن فریت زا بوده و منطقه آستنیتی را کوچک کرده. و باعث افزایش تمایل به مارتنزیتی شدن فولاد و ایجاد رسوبات کاربیدی می شوند.
همانگونه که ذکر شد سختی منطقه جوش در همه نمونه ها تقریباً ثابت و در حدود 250 ویکرز بود. که سختی کمی است. بنابراین انتظار داشتن فازهای فریتی و پرلیتی را در منطقه جوش داریم شکل (8). فازهای دیده شده در منطقه جوش ایجادی در اثر جوشکاری با 4 نوع فلز پر کننده را نشان می دهد. ساختار به وضوح دو فازی بوده و در تمام نمونه ها حالت فازی مشابهی را با تفاوت های اندک داریم. فاز تیره پرلیت و فاز روشن فریت می باشند.
سختی همه نمونه ها بجز S-G ثابت بوده و در حد سختی ساختار فریتی-پرلیتی است. در حالت اخیر سختی از مقادیر کمتر از سایر نمونه ها شروع شده و با دور شدن از مرکز جوش زیاد شده. و بالاتر از سختی متوسط 250 ویکرز قرار می گیرد. با توجه به ساختار میکروسکوپی نمونه S-G نیز بنظر می رسد مقادیر پرلیت کمی کاهش بیابد و فریت بیشتر می شود. بنظر می آید عدم یکنواختی توزیع فازهای پرلیت و فریت در این نمونه و ایجاد موضعی فاز بینیت. مسئول توزیع غیر یکنواخت و افزایش سختی در منطقه جوش باشد.
نمونه های سایشی از منطقه ذوب تهیه شده و بنابراین باید تابع سختی این منطقه باشند. بدلیل سختی بیشتر این نمونه، مقاومت سایشی این نمونه نیز بالا می باشد. غیریکنواختی در ساختار و وجود بینیت همچنین باعث ایجاد مناطقی با استعداد ایجاد ترک و کاهش شدید چقرمگی این آلیاژ شده است.
شکل (9) نیز ساختار منطقه تحت تأثیر حرارت را در آلیاژهایی که با فیلرهای مختلف جوش شدند نشان می دهد. با مشاهده شکل (4) و عرض منطقه با سختی ثابت که حدود 3 تا 3/5 میلی متر است. مشخص است که عرض منطقه جوش با تقریب حدود 7 تا 7 میلی متر بوده است. بعد از منطقه جوش سختی بسرعت افزایش می یابد و به سختی فلز پایه میل می کند.
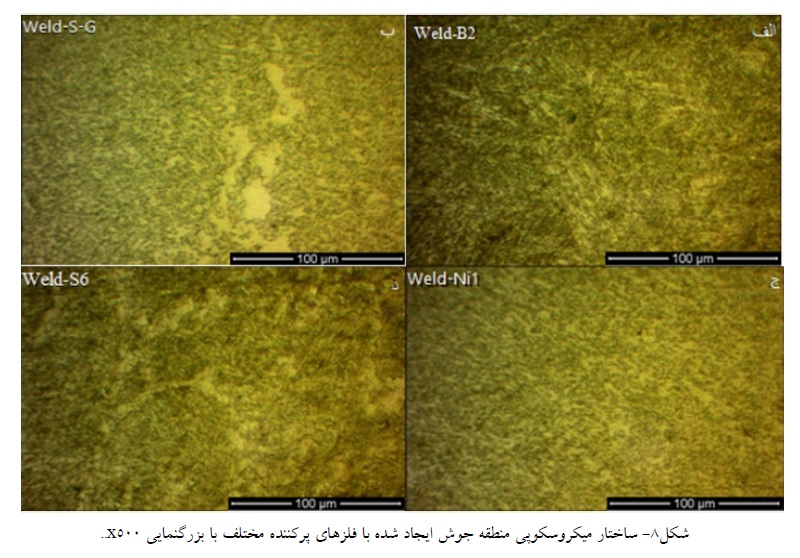
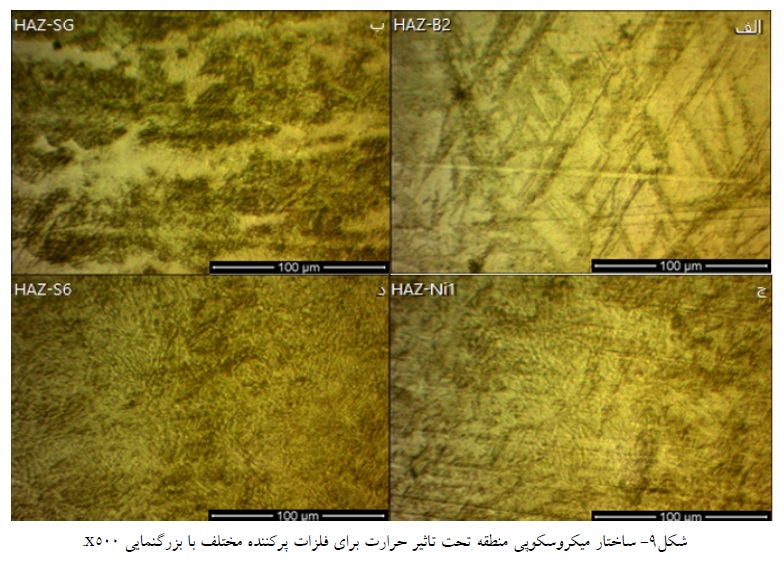
ورود به منطقه آستنیته در اثر حرارت ورودی جوشکاری و افزایش دما می تواند باعث حل شدن کاربیدها. و ایجاد فاز و دانه های آستنیت گردد. این فاز آستنیت در مراحل بعدی با توجه به سرعت سرد شدن می تواند به فازهای مارتنزیت-بینیت یا پرلیت تبدیل شود. با توجه به نوع و مقدار فازها سختی نمونه ها متغیر خواهد بود. سختی متوسط در منطقه تحت تأثیر حرارت به حدود 550 ویکرز می رسد. که معادل سختی ساختارهای مارتنزیتی و بینیتی است.
اثر فلز پر کننده
بطور کلی فلز پایه دارای کمترین استحکام کششی و تسلیم بیشترین قابلیت انعطاف و بیشترین چقرمگی بود. که نشان دهنده فاز بسیار نرم در این آلیاژ اولیه می باشد. بنابراین این فاز می تواند با توجه به سرعت سرد کردن و عملیات حرارتی آلیاژ اولیه عمدتاً فریتی و پرلیتی بوده. و یا ساختار مارتنزیتی به شدت تمپر شده باشد.
ساختار مربوط به نمونه S6 مارتنزیتی کاملاً تمپرینگ است و بنابراین انتظار داریم که آلیاژ مربوطه دارای مقاومت سایشی کمی باشد. کمترین مقاومت سایشی مربوط به این آلیاژ است. ساختار نمونه B2 نیز به وضوح تیغه های مارتنزیت را همراه با بینیت بالایی نشان می دهد.
ساختار نمونه Ni1 مارتنزیت تا حدی تمپر شده را کنار تعداد محدودی تیغه مارتنزیتی نشان می دهد. بنابراین ساختار در سه نمونه مورد بیان مارتنزیتی است منتها از B2 و سپس Ni1 و در نهایت S6 میزان تمپرینگ بیشتر می باشد. سختی نیز به همین ترتیب کاهش پیدا خواهد کرد.
در مورد نمونه S-G فازها کاملاً متفاوت هستند. در این مورد مارتنزیت تمپرینگ در کنار مقدار زیادی از فریت نمایان می شود. با توجه به عرض منطقه ذوب یا همان منطقه با سختی ثابت نمایان است که با افزایش عرض ذوب. سختی نهایی در منطقه تحت تأثیر حرارت افزایش می یابد. افزایش عرض ذوب به معنی حرارت ورودی بیشتر و دمای بالاتر و زمان بیشتر توقف در منطقه آستنیتی. و در نتیجه احتمال بیشتر دستیابی به فازهای سخت مارتنزیت و بینیت می باشد.
در آلیاژ B2 در مقایسه با دیگر نمونه ها بیشترین حرارت ورودی در جوش وجود دارد. بنابراین آستنیت بیشتری در منطقه تحت تأثیر حرارت ایجاد شده و بدلیل دمای بالاتر. و در نتیجه سرعت سرد شدن بیشتر انتظار سخت ترین فاز را در این حالت در منطقه تحت تأثیر حرارت داریم. ساختار در نمونه Ni1 بدلیل حرارت ورودی و سرعت سرد شدن کمتر. نتوانسته است مارتنزیت با جهت گیری مشخص زیادی تولید کند. اما ساختار ظریف مارتنزیت تمپر شده را ایجاد کرده است.
بدلیل این ساختار بسیار ریز و یکنواخت بیشترین مقاومت سایشی در این آلیاژ ایجاد می گردد. تأثیر حرارت ورودی در جوشکاری قوس دستی نیز توسط تقی پور و همکاران [19]. بر روی میزان فریت و بینیت و سختی و انرژی ضربه ای فولاد HSLA-100 نمایان و مشخص است. آلیاژ مرتبط با فیلر S-G دارای ساختار فریتی-مارتنزیتی است منتها در این مورد ساختار دارای توزیع یکدست و یکنواخت نیست. بنابراین نمایان است که جوشکاری در منطقه جوش باعث ایجاد ساختار فریتی پرلیتی درشت با سختی کم می شود.
کمی دورتر در منطقه تحت تأثیر حرارت در اثر حرارت ناشی از جوشکاری فازهای مارتنزیت و بینیت توسعه پیدا کرده است. تغییر در نوع فازها و مقدار و اندازه و نحوه توزیع آنها در اثر تغییر دمای بیشینه جوشکاری و سرعت سرد شدن. و میزان حرارت ورودی باعث تغییر خواص در منطقه تحت تأثیر حرارت می گردد. وجود فازهای سخت و مستعد ترک در منطقه تحت تأثیر حرارت موجب شکست نمونه ها در تست کشش در این منطقه گردید. خواص کلی حاصل از جوشکاری نیز توسط منطقه تحت تأثیر حرارت کنترل می شود.
5- نتیجه گیری
در این پژوهش خواص مکانیکی و تریبولوژی جوش حاصل از 4 نوع فلز پرکننده مختلف بر روی فولاد AISI 1/6959 مورد بررسی قرار گرفت. و بدین منظور آزمون های کشش، ضربه، سختی، سایش و متالوگرافی بر روی نمونه ها انجام شد. بهترین قابلیت جوشکاری و خواص مکانیکی، در جوشکاری با استفاده از فلز پر کننده جوشکاری B2 حاصل شد. تنش تسلیم و استحکام کششی جوش مورد انجام با کمک این فلز پر کننده به ترتیب 830 و 1100 مگاپاسکال می باشد. که 32 و 48 درصد بیش از فلز پایه می باشد.
اثر فلز پر کننده
میزان تغییر شکل متوسط تا نقطه شکست نیز 14/65 درصد است. که بسیار نزدیک به فلز پایه است. حضور عناصر آلیاژی مولیبدن و کروم در این فلز پر کننده منجر به افزایش استحکام اتصال جوش می گردد. در هنگام طراحی اتصال جوشکاری فولاد 1/6959، در شرایطی که استحکام و سختی مد نظر باشد. فلز پرکننده B2 گزینه مناسبی خواهد بود.
با توجه به نتایج آزمون ضربه، بهترین چقرمگی و مقاومت به ضربه نیز در اتصال جوش حاصل از فلز پرکننده B2 حاصل گردید.
سختی منطقه جوش در تمامی نمونه ها تقریباً ثابت و در حدود 250 ویکرز میباشد. و سختی منطقه تحت تأثیر حرارت در نمونه ها بین 580 تا 620 ویکرز است.
بهترین مقاومت به سایش و کمترین میزان کاهش وزن در جوش با فلز پرکننده Ni1. و کمترین مقاومت به سایش و بیشترین کاهش وزن در جوش با فلز پر کننده S6 حاصل گردید.
نمونه B2 نیز دارای مقاومت به سایش مناسبی می باشد.
با توجه به نتایج مورد حاصل می توان نتیجه گرفت. که در صورتی که نمونه جوشی تحت سایش نبوده و یا شرایط سایشی بسیار سبک باشد. می توان از فلز پر کننده S6 و در شایطی که نمونه جوشی تحت سایش شدید باشد. از فلز پرکننده Ni1 جهت جوشکاری استفاده کرد.
به عنوان یک نتیجه گیری اساسی می توان گفت در شرایط کلی جهت جوشکاری فولاد کم آلیاژ 1/6959. و به منظور دستیابی به خواص مکانیکی مطلوب بخصوص در شرایط وجود ضربه. استفاده از فلز پر کننده جوشکاری B2 توصیه می شود. در شرایطی که صرفاً مقاومت به سایش مد نظر باشد. با توجه به نوع و میزان سایش، فلز پرکننده Ni1 و B2 توصیه می گردد. در حالتی که بیشترین قابلیت انعطاف و کمترین استحکام و سختی مد نظر باشد نیز کاربرد فیلر S6 برای جوشکاری توصیه می شود.
اثر فلز پر کننده
فلز پرکننده S-G در بسیاری از حالات نظیر استحکام کششی و تسلیم و انرژی ضربه ای. و سختی شبیه به پر کننده S6 عمل می کند، و تنها در شرایط سایشی بر S6 ارجحیت دارد. بنابراین با توجه به موارد مورد بیان و بدلیل غیریکنواختی در ساختار و استعداد به ایجاد ترک برای جوشکاری آلیاژی 1/6959 توصیه نمی شود.
دیده شد که تغییر در ساختار میکروسکوپی نمونه ها در منطقه جوش. و منطقه تحت تأثیر حرارت در اثر تغییر فلز پرکننده می تواند باعث تغییرات در خواص کلی و خواص منطقه جوش شود.
محمد مهدی جعفری 1، احمد افسری1، سید احمد به گزین2*، شاهین حیدری 3
1- گروه مهندسی مکانیک، واحد شیراز، دانشگاه آزاد اسلامی، شیراز، ایران
2- گروه مهندسی مکانیک، دانشکده فنی و مهندسی باهنر شیراز، دانشگاه فنی و حرفه ای، شیراز، ایران.
3- مرکز تحقیقات بیماری های پیوند و استخوان، دانشگاه علوم پزشکی شیراز، ایران.